What’s new in NX 12 for manufacturing
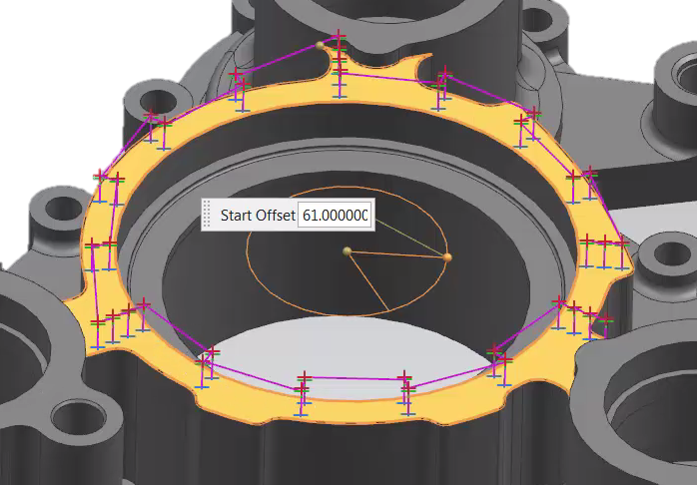
Transform your part manufacturing using a digital machine shop
NX CAM
New advanced capabilities in NX CAM 12 for mold and die machining, production machining and complex parts machining provide powerful advantages to part manufacturers.
Mold and die machining
Adaptive milling is a new high-speed cutting strategy that can reduce machining cycle time by up to 60 percent. This intelligent roughing method enables deep cuts and constant tool load that increases material removal rate, while extending tool life. Although ideal for cutting hard materials such as steels used for tooling, Adaptive Milling can be used for high-speed machining a of range of materials, including production machining of aluminum parts.
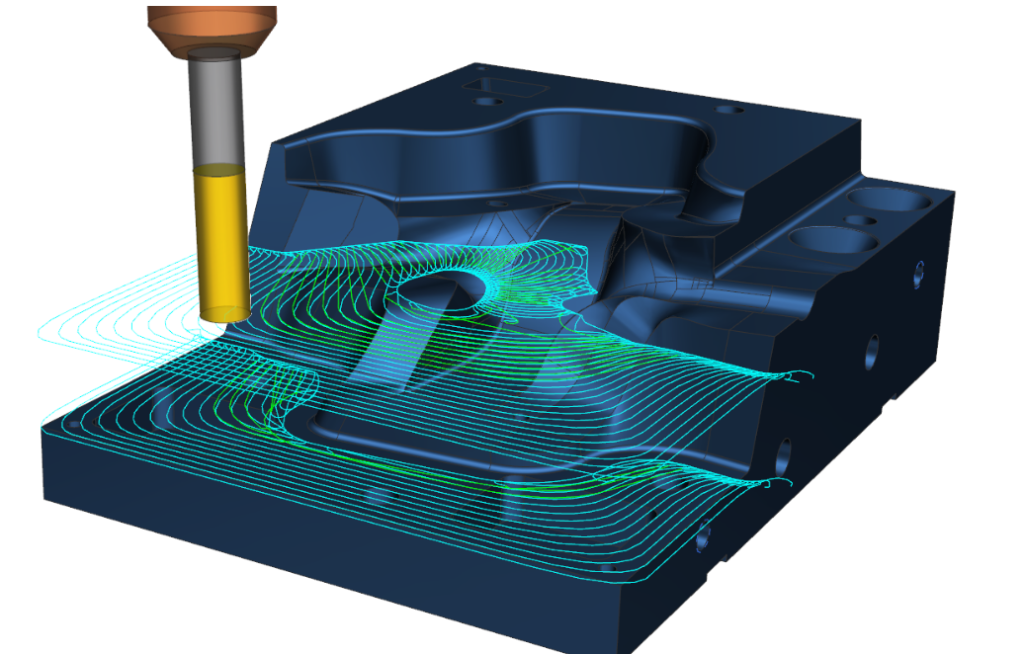
Machine 60 percent faster with Adaptive Milling, a new high-speed roughing method in NX CAM 12This innovative cutting strategy maintains consistent chip thickness by dynamically adjusting the machining parameters, including step over and feed rate. By maintaining consistent chip thickness during the entire cutting operation, the cutting forces can be significantly reduced which enables high speeds and feeds using the entire flute length. This gives you an advantage over conventional milling where you can use only a small portion of the flute length for cutting. With Adaptive Milling, you can use high machining speeds, while reducing the productions costs by extending the cutting tool life.
