Service Engineering: Improve Outcomes with Service Events
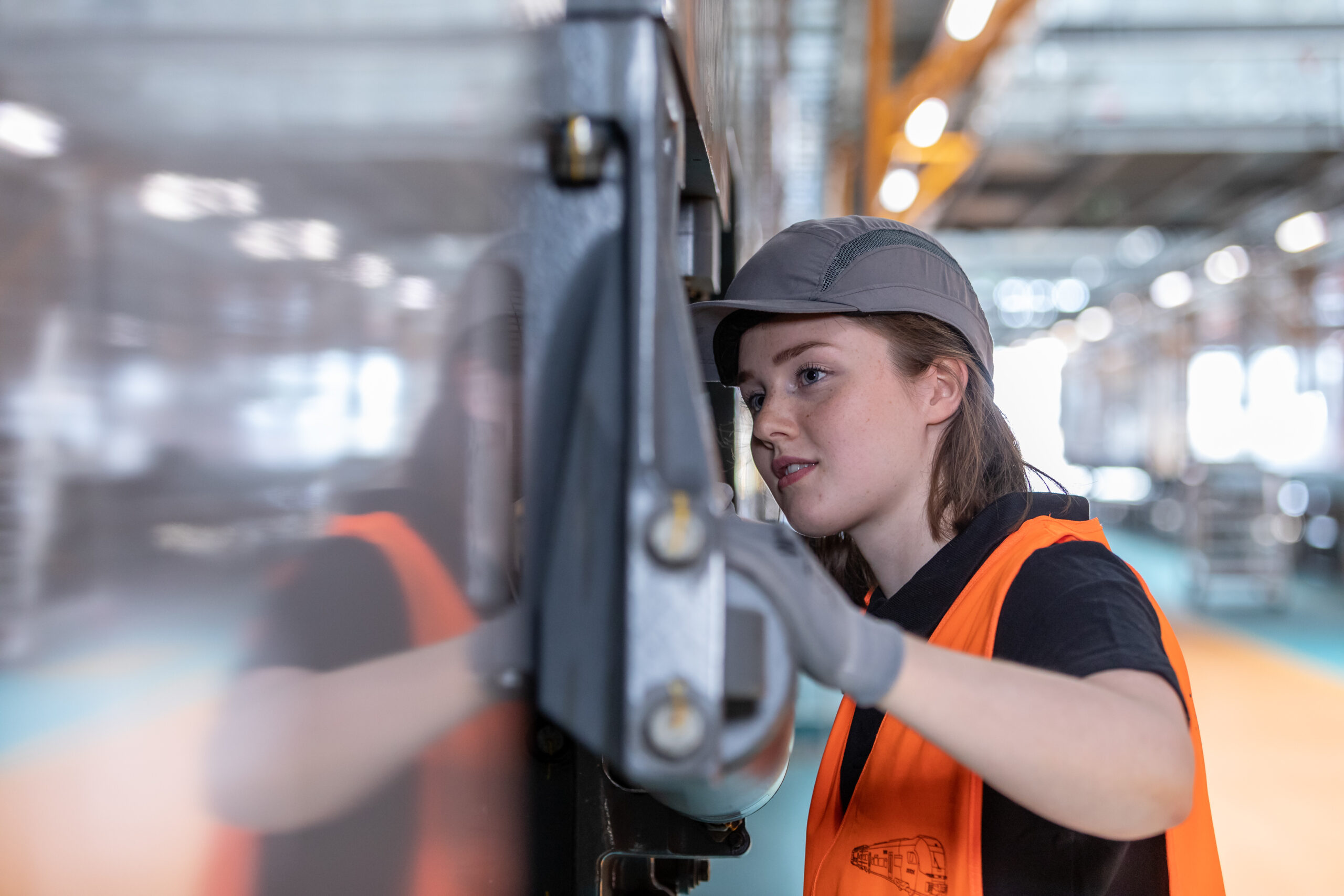
Learn more about using Service Events in Teamcenter to capture physical structure configuration data and changes, to improve your service engineering outcomes.
