How simulation pushes robotic systems to their physical limits
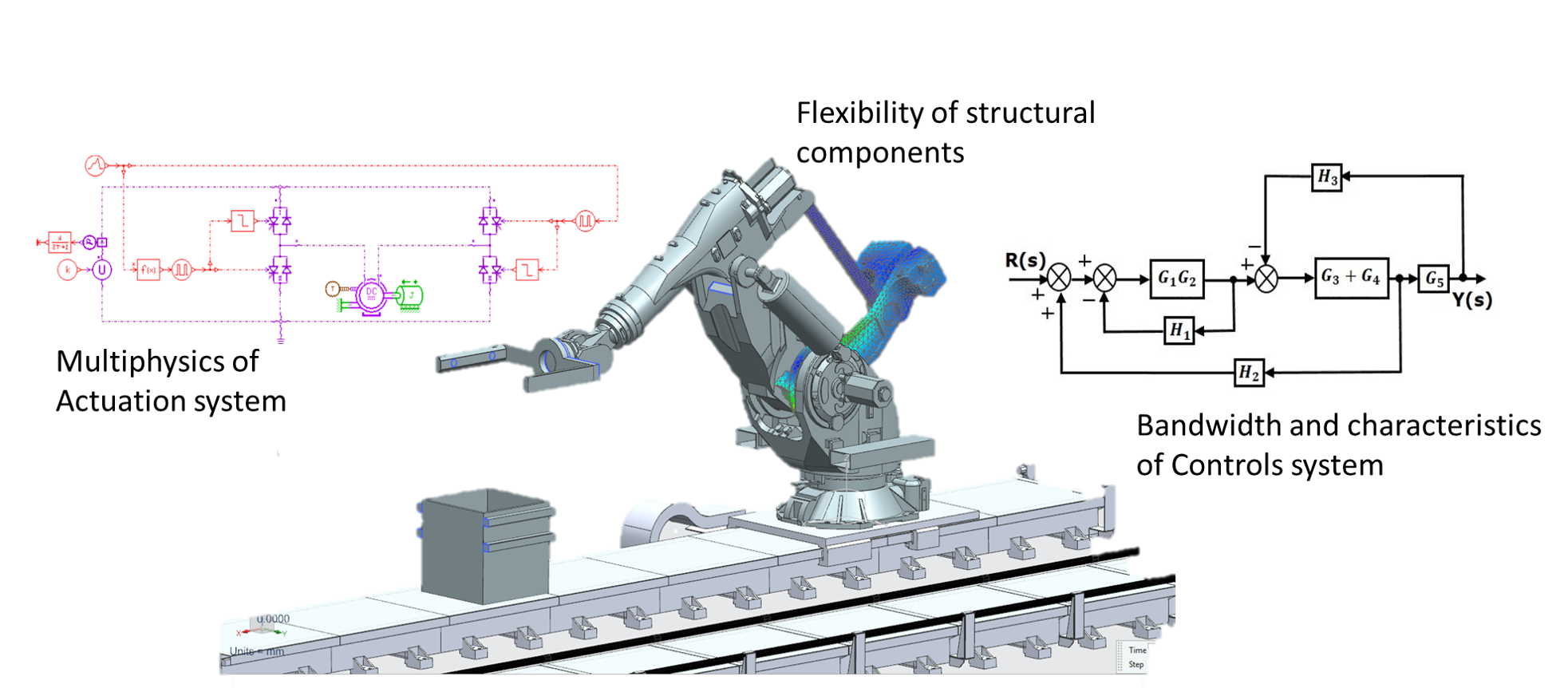
Robots are revolutionizing industries, but pushing them to their limits without compromising safety is a challenge—here’s how companies are modelling and analyzing robot behaviour using simulation!
As Machine Learning and AI take center stage in engineering, today’s scalable electronic control systems can handle a multitude of sensors and input data to perform complex tasks. Trends like collaborative robots and autonomous systems are becoming the norm, from shop floors to nursing homes.
