Emerging Manufacturing Technologies to Watch in 2021
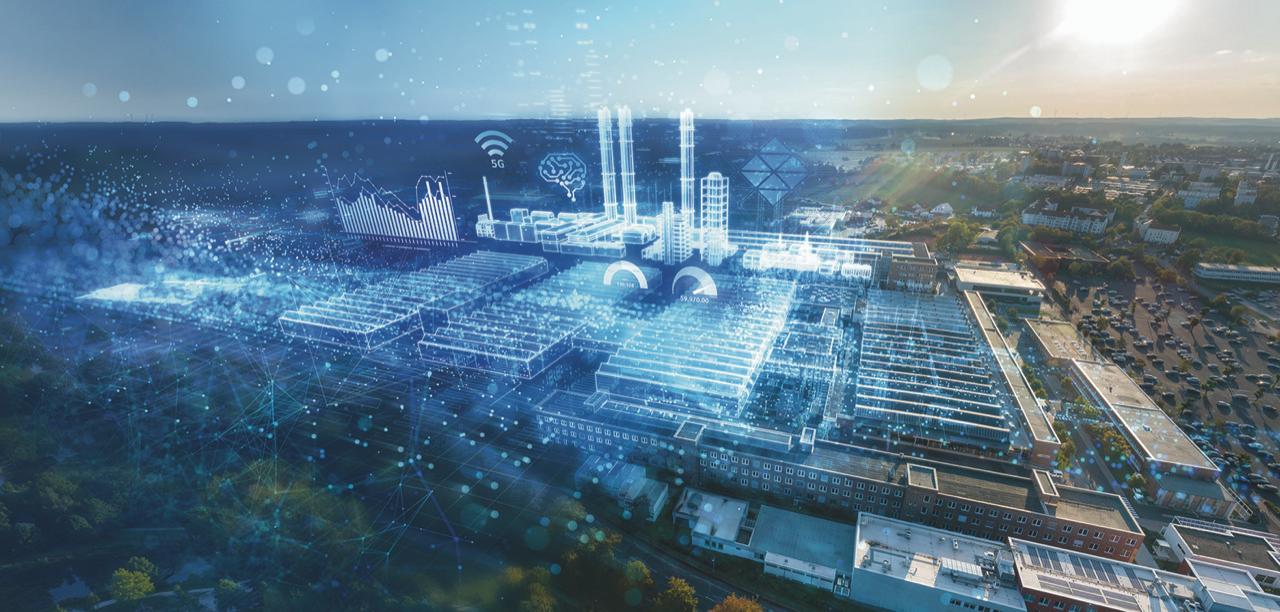
Zvi Feuer is senior vice president of Digital Manufacturing Software Solutions for Siemens Digital Industries Software. Digital Manufacturing Software develops software products to deliver world-class solutions for Manufacturing (Part & Assembly) planning, simulation, and validation and Operations (MES, Scheduling, Quality and automation)
In a recent blog post, I shared my perspectives on 2020 and the importance of digitalization for the future of manufacturing. Having a good digital twin of your products and manufacturing process is essential. It not only helps you produce higher quality products and a lower cost today, but also forms the backbone for manufacturing technologies that are just around the corner. Today, we will explore some of these emerging technologies and the role of digitalization.
Four Pillars for the future of Manufacturing
Our goal at Siemens is to build software solutions and services that can enable any engineer on the globe to plan, design, simulate, prepare for production and produce innovative SMART products in a cost-effective and timely manner, while also supporting the environment and providing significant, tangible value to the consumers of these products.
We build our vision of the next five years on four pillars:
- Make me a Product – transform business models with an online marketplace and make our solutions available to the world. Include solid links to crowdsourcing, buyers, suppliers, machine vendors and material vendors, where anyone can upload their challenges and we will support or help find who can support. (democratizing access to top of the line Digital Manufacturing technologies)
- Self-Organizing Production, more relevant to manufacturing. – offer a new level of flexibility in Digital Manufacturing planning and operations to support “lot size one, Mfg. on demand”.
- Smart and Digital Service – extend the Digital Twin to the service lifecycle.
- Data-Driven Engineering, Manufacturing, and Service – harness the ability to collect, analyze and turn data into actionable information.
These pillars form the foundation of your future manufacturing processes and serve as an enabler for tomorrow’s manufacturing concepts and technologies.
