Executable Digital Twins: A Smartwatch for Machines
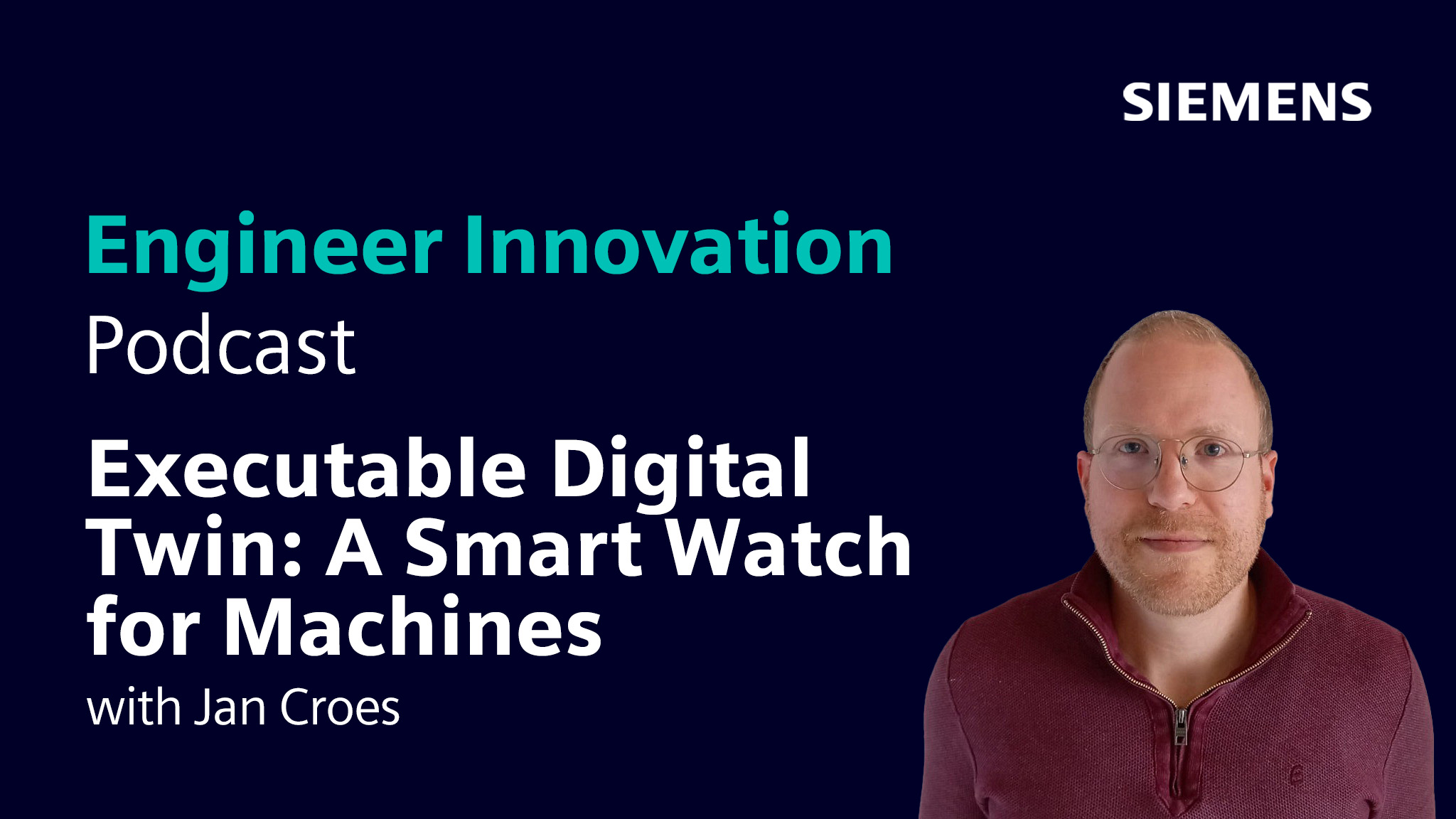
Listen to the Engineer Innovation podcast on
Many of us have become almost entirely reliant on our smartwatches. My smartwatch can tell when I’m stressed. It nags me about not getting enough sleep. It tracks how much I move. It monitors my heart rate 24/7 and predicts how much oxygen is being circulated around my body. And it pings me with an endless stream of social media notifications, that I really should be ignoring.
