Accurate Maintenance Forecasting With PLM-based SLM
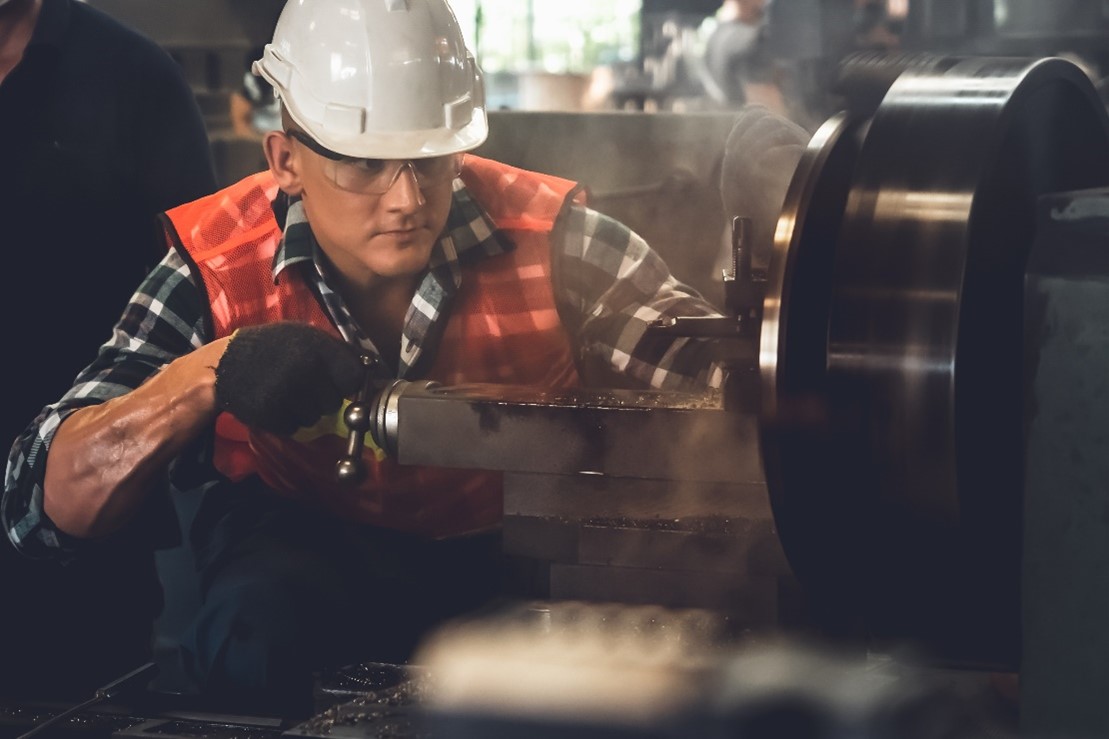
Maintenance forecasting leveraging a comprehensive digital twin
Need to get a better handle on maintenance forecasting for your complex products? Read on to learn how a PLM-based digital twin with integrated service lifecycle management can help you save time and money in your maintenance activities, while gaining customer satisfaction.