Enhanced finishing strategies in NX CAM 12 can further improve the quality of a machined surface. The consistent stepover can now be achieved across the entire machined area, regardless of the slope. Also, the intelligent finishing toolpaths can recognize small cavity features in machined surfaces and machine over them, which improves cutting conditions and minimizes part preparation operations.
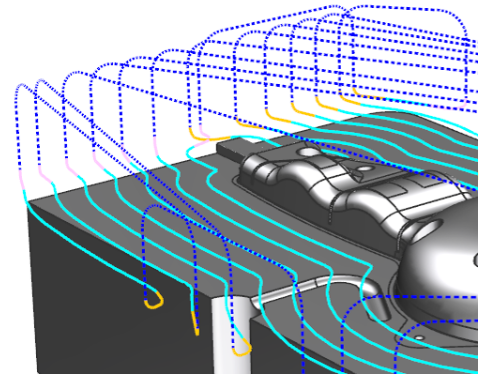
NX CAM software has advanced capabilities to create toolpaths with smooth cutting moves. NX 12 gives you even more control to apply smooth engage, retract and transfer moves. The resulting optimized toolpaths without sharp corners eliminate sudden stops and changes of direction during the machining process. These optimized toolpaths can significantly minimize the wear of machine tools, which increases equipment uptime and reduces production costs.
Production machining
New in NX 12 is NX Machining Line Planner software for high-volume production of complicated parts with many features. NX Machining Line Planner combined with integrated NX CAM software enables distribution, balancing, programming and simulation of operations over multiple setups and machines. This integrated solution allows bi-directional change management between programming and line planning. By using a digital twin of complete machining lines to optimize the process, automotive and machinery manufacturers can reduce planning time and increase throughput.
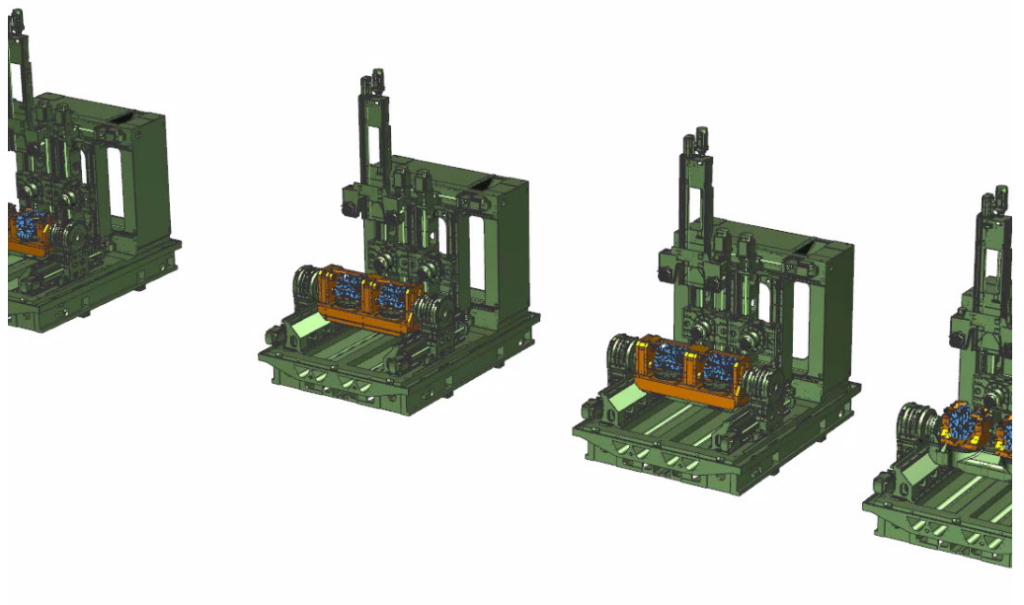
Plan and optimize high-volume flexible machining lines using NX Machining Line Planner. Program detailed NC operations using integrated NX CAM.
For programming of multi-function machines, keeping track of the in-process state of the workpiece is a critical capability. The seamless transfer of the in-process workpiece (IPW) between milling, drilling and turning operations enables accurate visualization of the complete machining process. The enhanced IPW capabilities also let you identify possible collisions between the in-process workpiece and tool holders. With these new capabilities, you can quickly create optimized and safe toolpaths to take a full advantage of the latest mill-turn machines.