But what if this technology was available for machines?
At engineering school one of the first things we learn is how we can measure torque and bending on a shaft using strain gauges that convert deformation into an electrical signal that can be measured (and calibrated). But in the words of our guest, Forcebit CEO Jan Croes:
“And sticking strain gauges on a shaft is not fast, it’s not easy, and it’s not reliable. Because what you have to do is you have to build up a sensor from scratch onto a shaft in an environment that is oily, that is messy, there is no room. And what you have to do is you have to completely put a barrier shaft, you have to mount strain gauges, you have to wire stuff, you have to balance it, you have to put duct tape around it, and you have to pray that things don’t fly off.”
Jan Croes, CEO, Forecbit
This episodeof the Engineer Innovation Podcast is about the engineering challenges involved in designing Forcebit a device that aims to make measurements on rotary drive systems as fast and easy as putting on a smartwatch. This is an important application of the digital twin technology in which the combination of simulation and measurement allows virtual sensors to replace physical sensors and increases our understanding of complicated systems.
- The benefits of a combination of virtual and physical sensors over physical sensors alone.
- The engineering technology that allows Forcebit to function
- How data collected from Forcebit can lead to better engineering decisions
- The sustainability implications of reducing over-engineering through improved data
- How engineering simulation empowers startup companies to get their product to market more quickly
This episode of the Engineer Innovation podcast is brought to you by Siemens Digital Industries Software — bringing electronics, engineering and manufacturing together to build a better digital future.
If you enjoyed this episode, please leave a 5-star review to help get the word out about the show.
For more unique insights on all kinds of cutting-edge topics, tune into siemens.com/simcenter-podcast.
- The benefits of a combination of virtual and physical sensors over physical sensors alone.
- The engineering technology that allows Forcebit to function
- How data collected from Forcebit can lead to better engineering decisions.
- The sustainability implications of reducing over-engineering through improved data.
- How engineering simulation empowers startup companies to get their product to market more quickly.
In this episode, I talk to the CEO of Belgian startup Forcebit, who are developing a smart watch for machines. And I started off the interview by asking my guest to introduce himself.
Jan Croes (00:57):
Okay. So, uh, my name is Jan Croes. I, uh, s- recently, uh, founded a startup, it’s called Forcebit, and our aim is to make measurements easy for the machine industry. Basically what we designed is a smart watch which you put on the shaft of a vehicle or a machine and does the most important characteristics related to its health and performance. And for a machine or a vehicle that means the torsional loads, bending loads, and rotational vibrations.
Stephen (01:24):
And so, most of the people listening to this now will be familiar with putting strain gauges onto equipment. So, how is what you’re doing different than just sticking strain gauges onto a shaft and measuring torsion that way?
Jan Croes (01:38):
So, the thing is, or the motto is, we are fast, easy, and reliable. And sticking strain gauges on a shaft, it’s not fast, it’s not easy, and it’s not reliable. Because what you have to do is you have to build up a sensor from scratch onto a shaft in an environment that is oily, that is messy, there is no room. And what you have to do is you have to completely put a barrier shaft, you have to mount strain gauges, you have to wire stuff, you have to balance it, you have to put duct tape around it, and you have to pray that things don’t fly off. ‘Cause that happens [inaudible 00:02:15] and off.
(02:16):
Now what we do, we have a bracelet which you put around a shaft and that gives you this torque and bending straight away without all the hassle that you normally have with putting on strain gauges.
Stephen (02:27):
So literally it’s like a smart watch for your-
Jan Croes (02:30):
Yeah.
Stephen (02:30):
… for your… That’s how you’re describing it as well.
Jan Croes (02:31):
Yes. Yeah.
Stephen (02:32):
Which is a really clever analogy. And how does it… How does the technology work inside your device? If it’s not a commercial secret, of course.
