Quality Management that Shifts the Focus to Improvement
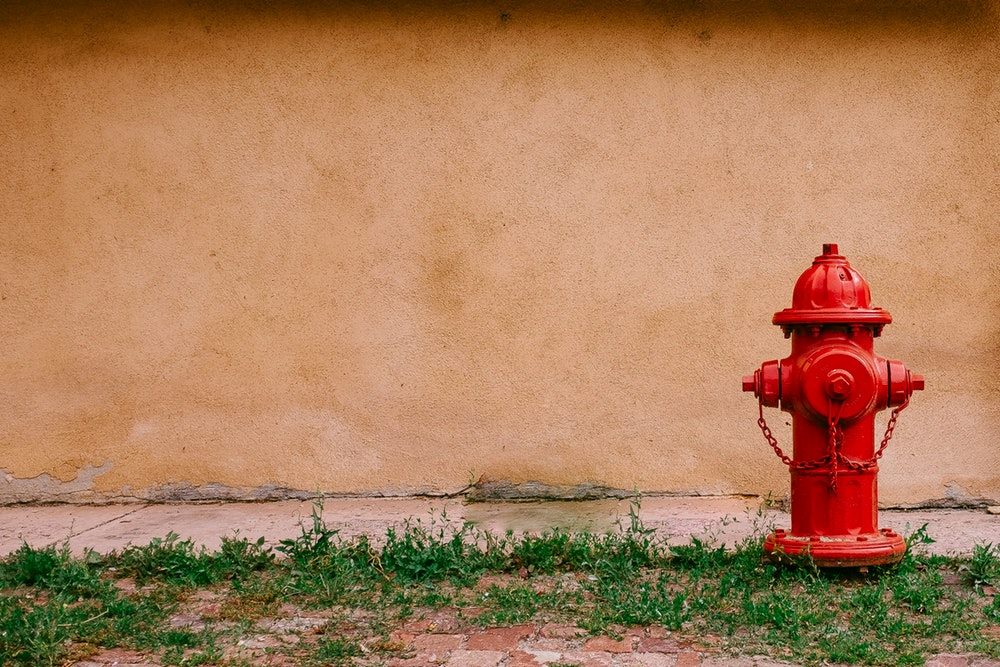
Quality managers have to spend some of their time putting out fires. The question is, how much?
With the right kinds of continuous improvement processes in place, effective quality managers spend less than 5% of their time dealing with urgent problems, and much more of their time driving production costs down. Without good continuous improvement processes and process management software, managers can spend more than 30% of their time tackling costly late-stage problems.
Production manufacturing processes are cyclic, they iterate repeatedly. But unless product engineers can identify, capture, and apply the lessons learned on each iteration for the next cycle, quality suffers and mistakes get repeated. Then they are putting out fires, again. The question is, how do you capture all these errors in a systematic way in order to prevent them from recurring?
Traditional quality control processes often use paper-based reporting. Notes are kept in a binder, but if that binder’s in Akron, OH and you need it in Fremont, CA, it’s no help. Project spreadsheets only capture point-in-time information. Quality data and engineering notes may be scattered across your whole enterprise. And what about your engineers and your off-shore plants who need to see it all in a different language? If you could solve your quality problems early in the production cycle, you’d be saving 90% of the costs of fixing them later.
A robust closed-loop quality system is your answer – a system that tracks all events and issues during the entire product life cycle, ensuring that these items are properly addressed in the short term, and that this information finds its way back to the product development process. Those steps enable appropriate changes to the design before it gets too expensive to change and retool.
Closed-loop quality management allows you to:
- Communicate changes throughout the life cycle
- Work on FMEAs and Control Plans collaboratively with a Document Management Solution
- Use a single source to update all information about any characteristic, including inspection and test data
- Map corrective actions to design changes
- Support quality initiatives like lean manufacturing and operational excellence
- Communicate easily in multiple languages.
Quality management software that allows more time for the quality manager to focus on improvement has all these capabilities. Production teams anywhere can abstract important information throughout the product cycle. This, in turn, enables lessons learned to be applied to new products of all types in the future.
Spend less time putting out fires, lower your costs, and achieve continuous improvement with a full-function quality management system. Visit our website for more information.