Electrical Systems podcast (Ep. #2): “Design Tools and Practices – Past, Present and into the Future”
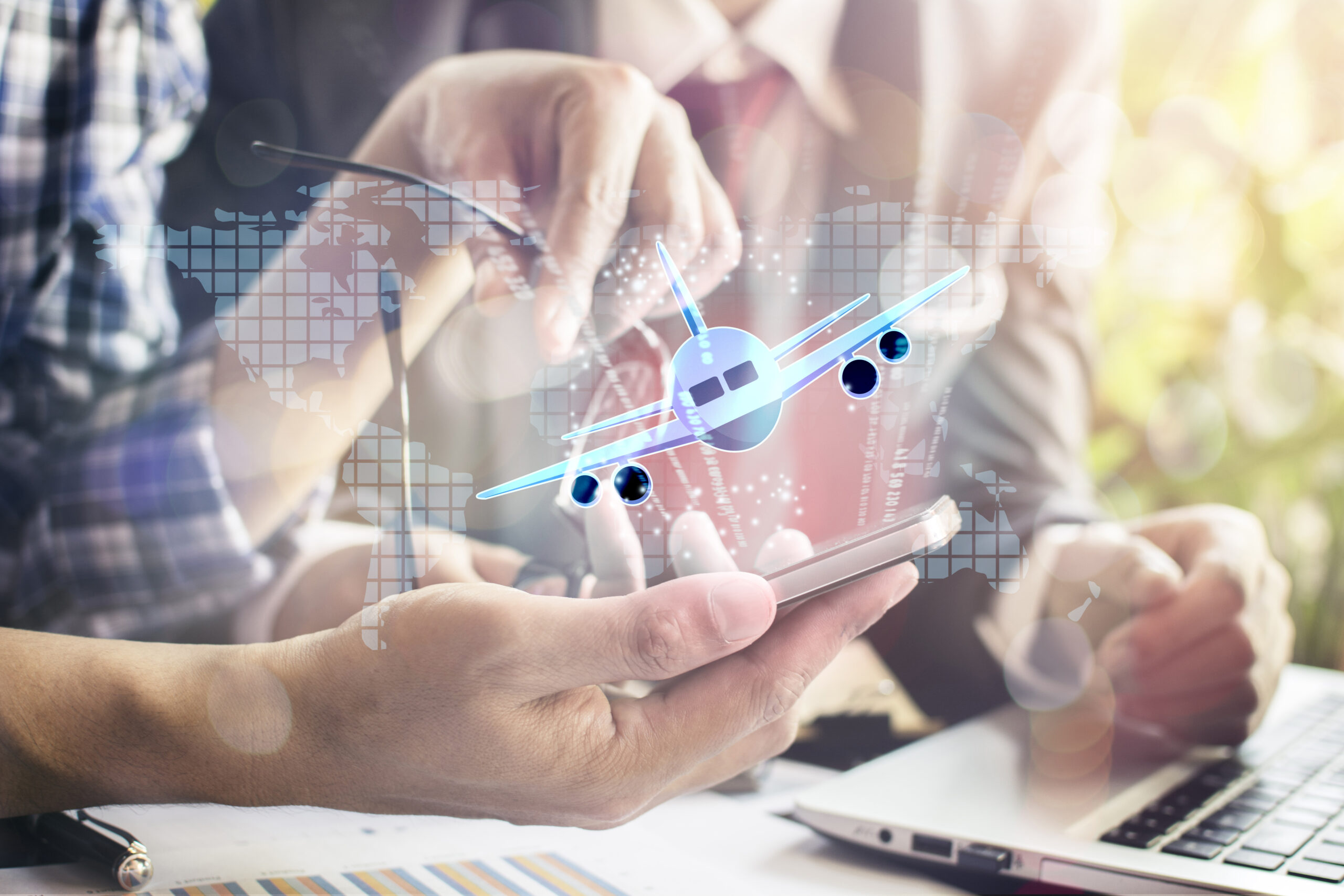
The digital transformation has allowed us to design, engineer and build in ways never before imagined. But what was it like back before desktop computers or 3D CAD?