The Challenge: Maximizing Performance, Durability, and Safety
How can we push these systems to their physical limits while ensuring durability and safety? It’s like finding the perfect balance between speed and stability – think of a tightrope walker carefully adjusting their steps to maintain equilibrium.
Balancing performance through Simulation
Just as the tightrope walker relies on practice and precision, engineers working on robotics can use simulation to find the optimal balance between performance and safety in robotic systems. By simulating robotic systems, we can optimize performance, reduce downtime, and increase productivity. Let’s look at the automation of production and industrial processes, where time is money. Take, for example, a pick-and-place robots. How can simulation help us develop such systems?
Multi Body Simulation
Kinematics are the first thing to assess, e.g. avoiding collision with other objects. But in addition, what defines the forces acting on the structural components? How can those can be designed and sized accordingly? One way to look at this is Multi Body Dynamics(MBD). The animation above shows the result of a simulation. Each component of the machine is represented by its mass and inertia. The model takes into account gravity, external forces (like the weight of the box) and the kinematic degrees of freedom.
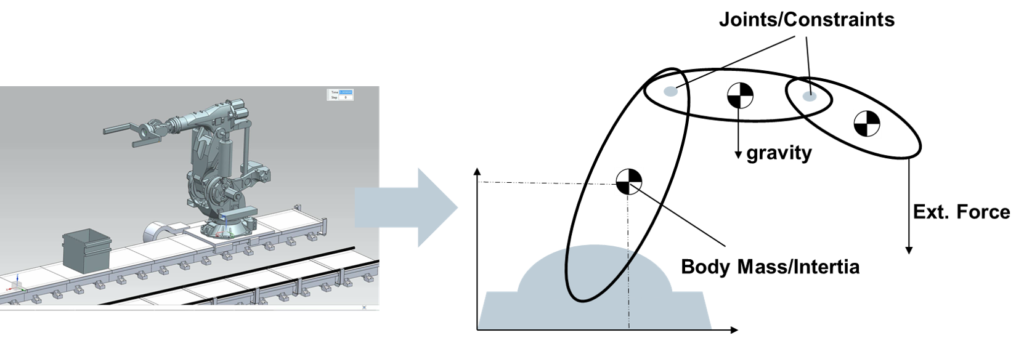
While this is a big step forward, we can increase fidelity further in order to get full information. The forces on the components increase, when we perform the movement faster.
How fast can this movement actually be performed in the simulation? I am glad you asked.
Actually, the bandwidth of the actuators and the control logic of the robot define this limit. With co-simulation, the MBD model “cooperates” with a controlled Multiphysics model of the actuation. At simulation run-time two (or more) solvers exchange information. For example: The MDB solver gives positions and accelerations to the controller/actuation, while the Multi-Physics solver responds with corresponding forces.
Lastly, performing the operation faster leads to more dynamic or abrupt movements. Components will start to deform or vibrate. These effects can be considered in the MDB model as well.
