Meeting Regulatory Quality Requirements in the Automotive Industry
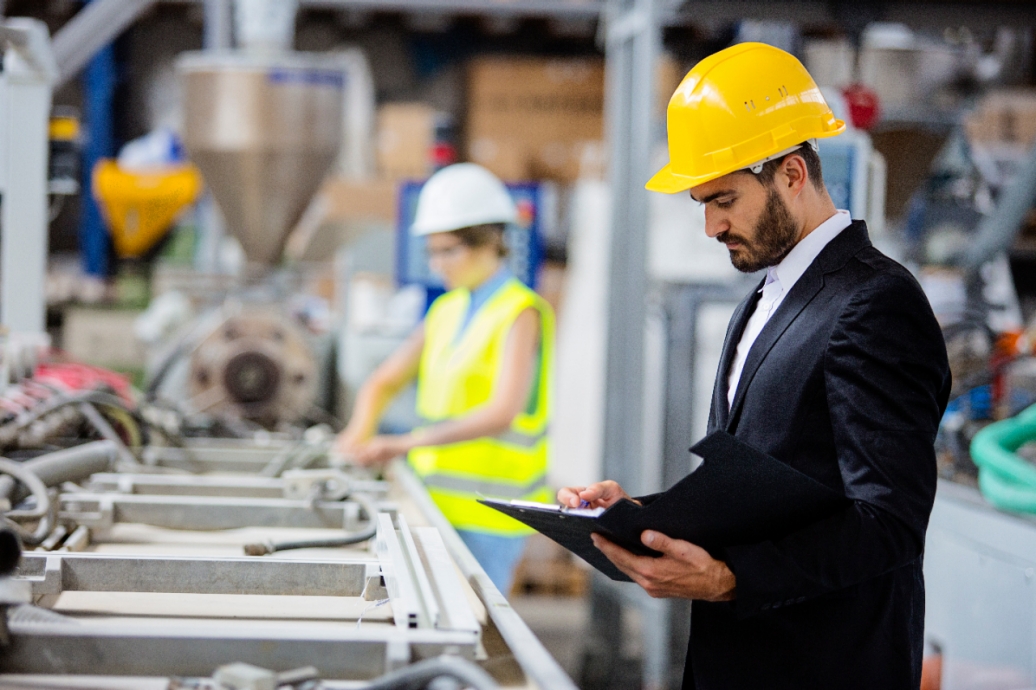
How many mistakes do we make? Do we really solve the problems? Sometimes typical solutions to a problem are based on quick actions to contain the problem itself. But only if we deeply analyze root causes and implement measures to correct those underlying flaws can we expect the problem not to occur again.
Applying the adage, “An ounce of prevention is worth a pound of cure,” to an industrial context, what are the quality standards we are required to meet, and what tools help us to avoid recurrent mistakes and root out the problems?
Direction from International Standards
IATF 16494:2016 (from the International Automotive Task Force) is an automotive-specific standard that is aligned with the ISO 9001:2015. The focus of these regulations is to provide both guidance and tools for a company to develop a strong quality management system (QMS).
According to ISO, to pursue the model of process-based quality management defined by the standard, it is important to focus on:
-
- Comprehending and meeting requirements
-
- Evaluating the added value from each process
-
- Gaining results from processes
-
- Continually improving on the processes themselves
So, in the model proposed by the ISO, continual improvement is of fundamental importance.
On top of ISO 9001, IATF adds requirements in a specific section dedicated to improvement, including:
-
- Problem solving
-
- Error proofing
-
- Warranty management system
-
- Customer complaints and field failure tests
What happens with regard to continual improvement when a company must be certified by a third-party organization for ISO or IATF? What are the main parameters the auditor uses to judge how much improvement is needed to “pass the exam”? For any industry, but especially the automotive industry, an auditor is interested to know the mechanisms by which you are performing the improvement. It’s not enough to provide a description in the quality policy documents of the company’s philosophical concept of improvement. It’s important to demonstrate the workflow in place to improve your processes effectively.
Ideally, an organization will improve day by day in the effectiveness of its QMS. The main tools that could be used are internal policies, audits, data collection and analysis, but a special focus should be given to the management of corrective and preventive actions.
What elements are needed to address IATF’s specific improvement standards?
First, if a nonconformity occurs in a production process, it is important to analyze the issue and to define the root causes. Once the main causes of the nonconformity are discovered by using specific quality tools (such as Ishikawa, 5 Whys or 8D), corrective actions should be undertaken to resolve problems at the root cause.
Once these immediate corrective actions are put in place, they must be reviewed to ensure that they are having the intended effect. Corrective actions usually mean you will need to update your QMS processes and/or risks and opportunities determined during your planning processes. Records describing nonconformities, actions taken, and the results of those actions must be kept. The problem-solving process must use error proofing approaches.
Moreover, if the organization is providing a warranty on products, it is mandatory to define a warranty management process. To meet this requirement, the organization has to structure the analysis and collection of customer complaints and field failures. For example, a plan must be created to collect the returned parts from services, to analyze them by comparing them to the quality periodic failure rates (or key performance indicators, KPIs) and must define corrective actions to improve the overall product quality perceived and delivered to the customers.
Finally, the company has to demonstrate that its processes are capable and stable. To fulfill this requirement, the organization is obliged to document the processes (methods, targets, workflow, KPIs). The creation of a quality improvement plan for all aspects of the product and manufacturing processes is a critical tool, because it is important not only to track and provide documented evidence, but also to prepare a risk analysis and a manufacturing process plan.
How does Siemens Opcenter Quality (formerly known as QMS Professional) support your company’s efforts to fulfill the auditor’s requirements?
To continually improve your quality processes, Siemens Opcenter Quality (formerly known as QMS Professional) supports your company with an end-to-end, closed-loop approach to quality.
Root cause analysis and problem-solving tools are capabilities provided by Siemens Opcenter Quality
(formerly known as QMS Professional), as is full traceability of actions taken. Siemens Opcenter Quality modules that help manufacturers fulfill these requirements include Control Plan, Failure Mode and Effects Analysis (FMEA), Statistical Process Control (SPC), Audit and Action management, Concern and Complaint Management (CCM), Supplier Portal and Warranty Management. The plan-do-check-act (PDCA) approach is ensured. All data, whether it comes from a machine, human or test, are consolidated in one, always available, easily accessible system).
Today, the Automotive industry needs a quality platform built to support evolving regulations. But more importantly, it needs a platform that delivers pounds of prevention, so manufacturers can avoid needing to cure quality defects that escape to the market, and the potentially devastating impact to their customers, their brands, and their bottom lines.
Discover Siemens Opcenter Quality (formerly known as QMS Professional) today.