Machining Steep and Non-steep Geometry
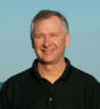
Several years ago, I hiked into the Grand Canyon. I spent a couple of months training my body for the trip. I loaded up my backpack with 45 lbs. (about 20 kg) of material, and hiked 3-5 miles every day. My plan was to hike in on the Bright Angel trail to the campground, spend the night, and hike out the next day. Despite my physical preparations, I was so exhausted when I arrived at the campground that I needed help just to get my tent setup. Why had my training failed? Looking back on it, I realized that my training had been on very flat ground, whereas the canyon hike was anything but flat.
Like my hiking experience, not all machined geometry is the same. Different strategies are required for different geometry. In the section view, you can see that some geometry is almost perpendicular to the tool axis, while part of the geometry is almost parallel to the tool axis. We call the almost-parallel geometry “steep”, and the nearly-perpendicular geometry “non-steep”.
To see why a one-size-fits-all approach does not work well, I will create tool paths on a very simple part that has both steep and non-steep geometry. First, take a look at our old pal Zig-zag. Zig-zag has at least two problems:
- Feedrate must be lowered as tool moves up/down steep geometry and sped up when machining non-steep, because the cutting tool is experiencing more material engagement while encountering steep geometry.
- The actual stepover from one pass to the next can vary widely as the tool marches up and down the steep geometry. If you examine the picture closely you can see that is the case when the cutter is proceeding up the side of the steep geometry (direction of pass not normal to steep).
OK, then, what about the offset pass methodology? It has the same problems as Zig-zag.
Other cutting strategies have been developed to help with this. This starburst pattern is called Radial Zig-zag. Because the stepovers get progressively farther apart, this pattern is usually limited to small areas.
Finally, here is a concentric arcs cut pattern.
Now that I have laid out the case for NOT using these cut patterns on mixed geometry, I will show a better way…in my next blog post.
Thanks for reading!
Jim has a Master’s degree in Business Administration from the University of Central Missouri. He has over 30 years of experience in the manufacturing industry, and over 25 years of experience in the CAD/CAM field. He serves as Field Support for Siemens PLM CAM products. Prior to his current role, he held stints as CNC Programmer, CAD/CAM Department Manager, CAD/CAM instructor, and Project Coordinator for Siemens PLM CAM software development. He also made the Kessel Run in slightly over 18 parsecs.