CNC lathe development: cutting the simulation time in half
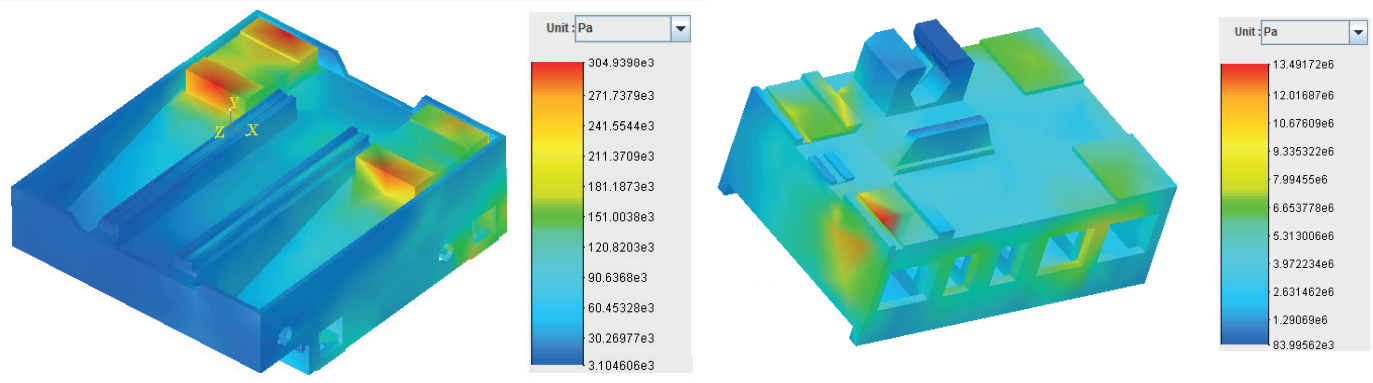
To become a pioneer of Industry 4.0, industrial machinery manufacturers need to develop innovative products with maximum performance and minimum operational cost and downtime. They need to provide the best possible accuracy, and at the same time comply with ever stricter standards and regulations. Apart from the environmental aspect, this also concerns safety and reliability. This strongly relates to the overall vibration behavior of a design, as strong vibrations can lead to structural damage and even to life-threatening situations.
Shenyang Machine Tool Co., Ltd. (SMTCL), a Chinese machine tool manufacturer, designs and produces Computer Numerical Control (CNC) lathes. Engineers at SMTCL realize very well that analyzing and refining machines using trial-and-error will not be sufficient to keep them in the race. They use simulation technologies that help make right decisions in the early design stages and deliver higher product quality on the first attempt. This drastically reduces the total development cycle, saving time and money.
With LMS solutions from Siemens PLM Software, SMTCL found the most complete offering that covers all steps of the entire process. Those align multi-domain system simulation, detailed 3D analysis and test-based engineering into a streamlined development process from concept modeling to physical prototype evaluation. Merely by using LMS Samtech Samcef, that combines the finite element method (FEM) with multibody modeling, SMTCL engineers could get a higher simulation accuracy then before in only half the time. They now plan to include electronics and controls in simulation, and take the next step in intelligent machinery development.