Products
Precise, Digital and Flexible – Simulation-based force compensation helps robots perform accurate milling jobs
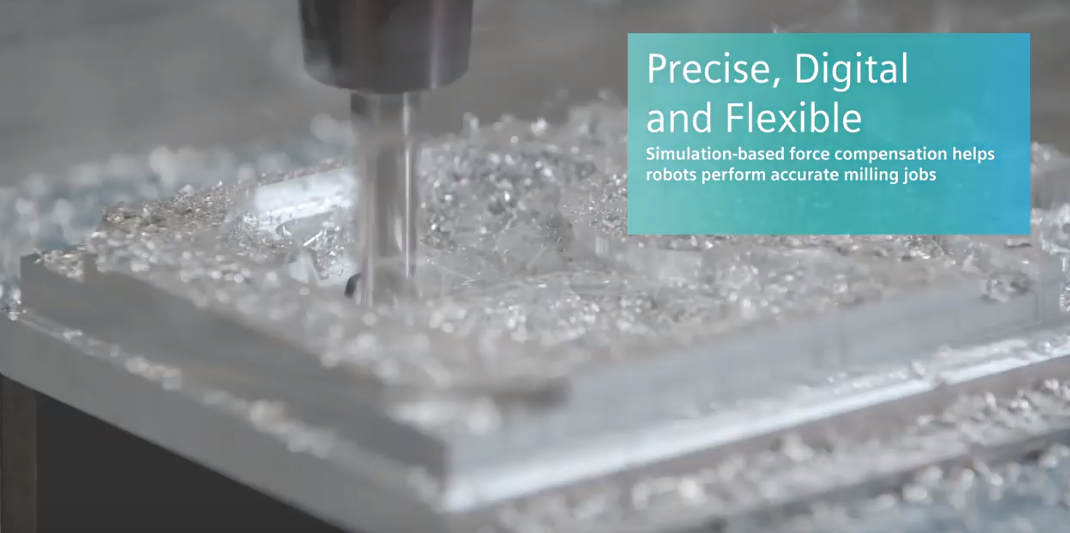
Robotic Machining has always been limited by the achievable accuracies. Simulation of the machining process and calculation of the corresponding forces (NX CAM) allows users to predict the deflection of the robot using its digital twin.
With this knowledge deflections can be compensated by the control (SINUMERIK Run MyRobot /Direct Control) achieving accuracies allowing the use of robots for industrial milling tasks. Simulation-based force compensation helps robots perform accurate milling jobs. https://new.siemens.com/global/en/com… https://new.siemens.com/global/en/pro…
Watch the video, “Precise, Digital and Flexible”
Comments
One thought about “Precise, Digital and Flexible – Simulation-based force compensation helps robots perform accurate milling jobs”
Leave a Reply
You must be logged in to post a comment.
Hi,
On the CAE side, we were involved in a European project called “Twin-Control”.
As said in the article below:
In the Twin-Control project, our focus is set on the dynamic modeling of the machine tool including its Computer Numeric Control (CNC), and its interaction with the machining process. To properly simulate modern high-speed machine tools, which show close interaction between the dynamic behavior of the mechanical structure, drives, and the CNC, it is crucial to build models that represent the flexibility of all components and their interactions.
Our Simcenter blog on the topic:
https://blogs.sw.siemens.com/simcenter/the-digitalization-of-industrial-machinery/
The link to the full article on the project’s website:
http://twincontrol.eu/2018/02/digitalization-for-industrial-machinery/
If there is any interest for this technology, don’t hesitate to contact me.