Driving Transparency – How Quality Management Systems Prevent Catastrophe
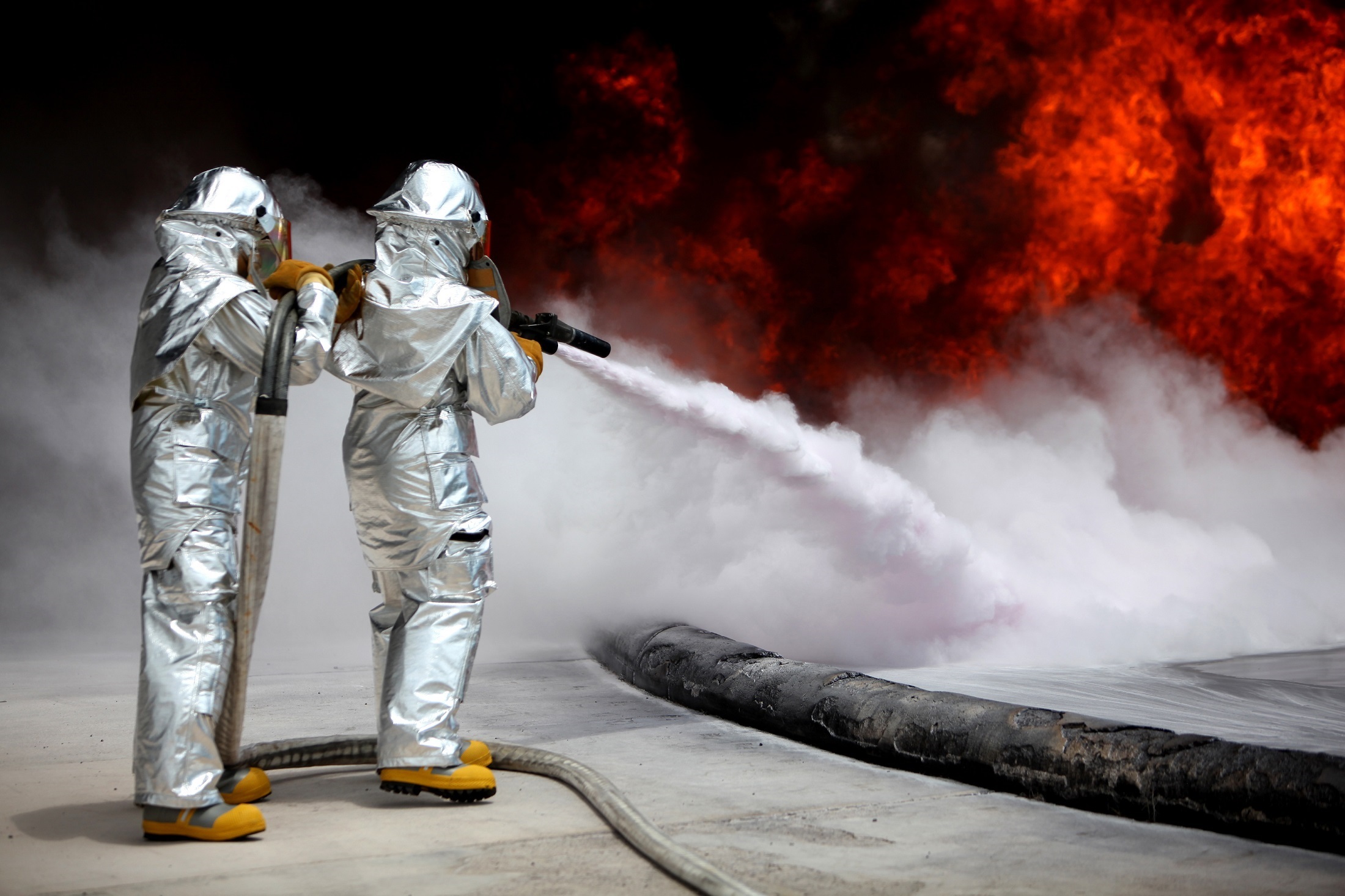
We have all heard about public disasters around potential systematic disregard for quality problems in companies – from the automotive industry (think emissions tests, brake failures) to the oil & gas manufacturing industry (think major spill disasters). The impact can be staggering. Let’s look at some of the repercussions:
- The CEO resigns.
- There is an exodus of key talent and management.
- There is a precipitous drop in the stock as the market reacts.
- Millions to Billions are required to address regulatory fines, class action judgments from impacted stakeholders, not to mention fixing the quality problem itself.
It takes years for these companies to recover. In each case, accountability will be scrutinized. What about the companies in which the CEO previously claimed he or she had a hands-on style of management, that they insisted on transparency? They are left in a very difficult position. If the CEO was, in fact, hands on and indeed insisted on transparency, how could this type of public disaster have happened without him being aware of at least the potential for a problem? If he were totally unaware, then there was a total failure in the management reporting chain and the culture of corporate integrity. This puts the CEO in a lose-lose position.
The need for transparency is an imperative for a healthy and effective corporate culture. One of the most effective tools a company has to assure transparency is the presence of a well-conceived and effectively implemented Quality Management System.
If we distill the prime elements of an effective Quality Management System to its most basic terms it comes down to:
- Communication: Assuring that all involved know what they are supposed to do and their impact both upstream and downstream on the process, their colleagues and the business. The QMS tools for this would typically be Document Control and Training and Competency, supported by a robust Management Review process.
- Education: Taking care to assure that knowledge sharing is encouraged, cross functional and always coupled with conveying the responsibility for one’s actions and behavior on coworkers, the product, the end-user and the world in which the business operates. This would also include training and competency along with team approaches to developing bench marking and best practice. In many organizations, this is built around “Lessons Learned” exercises.
- Correction: This is one of the most critical elements. Once that communication and education has taken place, tools for assessment, correction and change are imperative. By its very nature this includes providing members of the organization the means to report and escalate concerns about anything that comes to their attention. It is then incumbent on all levels of Management to take appropriate action on further escalating information up the chain of command. This would involve interactions between Corrective and Preventive Actionprograms, strong internal assessment programs and an equally important emphasis on “Voice of the Customer” programs for dealing with complaints and issues.
Coordinated and conscious efforts to defeat and circumvent regulations, compliance, and policy are virtually impossible when transparency is systematically enforced. Today’s technology assures the effective enforcement of the safety nets that have been so well conceived to prevent these types of public disasters. While those protections have typically been created for the safety of the consumer, the companies and shareholders should insist that they be transparently implemented and enforced. It simply makes good business sense.