KineoWorks Version 7.0
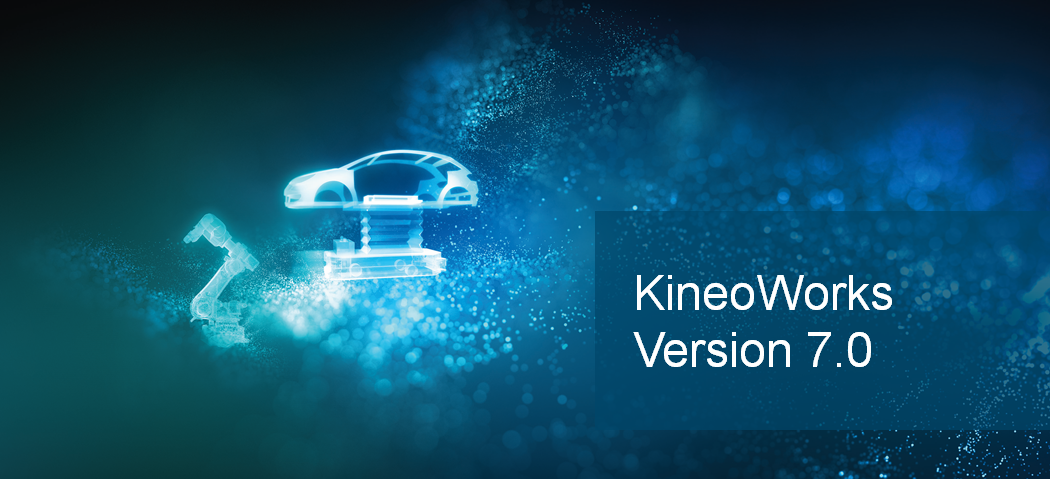
KineoWorks is a software component that automatically computes collision-free motion, solving complex path-planning problems in applications such as robot simulation/control and virtual assembly/disassembly verification. KineoWorks version 7.0 includes the following new features:
Accelerated scenario development and verification – Kwik
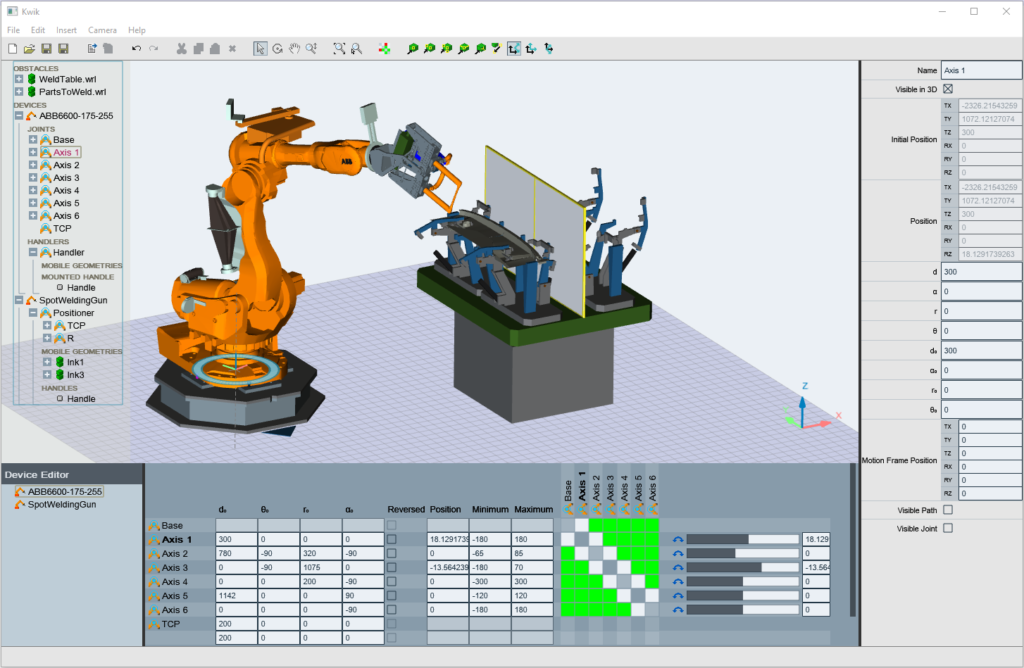
KineoWorks version 7.0 comes with a new standalone application – Kwik – for accelerating your KineoWorks application development.
Kwik has a simple and ergonomic graphical interface for configuring robots, devices and cells quickly and easily, enabling you to develop and verify scenarios for use in your own KineoWorks application.
Some of Kwik’s key features include:
- Model a complete robotic cell with multiple robots, devices, tools, etc.
- Load kinematics information direct from the robot manufacturer’s specifications – DH parameters, joint distances, home position axis values, etc.
- Import CAD data to define robot geometry, work-stations, work-pieces, etc.
- Configure collision detection settings -self-collision, cell-level interference, etc.
- Share data between Kwik and your own KineoWorks application via Kineo XML
Watch this video to learn more about Kwik:
Once defined and verified using Kwik, robot systems and their operating environments can be exported in Kineo XML format for re-use in other KineoWorks applications.
Trajectory Simulation
In robotics, a trajectory represents the movement of a robot as a function of time and is described by a series of positions, velocities and accelerations for the moving components.
By combining the geometric path that KineoWorks computes between positions in space with the motion laws for a given robotic system, it’s possible to compute collision-free trajectories automatically. Version 7.0 introduces the capability to set up and simulate such trajectories on robots. A Robot Controller Software (RCS) module is included to enable full trajectory simulation without the need for a 3rd party controller.
Trajectory Optimization
Version 7.0 also enables trajectories to be optimized for user-defined criteria, including robot cycle time and/or energy consumption. To achieve this, KineoWorks implements a genetic algorithm which applies principles of evolutionary biology to identify the best-performing trajectories. A simplified example is illustrated below:
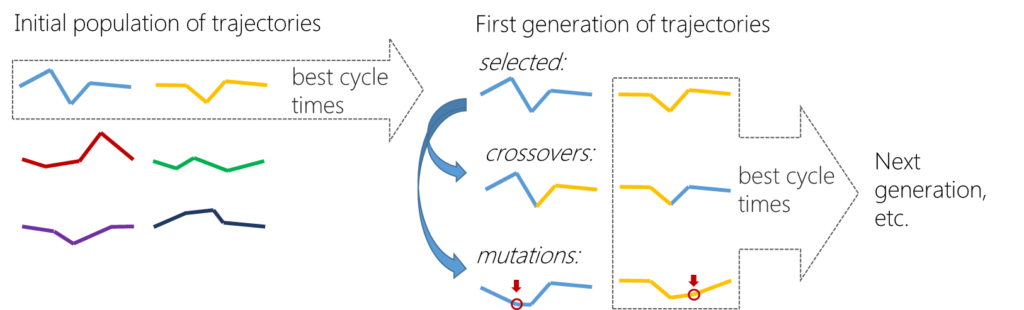
- A population of candidate trajectories is evaluated against cycle time.
- A subset of trajectories that achieves the best performance is selected (“parents”)
- The parents are subject to genetic operations, including cross-over and mutation, to generate new candidate trajectories (“children”).
- The parents and children are evaluated against cycle time. The subset of trajectories that achieve the best performance form the next generation of parents.
- Steps 3 and 4 are repeated for a user-defined number of generations. The optimal trajectory is the best-performing trajectory in the final population.
In initial test cases conducted by our research and development team, the genetic algorithm dramatically accelerated the optimization process, compared with optimization by the user. In addition, cycle times and energy saving improved over a range of 12-34%, compared with the results of user-optimization.