This episode, “Design Tools and Practices – Past, Present and into the Future” explores the tools and methodologies engineers used throughout the decades. …An amazing trip down memory lane and a look into the future. Of course, all this from the perspective of electrical engineers responsible for the development of electrical systems and platforms in aircraft.
The industry has gone through major catalysts, or inflection points, through the years. We’ll discuss a few of these catalysts – why they happened and how they moved the industry forward.
Listen to this episode now.
This is episode #2 of a five-part series.
The digital transformation has allowed us to design, engineer and build in ways never before imagined. But what was it like for engineers before software and even computers? …Are you kidding? Yes, once upon a time drafting tables with lots of ink and Mylar paper were the modus operandi for the industry.
Welcome to season three of Talking Aerospace Today. In this episode, “Design Tools and Practices – Past, Present and into the Future” we discuss the tools and methodologies engineers have used throughout the decades. We’ll look at current and future technologies, too. Of course, the perspective we’ll be taking is that of electrical engineers responsible for electrical systems and platforms in the Aerospace and Defense industry.
The industry has gone through major catalysts, or inflection points, through the years and we’ll discuss these catalysts, why they happened and what was the result?
I’m excited to get started. This will be fun.
Our guests today, first the inspiring and insightful Steve Caravella, a Solutions Architect from the Capital Team at Siemens Digital Industries Software. Steve has many years’ experience in the aerospace and defense industry (as you will soon discover). Steve goes way back in the time machine. Next, we’ll be joined by Tony Nicoli, the Aerospace & Defense Director of Integrated Electrical Systems for Siemens Digital Industries Software. Steve and Tony will also discuss design tools and methodologies related to today’s digital transformation. Lots of ground to cover here, folks.
My name is Scott Salzwedel and I’m the host of Talking Aerospace Today. I invite you to take a listen to our latest podcast series that focuses on electrical system design in the A&D industry.
In this episode, you will learn:
- What does Steve do at Siemens? (2:23)
- The tools Steve used in the days of B.C. – “Before Computer” (3:19)
- How the computer shifted Steve’s job (4:26)
- A major new catalyst: Computer Aided Design (5:01)
- The evolution into 3D CAD (6:38)
- The latest catalyst for change, model-based design (7:11)
- The digital thread – what is and what it isn’t (10:54)
- About Siemens new Capital E/E Systems development environment (12:13)
- How Airbus A380 exploited multidisciplinary opportunities (13:39)
- The collaboration between ECAD/MCAD co-design (18:01)
- What is model-based design? (19:55)
- The benefits of the model-based design approach (20:32)
- The difficulties of adopting new tools (21:51)
- Using Siemens Digital Industries Software and Xcelerator portfolio (23:16)
Connect with Steve Caravella:
Connect with Tony Nicoli:
Resources:
- Capital website
- Blog: The Capital E/E Systems development solution. Exactly how has Capital evolved?
- Podcast #1 from the Capital podcast series: “The Evolution of Electrical Design in Aerospace
Scott Salzwedel: Hello… and welcome. This is Talking Aerospace Today – the podcast for the Aerospace & Defense industry and the trends that drive the digital enterprise, a place that brings the promise of tomorrow’s technology to the years of our listeners today.
And I’m your host Scott Salzwedel. Welcome to episode two of our five-part series.
In this episode, “Design Tools and Practices – Past, Present, and into the Future” we’ll be discussing some of the tools and methodologies engineers have used throughout the decades in their pursuit of developing electrical systems and platforms for aircraft. We know this is a time of great innovation and transformation for the industry. And when it comes to electrical system design and development, there’s a lot to discuss.
Before we dive into this episode, a reminder that our first episode covered the trends OEMs and suppliers are facing during these times of intense complexity. I urge you to give our first episode a listen. That’s Talking Aerospace Today, season three. You’ll find our podcasts on iTunes, Spotify, Stitcher, Google, or wherever you go to listen to your favorite podcast.
