Understanding and Communicating Your Design through Visualization
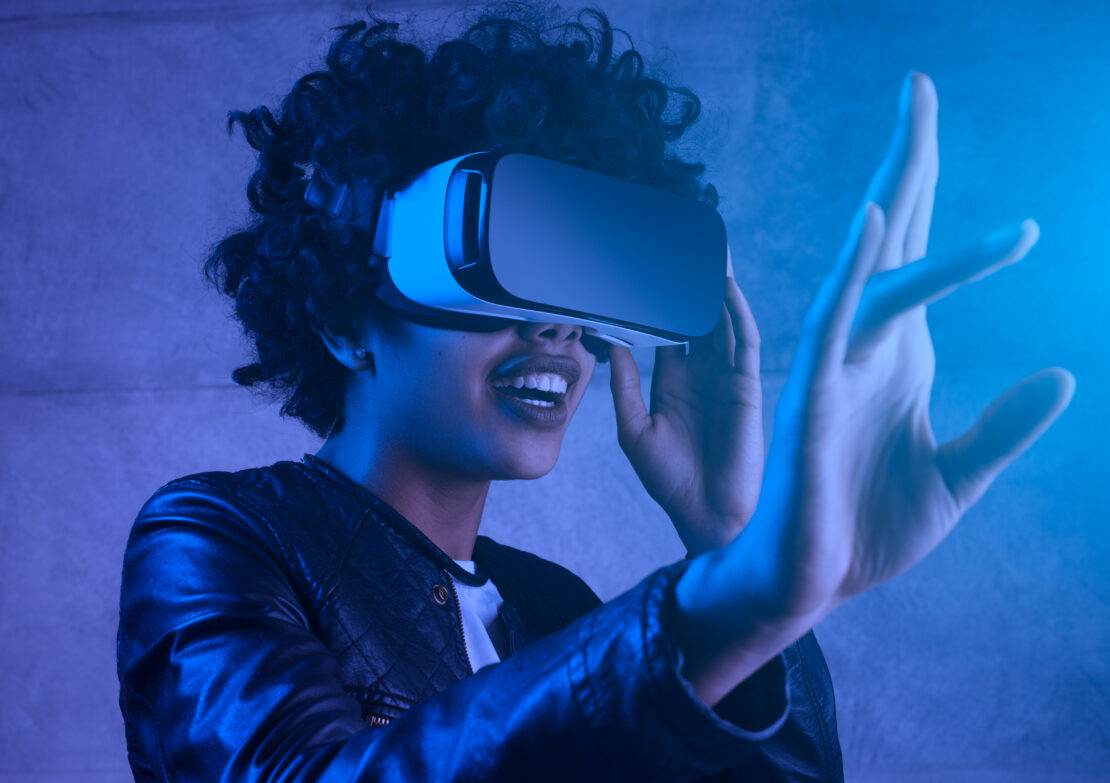
What is digital visualization all about and how is it helping design engineers? To answer this question we first have to understand the types of visualization tools that are available and how they work. General visualization for design can include standard display, realistic rendering, and immersive 3D virtual reality. Standard display helps design engineers to provide better understanding to the shape of their design and the relationships between objects while also simulating and validating the operation of design. Realistic rendering is about helping to explain designs better to other people and understanding it in context of the environment. Lastly, Immersive 3D virtual reality provides realistic display in terms of scale and spatial relationship between objects.
Summary
Design processes within the digital space are evolving every day. Living in such a fast-paced and advanced world leaves little room for error within engineering and manufacturing spaces, so it’s imperative that designers are utilizing the best and most efficient forms of tech.
Joining me on today’s episode to discuss the strides being made within the Immersive Visualisation space are Senior Executives at Siemens Digital Industries, Patti Longwinter, Tod Parrella and Dave Hutchinson! We discuss the fascinating industry of visualization technology and how it can be used to communicate designs more effectively while they’re still in development.
We also dive into the different types of digital realities, spanning from Virtual to Augmented, how industries outside of tech and engineering have benefited from the use of these products, and how they have integrated with early marketing design data.
To learn more, tune in to Episode 9 of Next Generation Design!
