BLOG: Perspectives from Realize Live 2020: Opcenter Portfolio Update
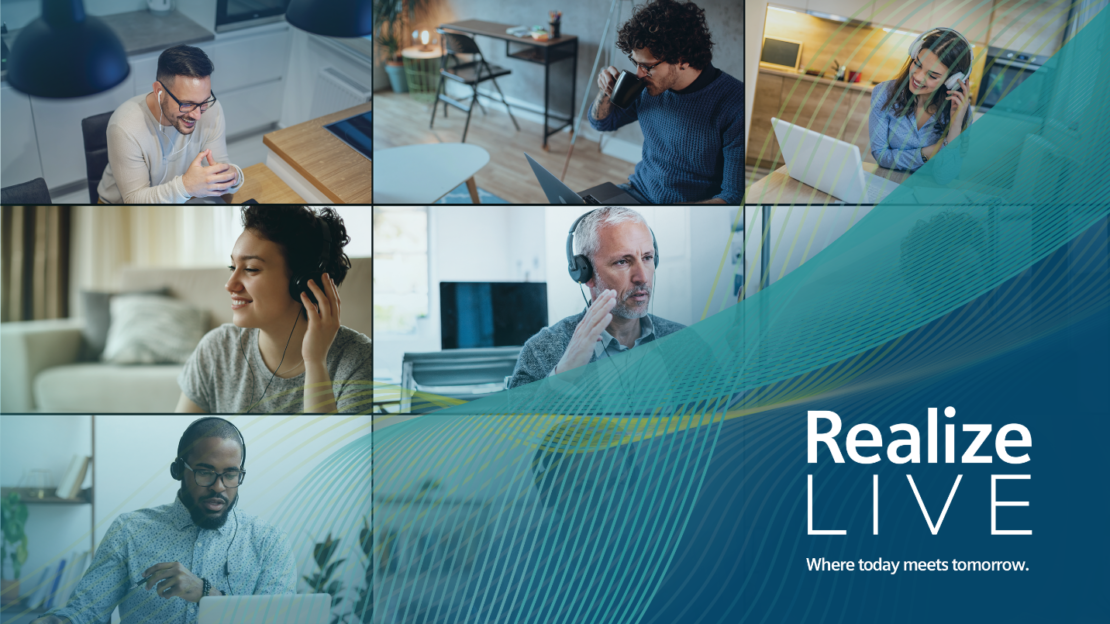
In June, thousands of people from around the globe joined our first virtual edition of Realize LIVE and inspired our community with stories of how we can succeed during challenging times when we come together around topics that we are all passionate about.
While we encourage you to continue the discussions in the Siemens community, we also want to highlight the next editions that will take place: Russia (15 September), Europe (3-4 November), and China (11-12 November) (https://events.sw.siemens.com/realizelive/)
During Realize Live 2020, we provided an extensive update on our latest and greatest innovations in the Opcenter portfolio. Below is a recap of the information provided during a Q&A session with Rene Wolf, Senior Vice President of Siemens Digital Industries Software, and Tobias Lange, Vice President R&D MOM at Siemens.
The Digital Transformation Roadmap for Manufacturing
As you chart your digital transformation roadmap, the first thing to do is conduct a thorough analysis of your business processes to discover where the biggest opportunities for improvement are – where the business is experiencing the most pain. Have a discussion with operators on the shop floor who typically have a good understanding of where workarounds have been applied and where workflows are not as smooth as they should be. You will likely find a plethora of spreadsheets floating around on the shop floor, combined with manual lists on pieces of paper. This is still the reality of things, even in some highly automated factories.
If you start with good visibility and transparency on your shop floor, you can create a dashboard solution with clear KPI management and actionable operational intelligence. This is a good first step that allows you to gain quick results at a relatively low cost. From there, you can chart your roadmap based on the most important process opportunities you have identified, and where your KPIs need the most improvement. You can work on the automation of certain processes, whether that’s headed towards supply chain integration or overall traceability. If you have complex processes, you can monitor WIP closely to improve overall quality management. By changing the process, you can eliminate the human error side of the equation and drive process enforcement. This progress typically yields better process and quality, which leads to better control over the output of your factory.
When we look at prioritizing MES, MOM, and IoT solutions, it is important to understand the use cases associated with each. Opcenter has a different set of use cases than Mindsphere, an IOT-type platform with associated apps. If you want to control your processes and implement process conformance on the shop floor – simple workflows, electronic work instructions, quality measurements and enablement, or advanced planning and scheduling – you would look to Opcenter. Orchestration and optimization of those processes is core to the Opcenter portfolio, and not something you would solve with an IOT platform.