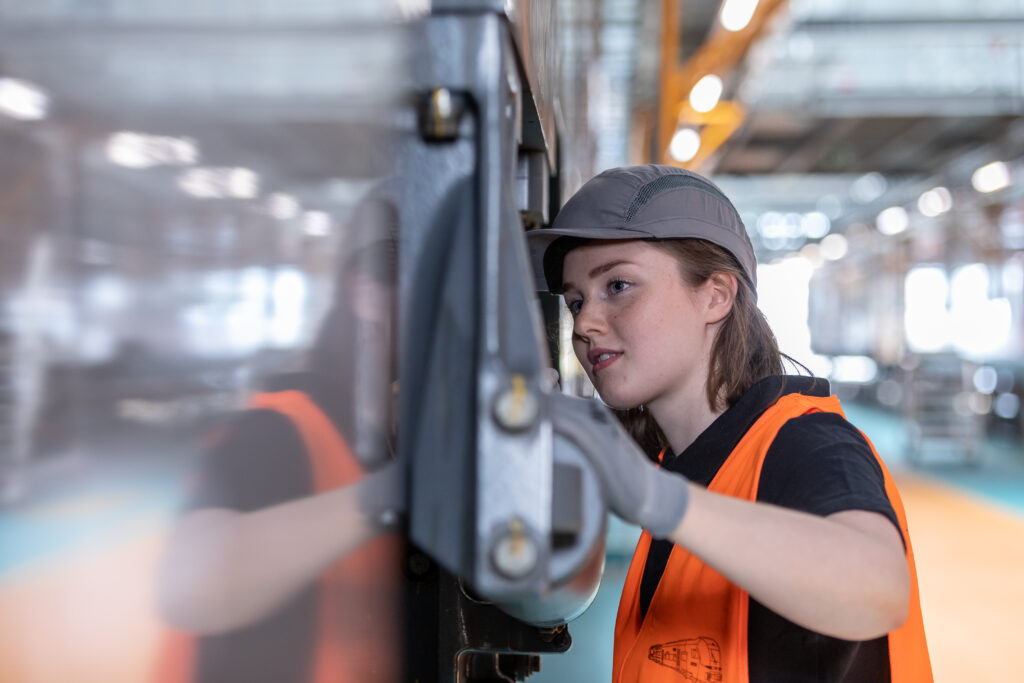
Efficiently tracking service engineering activities can help you avoid costly mistakes, and help you make better decisions around your current and future service needs. Just as maintenance forecasting benefits your business by saving you time and money, tracking maintenance activity and recording changes to physical assets is equally important, and can positively impact your business.
Address Service Engineering with Service Events in Teamcenter
Teamcenter Service Lifecycle Management or SLM, helps you address your service engineering needs, such as tracking physical assets and their current configurations, and service planning. It also integrates to operational aspects of service, and is able to track service activities such as usage, configuration changes, and upgrades of physical parts, along with reporting discrepancies and asset characteristics. Maintenance activities that happen outside of Teamcenter, are tracked using Service Events in Teamcenter. With Service Events, maintenance activities are tracked and recorded, giving visibility to impacts on the configuration of the physical asset. Service Events can also be used as light weight execution systems, eliminating the need for duplicate data re-entry into other stand-alone systems. Service Event management in Teamcenter can help you more accurately project order delivery dates, and make better decisions.
- Service Events capture information such as the service type, work scope, resource information, maintenance time, and cost
- Service Events are used to track the service history, and the impact on the configuration of the physical asset managed in Teamcenter
- Service Events can capture any kind of activities such as inspection, repair, overhaul, etc.
Service Technicians can create Service Events in Teamcenter to represent service activity such as oil changes, battery replacements, filter replacements, etc. For example, let’s use the scenario of a Service Technician assigned to inspect a pump. In Teamcenter, the Technician will create a Service Event item of type Inspection on the physical asset representation of the pump. He or she adds all the related information in this Service Event, including information like: when the Service Event is started, when it needs to be completed, the type of Service Event, the location where it is performed, the purpose of the event, and the cost of material and labor.