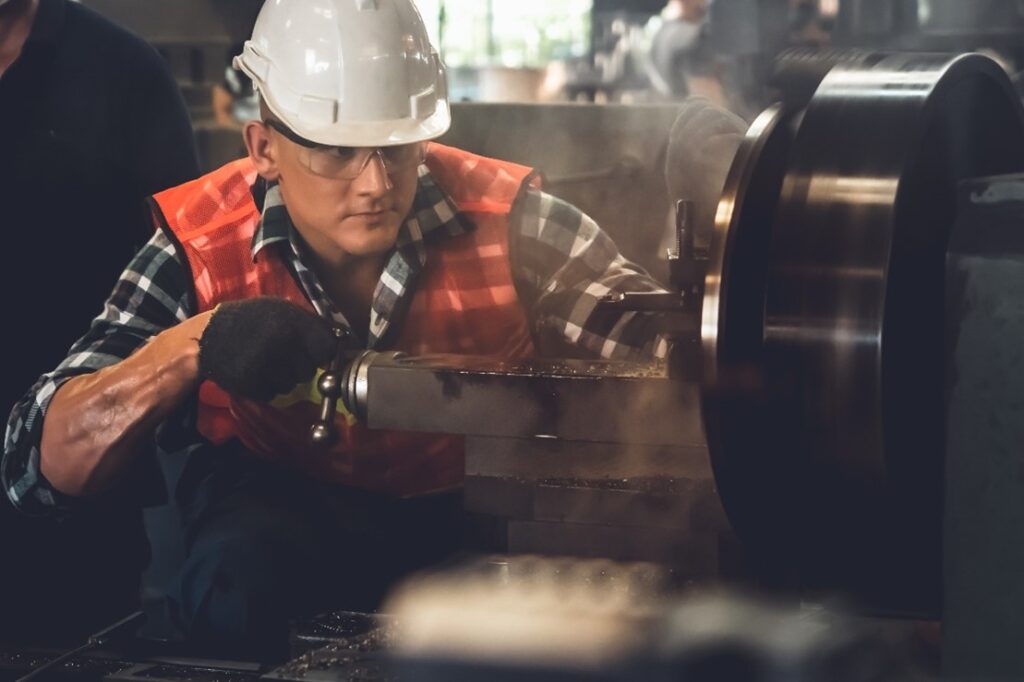
For increasingly complex products, maintenance forecasting must be accurate for fielded assets to avoid downtime and increased costs. Having the right maintenance forecasting tools in place, you can equip your service planners and service teams with the right information and resources to improve service and maintenance efficiencies, while lowering costs and increasing customer satisfaction.
Integrating maintenance forecasting with a comprehensive digital twin that uses core product lifecycle management (PLM) capabilities such as intuitive search, BOM and document management, workflow, and visualization helps you eliminate data silos between functional domains, ensuring efficient and accurate maintenance forecasting, with a tight connection between product design, manufacturing, and service activities. Planners gain visibility and access to data in the right context across the entire product and service lifecycle. This will help avoid excessive time spent searching for information related to an asset and its maintenance requirements. Working smarter and faster in the maintenance forecasting space leads to positive downstream outcomes – like reduced errors in the field, increased asset performance, and happy customers.
Benefits of Effective Maintenance Forecasting
With effective maintenance forecasting, you have a clear understanding of the serialized physical asset, its service requirements, and required resources to maintain it. This helps you ensure proactive service planning, and increases your potential of service profitability. With visibility into the current physical asset configuration of the product, you know exactly what parts will need to be maintained and the skill sets required to maintain them. For example, do we need to send a maintenance person with a special certification? Do we have the right spare parts define for the job? Do we have the service records and usage data? Do we have insights we can leverage from past maintenance activities? This information is key to ensuring effective forecasting.
Teamcenter Service Lifecycle Management (SLM) for maintenance forecasting provides capabilities to effectively plan for maintenance.
Maintenance Forecasting with Teamcenter Service Lifecycle Management
With an intuitive Teamcenter user experience, you benefit from complete visibility into your asset maintenance initiatives – current and future. For example, a maintenance supervisor can open a representation of a physical part in Teamcenter and view its maintenance due dates, frequency, and status. With Teamcenter, information related to service planning, service requirements, and execution of service is available in a single environment. This helps you to be more proactive in maintenance capacity planning, and reduces your risk of errors.

Teamcenter SLM provides flexibility on how you view your service information. Service requirements, for example, can be viewed for a selected part, or all levels of a part. Each view provides the associated service requirements of a part, its frequency, and the status of the service. Teamcenter SLM also facilitates confident planning of upgrades, provides timely instructions for issue resolution, provides visual service documentation, and optimizes spare parts inventory leveraging accurate asset knowledge.
Learn more about Teamcenter Service Lifecycle Management (SLM)
Hear how Siemens customers leverage Teamcenter SLM for success
Start a free 30-day software trial to explore Teamcenter SLM today
Watch the video to learn more about the role of SLM in service excellence