Complex parts machining
Five-axis machining in NX enables you to produce precision complex parts with fewer operations and setups – reducing cost and delivery times. NX CAM 12 introduces new advanced capabilities that streamline the NC programming while creating efficient multi-axis toolpaths.
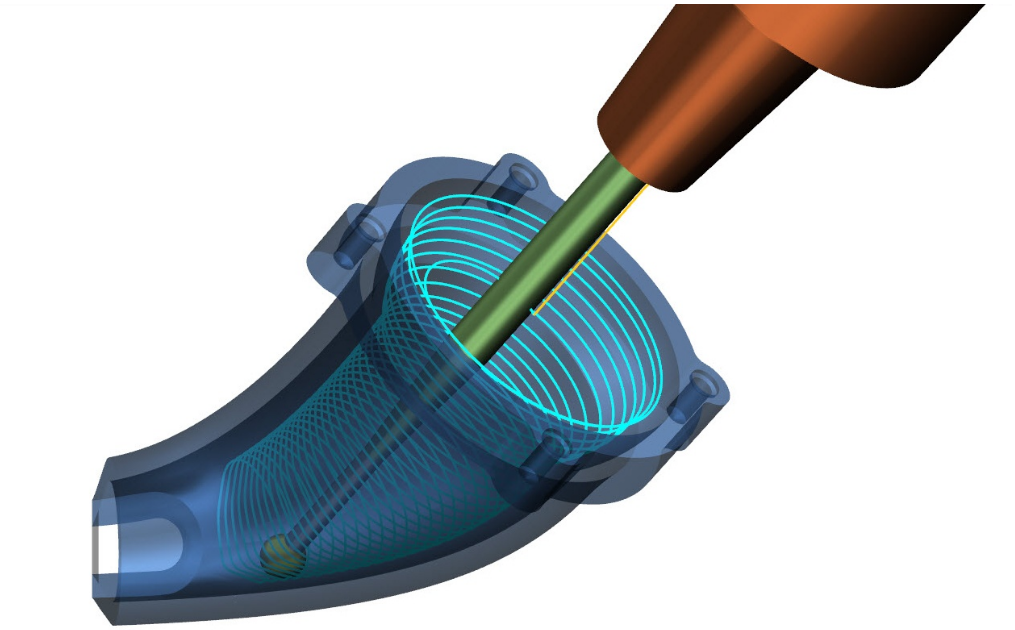
Easily create error-free 5-axis roughing and finishing operations with Tube Milling in NX CAM 12.
The new Tube Milling 5-axis capabilities drastically simplify programming of hollow and narrow features, including ports of engine blocks. Programming these features using conventional methods can be very time consuming and prone to errors that result in machine downtime on the shop floor. Tube Milling streamlines the NC programming process and allows you to eliminate preparation and minimize input of parameters, which enables you to easily create consistent and error-free toolpaths. These efficient roughing and finishing operations ensure high-speed and error-free 5-axis milling that shorten machining time, and improve machined surface quality.
Robotics for part manufacturing
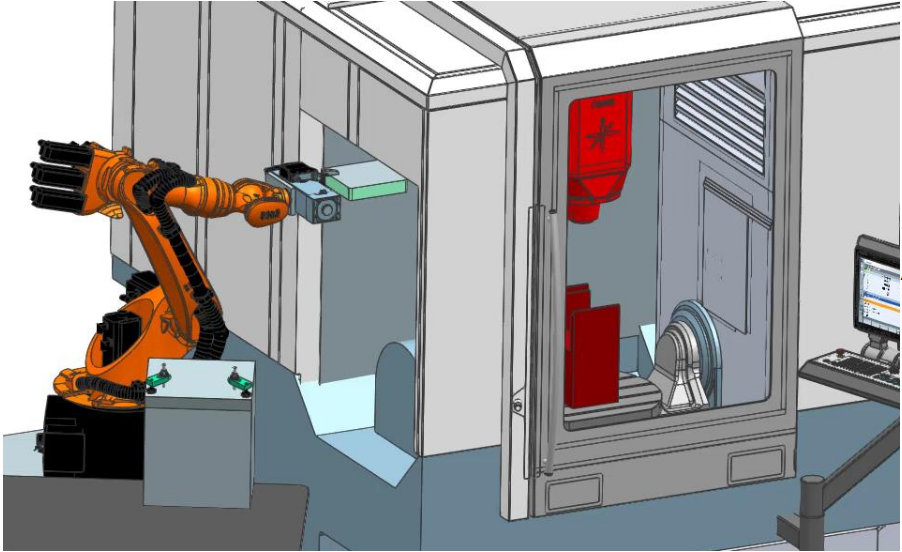
In the previous release of NX, new robotic machining capabilities were introduced. Using NX CAM robotics machining you can program robots to perform precise machining-type tasks including trimming, de-burring, grinding, and polishing.