If there are multiple Service Events, they can be grouped into a single Service Group as per different Service Event types. This will allow better organization of the Service Event.
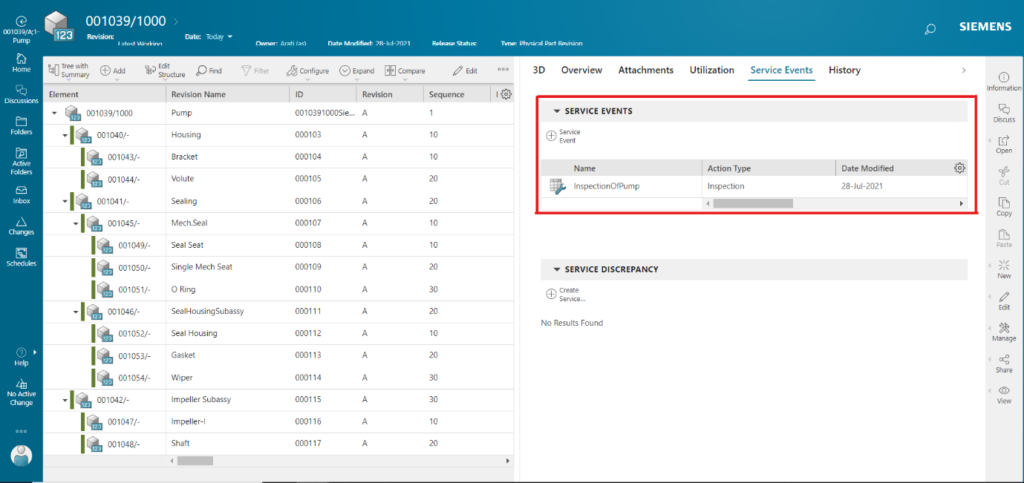
Interested in learning more about Service Lifecycle Management and how it can help you reduce risks?
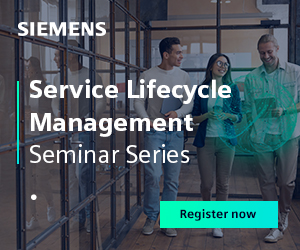
For a complete list of Service Lifecycle Management virtual seminars and dates, go here.
Service Discrepancies and Activity Entry Values
Irregularities that are observed while performing service activities of assets or physical parts are defined as Service Discrepancies on the physical asset representation in Teamcenter. Any failures identified with physical parts are also defined as Service Discrepancies.
To record irregularities observed while executing the Service Event, a Service Discrepancy can be created. This Discrepancy is created with respect to the Service Event being executed. For example, while executing a Service Event of a pump inspection, an irregularity such as low water flow rate is found. This is captured with a Service Discrepancy item in Teamcenter, with respect to a Service Event being executed.
You can also create Discrepancies to record failures observed on the fielded asset. This Discrepancy is created with respect to the fielded asset. For example, a dent found on the pump before executing any Service Event can be captured as a Service Discrepancy with respect to pump.
A Service Discrepancy may contain the Fault Code, which is used to identify problems that occurred with an asset.
Based on the information in the Service Discrepancy, a Corrective Action must be created to resolve the Discrepancy.
A record of characteristic values, part movements, and part request as a part of Corrective Action – are used for resolving the Service Discrepancy.
