A bright future for controls engineering
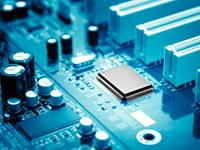
Very seldom do you run across a modern product or system that is purely mechanical. Even the most basic item, like a lawn mower, a power tool or a dishwasher has something “smart” or mechatronic about it today. But how do you go about designing a mechatronic system? And, even more importantly, how do you design it right the first time?
This is one of the principle challenges that engineers face today. How does one get the mechanical design aligned to the electronic control systems and software to meet a variety of performance targets? Lucky for us, it seems that control systems expert and director of MBSE (model-based systems engineering) solutions for Simcenter Engineering, Dr. Shiva Sivashankar, has the answers.
How do you go about designing a control system?
The first step is to understand the requirements. You can design a control system that can meet multiple objectives, but it is important to understand the different objectives and the interactions. How fast should a product react to change in the system? What about a change in external conditions?
You need to get a big picture view. Some of the requirements could set performance goals, which have to be optimized, while others serve as constraints to be satisfied. Some of these requirements can be competing against each other and the design should carefully trade off between competing requirements.
After you understand the requirements, what’s next?
Then we draw out a boundary diagram of the system architecture. What are the components of the system that can be measured by sensors, and which system properties can be changed by actuation to satisfy the requirements? At this point, we do a requirement feasibility analysis to see if the existing sensors and actuators can actually meet the system objectives. Such analysis is mostly done today using system simulation with computer models. Examining the analysis results, we can see if the conceptual system architecture is really possible. If yes, we start a detailed design.
What do you actually mean by “detailed design?”
We start by dividing the controller into units according to the required functions. When designing an engine control system, for example, we have to make sure that we are delivering the required torque. To do this, you design a torque management function that “measures” the torque demand through the driver accelerator pedal input. Then this is translated into appropriate airflow and spark-timing actuations to deliver the demanded torque at the engine crank shaft.
In parallel, you look at the fuel management function that seeks to minimize fuel consumption while delivering the required fuel to generate torque. The emission control and thermal management functions also impose constraints on how the airflow, spark timing and fuel system are actuated to ensure that exhaust emissions are minimized and the engine operates in an efficient temperature range. It is a bit like completing a 10,000 piece jigsaw puzzle.
What is the next step?
To realize the control system within the overall architecture, we start to define the interfaces and populate the various system functions to fulfill requirements. Today, computer models of the controller units are built to virtualize the functions. The units and their interfaces are rendered graphically to assist the engineers in rapidly evolving design processes. In parallel, we design and implement test cases to make sure that the control system works and meets requirements. This is called validation and verification or V&V.
So this early in the process, you test?
Absolutely. Early verification and validation is critical to a product’s overall success. So we design and then we test in stages. Testing at this stage can be done in various ways. The classical method was to use hardware. When I started in the field many years ago, we would make some changes to the control software and then take it to the product and test it, but this was very expensive and took a lot of time. Today, we are moving toward model-based systems engineering and “real world” virtual prototypes.
You virtualize the physical system that you are trying to control and you virtualize the control system. Then you apply the virtual control system on the virtual system prototype. This is all done on the computer using models and then you run the test cases on the virtual product to verify if the requirements are being satisfied. Engineering such virtual products with sophisticated control systems and then testing them in the virtual world without creating physical design prototypes will become common in the future.
Are there specific solutions for certain industries?
The beauty of controls engineering is that the principle steps and the methodology remain the same across all industries. The concepts can be applied across the board. Many ideas that we have pioneered and innovated in the automotive segment can be easily transferred to other sectors like industrial machinery, off-road or ground vehicles and consumer electronics.
Where does the Simcenter controls expertise fit into the bigger picture of Siemens PLM Software?
As part of Siemens PLM Software, we will have a great opportunity to expand into a variety of exciting industries from energy to high-speed trains. It is an excellent feeling that, in our own way, we can contribute to the bigger product sustainability picture. I think we can help solve some critical controls engineering puzzles and help take controls engineering to a different level.
Interested in knowing more about Simcenter solutions for controls engineering?
Read the Simcenter solutions for Controls development, verification and validation fact sheet