Jan Croes (02:40):
We- We- We patented part of the solution, so all the hardware, which is visible, uh, it’s- I don’t mind telling it. So, what we basically make is we make a weak spring that we put around the shaft and that takes over the deformation of the shaft. And because the spring is so weak, the shaft doesn’t really feel that there is extra part on it. It’s really light, it’s really flexible, so it doesn’t change the system dynamics at all. And this part which we put on top of the shaft, it will deform along with the shaft and this deformation is something that we’re measuring. And that deformation is representative for the torque and the bending moments inside of the shaft.
Stephen (03:19):
So it calcu-… Oh, so a single device measures all those things as well. You’re not just measuring torque. You’re measuring torque, bending moment.
Jan Croes (03:25):
Yeah. And then rotational displacement, velocity, and acceleration.
Stephen (03:29):
Does the device come or will it come in different sizes? Will you have for different shaft diameters? Or is it adjustable?
Jan Croes (03:35):
That’s the thing also. If you’re making a weak spring, putting it around the shaft, it needs to of course comply with the diameter of the shaft. Of course we know that, uh, not every shaft is perfectly round. There is some variation in the diameter of a few tenths because of production tolerances. We can all compensate for those kind of things. But a shaft of 30 millimeters, you fit a sensor around it, it can be slightly smaller, slightly bigger. But still, it fits within a really narrow a- area. That’s- That’s something important to mention.
Stephen (04:04):
So, your device is collecting data. How do your customers use that data?
J
an Croes (04:08):
So, we’re collecting the data. Really the high throughput data. We’re not doing any feature extraction up front. We’re collecting the high throughput data and that one directly goes to the customer. And then the customer, what does he do? He- He evaluates the durability with it, he evaluates energy efficiency, and he evaluates performance.
Stephen (04:26):
And so, you’re intending this to be used inside, uh, a lab for kinda testing, or on final kind of vehicles as well?
Jan Croes (04:35):
It’s really meant vehicles and machines that are in the prototyping phase, having the first field test to really understand what’s going on and to- how to, sort of, improve it. Also in the framework of troubleshooting. If you spotted some- some, uh, weird vibrations are popping up, or if your process is not exactly as you envisioned it and some weird orders are happening or some- some things are breaking down, it’s the quick tool to assess what’s going wrong and how to improve it.
Stephen (05:04):
And so, basically you use engineering simulation, I guess using Simcenter, to analyze and to perfect this device. How have you used simulation and design of… is it… Forcebit, it’s called, isn’t it?
Jan Croes (05:15):
Yeah. So, what we exploited the most is the, um, the finite element package. So first the CAD design, the CAE design. So first we need a design that is very parametric so that we understand how does it size with the shaft diameter. How do we account for, uh, small curvatures? How do you account for thickness of certain parts? Because we need to assess the durability of the sensor, we need to optimize the sensitivity of the sensor, and we need to optimize the contact of the sensor onto the shaft. So there’s a lot… a lot of nonlinear finite element analysis on there to make sure that this contact is just right. We know that there’s a slip, but we need to contain the slip. We know that there will be of course some small deformations when you are clamping the part. We need to analyze ball pre-tension. And all these things we exploit Simcenter for it to ensure that we’re really getting an optimal design.
Stephen (06:11):
And who’s doing the simulation? Are you doing the simulation yourself?
Jan Croes (06:14):
Yeah.
Stephen (06:14):
You’re a CO… You’re a CO and you’re also getting your hands dirty. And so, who’s your colleague who works with you? What’s his name, or her name?
Jan Croes (06:19):
Yeah. He, uh, i- is called Peter and he has a background in, uh, business economics-
Stephen (06:25):
Okay.
Jan Croes (06:25):
… and law.
Stephen (06:25):
So he’s not much help with the simulation part. You’re doing all the dirty, hand down stuff as well. So you have a full understanding of your project, at the moment your product as well. That’s- That’s really impressive.
(06:34):
Um, uh, so in terms of your customers, people who… or the eventual customers for this product, what benefits do you think they can get from better understanding how their devices are performing on the test bed? So- So having a better understanding of what the torques are, what the bending moments. What is the payoff for those guys, do you think?