Opcenter (MOM functionality) typically sits on top of all the other shop floor systems, gathering data provided by the SCADA, an automation system, or sensors. That information is fed into a data repository which could be on premise or, in the case of Mindsphere, in a data lake. The Mindsphere apps then use advanced data analytics or dashboards across multiple plants. It is a collaborative model between Opcenter and Mindsphere, rather than an either/or question. If it comes to simple dashboarding, there are solutions available in both portfolios, and it becomes a question of whether you are a single/local production facility – in which case you might find that an on-premise solution is a better fit – or if you’re looking for cross comparison and KPIs across your whole enterprise, with future predictive and prescriptive insights – then, an IOT solution like Mindsphere is a good choice. In general, shop-floor operational workflow, compliance, and quality management is all done within Opcenter.
The Opcenter Innovation Roadmap
We built the Opcenter portfolio out of our own R&D efforts and various Siemens acquisitions over the last two decades. We have a variety of excellent solutions that were and still are well-known brands. In some cases, prior to becoming members of the Siemens family, companies such as Camstar, one of our flagship MES solutions predominately for the semiconductor and medical device industries, dominated their space. What we are focused on now is combining the best of these many worlds, with the various solutions and their unique strengths to fit target industries, actually sharing code and common components in order to achieve a common user interface. Our customers will have one way of storing data in a database, with one login mechanism. Across the portfolio, we have harmonized the user experience. This is what drives our innovation streams, whether our customers are heading towards cloud or integrated processes on the shop floor – our goal is to develop and provide a highly interoperable set of solutions with a common user experience.
For complex manufacturing segments, we are bringing production execution (MES) and quality management (QMS) processes together to enable you to approach your quality and your execution in a holistic way, rather than doing them in separate systems. Our goal is to take quality planning and continuous improvements processes and integrate them with the product lifecycle and quality execution processes. Quality management will be a seamless flow into your execution system, becoming part of the build process. We have several steps and iterations to get there, and our roadmap includes releases in the upcoming months.
When we look at closed-loop manufacturing, Teamcenter is the approach to integrate your quality processes. To integrate your quality execution with your manufacturing execution systems, the answer becomes Opcenter. For the golden triangle between PLM, ERP, and MOM, Active Integration, an already proven integration backbone of Teamcenter to SAP, is currently the central component.
As we look at our cloud strategy for Opcenter, we are looking at the holistic picture. We have a great existing portfolio with rich functionality that we are evolving over time into a more modular architecture. Individual modules will be deployable across on-premises, edge, and/or cloud, and working together in a seamless fashion across those deployments and with other systems, including the shop floor.
We have a three-step strategy for cloud:
1) certify and offer deployments in the cloud of our existing portfolio, including as a Siemens-managed service
2) offer standalone cloud-based solutions (e.g. for Opcenter Intelligence)
3) offer the holistic architecture mentioned above as an evolution of our existing portfolio
We are actively working on all three streams and have launched various solutions. We will have additional products and services available in cloud deployments, while continuing to support and enhance the existing portfolio. We are excited about future announcements in this space.
With Mendix, Rapid Application Development platform of Siemens software portfolio, Opcenter can be used for purpose-built apps per customer business process needs. From an architecture perspective, Mendix works best with modern architecture(s) using restful APIs and legacy data format. With Opcenter, there are some early stage solutions using Mendix for some of our customers, and there is a certain implementation required to completely see the APIs in the data. For example, building an offline application for offline execution in certain environments.
Today’s imperatives
Today’s environment amid COVID-19 has presented new challenges. There were and continue to be many lessons learned, and different industries have been hit in different ways. For instance, in the pharmaceutical industry the current challenge is first and foremost research, but also mass production of things like hand sanitizer. Products like toilet paper became scarce when the lockdowns first occurred, and the supply was unable to keep up with demand. The paper industry focused on ramping up production to meet demand.
On the flip side, the automotive industry came to a screeching halt as the demand for cars has been basically zero, forcing a complete shutdown of that industry. The demand impact has been vastly different between the industries. If a manufacturer has complete digital control over their processes, they then know exactly where the bottlenecks are and exactly how to ramp up and more efficiently drive production when the need arises.
Fortunately, we don’t have these types of global crises often, but it is clear that when there is something dramatic going on, the more agile a company is, the more digitized they are. This is one of the lessons learned. Obviously, there is a supply chain element. With China being the first to be hit by the COVID-19 virus and hence shutting down, it became quite obvious how much of the global supply chain is really reliant on the output of China as a single source. That made life miserable for many people because alternative sourcing has been neglected. So, another lesson learned is that a company needs alternative sources, and from a geographical perspective that might not be totally driven by price.
In the end, digitalization makes a company stronger, giving them the ability to handle these crisis situations more effectively and quickly when they arise.
With Opcenter Portfolio products (as part of Xcelerator), Siemens is not only supporting our customers for today but also bringing tools and technologies to empower manufacturers for tomorrow.