The robotic machining in NX CAM 12 was significantly enhanced by a virtual teach mode technology. This allows the user to easily program a robot to do pick-and-place operations, including machine tending and tool loading.
By combining NX CAM software with the embedded Virtual NC Controller Kernel (VNCK) from Siemens’ Sinumerik 840D SL controller, you can achieve a new level of accuracy and completeness when using 3D simulations to validate the robot motions.
With the new robotics programming capabilities in NX CAM, you can program robots to perform CNC machining and pick-and-place operations using one system, enabling you to farther automate your part manufacturing process.
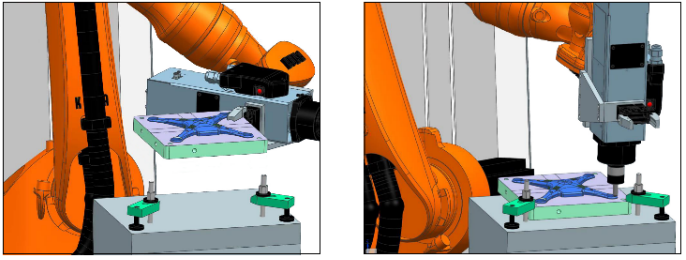
Tooling manufacturers can now automatically and accurately determine tooling production costs using the new integrated capabilities of Siemens PLM Software’s solutions. The digitalized process, from part design to tooling cost estimate, can replace the time-consuming manual job tasks. This gives tool manufacturers a unique advantage in this highly-competitive industry.
NX Feature2Cost can automatically identify features on molded or stamped parts using the robust feature recognition capability. It lets you easily recognize many part features, such as undercuts, ribs and bends. During the cost calculation process, the software gives you flexibility to make right decisions based on your experience.
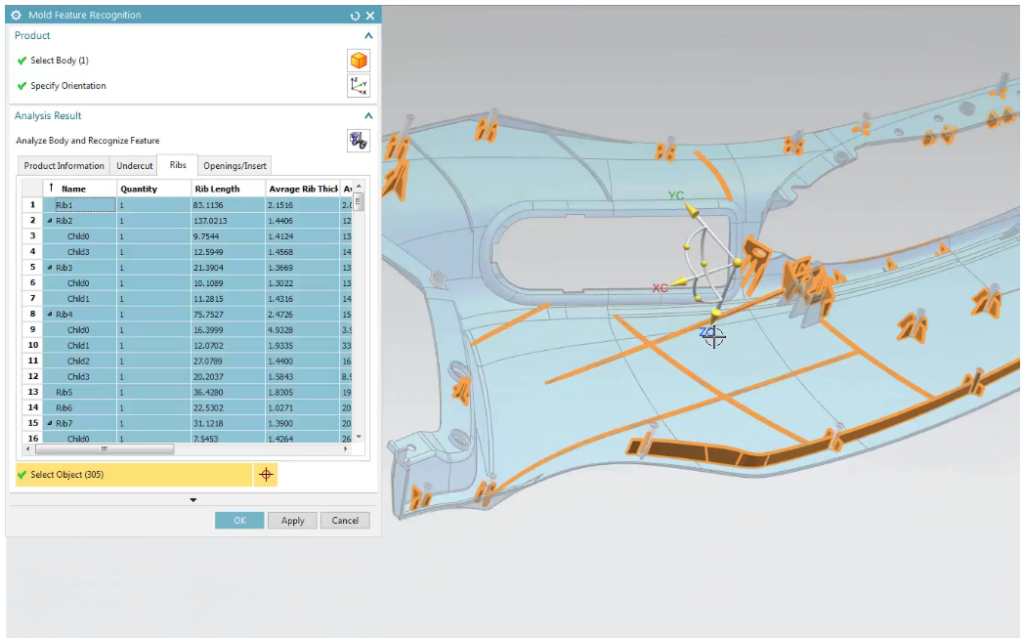
Automatically recognize features on molded and stamped parts, including undercuts, ribs and bends using NX Feature2Cost.
The complete set of recognized features along with their parameters is seamlessly transferred to Teamcenter Product Cost Management software. After providing additional information, such as the production site and machines, the system can precisely calculate the tooling cost. By being able to quickly provide accurate quotations, tooling manufacturers are positioned to win more orders and increase their profitability.
