VirtualCT: realistic composite material modeling using micro-CT-based voxel approach
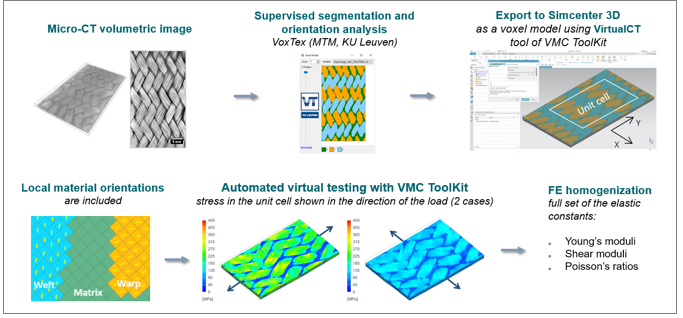
Recall the blogpost a few weeks ago about the Simcenter 3D Virtual Material Characterization (VMC) ToolKit for materials engineering of lightweight components[1]. With the VMC ToolKit, the material design process can be completed with fewer tests, and then up-scaled to the component level via homogenization techniques. The multi-scale modelling workflow starts with the generation of a representative unit cell of a fiber-reinforced composite (in the size of millimeters). Subsequently, a detailed finite element (FE) model is automatically set up in Simcenter 3D and solved to obtain properties that can be homogenized for the entire volume which is representative for the studied composite material. The VMC ToolKit has been created in collaboration with several academic partners in the scope of the SIM M3 Program, using NX Open © to interface with key third party solutions such as the “WiseTex” suite for fiber-reinforced composites geometry generation (courtesy of KU Leuven, Belgium) and key methods such as virtual parameter identification schemes required to model composites damage (courtesy of Ghent University, Belgium).
The geometry generator, WiseTex, produces so-called “idealized” unit cell structures (Figure 1 (left)). Such an approach accepts certain assumptions of, for example, a simplified shape of the yarn cross-section, its constant form along the yarn length or warp/weft yarns alignment [2, 3]. However, real-life structures are not perfect, which also applies to composites (Figure 1 (right)). Real composite materials are subjected to geometrical variability and possible defects introduced by the different phases of the manufacturing process [4].Figure 1: Examples of “idealized” (left) and real (right) composite geometries (a micro-CT image). The dashed rectangle indicates a defect in the composite specimen [5].
It is known that more reality (details) in the modeled geometry leads to a higher accuracy of the modelling prediction. Thus, the next R&D question is: how can the real geometry of composites be introduced in simulations? This blogpost will show a positive answer to this question: with the help of modern image processing techniques leading to the generation of materials models based on Micro-CT images. This is the topic of a VLAIO-funded postdoctoral research “Innovation Mandate” called “MicroCT-based Model Generation Engine for Virtual Material Characterization” between Siemens Industry Software NV and the Department of Materials Engineering (MTM), KU Leuven. The aim is to provide a new “VirtualCT” functionality to the VMC ToolKit that allows delivering more realistic composites models, by getting information (geometry, orientation) directly from pictures taken, and directly translating that information into models.
First, let’s take a look at the core imaging technique “Micro-CT” (or in full: “X-ray Micro–Computed Tomography”). What is this about? As shown in Figure 2 (left), the sample is placed on a rotation stage and radiated with X-rays. The rotation step θ is defined by the user. A detector acquires high-resolution “X-rays shadows of the sample” (called radiographs) at each rotation step. This process is similar to what radiologists perform on people in hospitals. Afterwards, a 3D volumetric image of the sample is created from the radiographs using a reconstruction software (Figure 2 (right)). Beyond medical applications, this technique is widely used in materials science. For composites, one should know that matrix and fibers usually absorb X-rays differently (except for carbon fiber-reinforced polymers; both matrix and fibers have a high carbon content), so there is the advantage that the general texture and layup of reinforced plastics can be observed in the micro-CT images (Figure 1 (right)).
Figure 2: Micro-CT (X-ray Micro-Computed Tomography): schematic view of the process [6] (left), 3D volumetric image of a PVC foam (courtesy of Department MTM, KU Leuven) (right).
The VirtualCT process of the Simcenter 3D VMC ToolKit illustrated in Figure 3 is applied on a woven composite material. First, the acquired micro-CT volumetric image of a composite sample is split into sub-volumes (voxels) and analyzed for material components (segmentation) and local fiber orientations using the micro-CT data analysis software “VoxTex” (courtesy of Department MTM, KU Leuven) [7]. The obtained result is then imported into the Simcenter 3D simulation platform as a voxel rectilinear mesh with the evaluated material orientations using the VirtualCT tool. Afterwards, 2D or 3D periodic boundary conditions, tensile and shear loading cases are automatically created for the stiffness homogenization using the available functionalities of the Simcenter 3D VMC ToolKit. As a result, a material card with the elastic constants is automatically generated for the studied composite sample.Figure 3: Workflow “from micro-CT images to material properties” by example of a laminate manufactured from a 30˚-sheared woven organo sheet [5].
