Drop test simulation for coping with clumsiness
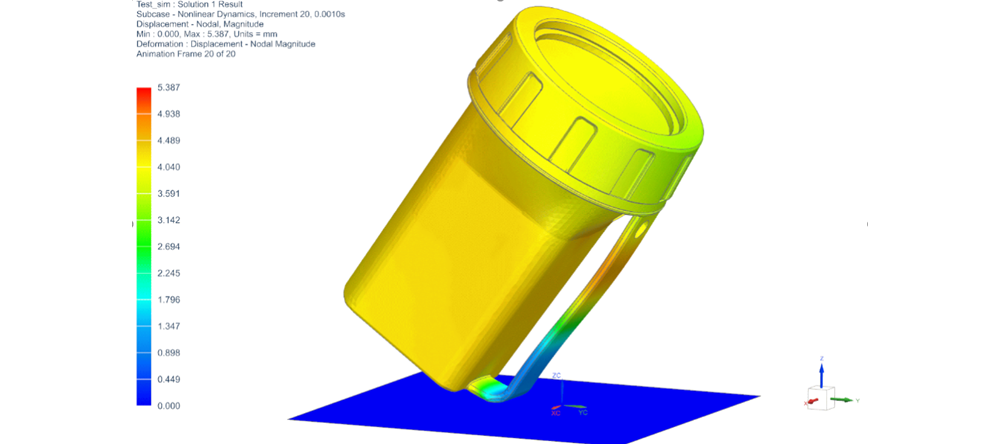
Simcenter 3D has you covered!
Who doesn’t know something like this from personal experience?
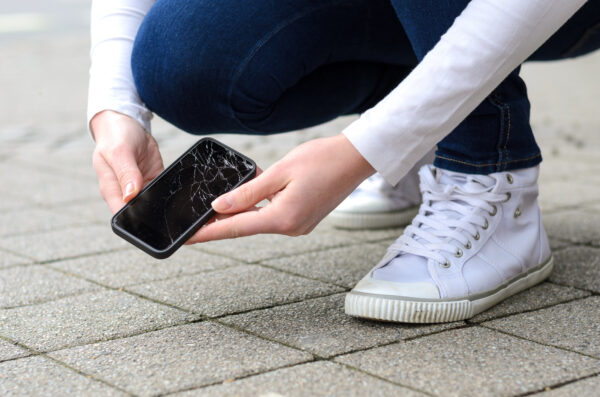
Walking down the road in a hurry, the phone is buzzing and suddenly … – a few hundred dollars are gone and at least the next couple of days are ruined. ☹
Mobile phone companies have done their homework to improve the situation: Protective glasses, special cases & covers and also more rounded designs.
In this blog we would like to take a look behind the scenes of development of consumer products and electronic devices. In that context, drop tests are a crucial engineering aspect in the design. In all industries this engineering domain has evolved from pure testing to more and more simulation-based evaluations. While it used to be a discipline for dedicated experts only, let us take a look, how today you can more easily use drop test simulation during the design phase in order to predict and mitigate what happens when things do happen to fall down.
Virtual Drop Test
Let us take a flashlight as a classic example of a product prone to dropping:
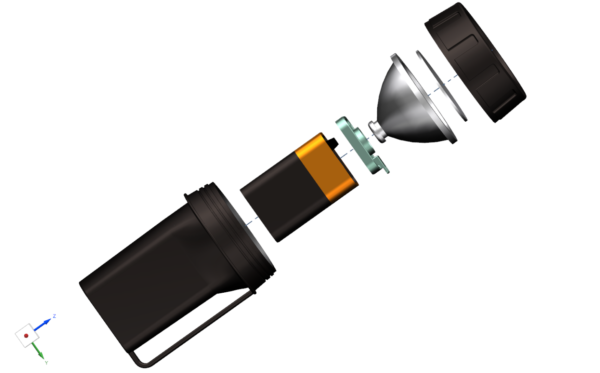
Drop Test Simulation for Designers
In the past – in order to perform a finite element simulation – an expert analyst would have to manually walk through the steps of finding and cleaning up the geometry, seed and mesh the parts, define boundary conditions for the simulation, perform the solve and iterate.