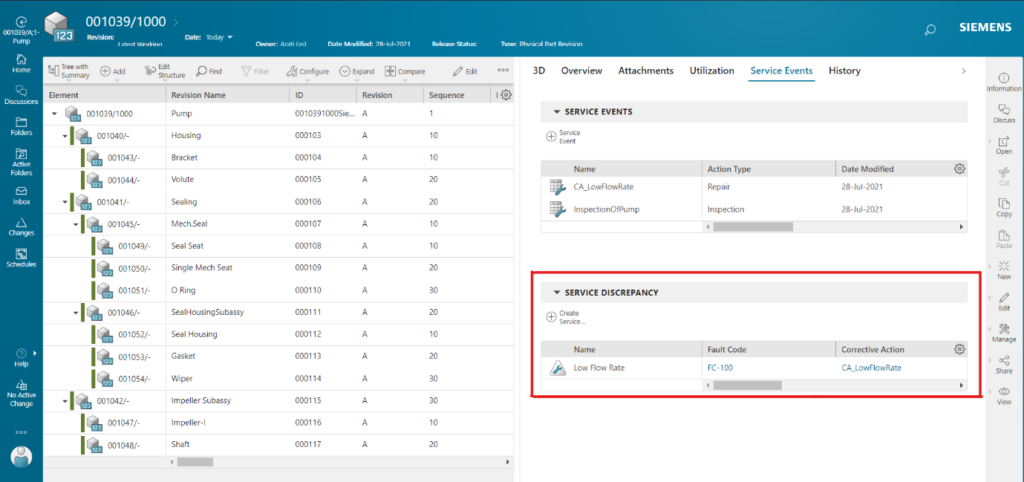
Characteristic values recorded for Service Events are called as Activity Entry Values. Life, date, and observation characteristics can be recorded as a part of Activity Entry Values on Service Events. Characteristics defined on an item in a Service BOM (SBOM) are available for recording during the execution of a Service Event on the specific physical part. At this point they are not applied on physical parts. These values are recorded on the physical part once the Service Event related to the Activity Entry Value is approved.
Part Requests
Part Requests are created by Technicians when they require a specific part during the maintenance procedure. An authorized person, like a Supervisor, can approve/close this request to have the part issued to a Technician.
Any tool, replacement part, or material required for the maintenance procedure can be requested as a Part Request.
Part Requests can only be created on Service Events or Corrective Actions. Another important point is that the Part Request is the interface point from Teamcenter to the inventory system. It can be used to issue the part from the inventory system. A Part Request can be marked as closed or rejected/cancelled depending on the availability of the part/resource being requested, or the correctness of the request. When a Service Event/Corrective Action related to a Part Request is approved, it will subsequently close the Part Request.
Part Movements
Installation, uninstallation, or replacement of parts in an asset are some of the Part Movements which can be captured through Service Events/Corrective Actions. In the image below, Part Movement for replacing the O Ring is captured on the Corrective Action of “Low Flow rate” Service Discrepancy.
Changes recorded on physical assets as a result of Part Movements are reflected on physical assets, once the corresponding Service Event or Corrective Action is approved. In the example of replace O Ring, approving the Corrective Action will replace the existing O Ring part with its alternative part.
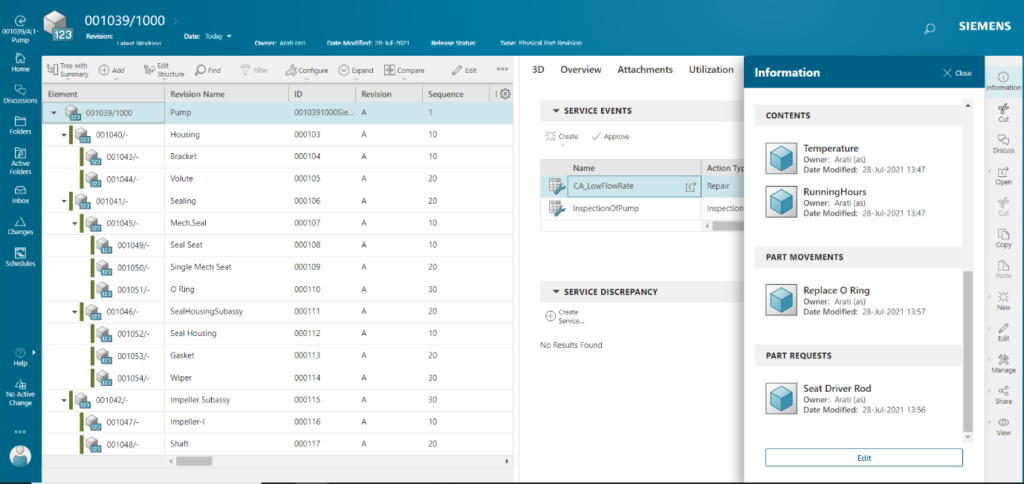
Install Part Movement updates the asset with a new or existing physical part into the asset. Uninstall Part Movement removes the physical part from the asset. Replace Part Movement removes the part and installs new or existing physical parts into the structure to which the Service Event/Corrective Action is related.