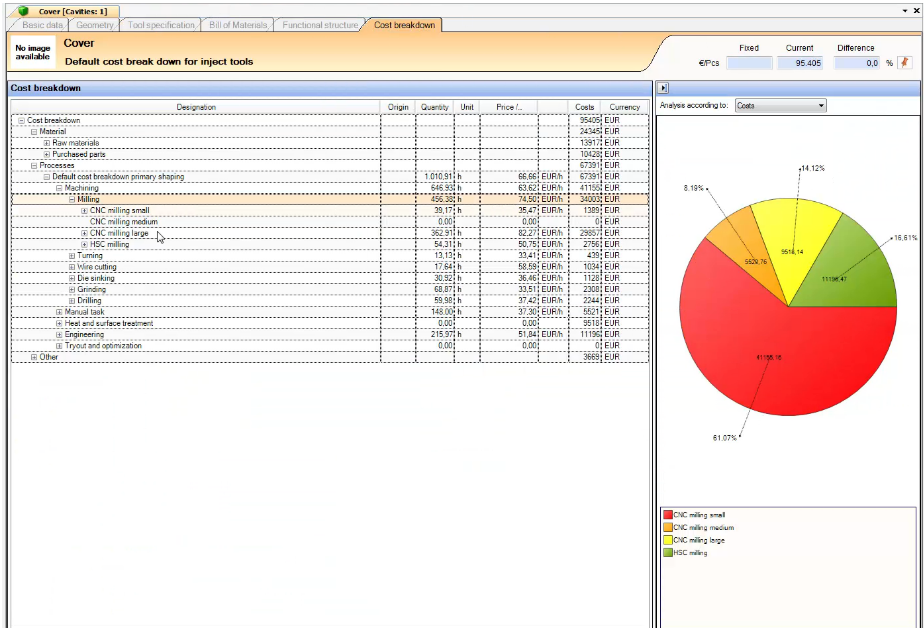
Accurately determine the tooling costs using the powerful Teamcenter Product Cost Management software.
NX Additive Manufacturing
Industrialize additive manufacturing with NX 12
Powder Bed Printing
Powder bed printers remain the most popular option for printing of metal parts and NX 12 now has a robust, integrated connection with these printers.
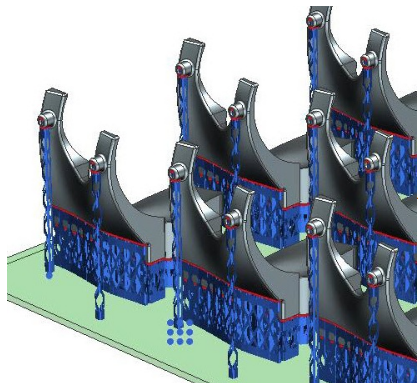
This new module, which is powered by Materialise, includes facilities for creation of support structures as well as for the setup of the build tray, positioning and patterning of parts in the build tray, and a build processor framework for connection to powder bed printers.
With NX 12 you can setup, connect, and print with powder bed printers all in a single system meaning you can now have a single, uninterrupted digital thread from design to print.
HP Multi Jet Fusion Printers
The landscape for printing plastic is evolving as new vendors are entering the industry. One exciting new addition to the hardware landscape for plastic printers is HP with their Multi Jet Fusion technology.
NX 12 has a new module, certified by HP and powered by Materialise, enabling customers to design, optimize, simulate, prepare print jobs, and inspect processes for HP Multi Jet Fusion 3D printers. NX users can load multiple models, auto nest the models in 3D, and submit the job to HP 3D printers in a single NX environment and with a minimum number of steps.
When HP’s new 3D printers are combined with the power of Siemens NX, printing of plastic parts is easier, faster, and more accurate than ever before.
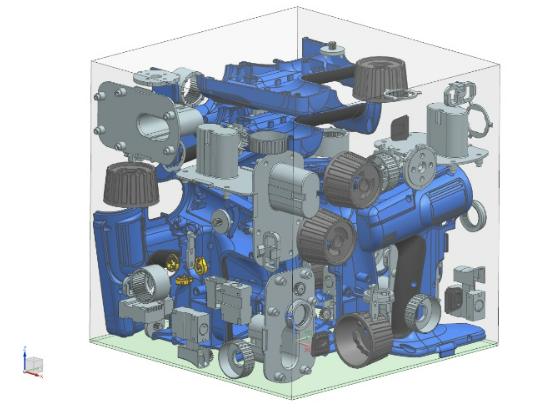
Design for Additive Manufacturing
Companies are looking to innovative solutions in the constant drive to reduce component weight and improve resource usage. Lattice structures are one way designers can meet these goals without compromising on strength and structural integrity. NX 12 delivers on these new approaches to design for additive manufacturing with the integrated ability to create lattice structures, powered by Materialise.