However, Simcenter 3D has created a dedicated and automated drop test simulation process so that these steps can be transformed into a guided and streamlined process by engineers who are less experienced in drop test simulation methods.
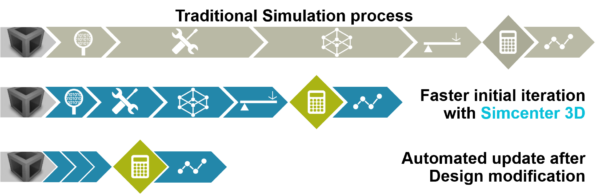
Dedicated Drop Test App
Let’s have a look at this in practice with a customized DropTest-App. The user is actually guided through the four main steps of the process from CAD preparation, via Meshing and Simulation to Postprocessing. Let’s see this step by step:
Step 1: CAD preparation
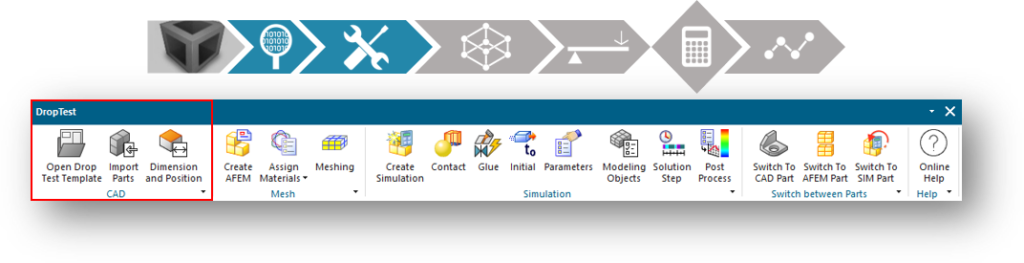
The first task it positioning the lamp and define in which angle it will hit the ground.
Step 2: Meshing and model preparation
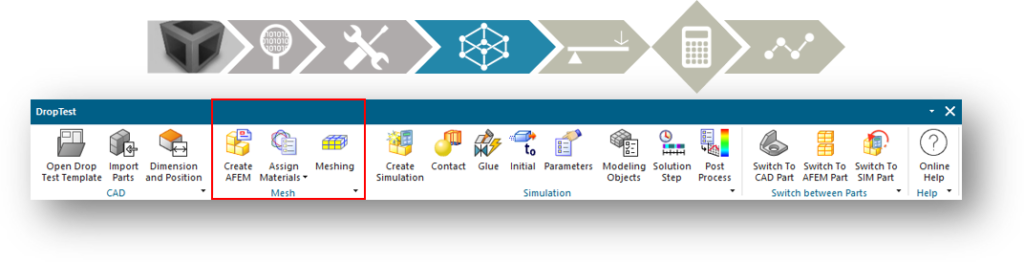
With the flashlight in place and ready to drop, all components now need to be meshed, which in essence can be automated to the most extend: Only the most relevant inputs are necessary in order to mesh all components and automatically create the full assembly-level Finite Element model.
Step 3: Simulation
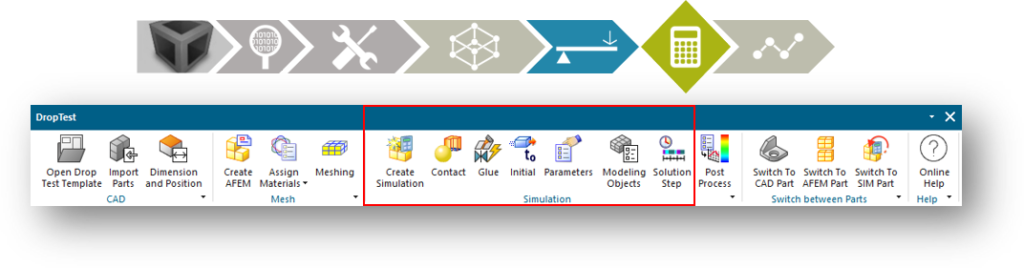
With the model in place, now the simulation can be set up. Based on simple selections the contact areas are defined and adjusting the height will compute the corresponding impact velocity.