Some Questions I Ask:
- What is ‘General Visualization’ and how does it work? (3:10)
- Why do you think visualization is so important for design? (5:01)
- How can people approach design while implementing Immersive technology? (11:09)
- What is the most innovative feature of the Visualization technology? (12:37)
- Does the accuracy waver depending on the Visualization solutions available? (13:33)
- Tod, do you have any experiences to share as a Product Designer? (14:38)
- Dave, could you talk about how early marketing design data integrates with Visualization technology? (23:20)
- Are there other departments within organizations outside of engineering that would also be benefiting from this technology? (25:02)
In This Episode You Will Learn:
- The three aspects of ‘General Visualization’ (3:15)
- How Virtual Reality is helping engineers better comprehend and communicate their own designs (5:33)
- The main benefit of using visualization (6:48)
- The industries that are benefiting the most from visualization (8:27)
- How industries outside of tech are utilizing Visualization technology (9:34)
- Tod’s experience as a Design Engineer overseeing Industrial Design and conceptualization processes (15:03)
- When Visualization became critical to Tod’s industry (16:19)
- Why Tod believes that Visualization spans across the simulation world (19:06)
- Dave’s breakdown of each of the digital realities (20:21)
Connect With Jennifer Piper:
- Siemens Digital Industries – Website
- Siemens Digital Industries – Facebook
- Siemens – Twitter
- Siemens – Instagram
Connect With Patti Longwinter:
Connect With Tod Parrella:
Connect With Dave Hutchinson:
In this episode of the Next Generation Design Podcast, our guests discuss digital visualization, an area that is growing rapidly across industries to provide an interactive design and evaluation environment for their products.
The main benefits of visualization tools include evaluating if the designs you’ve created are the way you want them, being able to accurately describe your designs to other people, while correlating you designs to something in the real world. When using visualization for the first time many often exclaim “Wow, now I get it! This is my design and I’m seeing it before it is manufactured, in a realistic way.”
Consumer experience has been what has led the way for how visualization in engineering has developed. From the design engineer perspective, it is augmenting processes already in place; and extension of the design environment with the click of a button to more accurately assess more design options and fine tune a product quicker than traditional processes.
Visualization and the digital twin is a critical cost saver in design engineering, and allows for early review of concepts; making proportion, scale, relationships easier to evaluate, allowing users to make decisions on them well prior to any physical production that would add cost and time to market.
Jennifer Piper: Welcome back to another episode of the Next Generation Design podcast. I’m your host, Jennifer Piper. Designing the technology of tomorrow is no easy task. Sure, it may seem easy, but it’s easy not to think about the design process of something once it’s already made. We tend not to think about all the work that goes into making the tech we bring into our everyday lives. All tech starts with ideas and blueprints. And once these ideas are paper, it’s a long road to make them a reality. In our case, a virtual reality. In today’s episode, we’re talking about the digital space and the design processes behind them. Who better to talk to than those who are a part of the process, right? We have three guests today and together we’re going to explore what digital visualization is all about.
Patti Longwinter: This is Patti Longwinter. I recently joined Siemens Technology and Software partner NVIDIA, where I’m now the Strategic Alliance Manager to Siemens Digital Industries Software. I actually started my career as a designer, actually working on the drafting board – not even using CAD at the time. I was the first in my department to make the leap to CAD and I was responsible for setting up the new processes and writing custom programs, which led me to software engineering, where I then worked to apply graphics technology to NX. And then, ultimately, I transitioned into Product Management, planning for the NX visualization products. I’ve been really lucky in my career to see the evolution of computer graphics technology over the years. I’m really excited to be working for NVIDIA who revolutionized computer graphics with the invention of the GPU. I’m also glad that I can continue to work with the Siemens NX team to leverage the technology to bring great digital visualization solutions to NX design users.
Tod Parrella: My name is Tod Parrella, and I work in the NX product management organization in a team of industry product managers who take into consideration our eight core industry customer segments in terms of our product and planning process. And I’m also the Manager for the NX design products – it is the core CAD product that most or all of our customers use to design their products. I am a Product Manager here with Siemens Digital Industries. I was a Design Engineer at a consumer products company in the Boston area, a world-leading Consumer Products Company, and I was a design engineer working across the industrial design and engineering in production.