Okay, I’m excited to get started. In this episode, we’ll take a walk down memory lane and talk about the design tools used decades ago, and how things quickly progressed over the years, how we moved from drafting tables and handheld calculators to computer-aided design, to where we are now with model-based design – how the promise of future technology shapes how we use our tools today. In this episode, I’ll be talking with Steve Caravella, a Solutions Architect from the Capital Team at Siemens Digital Industries Software. Steve has many years of experience and has been involved in Aerospace BC (that’s Before Computer). So, we’ll hear from Steve, and then later in the podcast, we’ll be joined by Tony Nicoli. Tony is the Aerospace & Defense Director of Integrated Electrical Systems for Siemens Digital Industries Software. Tony and Steve will discuss design tools and practices as they relate to digital transformation. It should be a really good conversation. So, welcome Steve! Could you please share with our listeners a little bit about your past and what you do at Siemens?
Steve Caravella: Hi, Scott. It’s great to be here. As you mentioned, I’m a Solutions Architect working with Capital products with a focus on the needs of the Aerospace & Defense industry. I joined Siemens earlier this year after spending the past 28 years working for several aircraft manufacturers. I’ve done engineering design certification and manufacturing support in most parts of the business ranging from service centers to new product development, including roles in program management, and as an engineering leader.
Scott: Wonderful! It’s great to have you, Steve. Thanks for appearing on the podcast.
Today, we’re in the early stages of digital transformation. It’s amazing to look back at the tools we used and how he got to this point, just how far we’ve come. The industry has gone through some rather intense catalysts or inflection points to get us to where we are today. So Steve, how far back are you going to take us? Back to the days of #2 pencils, drawing pads, and plastic triangles? What do you think?
Steve: Oh, yeah, don’t forget Ink and Mylar, typed documents, hand calculations, what I like to call the original “Copy and Paste”. Go to the copier, cut it out, and use your scotch tape. So, it’s just interesting. I think back to my first job, and I walked into the engineering design office, it was this huge floor space and I just see a sea of drafting tables. It’s a good old-fashioned drafting. You had your pens and pencils, motorized erasers, racer shields. When you’re working with Mylar you’re going to use ink pens, but a lot of people will remember those motorized erasers. A lot of the stuff beyond the design was hand calculations. Now, we did have calculators, so I never did learn to use a slide rule but you’re still going back to a lot of hand calculations on paper. And as I mentioned the classic copy-paste, we were doing reports, taking copies off of drawings or out of our notepads, and pasting them into sheets of paper to compile our reports.
Scott: Wow… Okay. And these paper-based practices were soon replaced by the computer. So, why did the computer become so popular?
Steve: Well, primarily, we moved to computers to reduce the use of paper, which is interesting, because it seemed to generate more paper. However, the other thing computers provided with us was an easier way to draw at scale. Of course, we could print out multiple copies, and it was really a lot easier to draft and make changes. Also, the computer did the calculations and math for you, so you really didn’t have to move over to a calculator to do that.
Scott: And another catalyst was when computers ushered in the new era of computer-aided design or CAD, isn’t that right?
Steve: Indeed. So, computers enabled the introduction of computer-aided design and suddenly we were able to produce electronic files. This was a huge shift. We had a specialized tool to do the analysis come online at the same time, so programs like MATLAB, Mathcad, and others. So, suddenly we go from doing everything on paper. So now, we have CAD systems, word processing, spreadsheets, this all moved everything into the computer. We would do drawings in the CAD tool, but we still put paper drawings out to people, we still have physical vaults, where the drawings and the printed documents would go, we would have files saved on floppy disks, sometimes they would go to the vault, sometimes they’d just stay in your area. But we still have manual integration. Spreadsheets and databases were built to store connectivity information for review and validation and we still had design drafting and checking. With this, we could pull from symbol libraries, which some people call ‘blocks’, and apply line styles electronically for drawing designs and creating documents.