Jan Croes (06:53):
Well, we noticed that, uh, a lot of companies still tend to oversize their products. We also noticed that a testing campaign quickly gets really, really expensive. And then they have to make a compromise with what they want and what they can afford within a certain timeframe. And because we noticed in testing a big bottleneck is the time plan for the testing campaign. So, you need to make sure the testing space is available, and you need to make sure the machine or the vehicle is available, and you need to make sure that all the technicians are available to instrument the machine, and that really make sure that there’s very high time to do this.
(07:32):
What we mainly do is we shorten the cycle a lot, so it can measure much more. Shorter timeframe, get more value, and keep on feeding this digital twin that you are developing with all the Simcenter-
Stephen (07:43):
And so, we’re also reducing the amount of over engineering. Because, you know, you understand your product better, means you can use less material, uh, less energy. And so, it’s actually a- a way of, you know, designing more sustainable products as well, I guess.
Jan Croes (07:56):
Yeah, indeed. Indeed. Because yeah, the more… the more you can really understand what the loadings are inside your machine, uh, the less likely you’re going to make it more ro- robust and actually need it. And making things small because you can, because you’re not oversizing anymore, you can make things faster. Making things faster means you produce more per hour and the whole cycle gets more energy efficient.
Stephen (08:22):
Um, and so you describe yourself as a startup, but how far along the startup process are you? Have you gone to market yet with this, or is it still a prototype?
Jan Croes (08:30):
So, um, I started incubating the product while I was in university. Noticing that when we’re working with industry that they tended to say, like, a- as I advised them, said, “Look, it’s really important that you need to do the measurements on these particular places,” because [inaudible 00:08:47] build a simulation model for them. And then they said, “Just do more simulations.” Because they were just… It’s such a hassle to actually perform it.
(08:57):
So, I started developing the product and it took me over four years to get a prototype that is good enough, that demonstrates the concept. And then last year, somewhere in the… in October, we started up the company. And- And we burned quite a bit of money to get this problem, uh, market ready and now we are really… you cannot see it, but it’s really this close. So it’s like one month, maximum two, and then we have the pilot cases with our first customers.
Stephen (09:23):
That’s exciting. So thang- thank you for coming to Realize LIVE to tell your story when clearly you were at critical time for the company. But it’s good to get the word out, isn’t it, as well. And- And hopefully we can… we can do that as well. It also seems to me that this is just a great time for this sort of technology. We’re talking at this con- Realize LIVE you’ll hear people talk about digitization. But, you know, we live in a world, like as you say, where it’s difficult to measure the sha-… uh, the- the torsion of a shaft. Which, you know, in engineering school, that’s one of the first things you do. Yeah? And it’s… You’d think it’s one of the problems that’s already been solved.
(09:55):
So- So having this capability to more easily model those things, or measure those things, I think it’s- it’s a really critical time. And I- I would imagine that obviously your core business model is in product development and trying to understand new products. There must be loads of old products, you know, existing machinery that’s in operation today, but we don’t have a good understanding of how it works. And so, that’s surely another market as well, isn’t it?
Jan Croes (10:18):
Yeah, indeed. So, in the existing portfolio of machineries that are already out there, we already know a lot of them are over damage. We also know that the refurbishment is becoming more and more popular every time, and also that the investment of a mash- new machine is also getting a lot bigger. And then analyzing which parts, which motors are oversized, which par- subsystems are overcharged, that can help you if you’re refurbishing it. Instead of, um, we’ll use a new gearbox. I will change a different motor. That will help us to assess what are the loads on the system and then, if we make a design change, yeah, what is the best choice to make.
Stephen (10:57):
Yeah. And I also think there’s lots of opportunity. Um, again, your- you’re manufacturing a device. But for people to use the device, that’s part of digital twins as well. So, we talk a lot about you… Obviously your business is based around the difficulty of putting sensors on equipment, yeah? You’re making it much easier. But you can’t have sensors everywhere. And so, combining simulations, which you’ve already done, you know, of the shaft with your sh-… the sensors that you’re giving, gives people the ability to predict nos- not- not only what’s going on where you put your Forcebit smartwatch on the shaft, but across the whole shaft. You have that information.
(11:32):
And- and that’s a critical part of this whole digital twin story, is having access to good sensors, reliable sensors. I think that’s a- a really impressive and exciting development.