Dave Hutchinson: My name is Dave Hutchinson. I’m the Director of Technology and Operations within the Lightworks Group – a subgroup of the NX team – and we’re focused on providing high-end visualization software and services within the Siemens NX group and also to external software OEMs and manufacturers. I have been involved in computer graphics my whole career. And, in fact, up until a year ago, we were part of a separate company of which I was the CTO and we were acquired by Siemens – and I’ve spent time in development, presales, product management, and leading our sales product and engineering teams within the Lightworks Group.
Jennifer Piper: These three know a lot about the world of design in general visualization. It’s not just a world of pretty pictures and pixels projecting onto screens. That’s some of it but not all. What is general visualization? And really, how does it work?
Patti Longwinter: Let me answer that in terms of what general visualization is for design. We look at it as three different aspects of visualization. And that’s standard display for design work, where you have to have very fast tools, it has to be efficient, but it’s really all about understanding the shape of your design, relationships between objects in your design, and being able to simulate and evaluate the operation of your design. So, standard visualization is a key aspect of visualization for design tools. And then, another aspect of visualization is realistic rendering. And it’s really not just about a pretty picture and generating images – although that is an important aspect of it for marketing and for selling your product. It’s really about communication. It’s about being able to explain your design to other people, understanding it yourself in the context of an environment, and really, a realistic representation of your model; it is not just about aesthetics, but really understanding it. Whether it’s a mechanical part or a factory, you really need realistic rendering to understand what you’re looking at and understanding your design, your digital twin. The third aspect of visualization for design is immersive or 3D – and currently, we’re using virtual reality and virtual reality tools. And this is about getting to realistic display in terms of scale, and the spatial relationships between objects. It’s another important aspect in becoming even more important as technology evolves.
Jennifer Piper: And so, why would you say it’s important for design?
Patti Longwinter: Again, NX visualization – and visualization for design – is about understanding and communicating your design. So, that’s understanding, how your design is going to operate? Are the shapes the way you want them? Describing them to other people is important in a 3D tool in the past, or if you’re just looking at a 2D representation of your design – not everybody understands that. It takes a little bit of knowledge to take a 2D representation and correlate that to something that’s real world, where we’re getting more and more in visualization for design, in realistic representations of the design. So, on your computer or your laptop, you see it in 3D, you’ll understand it better. But when you’re in VR, you understand it even more. We see people put on the VR goggles and they understand conceptually that it’s a good thing, but once they put the goggles on, and they see their design, we hear a lot of, “Wow! I get it! This is my design, and I’m actually seeing it before it’s manufactured.” And it’s not only exciting, it’s really important, again, for understanding.
Jennifer Piper: I know when I have used or tried these types of virtual-reality-type experiences – whether it’d be a trade show or what have you – it really is unbelievable! Like you said, once you get those goggles on and you feel like you’re either on the manufacturing floor or somewhere else, it really puts you right there and you really can consume all of the detail of the part that you’re really looking at. So, what would you say is the main benefit of visualization?
Patti Longwinter: Again, I think it really gets down to communication. It is having that interactive experience. Some of the use cases that you would use visualization tools for, of course, for your day-to-day design, if you’re creating fillets, or creating a new surface, or putting your assembly together in your design, you have to visualize and you have to do it quickly. So, that’s really important. And the faster that you can do that, the faster, of course, you get your product out to market. And it gives you more opportunities. Not only is less time to evaluate your design, but it gives you more opportunity for different design options, too, which is really important; to differentiate your product is to have different design options. So, that increase in productivity will help you with creating new designs. And then, again, communication to others is really important too. And being able to do design reviews to generate images or to do interactive visualization during a design review really helps with understanding, speeds up the process. And getting those images out – and especially for marketing images, getting those out before the product is even manufactured, is really going to compress the time that it takes to get your product out to the market.
Jennifer Piper: So, who actually uses this technology? We know we can buy a VR headset online and play the coolest video game on the shelf. But, beyond that, how do these visual tools function in the world? What industries have you seen benefiting most from visualization?