Scott: Steve, sorry, but it sounds like a total geek fest – I’m sure some of our listeners can relate to what you’re saying here – but it’s really good stuff!
Steve: Well, that’s true. You’ve got to remember, these are tools of the trades for engineers and designers. And moving from manual to computer tools really made things easier. A simple example is if you were a drafter and you had to draft a side view or a top view of a part, you would have to draw in projection lines for those views. Now, suddenly, you can do that on a computer and when you’re done, you remove them, and you’re good to go.
Scott: Great. Perfect. Okay, so another significant change was when 2D CAD turned into 3D CAD. Who was the catalyst behind that?
Steve: Well, at this point, time and efficiency became really critical factors. When you go to 3D CAD, you get automatic view generation, and that saves you a lot of time. The other thing 3D CAD brought us was the ability to do digital mock-ups, so physical mock-ups weren’t as necessary. Suddenly, there was much better collaboration and the design accuracy improved. We were doing everything much faster while cutting costs. We reduced new program costs and time, and this was all happening in the early ‘90s.
Scott: And now let’s fast forward to the early 2000s, when…
Steve: When model-based design begins.
Scott: Yes, another catalyst. Okay, so before we go any further, could you please define for our listeners what you mean by model-based design? From what I can tell, there are multiple definitions floating around out there.
Steve: Sure, that’s a good question. To me, the simplest way to explain model-based design is that it eliminates drawings. Now, when we started doing this, the advances in the CAD systems allowed us to move PCs. And the PCs were great at handling the 3D modeling part of it, but what was interesting is when you looked at the computer to generate views of the 3D models for your drawings, it was really computer-intensive, and larger models continued to crash. So, in a lot of ways, creating the drawing was more than the PC can handle. But it also begs the question when you start to think about it, “If all the information about the part that you’re designing is in the model, why do you need drawings?” So, these questions lead us to really thinking about why do we need drawings, and here we are with model-based design.
Scott: Okay, thanks, Steve. Can you sum up what all this means? I don’t think we’re pushing the slide rules or plastic rulers anymore. That’s for sure.
Steve: No, not really. Really, just to kind of hit the highlights of this, so, first and foremost, we replaced drawings with direct use of the 3D models. These are intelligent models, so you get graphical depiction with the information about the part and piece – that might include materials that might include processes. The great thing this does is this enables checking, and validation to be done inside your software. So, the model is a richer source of information and so now you can interrogate that to do your design checks, which will cut a lot of manual checking. One thing to keep in mind is that going to model-based design does change your business paradigm. So, suddenly you’re going from a paper system where you have your hands on your intellectual property and now you’re going digital with everything. So, you’ve got to concern yourself with access, data integrity, and longevity of electronic files. Nobody used to worry about a 50-year retention on your design data. But think about it from the advances in software and the ability to open up a design 50 years from now. The other thing it caused a rethink of is how to interpret and inspect models given that they can see everything. Inspection and manufacturing people were used to seeing the dimensions portrayed on the drawing that were decided by engineers, now suddenly, they have full access to every feature on that part. Another benefit was that we’re able to pass and share information pretty much in real-time. If I save my data to my PLM system or my storage vault, as soon as it’s there, other people can access it. And then finally, I do have full traceability because I’ve got digital threads connecting requirements to design, to analysis, to the manufacturing records, and even into compliance.
Scott: Traceability, the key to first-time-right design, keeping costs down, and really the door to innovation. So glad you mentioned traceability because now we can talk about Siemens and how it actualizes the digital enterprise.
Steve: Exactly, Scott. Yes, it’s about data continuity, for sure, not just in design and manufacturing, but throughout all facets of an organization. So, let’s first talk about the digital thread. Let me be clear on what it isn’t. The digital thread is not just a document vault with data pressed into a standard format – such as a PDF – and stored electronically, and it is not manually extracted static exports and imports of your information.