Jan Croes (11:44):
Yeah. It’s also the main reason why I didn’t start my career as a testing engineer. I build a lot of models in Simcenter training sim and I realized it’s super nice and gives you a lot of power to design what if scenarios. What happens if I boost up the speed? What happens if I change a subsystem? But then we also noticed that there were some parameters that are quite uncertain and that changes the conclusions. And that made me realize that it really needs to make this connection with experimental data, because the digital twin is only as powerful if it really complies with reality.
Stephen (12:18):
Yeah. Yeah, absolutely. And that’s- that’s the issue, isn’t it, of all the… Well, the whole issue with… So, we can talk about digital twins, but they’re about generating huge amount of data. But you have to be able to trust the data, because otherwise… You know, we talk about machine learning. You’ll hear a lot about this week, about artificial intelligence. But if that data isn’t good, or from simulations which are not good enough, then the results.. you- you’re training an algorithm to do something using the wrong data and that’s not impressive either as well. So, I think you have a… to me it sounds like a very exciting product and, uh, one which I’m sure will be very successful as well.
Jan Croes (12:53):
I- I hope so too. The sign of the market are good. We know that there are people waiting for it. I also… I think it’s important the put next to all the artificial intelligence part, because sometimes artificial intelligence has led to the belief that merely the fact that having data will allow you to analyze everything. But it’s really the type of data. It’s really at the source, that the source of the data goes through your full analysis. And if the source is crap, it’s garbage in, garbage out.
Stephen (13:22):
Yeah. Always, yeah.
Jan Croes (13:23):
And- And- And that I think there, exploiting simulations to understand where do I need to measure and then measuring stuff that is actually physical, that tells you something about the energy efficiency, about performance, makes a big difference. Than saying I combine a lot of things and I have a feature and I see that this feature does something, but I don’t really understand what it means. I just have a cause-effect, but I don’t understand the relationship behind it.
(13:50):
And that’s also something that we want to try to do. We want to exploit the physics. That it will not only help for this particular design, but it will help also feeding your model, that the next generation of design can also benefit on. Because you’re really making sure your model is more representative of your reality. And if the physical model is representative, it’s scalable for your next design.
Stephen (14:15):
I’ve been working in simulation for 30 years and validation was always something you did maybe once or twice using ide- idealized scenarios at the end of the process when it was probably too- too late to change it. So, getting earlier, cheaper, more effective testing so you can validate your- your stress models or whatever models you need, is- is- is incredible and a big, big, big advance, I think, for- for the industry as well. So…
Jan Croes (14:40):
An important thing is also after the fact. Because most of the time a system integrate, it gets parts from different suppliers, and every component supplier has a certain set of specs. We don’t really know whether they are correct or not. They are integrating things and it doesn’t work. Who is to blame? The person who set the specs, or the person who designed the gearbox, or the motor, or whatever? And then doing a validation, a quick check. Does my torque, does my vibrations actually comply with the specs I put out for? That helps you to decide, well yeah, where is the discrepancy? What do we need to change?
Stephen (15:18):
Yeah. I- I get that completely. So- So that- that’s also a big problem. So, uh, so- so you’re based in Leuven still. Where- Where would you intend to manufacture the produ- product? Or haven’t you got that far yet?
Jan Croes (15:31):
Well, the- the nice thing now is that you can make your designs very detailed, very customized, and that, yeah, the internet just makes it very easily available. Additive manufacturing really lowered the threshold to making something. I can have a really high end [inaudible 00:15:49] milling machines just by sending the drawings and they come back to me within two weeks. So that really lowers the cost of the hardware I need and then it’s the… what we only do is assembly.
Stephen (16:01):
Okay. But that… And that’s really important for a startup like yourself. Trying to… Trying to get those first prototypes working is- is… yeah, is really expensive. And once you- you get through all the problems of doing that, then- then you’re a big step forward, uh, closer to- to going to market.
Jan Croes (16:14):
Software licenses are also very expensive, so, uh, if we can (laughs) get some endorsement left and right.
Stephen (16:21):
Oh no. So- So you’re the second. So I’ve interviewed about five people today already, and you’re the second person who’s come in here as a startup as well. And, you know, I know that last week I was talking to- to Jean Claude, who is the boss of our division. He wants more examples of sustainable startups as well. ‘Cause, you know, that- as… You know, the name of our podcast is Engineer Innovation, and actually, you know, you get so much innovation from mature products or mature companies. It’s guys like you who change things as well.
