The Expanding Simulation Needs of Engineers
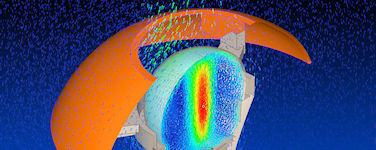
In modern product development, most everyone knows how important simulation is to successful design. Run analyses early to drive better design decisions. Run analyses late to verify performance. Do those two things and you should avoid multiple rounds of costly prototyping and testing. While most acknowledge the value that simulation can deliver, there’s still a lot of debate about how an organization can realize that value. Who should do what during which part of the design process?
For organizations that employ engineers with a wide array of responsibilities, the answers to that question is increasingly clear. The focus lies on enabling a multi-responsible engineer with the right tools at different stages of the design process. More and more, interestingly enough, the key enabler is not a single software application, but many.
Assessing Designs Early
The value of simulation early is well known. Run a quick analysis of each design change that an engineer explores. Watch how the performance of the design improves or worsens accordingly. This acts as guidance for more informed design decisions. When it comes to enabling engineers for this kind of analysis, key enablers include:
- Integration with CAD application as a means to propagate design changes.
- Automated meshing and easy application of loads and boundary conditions.
- Solves that strike the right balance between speed and accuracy.
- Fast visualization of simulation results.
Productivity, defined as quickly changing a design and running an analysis, is the goal here. Given that, simulation tools that are embedded or tightly integrated with CAD applications are the best fit. This empowers engineers to make quick changes to the design, propagate those design changes to the simulation capabilities or tool, and run a fast analysis. That, in turn, allows engineers to assess concepts and ideas, honing in on the right design solution.
Refining a Chosen Design
Once the engineer selects a concept or idea, the focus shifts to refining that design. This includes using simulation to scale geometric dimensions and other parameters. Ideally, the engineer will have information on which variables most directly affect performance against the many criteria that the design must satisfy. Overall, this equates to mapping the design space. Here, the key enablers include:
- Capabilities to run design studies, including optimization.
- Integration with CAD application as a means to automate changes to geometry.
- Automated updates to finite element mesh, loads, and boundary conditions based on geometry changes.
- Tracking analysis results for each design change that is explored.
- Solves more heavily weighted towards accuracy but still run fast.
- Visualization of design study datasets.
The objective here is markedly different from assessing design options early. The idea here is to determine the sensitivity of performance measures to design variables. This is commonly accomplished through automated design studies run autonomously by the software application. The best simulation solution for this job might be embedded with a CAD application, might run independently, or even be a simulation automation suite.
Validating Final Performance
In this last stage of simulation use before prototyping and testing, accuracy becomes paramount. This is the last step before a company invests an organization’s money into physical prototypes and a team’s time into running tests. The overarching goal is to pass that prototyping and testing stage the first time. In this context, the following capabilities are crucial to any enabling solution:
- Connection with CAD applications to open 3D models.
- Fine control over a simulation model’s finite element mesh.
- Granular command over a simulation model’s loads and boundary conditions.
- Selection of solvers and methods.
- Access and ability to change solver parameters
- Power over the options that control visualization of analysis results.
The goal here is straightforward: obtain extremely accurate results and validate compliance to requirements. The best solution for this application of analysis is dedicated pre-processor and post-processor applications. These tools provide a full range of controls over a analysis model’s mesh, loads, boundary conditions, solver selection, solver parameters, results visualization and more.
Implications for Engineers
For some time, the simulation-driven design movement has heavily emphasized CAD-embedded simulation tools. While these tools are a good fit for assessing designs early and perhaps a fit for refining a chosen design, they are decidedly not the right solution for validating final performance. For some, the idea of exposing anything but a CAD-embedded solution to engineers represents a risk, either in misuse or loss of productivity. However, this concern is often misaligned with reality.
Modern engineers are inherently problem solvers. That trait not only applies to finding design solutions that address requirements but also to address their own process obstacles and bottlenecks. The desktops and laptops of today’s engineers are often littered with a variety of tools they have uncovered that address a specific problem. Engineers are used to cobbling together their own tools into a larger process. The same applies to using multiple simulation tools during different parts of the design process.
At the start of design, while assessing designs early, engineers can use CAD-embedded simulation tools to explore different concepts and ideas. In the middle, while they are refining a chosen design, the might leverage a simulation automation suite. At the end, while validating final performance, they can rely upon an independent pre-processor and post-processor application. Engineers are resilient enough to learn and use many software tools. In fact, they have been doing it for years.
Recap
- At the start of design, engineers need tools that allow them to explore and analyze design concepts and ideas.
- In the middle of design, engineers need tools that automate the assessment of the design space, revealing which variables most directly affect performance variables.
- At the end of design, engineers need tools that simulate the performance of designs with a high degree of control over the model and solve.
- Today’s engineers cobble together a variety of software applications to streamline their own process. It is not a burden to allow them to use a variety of analysis tools, each of which is good fits for different parts of the design cycle.
Alright, folks. That’s my take. Would love to hear your feedback in the comments.