This new module allows users to create regular lattice structures as well as randomized structures within a volume. When combined with Convergent Modeling Technology™, which makes it possible to work directly with facet geometry, creating cutting-edge structures like these is easier than ever before. Furthermore, having these capabilities in a single system saves companies from the hidden data conversion costs normally required to work with such geometry.
With lattice structures and Convergent Modeling TechnologyTM in NX 12, companies can deliver lighter, stronger products to market in much less time, fulfilling the need for cutting-edge design of lightweight parts.
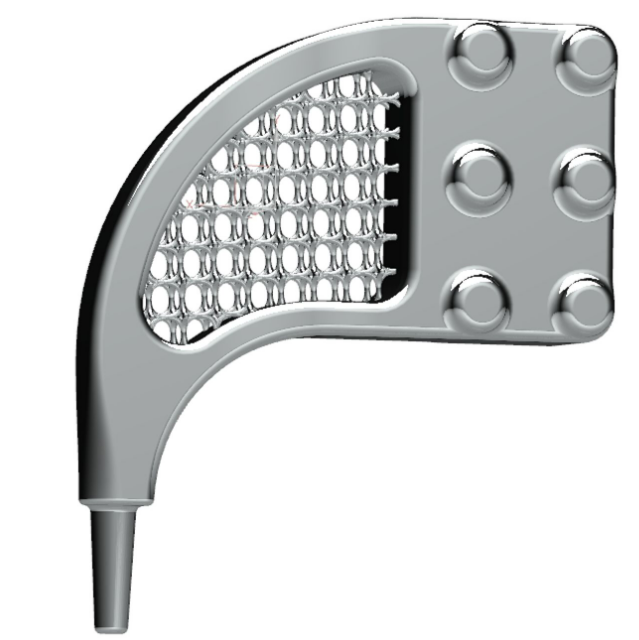
An example lattice structure created using the NX Lattice Structures Design module.
NX CMM Inspection Programming 12
NX CMM Inspection Programming enables programming of CMM machines, as well as visualization and analysis of measurement data into the NX graphical environment.
The new feature-specific inspection programming functions in NX 12 let you easily create point sets in circular patterns. New capabilities allow you to import inspection DMIS programs in NX to create inspection setups and generate touch trigger programs with minimum input. This enables Robcad CMM users’ easy transition to NX CMM. And, you can now use NX CMM Inspection Programming to analyze measurement data acquired by laser or white light scanner devices.
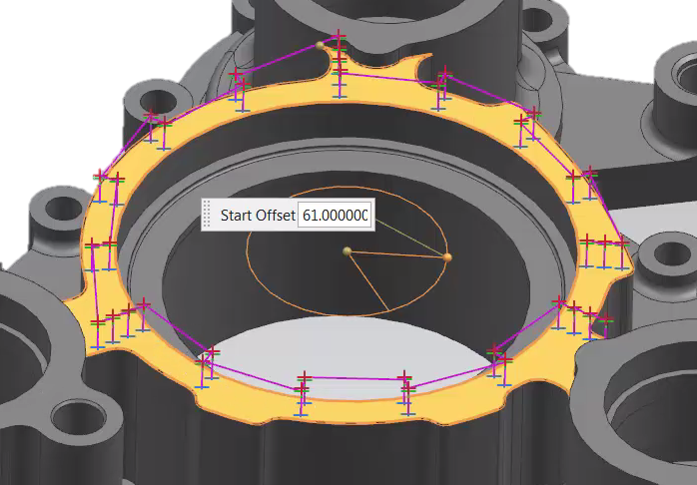
If you like receiving new product information through the blog, please give this article kudos (thumbs up)!
Additional Resources:
NX12 annoucement press release: Siemens’ latest version of NX expands toolset for digitalizing the machine shop
What’s new in NX 12 for your industry? This Tech Tip article is a summary of resources, organized by industry categories, describing NX CAM software updates available with NX 12.
Video: Next Generation Mold & Die Machining with NX CAM. Learn about the new mold & die capabilities in NX CAM 12.