Scott: And really what the digital thread is, it’s this connective tissue of technology and software tools that allows folks like you to optimize and automate operations to share digital information across domains and disciplines.
Steve: Indeed. The digital thread – let me tell you what it is – it’s the connection and sharing of information digitally across domains. So you have requirements connected to design, connected to material acquisition, to manufacturing, and to maintenance information. And you’re also, at the same time, connecting requirements to design to your compliance showing and your records of approval. The digital thread is also information utilized to drive integration between domains and it is ideally dynamic in real-time when it’s ready for the handoff.
Scott: Yes, the digital thread plays an instrumental role in the digital transformation going on in Aerospace & Defense today. And listeners, if you haven’t heard of Siemens’ Xcelerator Portfolio, I urge you to Google it. This is the engine driving innovation.
Okay, so at this time, I’d like to bring in Tony Nicoli, who is the Aerospace & Defense Director of Integrated Electrical Systems for Siemens Digital Industries Software. Hey Tony, how are you doing?
Tony Nicoli: Hey, Scott. Love the podcast so far. You and Steve have covered some interesting ground.
Scott: Thanks. I’d like to keep the momentum going by asking you to discuss the digital transformation of aerospace as it pertains to electrical system design and development. We’ve talked about design tools and practices from the past and present, and guess what, you’re representing the future.
Tony: Well, that’s a pretty tall order, Scott.
Scott: Tony, I know you, you can do it. So, if we’re looking into the future, I think of the new Siemens Capital E/E Systems’ development environment now available. What is it and what’s the impetus behind it?
Tony: The Capital E/E System is a development environment, and just to be clear, the E/E stands for electrical and electronic. So, a few things here. Today’s programs focus on reducing the time it takes to field new capability, while still assuring platform manufacturing quality and safety. One way to do this – which is becoming pervasive in the industry – is implementing functions electrically.
As a consequence, electrical system complexity is growing and is already at levels not seen in the past. This is making electrical regulatory requirements harder to meet and putting a premium on coordinating development among all the disciplines used to design the platform. This is an important activity because it lets us both exploit the opportunities inherent in multidisciplinary design and avoid the risks, cost overruns, schedule slips, other stuff that arise when we do this naively. To illustrate just how critical this is, I’d like to tell two stories about the Airbus A380 – one of exploiting a multidisciplinary opportunity and the other of a multidisciplinary problem. Would that be okay?
Scott: Sure. Please, do tell.
Tony: Okay, I learned these from my colleague, Kevin Michaels. Kevin is a great guy and an expert in the commercial jetliner ecosystem. The first one tells us how Airbus approached the aim of minimizing the A380’s weight. Because of the large size of the A380, Airbus needed to take innovative approaches to weight reduction. One of these was to employ electrohydraulic hybridization. Instead of using a traditional hydraulic actuation system, they used electro-hydraulic actuators.
This approach uses a local hydraulic fluid supply rather than a centralized hydraulic reservoir with numerous hydraulic lines. The local fluid reservoirs are controlled electrically, reducing overall fluid mass and line length to result in substantial weight savings throughout the aircraft. A knock-on advantage of this approach was the ability to employ higher hydraulic pressures in the system. Why higher pressure? Well, with higher pressure, you use smaller diameter hydraulic lines to achieve the required actuation forces. This means even more weight savings from reduced fluid and piping mass. Wahoo… If I could only use that to achieve weight loss!
Scott: Tony, last time I saw you were a walking stick figure. Okay, so part two of your Airbus story.