Tod Parrella: Visualization is used extensively across our eight core industries that we serve in the market, but particularly when we think of realistic rendered visualizations, the automotive industry has been a very early and high adopter of that technology; materials, colors, textures, lighting, those are all critical aspects to consumer goods that are evaluated in a showroom and people are making decisions on a product based on the way it looks, as well as the way you feel and interact with it. They have been an early adopter and you would say, equivalently, the consumer products industry as well. You might classify and say any products that are going to be in tough competition in the consumer market where appeal, aesthetics, as well as ergonomics and function are all being weighed heavily to the success of that product, that’s where we see it used extensively. I would say that, because of the advancements in technology, moving out of just a digital twin behind a computer screen, but actually into this virtual reality world, the rest of our industries are really taking notice and seeing a benefit there, as Patti mentioned – how do I live, and interact, and work with this product? And so, that’s really brought visualization to those other industries. We see it in large aircraft and ships – so in the aerospace and shipbuilding, in Marine industries where they want their customers to get a view of this product in its actual scale; you know, scale on that magnitude is not something you can represent well behind a computer screen. Being able to actually immerse yourself into that product and then walk around it, that’s where we see those industries have really taken hold of and been interested in adopting visualization tools.
Patti Longwinter: What I find interesting, too, is really, the other industries or the other products where you wouldn’t imagine that they would be interested in, especially generating realistic images. But we’ve got companies design things like pumps or heavy equipment that are generating their high-end rendering images for marketing, for putting on their website, or discussing the design with a specific customer. Still really important, too, that sense of realism and, as Tod said, the scale, the immersive visualization – the VR – is really important for those industries, too.
Jennifer Piper: Another question that kind of comes to mind is, how do people change their approach to design with visualization or VR, as opposed to traditional ways in the past?
Patti Longwinter: You know what? I think that as far as immersive visualization from a design standpoint, is that it’s really augmenting the processes that they already have. So, we like to think of VR as really an extension of your design environment. The 3D immersive environment is something that you can get to very easily with a single button click – so, that will send you into what we think, conceptually, is really the 3D representation more than even on your laptop or desktop. So, it’s just really a different form factor that you’re dealing with in viewing your 3D design. So, we’re seeing people actually do design reviews in VR, whereas before they might generate some images, they’re able to do interactive kind of design review sessions. I think that one change that they’re making, is that they can actually take a look at the design and rotate it around and walk around it, and then that really helps with the design review process.
Jennifer Piper: Interesting! Yeah, that’s something that I wouldn’t have thought of. So, I’m glad that you pointed that out. What is the most innovative feature of the visualization technology?
Dave Hutchinson: I mean, a concept that might not be from the software is actually, you know, the hardware guys are driving the innovation in terms of the quality of the eye-tracking and things like this so that you’re actually feeling more and more immersed. But that’s an NX product side of things, but that’s giving pace with how the hardware is evolving and the fidelity of the displays inside the immersive environments, the quality of what you can show inside there, the interactions that you can make, eye-tracking so that you don’t notice you’re inside of virtual environments. It just becomes a part of your natural environment.
Patti Longwinter: Yeah. And that’s part of the technology, for sure. And I think that the other point is that, yeah, the design-time visualization in the VR environment, being able to make a design change and see that in the VR environment, is really key to design workflows.
Jennifer Piper: So, depending on the different visualization solutions available, does the accuracy waver or tends to flux?
Dave Hutchinson: There’s a lot about the way you interact with the design itself and how accurately you can… If you could see your hands inside the immersive experience and you can actually touch some of the parts and move them very accurately, again, is driven partly by hardware but also by the connection with the design environment back in NX, for example. The more that you can do inside the virtual environment with optics or with tracking, then the finer tune the interactions with the actual model and design can be. It’s currently at its infancy right now.
Jennifer Piper: Of course, tech comes with its kinks. When’s the last time you’ve had your computer freeze for a moment, or a function take a little longer to buffer and load than usual? The good thing about this kind of tech is that there’s a lot of hands-on decks to make it work. It’s all in the design and its designers. Tod, I know that you have experience as a product designer. Did you have any comments or experiences that you wanted to share with the audience?
Tod Parrella: Yeah, as I mentioned, I worked at a consumer products company in the Boston area, a really world-leading dominating market segment in terms of consumer goods that they designed and developed and sold. As a design engineer, we had a unique position in my group because we worked across the industrial design department and did a lot of the engineering design, as well as working with the tooling and testing, and production people. So, we kind of got to see the whole process and that process really started in the industrial design phase where they were working out scale and proportion and relationships, they were working out colors, materials, and textures. This is a very costly part of a program when you’re building prototypes and concepts and, you know, in the old days, people used lots and lots of physical prototypes and concepts and they would run a hundred versions of different color studies, and materials, and textures – all to just get a few products on the executive management’s desktop to look at and give feedback on or put them in the market group’s hands to get feedback and make decisions.