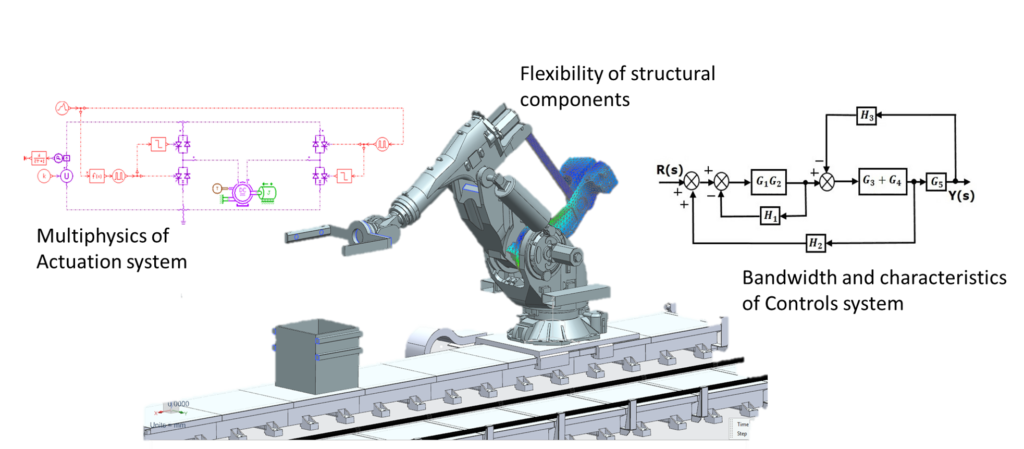
Such a simulation model gives valuable insights into the loads and operational conditions at every location of every component of the robot in order to optimize the structure and ensure durability. Take the example of controller failure below:
Related use cases
The same principals apply for many systems, e.g. the dynamics of controlled + actuated flight simulator platforms. In the following video E2M Technologies sheds light on how they use Simcenter 3D and other Siemens tools for various analyses of their platforms, e.g. the assessment of movement under actuator constraints to prevent collisions or the stress analyses of components.
So far, so good – for stationary systems in a defined environment. A previous blog covered how Aucma built Intelligent disinfection robots made with NX to help fight the virus. It is crucial to reflect on the tasks a robot is designed for.
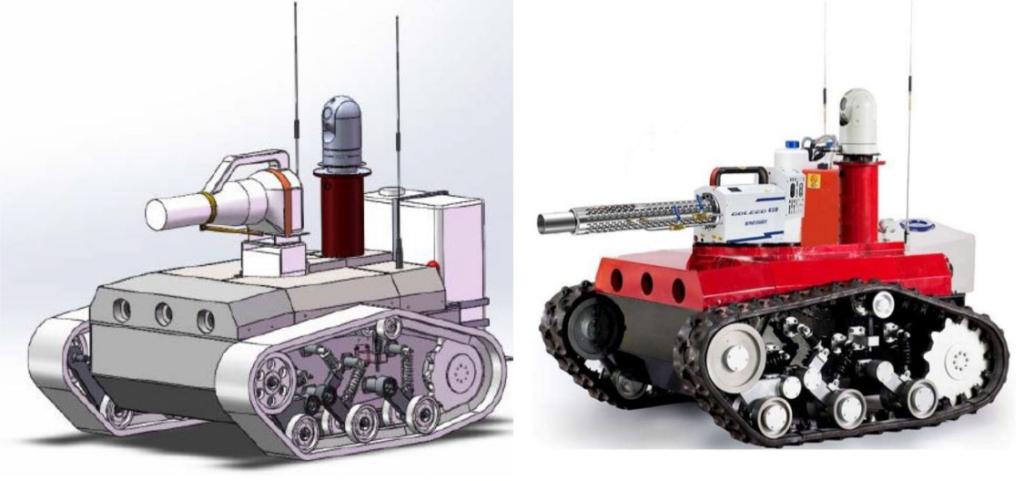
Creating virtual models representing real operational conditions helps to do just that. So while the disinfection robot operates on level building floors, other robot drones might encounter different terrains, like a rescue drone:
Conclusion
Whatever your robot might be up to: Simulation models of the dynamic system help ensure safe and lasting operation, considering all relevant aspects. There are, of course, more challenges to robotics engineering, such as energy efficiency or actuator sizing. It is the combination of simulation and engineering disciplines, which constitutes a Holistic Digital Twin. See my colleague’s blog for more on System Simulation for Robotics: https://blogs.sw.siemens.com/simcenter/robotics-engineering/
Listen to our free robotics webinar to learn many additional aspects : https://www.plm.automation.siemens.com/global/en/webinar/robotics-engineering/88189
There is one last thing. Do you know why your caged robots tremble and how to overcome it? You can read the following blog, which highlights vibration troubleshooting and characterizing unwanted resonance.