Tony: On the downside, many people know that the A380 was substantially delayed and took a serious development cost hit due to an electromechanical integration problem. But few understand the details of this problem. Airbus is a combination of the best of the historical aerospace providers from three countries, France, Germany, and Britain. These teams came together in the ‘70s to form a commercial and now also defense corporation that is among the best in the world. However, each came with legacy development environments that persisted as the program succeeded program. The teams evolved their mechanical and electrical development environments in much the same way that Steve has recounted, but they did not fully coordinate them among the legacy organizations. Each team had responsibility for different modules of the aircraft – wings, fuselage, systems, subsystems, central control – and they proceeded to design the aircraft electrical system while working hard to take its mechanical context into account. They did a fine job within the modules they were responsible for. However, because of their individual approaches to the multidisciplinary development environment, the 330 miles of wire harnesses on the aircraft were incompatible. Basically, when they came to assemble the modules for the first time, they found that the harnesses that they had been designing and installed for one module wouldn’t connect to the next. This caused multiple very costly iterations to the designs of the electrical and mechanical aerostructures. The program was delayed in 2005, and again in 2006, finally getting back on track in 2007. The total cost of this error is estimated to have exceeded six billion – yes billion, like in “Dr. Evil dollars.”
This event lives on in the minds of Airbus program leaders to this day and influences how they view the future of aircraft development. So, using modern multidisciplinary approaches to electrical and electronic system development is important. It allows us to realize its inherent possibilities while minimizing its intrinsic risks.
Scott: Wow Tony, great stories. Steve, is there anything more you’d like to add?
Steve: Yeah, I would just like to build off of what Tony described. Many companies have found that the key to pulling this off successfully is that they have integrated product teams, which means they’re doing cross-disciplinary design reviews and getting input from a variety of sources across the organization. Second, is they will use multi-domain workflow reviews so that again, they’re represented as designs are getting off boarded, and checked. And finally, this all gets wrapped up into coordination across not just one discipline, but across all.
Scott: So, the integration of multi-domain workflows is an intriguing notion, and I immediately think of the ECAD/MCAD co-design. Tony, can you give our listeners a better picture of what we’re talking about here?
Tony: Yeah sure, Scott. When we talk about ECAD/MCAD co-design, we mean enabling each engineering master – the electrical engineer, and the mechanical engineer – to work together in concert. This requires that they have the information that arises from the decisions being made by the person leading the other discipline, available in their development environment. That is right here immediately when they need it. Not sometime later, when they might bother to open the other person’s environment or have a meeting. They need the info that impacts their own decisions in real-time as they make them. For example, the electrical lead needs to know where they can route electrical wires and harnesses that is what space has been reserved for them by the mechanical engineer, as they make their design trades. And the mechanical engineer needs to know when an electrical engineer must violate these reserved volumes in order to comply with modern EU’s regulations. We’ve taken this into account as we’ve developed Capital so that these two professionals can collaborate effectively.
Scott: But do engineers know how to do this kind of thing? It sounds like there would be some shortcomings. Steve?
Steve: Yes, Scott. Well, it comes down to engineers taking a moment and thinking about a couple of key questions. When they look at what they’re doing today, they should ask themselves how much time do they spend exchanging information, and is it happening reliably? Second, how much change activity do you have due to error correction? And are you satisfied with that level? How much do you rely on experienced eyes to check design integrity and integration? And finally, how much could be checked by the system by checking the design against rules?
Scott: So more and more we see businesses and suppliers and aerospace digitalize their operations. We hear a zero-defect level or get it right the first time. I would imagine there’s a correlation there, right Tony?
Tony: Absolutely. This is where we can talk more about model-based design. Model-based design means the model is contained to design information that can be automatically interrogated by the verification algorithms built into the developing environment. It enables the system to check for errors we’ve experienced in the past via automated design rules. It enables direct sharing of the information without repeating data entry. It allows the environment to trigger checkpoints where ECAD – MCAD integration is verified for the alignment of critical properties.
Scott: Okay, so those sound like features of a model-based design approach. But what then are the benefits to the end-user?
Tony: Scott, the real benefit to the program is avoiding problems like those experienced by Airbus on the A380. Program teams gain the ability to virtually integrate the electrical system into the mechanical structure long before the first article assembly. This maximizes the probability of receiving harnesses from the wire shop that are right the first time. In fact, we have many customers who were amazed that they could design the electrical systems, define and specify the platform’s wire harnesses, order them, and then just install them. And the platform would work the first time. One company found that their need to make electrical system changes fell dramatically as well. They eliminated 90% of all electrical system changes just by deploying a model-based environment. Finally, a helicopter OEM discovered that they could drive their scrap rate down in production. You probably aren’t going to believe me, but they actually achieved production runs with zero scraps. This had never happened before.