(16:50):
So, I think Siemens probably would want to be associated with your brand, and I think, you know, trying to have a chat with people like Jean Claude Ercolanelli, who we can try and introduce you to, would be really… I mean, it’s worth having that conversation with him as well, because we should be supporting startups like you. Because of course we can sell you lots more software licenses when you’re operating in scale as well, so there should be some sort of investment as well. So- So I think those- those are conversations worth having this week.
(17:16):
I know that he’s looking for examples of startups using our software to solve these problems and, you know, the sort of things that will help us solve the climate emergency ultimately. You know, and it’s… I know that’s not explicitly the role of your company, but there’s loads of benefits in reducing energy, reducing costs, reducing materials. I think that’s a- a huge part of all this. And we don’t… we don’t get to solve these big problems without lot- making lots of… lots of changes, and this is one of them as well. So, it’s really exciting as well.
(17:41):
So, this is… Is this the first time you’ve been to Realize LIVE?
Jan Croes (17:44):
Yeah. You- As university in- at one of these, um, Siemens events, but I think it had a different name then.
Stephen (17:48):
When was it? Where was it? Can you remember where was it?
Jan Croes (17:52):
It was somewhere in Germany.
Stephen (17:56):
So, okay. But- But do- di- did you… did you get any value from attending the previous conference as well, do you think?
Jan Croes (18:00):
Yeah, yeah, for sure. Because the thing is, it’s a nice mix of having a lot of, uh, applications from customers. Really seeing how they do that, how they… how they struggle with things and how they solve that. So, in that sense it- it’s quite inspiring. And also, it’s a good idea to get a bit of a feeling on the air what are the new stuff that is happening in software, because it goes super fast and it starts from only… first it was only system simulation. Now they’re integrating more and more of the value chain. And it’s also nice to see that even a mastodon like Siemens needs other competitors. They are not… are not competitors. Other- Other partners to really ensure that they can offer the whole value. Even they cannot do everything.
Stephen (18:42):
I think that’s the difference between Siemens and some of our competitors. We like to have an open ecosystem so that you can use whatever tools are best suited to you, because we can’t cover it all. And it’s interesting that you said… you said that in that little section there. You talked about seeing the struggles of other people. Because I think that’s really important as well, is under- understanding that engineering, you know, doing new stuff, innovative stuff, it’s not easy what we do. And the fact that everybody else struggles and having kind of… u- understanding that and see how people solve their problems I think is a really key point about situations like this. I think we all live in our own little simulation bubbles and don’t see everybody else is having a hard time of it as well. So that’s quite a interesting observation, I think.
Jan Croes (19:24):
Yeah. It’s also good for your mental health. Because if you see people struggling sometimes, they get the belief that at simulation you click a few buttons and you’re there. Really it takes a lot of effort to make something. There’s a lot of failing. And then, if you see that the other big players are also struggling, it’s- it’s- it’s only natural. There- There is no… There is no quick fix. So, that helps.
(19:47):
And also, I also look at things that are a bit outside of my field sometimes to get a bit of inspire. And the broader your view is, it- it- it can only help. Because you don’t know what are the next steps along your path, or which- which field that will be.
Stephen (20:01):
And hopefully you might find some- some potential customers here as well.
Jan Croes (20:04):
Yeah, yeah, indeed. If we would find some money, that will also be great.
Stephen (20:07):
Yeah, that’s good. And investors as well. So, I think… I think that’s a really interesting application. The production, that- that’s- that’s a story we’d like to follow. So- And I’m confident that you’re gonna be successful, so good. Thank you very much.
Jan Croes (20:18):
Good. Thanks a lot.