Tod Parrella: And so, as I mentioned in the concept phase, we actually work three prototypes in parallel with one another because we, in a sense, we held our own competitions for what the best product was going to be into the market. And so, the whole point of this background is that visualization and the digital twin, and visualization on the digital twin became critical. It became a critical cost saver to the programs which could run in the hundreds of millions of dollars on a single program, and it allowed at least a large set of the audience that was involved in decision making a means to early visualizations of the different concepts and just start being able to visualize them and sort of make decisions well prior to having to do any sort of prototype and production tooling that was going to start adding cost and adding risk into the program.
Tod Parrella: I mentioned how important scale and proportion and the relationships are, as well as simulation of a function of a product, all being able to do that on a digital twin – and not only doing that on the digital twin but actually being able to do it on a very realistic representation of the digital twin, where you could actually see it physically, in its near-real color, and look, and feel. And we had a particular program where we went through this process and the early start of the process didn’t really leverage the benefits of the digital twin and everything that we could do. Virtually, right off the bat in that program, actually, I hate to say it, but we were kind of off to a rocky start because key things were missed in the design, key proportions were missed, key relationships were missed, which basically kind of got things off to a rocky start. But, by switching gears and sort of regrouping and taking more advantage of what we could offer in the digital software, including the rendering and animation tools, we were able to sort of turn things around a bit, we were able to turn things around with getting the right scale and proportion down, having people evaluating that much more quickly, and things eventually started to accelerate and ended up on the right track. And actually, that product ended up being one of the most successful products ever sold by my company to market.
Tod Parrella: But I guess the whole point is being that the value of this was doing it at design time in the early concept phases and being able to put people in front of a virtual representation of the product as quickly as possible. You know, at the end of the day, many companies still do end up with a physical prototype of their product, but they arrive at it at a much higher degree of confidence that the product they physically built is the right product, and is the product that’s going to be successful in the market. I might also end the story to say that, visualization, in my view, also spans across the simulation world. And again, being a tool where you can do all this in a single integrated environment where you could run design, create visualizations and virtual representations, as well as run advanced simulations and simulate what would happen to the product as in, maybe if you dropped it? What was it going to look like after you dropped it onto the concrete? We could do that. We could actually simulate that with a high degree of fidelity and we could also put the colors and materials in realistic rendering behind it, to show what the product would look like. And that just became an indispensable tool to the point where we actually, after some of the early days of doing all this, it started to become second nature, it became part of the process. People believed it, people were behind it and they knew that what they were seeing in the digital twin was, in fact, the way it was going to look and how it was going to work – and that made all the difference in the world for not only that brand but for subsequent programs down the road.
Jennifer Piper: Now, we’ve mentioned VR technology a lot in our discussion. And for those that don’t know, VR stands for virtual reality! If you’re deep into the technology world, you may have heard some other realities. I know, it’s a little confusing, right? But stay with me. There’s VR – we know that one. You also might have heard of augmented reality, or AR, or even mixed reality, MR. That’s a lot of realities! So, I had to ask our guests what makes them all so different from each other?
Dave Hutchinson: There’s also XR, as well, which is the fully encompassing term for all of those types of realities. VR – virtual reality – that typically means an experience where you’re putting on a headset and you’re fully immersed and everything that you’re looking at within that experience is CG generated. It’s a fully computer-graphics-generated experience. AR is a different type of device – augmented reality – where you can actually see the space around you as usual but you’re typically looking through some kind of transparent screen and you’re seeing additional information, computer-generated information, overlaid on top of your display. Typically, everything’s fully simulated. Augmented reality is where you might be doing inspection inside a ship and looking where piping may be, that you’re actually inside the ship but you’re seeing additional information about things for servicing and things like that. That’s where that could be useful.