The Lights out factory
One topic we see regularly is the concept of the lights out factory or the dark factory.
About 30 years ago, I was a young engineer in the Israeli aircraft industry. I was asked to work with a large aircraft manufacturer as part of an exchange program. They had just bought a new MES to support flexible manufacturing. They wanted to introduce a concept that they called the lights out factory. To do this, they wanted to connect four or five CNC machines with an AGV, a conveyor, and a computer. The idea was to work two manned shifts and a third, unmanned shift in which a robot would feed the conveyor and the parts would move automatically. It never worked.
I think today we are closer to being able to support something like this due to a higher level of automation and a better way to sync between robots that are feeding the machines and the components themselves. However, some type of supervision is still necessary today. We need to prepare for this unmanned shift far in advance. Working two shifts to prepare for the third unmanned shift, you may be able to do it today. This is only possible thanks to the fact that we have advanced enormously in the domains of automation, robotics, gripping, machine learning, pattern recognition, and vision systems. If we can put all of this together, we may get to the point that in a CNC shop, where in some cells we can have a set of missions that are executed overnight without supervision or with one person who sits in a control room, but the factory itself sits empty.
Digitalization is critical because the basis for this level of autonomy is to have a good digital twin of the production floor and the production facility so you can properly simulate what you want to do and how to manage disruptions such as a machine going down during the unmanned shift.
Cloud Technology for Manufacturing
From a technology point of view, we think that companies will slowly go to cloud, but the cloud presents a bit of a dichotomy. On one hand, companies, especially smaller ones with limited IT resources, want the lower cost of ownership, ease of deployment, ease of use, and elasticity promised by the cloud. This must be balanced on the other hand with security risks posed by managing manufacturing data in the cloud. When it comes to manufacturing and shop-floor, we have seen adoption of cloud to be fairly slow as companies try to understand the best models for managing production data in cloud.
The cloud enables significantly greater access to the vast stores of data generated in every phase of manufacture, greatly enhancing manufacturing intelligence and the closed-loop value of this intelligence. For small and medium businesses, the cloud may also make powerful digital manufacturing tools available to manufacturers who would otherwise be unable to purchase or support on-premises versions. With rapid advancement of cloud-related technologies, such as the 5G communication standard and integrated industrial security, edge devices connected to cloud will increase the adoption of the cloud for manufacturing purposes where real-time speed, safety and availability become more crucial.
Machine Learning in Manufacturing
Machine learning, a branch of AI, uses algorithms and statistical models to get computers to perform a task effectively without being programmed explicitly. In other words, it enables the computer system to learn from multiple data points and to figure out the next step is by itself. Machine learning enables predictive and prescriptive insights for the entire manufacturing lifecycle.
If I want to operate a machine shop unmanned overnight (as in the lights out factory concept mentioned earlier) and the system finds out through closed-loop manufacturing that one of the machines that is next in line is blocked, what can I do? Should we stop production until a human team can come in to do an analysis of why the power failed and then restart production? No, this is, of course, not ideal. In the future, we should be using machine learning algorithms to figure out the skills needed for the next step and find another machine that can do the work. We should automatically allocate the part to this machine and use machine learning to change the programming so that part can be produced on this machine.
Do we have this technology today? No, at least not with complex processes, but this is the vision. It’s coming. It’s going to happen because machine learning is becoming more and more powerful. We have more opportunities to collect big amounts of data. The whole game is how much data you collect, how you analyze the data, and apply it to your processes.
We are optimistic about the future and the role that digitalization, through the digital twin’s concept, and emerging technologies will play to bring these ideas to life.
VR – Virtual Reality for Manufacturing
At first, we looked at VR as a kind of computer game, but recently, maybe thanks to the Covid 19 pandemic, we found VR to be quite effective. Two weeks ago, we participated in a real VR collaboration session done by one of our leading German customers. They had eight teams from eight plants – seating with VR Goggles working for 2-3 h sessions, discussing issues related to a launch of a new product which is planned to be launched in parallel at all these plants across the globe. The reaction of the teams was very positive, they all said that with VR sessions they could avoid the need to travel yet still accomplish their mission on time and with min risk.
Keep an eye on this blog as we are planning future posts delving deeper into these and other manufacturing operations management technologies.