Controlling the 5Ms in Pursuit of Product Quality | Part 1 – Material
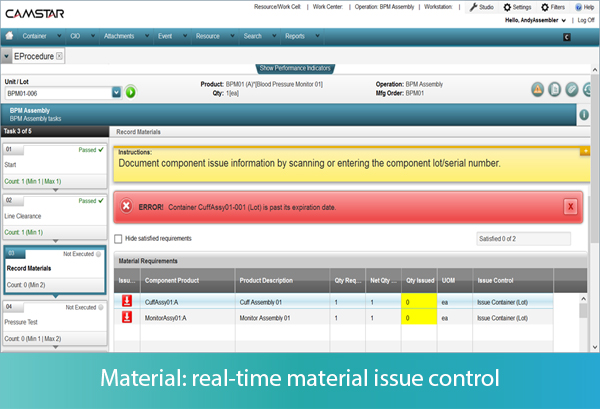
The more things change, the more they stay the same – translating a French proverb, “plus ça change, plus c’est la même chose.” Wiktionary interprets this, “Turbulent changes do not affect reality on a deeper level other than to cement the status quo.” With turbulent times for medical device manufacturers, it couldn’t be more true. Overcoming the challenges simply takes us back to basics – pursue product quality.
Pressure has never been greater for medical device manufacturers. The introduction of new products, accelerated clearance processes, and the ability to efficiently run new manufacturing activities in multiple plants globally are pushing a new era of agility. The globalization of companies and the need to support customization to satisfy consumer demand adds complexity. Regulatory bodies are imposing new compliance concerns, and the threat of recalls is daunting.
Yet many Medical Device manufacturers are still operating with paper-based and open-loop systems, using sheer human determination to control quality. Let’s do a reality check. If we get back to basics, we know that product quality is rooted in the control of the “Five Ms” – material, man, machine, measure, and method. Still the same. We simply have a better way of getting control over the 5Ms today than we had in the past – namely using a Manufacturing Execution System (MES).
This 5-part blog series takes a deep dive into how today’s manufacturer can control the Five Ms automatically, using an MES to take advantage of digitalization to automate control. Part 1 of this series looks at the control of Material.
When we think about control of material, the first thing that comes to mind is that we want to use only the materials intended for the product, and we want those materials to be in the proper condition. Good materials make good products.
The MES contains the bill of materials (BOM) list that defines what materials should be used for every step of the manufacturing operation. The MES automatically checks whether material lots are valid, and signals to the operator when non-compliant materials are introduced. The MES records in the electronic Device History Record (eDHR) what materials were used, creating full electronic traceability for each product. It is “self-auditing,” meaning that it automatically enforces correct materials while creating the appropriate quality records.
Let’s look at a few examples. First, the MES system presents to the operator the instructions for component issue applicable to the assembly operation, creating traceability of serial or lot numbers of a component to the finished good. The operator may use a bar code scanner to enter into the MES the serial or lot number of the material about to be used. The system will determine whether that serial or lot number is valid for the BOM. If the material entered is not identified on the BOM, including alternate or substitute items, the system will signal to the operator that there is an error, and prevent further operation until the error is corrected. If the material is part of the BOM, the system will additionally validate whether the material is expired, and again prevent its use in the operation.
Beyond the control of correct and valid materials, the system also supports lean manufacturing practices through enforcement of FIFO and LIFO usage, as well as control of other nonconforming materials and quantities, and unique business rules of the particular manufacturer.
An MES system today is a must have for manufacturers to ensure control of the materials they use in their products. Overcoming today’s turbulent Medical Device market means back to basics, with a little help from an MES.
In the next blog, we will talk about the control of second M – Man.
Comments
Leave a Reply
You must be logged in to post a comment.
Hi,
can we generate serial number in simatic it uadm. if yes please provide some example considering automobile industry .