Dave Hutchinson: And mixed reality could be AR or VR but you could consider the example of having a virtual reality experience of a car, for car review, where actually part of the car has been fabricated. And imagine you could actually reach out and touch the door and open it. But, in your virtual world, you’re actually seeing the real car. Whereas, in reality, it may be a horribly painted car with strange fabricated things by the engineers all over the place, but you wouldn’t be able to see that. So, you’re actually interacting with something in the physical world and seeing the result instantaneously being replayed inside the virtual world. So, you might get to sit inside the car, turn the steering wheel, and everything that you touch, then, would be hooked up to sensors, so that you could actually see the results in your virtual world. And this is kind of where a lot of the design-time review stuff is going because, in particular, for executives and stakeholders, they really want to experience the products as though they were real. So, they want to see exactly what they’re going to look like, but they want to touch and feel them and, like Tod was saying, without having to manufacture hundreds of prototypes; actually, you can reduce the amount of prototyping and replace it with a digital twin, as well. XR is essentially a term that encapsulates VR, AR, or MR.
Jennifer Piper: Ok. I understand. Yes, that makes sense, then. There are so many different terms flying around, so that’s helpful. So, I know that you had mentioned earlier when you were talking, Patti, about the early marketing with the design data. And so, Dave, could you talk a little bit about that, and how that’s working with the technology?
Dave Hutchinson: I was wondering how to present this and thinking about marketing in general, and what the consumer experience is, in some ways, that’s always been the thing that has led the way for how visualization and engineering have gone. So, you know, many years ago, consumers would just get single images of their products and if there were 20 colors, you’d get 20 images, maybe on a website, or in a newspaper. And now things have developed where manufacturers want to show all the variations of all their products. So, if you look back five or 10 years, then you’d see, again, people putting things on their websites, which might have maybe 10,000, or 20,000 different images behind them that represented all the different variations of products – through to today, where people are actually starting to directly interact, especially the car guys in the field here, they’re actually interacting live with dynamic interactive graphics on iPads or mobile devices and seeing all the product variations that are available. What’s happening is that during the design time, as Tod and Patti were saying, then, in order to get a product signed off, or to produce the best products or to increase the number of iterations that you’re doing, people really need to see and feel almost the same experience that the consumers are feeling so that they can get a good idea of, “You know, if I sign this thing off, then this is what I’m gonna get.”
Jennifer Piper: Are there other departments or organizations within companies and enterprises that would also be benefiting from this technology?
Dave Hutchinson: That’s a brilliant question! The answer is, absolutely, yes. I mean, yeah, virtual reality is being used on the factory floor, it’s starting to be used in either training, maintenance. And with the advent of the Internet of Things, so-called, when people have their cars or devices or products that they have delivered, actually, you need to know something about the exact model that you got. So, you actually need all the information and that can include visual information. But if we’re talking about visualization, you need your specific variant and products, and you need to know how that particular one works. And so, building as much of the digital twin in a way that you can actually visualize, whether it’s simulation, whether it’s press this button to order a cup of tea – whatever it would be – if you can capture all of that, then the benefits are really high. The digital twin is not just the product that you’re creating; it’s the whole way that you’re manufacturing and all the way through to maintenance and all the way through to sales and marketing. It is the whole story. So, some people are well ahead of the game. The auto guys are well ahead, and other people are starting to see it and starting to talk about it, and I’m pretty sure they’re gonna join in soon as well.
Jennifer Piper: Thanks to Patti, Tod, and Dave for coming on the show and sharing their insights on the world of design visualization. And thank you for joining us on this episode of the Next Generation Design podcast.
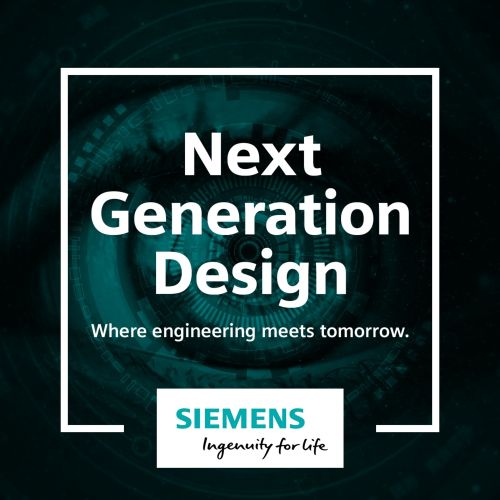
Next Generation Design
As product engineering tools continue to morph and expand at speeds human expertise may not be able to endure, Revolutionary design technologies that span beyond industry borders, will prove their necessity for companies looking to take over their markets in the future. What will the future of design technologies and machinery look like? What will your digitalization story be? Where engineering meets tomorrow.