Scott: Wow, zero scraps! That’s impressive.
The one thing we haven’t touched on is how difficult it is to adopt these new tools. I mean, I’m struggling with adding MS Teams to my daily work schedule, but the stuff we’re talking about here…
Tony: I feel your pain, Scott. No doubt, the hardest step is going from a manual process to an automated and integrated process. Individual users, design teams, management, and the company in general have a lot to consider. They have to identify and translate institutional experience – aka, tribal knowledge into process flows and rules for systems to follow. Most experienced people are not even consciously aware of the rules they use in their day to day work. Hand drawing with a computer 2D and 3D CAD was simple, you do the same job that you did manually using a different tool. People needed training and equipment, but otherwise, no one outside the immediate organization was affected. In contrast, model-based design is a huge step change. Even without increased integration, people need to be flexible enough to adopt new ways of working together and the organization must commit to implementing the digital infrastructure to support them. These things all take work and investment, but they can be done. And they are being done by the highest performing OEMs in the industry.
Scott: Tony, Steve, I have a feeling we could talk about this for hours. Unfortunately, our time is just about up. But I want to reiterate the advantages Siemens Digital Industries Software brings to Aerospace & Defense customers.
Tony: Of course, Scott! Fundamentally, Siemens’ Xcelerator portfolio is the most sophisticated and mature multidisciplinary digital development solution that Aerospace & Defense companies have access to today. As part of that portfolio, Capital is the only model-based electrical and electronic system development solution that connects the entire electrical development lifecycle from conception through design, into manufacturing, and on to operational sustainment. It is truly multidisciplinary, integrating activity between both the electrical and mechanical disciplines and among the core electrical ones, including electrical distribution, electronics, and networks. It speeds the sharing of information and change between these disciplines, assuring that each engineering leader has what they need when they need it to make accurate design decisions. It automates checking and verification to keep engineering leaders out of trouble and it allows them to virtually integrate the electrical system long before they build the first physical one, reducing the cost of first-time quality.
Scott: Man, very cool! This is indeed an exciting time to be part of the aerospace & defense community and Siemens is truly leading the way in the most comprehensive digital technologies. Well, that’s it for Episode Two. Thank you, Tony. Thank you, Steve. Thank you both for your insights and expertise and our walk down memory lane. I’m sure our listeners enjoyed it!
Tony: No problem Scott, thanks for having us.
Steve: Yeah, thanks, Scott. This was fun.
Scott: And of course, I’d like to extend my deepest thanks to our listeners. Thank you, listeners. I’m glad you tuned into this podcast.
Now, at the top of the show, I mentioned we’ll be doing a five-part series on “The Evolution of Electrical System Design in Aerospace.” If you enjoyed this episode and you want to give a listen to episode one, please check out the links in the podcast description. Be sure to subscribe to Talking Aerospace Today on Apple Podcasts, Spotify, or wherever you go to listen to your favorite podcast. That way you won’t miss a single upcoming episode. Our next episode will be on how the industry is dealing with change management. When a change happens, how do you keep configuration control? How do you implement across the entire organization?
My name is Scott Salzwedel, and this is Siemens’ Talking Aerospace Today. I hope you’ll join us again for our next podcast. Until then, bye for now…
Connect with Steve Caravella
Connect with Tony Nicoli:
Resources:
- Capital website
- Blog: The Capital E/E Systems development solution. Exactly how has Capital evolved?