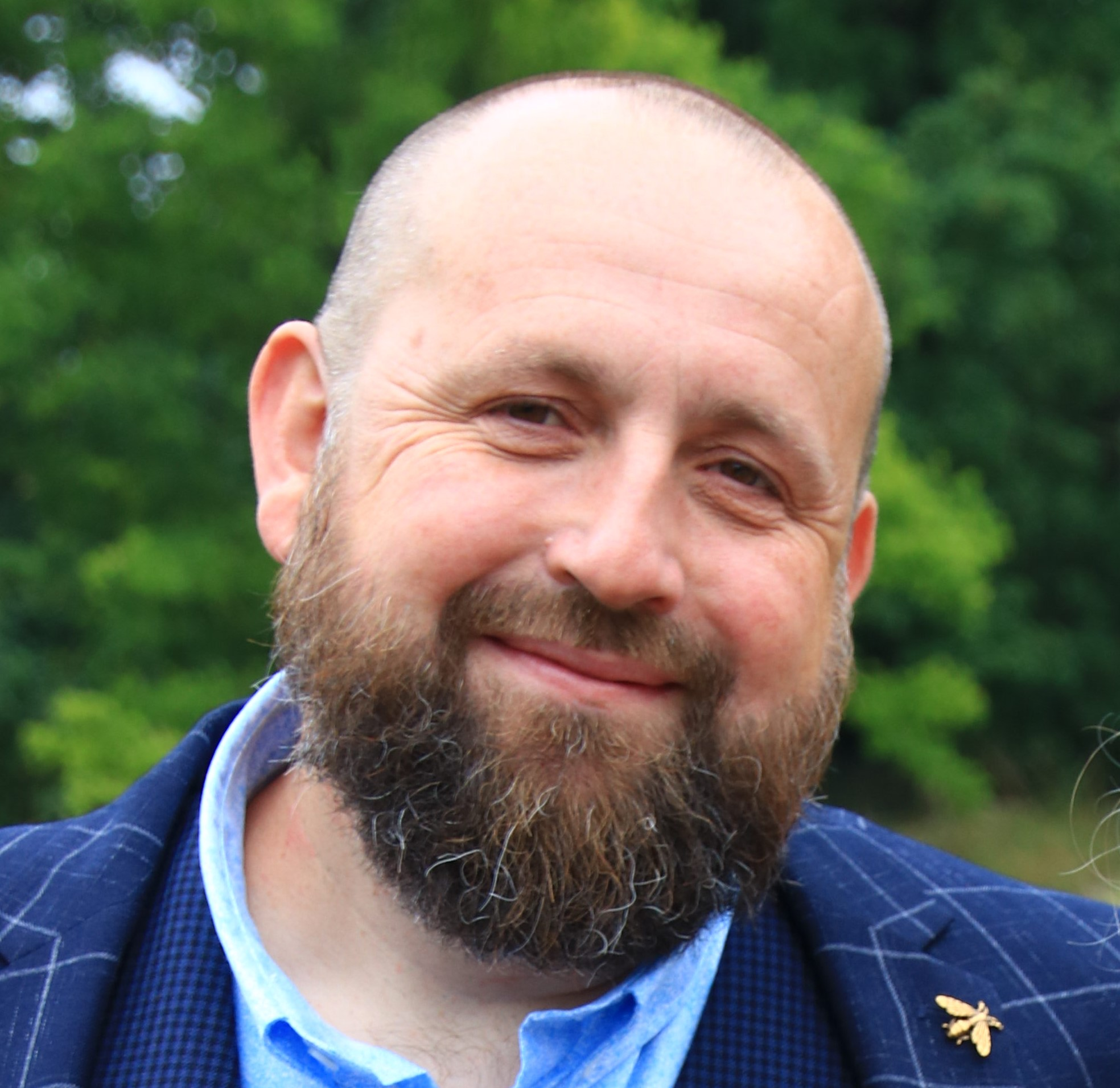
Stephen Ferguson – Host
Stephen Ferguson is a fluid-dynamicist with more than 30 years of experience in applying advanced simulation to the most challenging problems that engineering has to offer for companies such as WS Atkins, BMW and CD-adapco and Siemens. Stephen is entirely dependent on his Garmin Smartwatch.