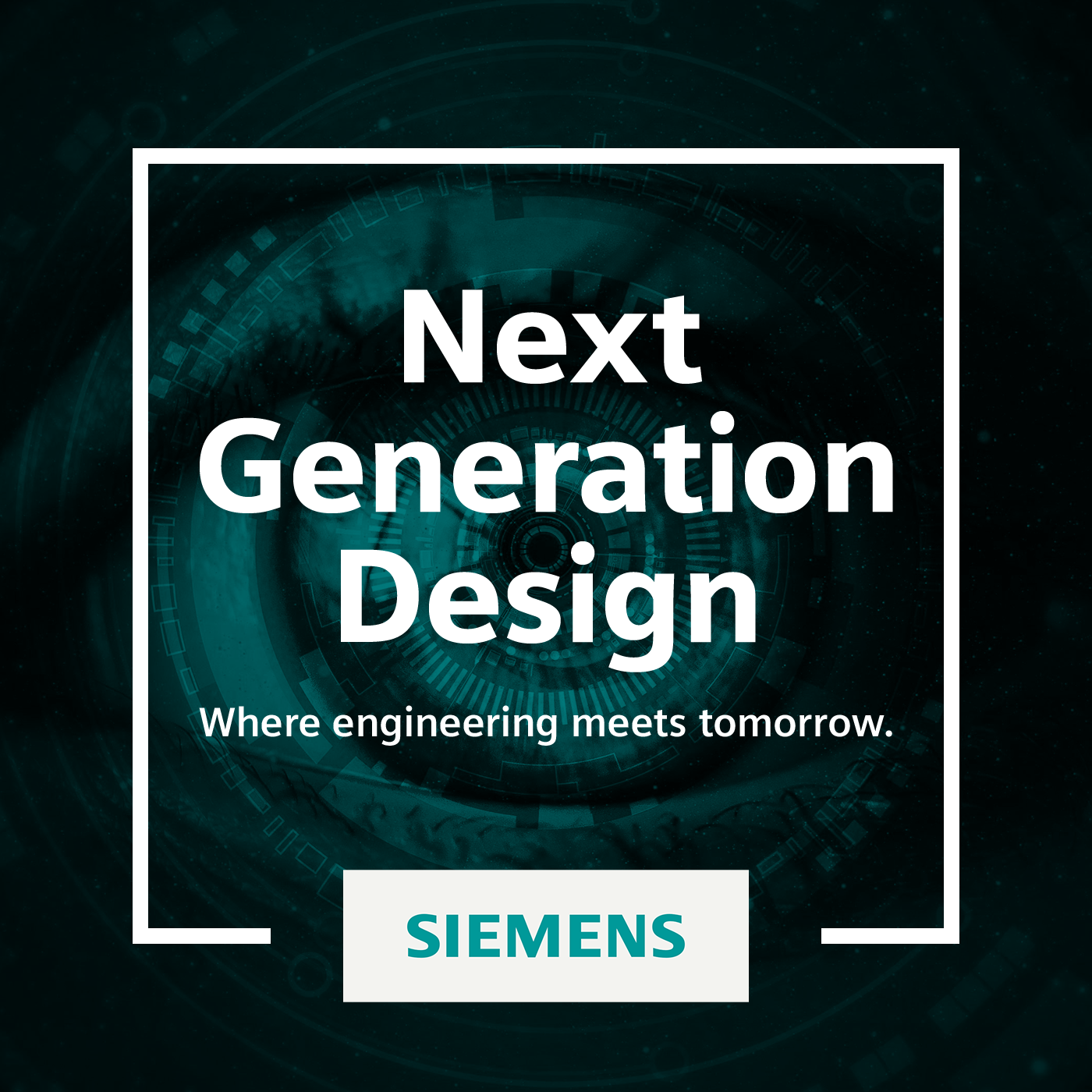
Next Generation Design Podcast
As product engineering tools continue to morph and expand at speeds human expertise may not be able to endure, Revolutionary design technologies that span beyond industry borders, will prove their necessity for companies looking to take over their markets in the future. What will the future of design technologies and machinery look like? What will your digitalization story be? Where engineering meets tomorrow.