Step 4: Postprocessing
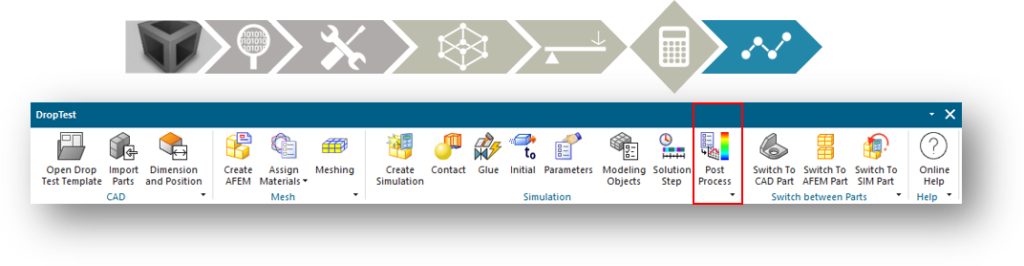
After the simulation is completed, the Drop Test App helps to qualitatively and quantitatively assess, whether the drop leads to critical vibrations, stresses and deformations:
Visually inspecting the results is handy and delivers immediate guidance for design improvements. Given the wobbly vibrations in the handle after impact, it is obvious there has to be a better way.
Design modifications and model update
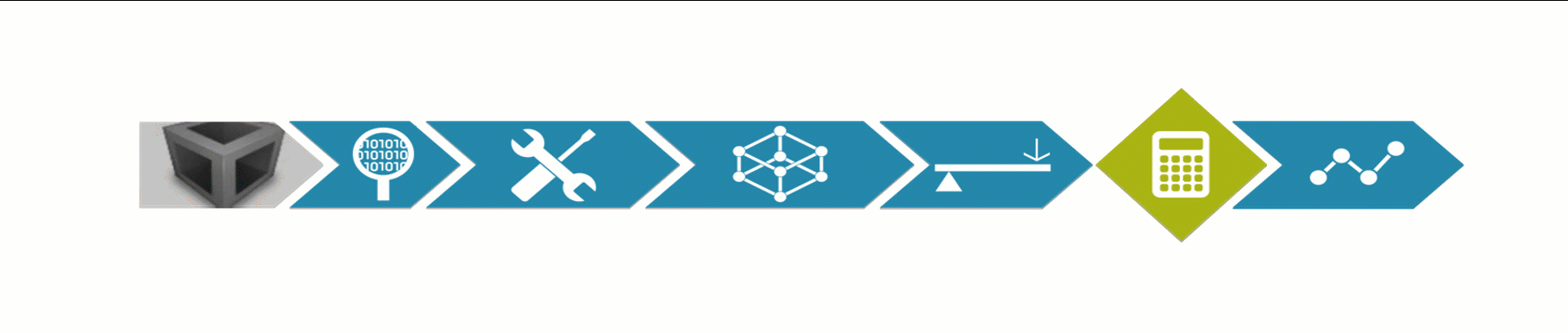
Let’s introduce some changes and see, how this impacts the results.
Conclusion
Capturing expert knowledge in smart processes with a strong focus on automation of otherwise manual work, enables product designers to perform tasks, which in the past would have required dedicated simulation experts.