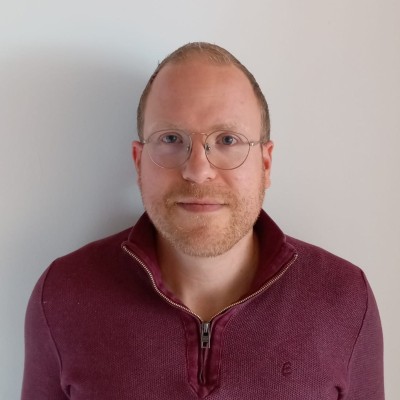
Jan Croes
Jan Croes is a mechanical engineer with ample experience in research, business development and project management. Many projects with various industrial players in the mechatronic industry confronted him with the pain and reluctance companies feel when experimentally assessing rotary drive systems. This inspired him to come up with a brand new technology making load and force measurement FAST, EASY and RELIABLE
Take a listen to a previous episode of the Engineer Innovation Podcast: “Adapting to a New Era of AI”
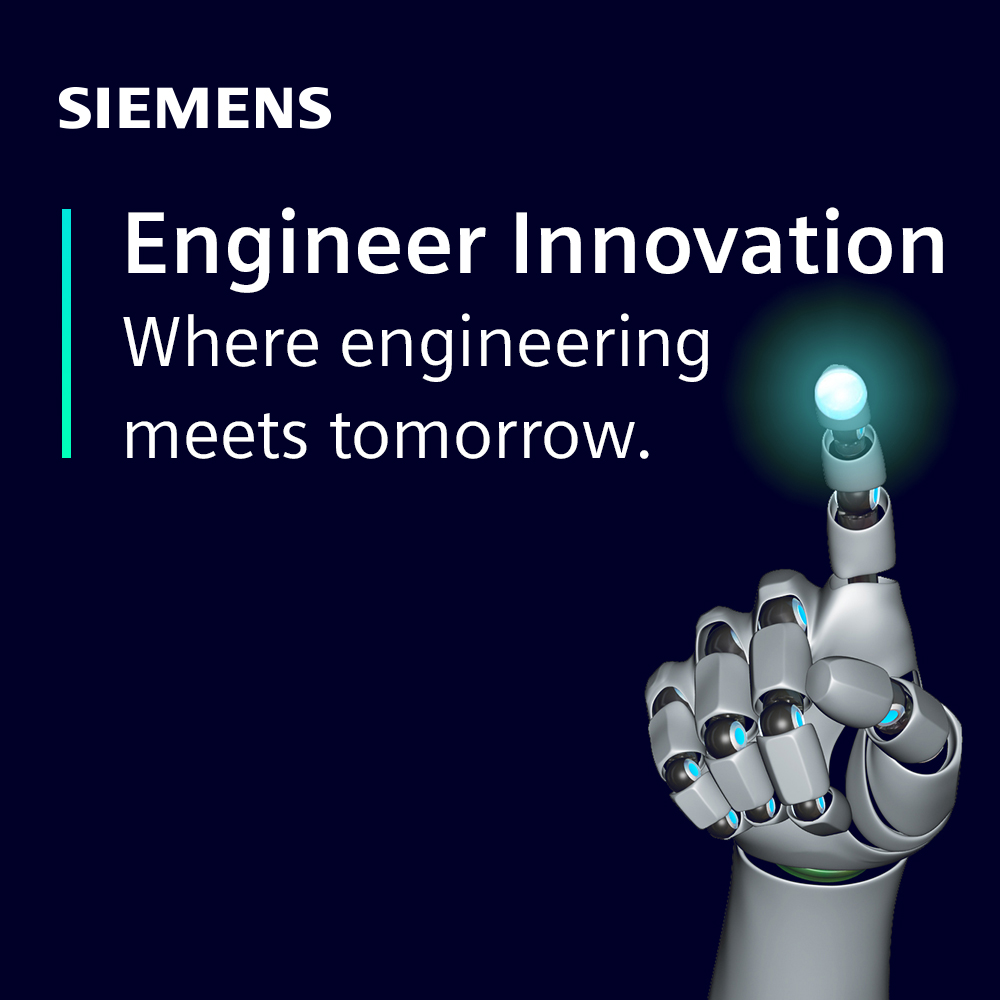
Engineer Innovation Podcast
A podcast series for engineers by engineers, Engineer Innovation focuses on how simulation and testing can help you drive innovation into your products and deliver the products of tomorrow, today.