Lights-out manufacturing – the myths vs the realities
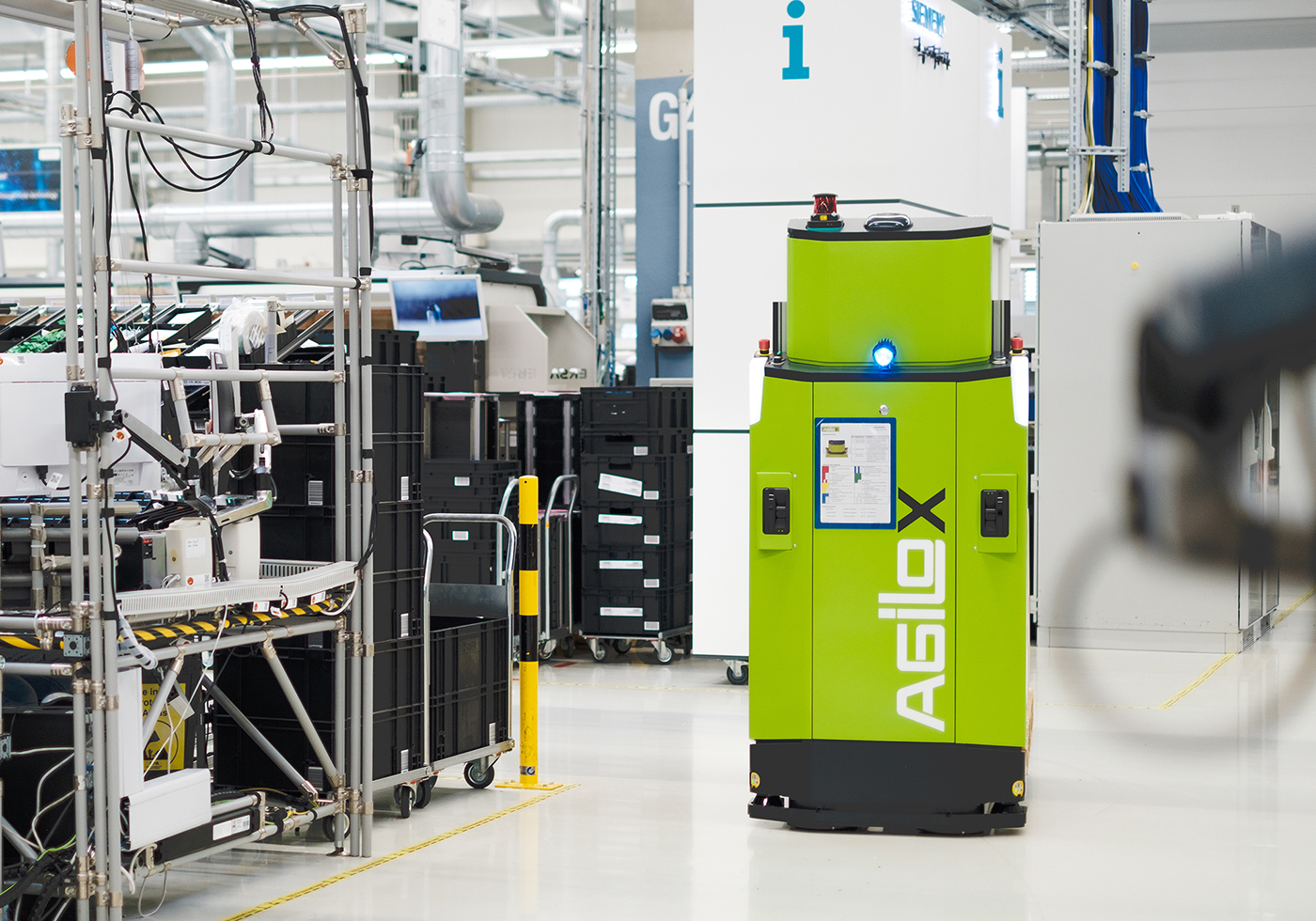
Reduced labor costs, automation of monotonous processes, agility and flexibility to meet changing demands, and increased efficiency are some of the drivers exerting tremendous pressure on virtually every business function and process in the manufacturing industry. These factors are forcing manufacturers to reconsider their strategies and explore viable options to combat these challenges. As manufacturers contemplate the future of factories, a “lights-out” factory appears to be a promising option.
The challenges of lights-out manufacturing
However, converting or constructing a fully lights-out factory depends on various factors and can be a highly expensive endeavor. To establish a complete lights-out factory, several components are necessary, including automated guided vehicles (AGVs), self-configuring machines like CNC machine tools and robots, self-loading and unloading production equipment or robots for each production step, reconfigurable conveyor belts, a large number of sensors, sophisticated vision systems, a comprehensive digital infrastructure, and a plethora of control software capable of managing the scheduling and coordination of the entire production process.
What is a lights-sparse implementation?
Consequently, the concept of lights-out manufacturing, where human involvement is minimal to the extent that the facility can operate in the dark, remains a rarity. However, for manufacturers, lights-out manufacturing is not an all-or-nothing proposition. Instead, manufacturers can adopt an incremental approach to lights-out implementation, commonly known as lights-sparse implementation, which does not require a complete transformation of conventional or smart factory operations. It involves identifying specific processes, areas within a facility, or time blocks during production where crewless operation is both feasible and valuable. This enables many manufacturers to enjoy the benefits of autonomous production without fully transitioning to lights-out manufacturing.
Read more about the role of Manufacturing Operations Management in a lights-sparse factory
A recent MachineDesign.com article explores the critical role of Manufacturing Operations Management (MOM) in implementing a lights-sparse factory, using a case study of Siemens’ successful implementation of an autonomous electronic box-built process with a laser, PXI testing, box assembly, and final assembly station at one of its factories in Fürth, Germany. The orchestration of all capabilities, as well as transportation, was achieved through the Siemens Opcenter MES system, which includes an advanced scheduling algorithm for online optimization.