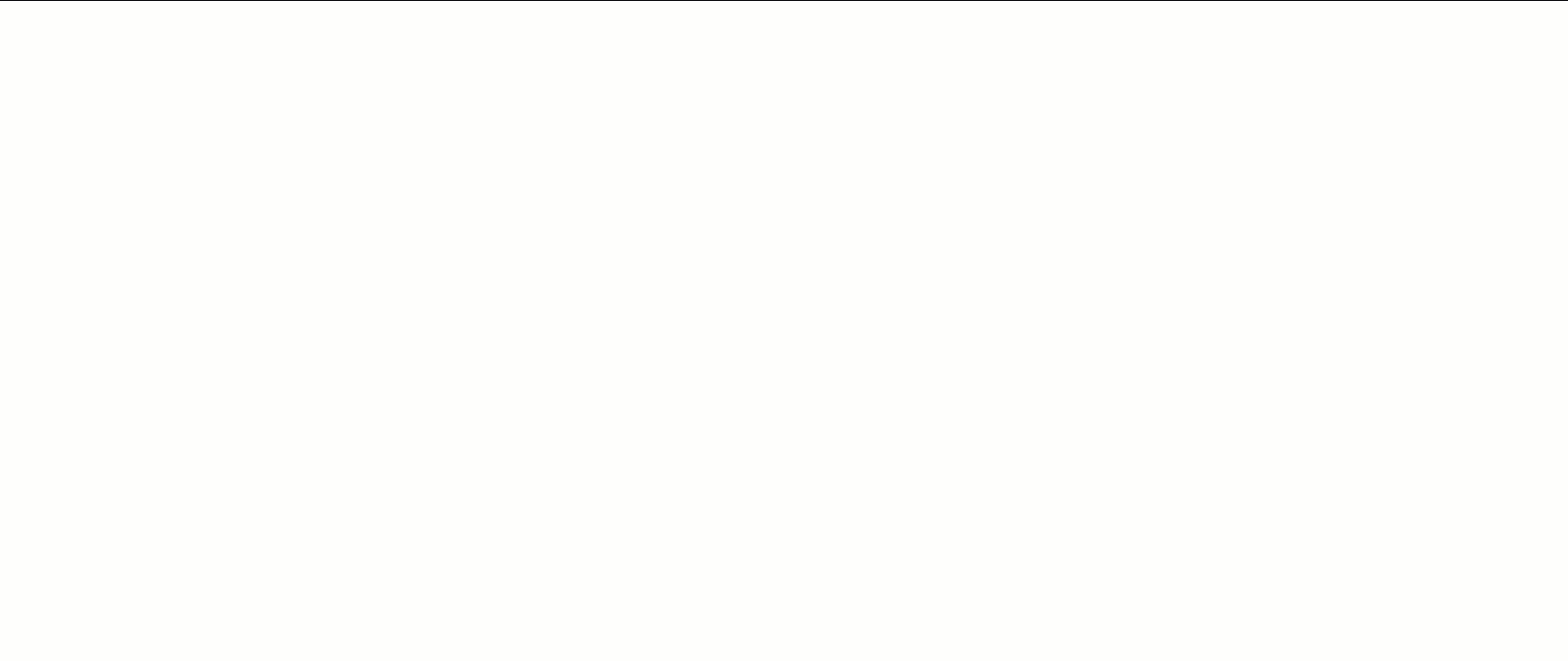
Taking insights from drop test simulation helps among other things to identify weak spots in the design and verify improvements very early, prior to building and testing prototypes.
The application ranges from handheld devices, consumer electronics to all devices, which happen to drop.
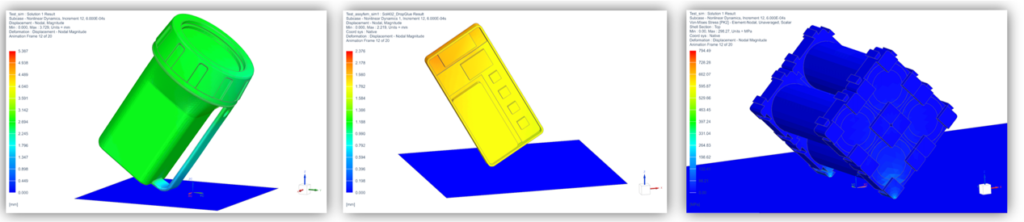
So, next time, when you drop your remote control and the battery compartment does not break take the time to appreciate and celebrate with us the engineering going into that. 😊
For more information on Simcenter 3D
- Simcenter 3D Droptest Application
- Learn What’s New in Simcenter 3D 2022.1 on January 11, 2022
- Simcenter 3D Solution Guide
- Free Trial: Try Simcenter 3D online today for 30 days
- Visit Support Center to download the latest version of Simcenter 3D or contact support
- New customer? Contact us to discuss further