- Podcast #1 from the Capital podcast series: “The Evolution of Electrical Design in Aerospace”
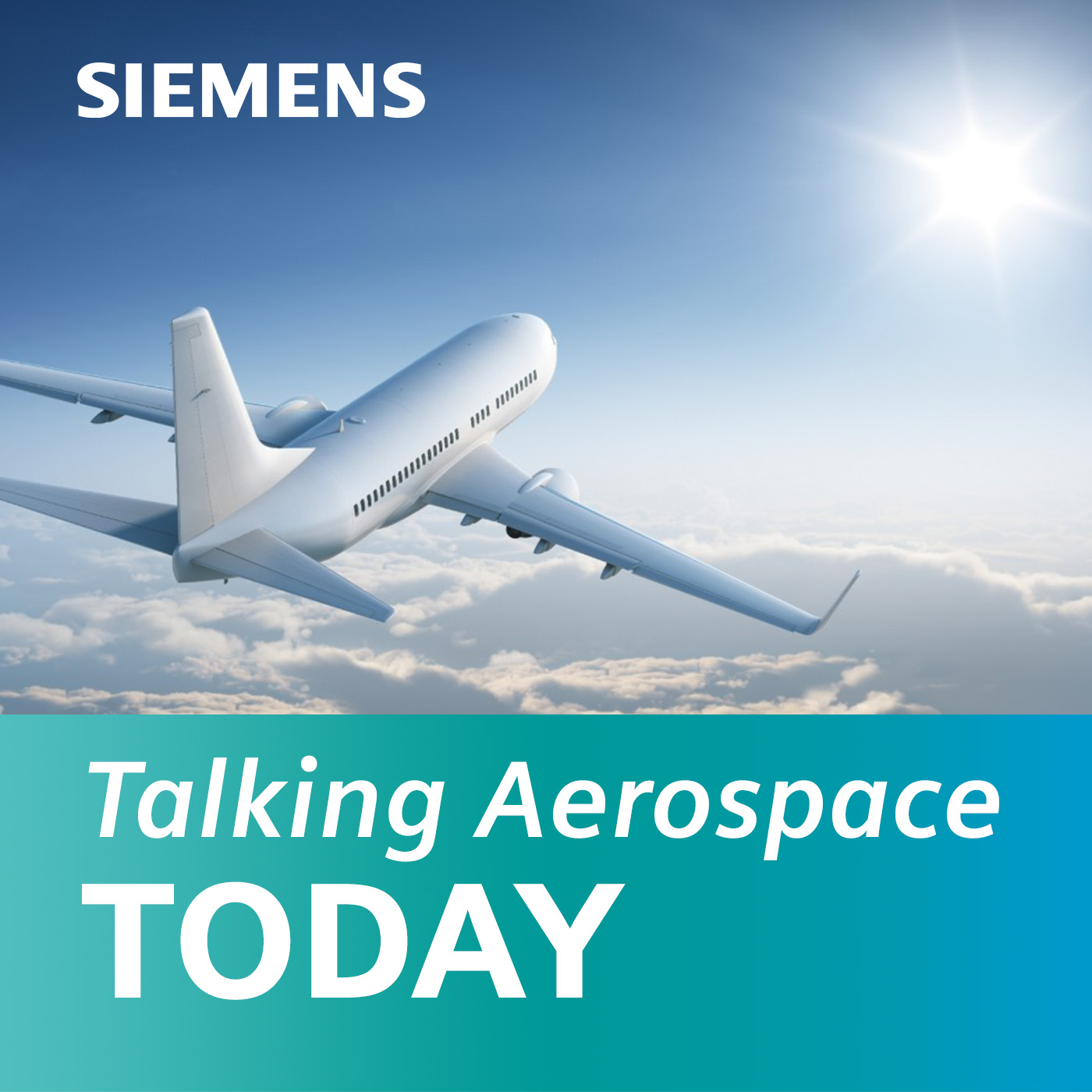
Talking Aerospace Today Podcast
The A&D Industry is at a serious inflection point. Transformation to the digital enterprise has opened up a new era in innovation and technological breakthroughs. However, complexity and compliance continue to hamper the best of efforts.
Join us as we explore how Siemens is turning complexity into a competitive advantage for many of our customers – today and well into tomorrow.