Part Movements can be categorized as traceable and non-traceable Part Movements. If the Part Movement is marked as traceable, then only it will update the physical structure. Changes recorded as a result of traceable Part Movement are applied to the physical asset after the approval of related Service Event/Corrective Action.
When a Part movement is untraceable, it will not lead to change in the physical asset, but it is mainly aimed to record the event happened on the asset. Such part movements are targeted for non-traceable parts not included in the asset/physical structure being tracked in Teamcenter. For example, if rivets are non-traceable parts, Part Movement can still be defined for those parts. Since rivets are not included in assets/physical structures in Teamcenter, such part movements will not lead to a change in the physical structure, however, the event would get recorded in Teamcenter.
Service Event and Corrective Action Approval
Service Events can result in the creation of one, or multiple workflows in Teamcenter. Workflows notify key stakeholders of items to work on, and review for approval. Once the Service Event is approved in Teamcenter, the asset/physical structure managed in Teamcenter is updated accordingly.
In the image below, changes are visible in a physical structure – as the Service Event, along with all Service Discrepancies and Corrective Actions are approved.
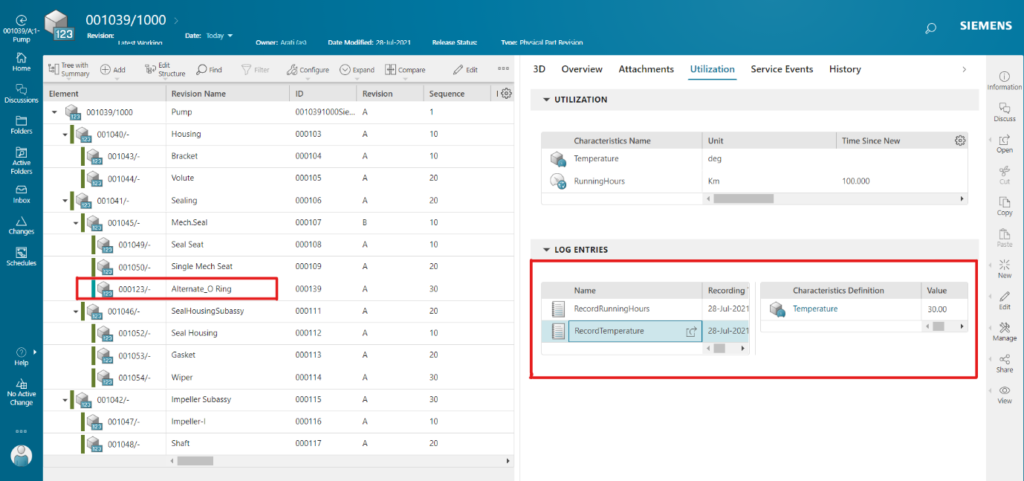
Service Events in Teamcenter, captured from external systems, or via system integrations, help you manage physical structure configuration data and changes, improving your service engineering outcomes. To learn more about this capability, and Teamcenter Service Lifecycle Management, be sure to read more here.
Learn More
Try Service Lifecycle Management for free, start your 30-day software trial
For a complete list of Service Lifecycle Management virtual seminars and dates, go here
Read more blogs about Service Lifecycle Management