Will Machinists Capitalize on the PMI Opportunity?
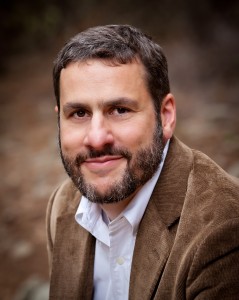
This blog post has been licensed for hosting by Siemens PLM. The concepts, ideas and positions of this post have been developed independently by Industry Analyst Chad Jackson of Lifecycle Insights. © LC Insights LLC
A couple weeks ago, I attended the Congress on the Future of Engineering Software (COFES) that is held out in Phoenix AZ about this time every year. It brings together industry analysts, users of engineering software as well as software providers for in-depth discussions on where the industry is going.
While there, I led a discussion session on the consolidation that’s been happening in the CAM industry. If you don’t know, this highly fragmented space has seen a number of mergers and acquisitions in the last few years. We got together to talk about the resulting implications.
The most interesting aspect of this discussion, however, wasn’t about the business end of CAM. It was how the participants stereotyped machinists as highly resistant to change. We all get set in our ways. But I started to wonder to myself, if there are technology advancements, will machinists take advantage of it?
The Trend of Increasing PMI
Am I talking about some far off technological leap for machinists? Actually, no. There’s a movement occurring right now that promises some value for machinists. In the 3D Collaboration and Interoperability study I am conducting right now, 40.2% of respondents are creating 3D models with Product and Manufacturing Information (PMI). What is PMI? Here’s the wikipedia definition.
Product and manufacturing information, also abbreviated PMI, conveys non-geometric attributes in 3D computer-aided design (CAD) and Collaborative Product Development systems necessary for manufacturing product components or subsystems. PMI may include geometric dimensions and tolerances, 3D annotation (text) and dimensions, surface finish, and material specifications. CAD application literature may also refer to PMI synonymously with Geometric Dimensions and Tolerances (GD&T) or Functional Tolerancing and Annotation (FT&A).
So basically, this looks, acts and feels like a drawingless movement. However, this same study shows that 38.7% of those creating 3D models with PMI are also still using drawings to create NC toolpaths. Believe me, drawings aren’t going to disappear.
The Value of PMI for Machinists
So why exactly is this a big deal? Well, essentially, it’s about automation.
When 3D modeling hit the industry, machinists were suddenly able to generate NC toolpath coordinate moves from design geometry. That automated part of the task, however. The machinist still had to use their experience and knowledge to select the tool, the feeds and speeds that were most appropriate based on the other characteristics of the design like materials used, surface finish required and tolerance needed.
Now that non-geometric information is being embedded within the 3D model, there is a new opportunity. That information can be extracted to additionally determine tools, feeds and speeds in an automated fashion. So now, machinists no longer need to laboriously tweak every single detail of the NC toolpath. Instead, they can verify that the toolpath does its intended job and validate there are no clashes.
For the machinist, this removes a lot of mundane detail work. For the organization, if the generation of toolpaths has been a bottleneck, machines can attain a higher utilization rate. So there is value on both sides of the fence.
Cultural Change is Never Easy
Is PMI new? Well, actually, this concept has been in existence for quite some time. And to be frank, few organizations adopted it over the past years. The difference this time, however, is that many defense contracts are now requiring the delivering of PMI as part of the 3D model. In fact, in the 3D Collaboration and Interoperability, 76.2% of those creating 3D models with PMI are contractually required to do so. Nothing like a customer requirement to get things started, right?
Now, nowhere in these contracts does it state that defense suppliers must machine using 3D models with PMI. It’s simply an opportunity. One that promises great value.
Summary and Conclusion
Let’s recap.
- Fully 40.2% of the respondents to the 3D Collaboration and Interoperability study are embedding Product and Manufacturing Information (PMI) into 3D models.
- PMI contains non-geometric information such as GD&T, surface finishes, material specifications and more.
- PMI can be used to automate the selection of tools and definition of feeds and speeds of NC toolpaths.
- This represents an opportunity for machinists to automate their daily tasks and increase machine utilization.
Now, getting back to my original question, are machinists ready to take advantage of this opportunity?
Take care. Talk soon. Thanks for reading.
About the Author
Chad Jackson is the President and Principal Analyst of Lifecycle Insights, a research and advisory firm that assesses the business impact of software applications and systems on engineering organizations. Chad has more than 15 years of experience with CAD, CAE, PDM, PLM and related technologies as part of the analyst community and software industry. Due to his industry knowledge and thought leadership, Chad is a sought-after expert, author and speaker that has advised, published and presented dozens of times domestically and internationally. |