The potential of the Simcenter 3D VMC ToolKit for micro-CT-based stiffness homogenization for composite materials was illustrated in [5] by an example of thermoplastic woven organo sheets sheared to various angles: 15˚, 30˚, 45˚ and 60˚ (Figure 4, A). The goal of this study was to virtually assess the effect of shear on the composites performance (elastic constants). The sheared laminates were made of two consolidated plies of glass roving-PA6 (thermoplastic-based) organo sheets with a woven architecture (2×2 twill). The manufacturing process was defined and commissioned by inpro, Germany. One specimen for each laminate type was cut from the plates and scanned by XRE NV (now TESCAN XRE), Belgium using their UniTOM XL X-ray computed tomography system. Micro-CT images of the sheared laminates are presented in Figure 4, B. Afterwards, a set of high-fidelity micro-CT-based FE models was created using the VirtualCT tool in Simcenter 3D (Figure 4, C). The models captured the realistic variation of yarn orientation and the thickness of the produced laminates. The effective elastic properties were determined and compared with the existing results of tensile tests by inpro [5], which showed to be in a good agreement (Figure 4, D).Figure 4: X-ray computed tomography-based FE-homogenization of sheared organo sheets [5].
In summary, the Simcenter 3D VMC ToolKit does not only allow the creation of idealized models of composites, but it has been extended with a new functionality to build the realistic models of composites on modern image processing techniques. The new VirtualCT tool adopts the voxel-based approach by interfacing with the VoxTex software. The status of the work demonstrates the potential of the Simcenter 3D VMC ToolKit for stiffness homogenization for real composite materials starting from their micro-CT images. The presented modeling framework is applicable in a broader multi-physics context by combining the voxel models with FE-simulations of different disciplines for strength, damage, permeability, thermal etc. homogenizations.
Acknowledgements:
The work on Virtual Material Characterization (VMC) leading to this publication has been funded by the twin projects SBO & IBO “M3Strength”, which fit in the MacroModelMat (M3) research program, coordinated by Siemens (Siemens PLM software, Belgium) and funded by SIM (Strategic Initiative Materials in Flanders) and VLAIO (Flemish government agency Flanders Innovation & Entrepreneurship). O. Shishkina thanks VLAIO for financing her work in the framework of the Innovation Mandate Project “MicroCT-based Model Generation Engine for Virtual Material Characterisation” (Grant no. HBC.2017.0189). The authors also thank inpro for providing the reference test data for the tensile properties of the organo sheets.
References:
[1] L. Farkas, K. Vanclooster, H. Erdelyi, R.D.B. Sevenois, S.V. Lomov, T. Naito, Y. Urushiyama, W. Van Paepegem, Virtual material characterization process for composite materials: an industrial solution, in Proceedings of the 17th European Conference on Composite Materials (ECCM-17), Munich, Germany, 2016.
[2]N. Isart, B. El Said, D.S. Ivanov, S.R. Hallett, J.A. Mayugo, N. Blanco, Internal geometric modelling of 3D woven composites: A comparison between different approaches, Compos. Struct. 132 (2015) 1219-1230.
[3]S.V. Lomov, Modelling the geometry of textile reinforcements for composites: WiseTex, in: P. Boisse (Ed.), Composite Reinforcements for Optimum Performance, Elsevier, 2011, pp. 200-238.
[4]A. Vanaerschot, F. Panerai, A. Cassell, S.V. Lomov, D. Vandepitte, N.N. Mansour, Stochastic characterisation methodology for 3-D textiles based on micro-tomography, Compos. Struct. 173 (2017) 44-52.
[5]O. Shishkina, A. Matveeva, S. Wiedemann, K. Hoehne, M. Wevers, S. V. Lomov, L. Farkas. X-Ray computed tomography-based FE-homogenization of sheared organo sheets, Proceedings of the 18th European Conference on Composite Materials ECCM-18, Athens, 24-28 June 2018.
[6]O. Shishkina. Experimental and modelling investigations of structure-property relationships in nano-reinforced cellular materials, PhD thesis, Department of Materials Engineering (MTM), KU Leuven, Leuven, Belgium, 2014.
[7]I. Straumit, S.V. Lomov, M. Wevers. Quantification of the internal structure and automatic generation of voxel models of textile composites from X-ray computed tomography data. Compos. Part A Appl. Sci. Manuf. 54 (2015) 150-158.