How NX CAM simulation capabilities validate machines and processes
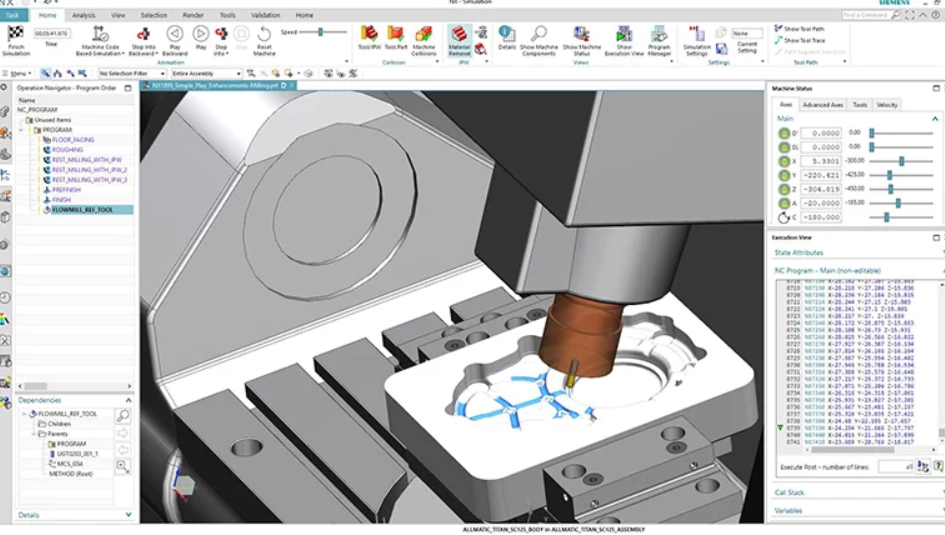
A recent article in SME.org, “Simulation Software for Error-free Metalcutting,” describes how the latest simulation packages offer CAD/CAM and NC-level code-checking to ensure fast, error-free machining processes to prevent costly programming mistakes.
Siemens’ Sashko Kurciski, Sr. Product Marketing Manager, NX for manufacturing solutions, offered insight about the need for accurate NC code simulation not only for toolpath validation, but also for machining process planning to avoid possible collisions and to optimize cutting time. Read what Sashko has to say in the following excerpts from the story.
Validating machines and processes
Modern machine tools can have complex kinematics, such as multiple channels with two or more multiple tools cutting the same part simultaneously, or multiple parts mounted at multiple spindles, noted Sashko Kurciski, senior product marketing manager, NX for manufacturing solutions, Siemens Digital Industries Software Inc., Plano, Texas. For example, five-axis machine tools typically have three linear and two rotary axes, which support unlimited tool positions and orientations within the workspace of the machine tool.
“For simultaneous five-axis motions, it is extremely important to understand how the actual controller executes the NC code, i.e., which kinematics solution is picked in order to avoid collisions or gouges,” Kurciski said. “These sophisticated machine tools only amplify the need for accurate NC code simulation not only for toolpath validation, but also for machining process planning to avoid possible collisions and to optimize cutting times. Using a highly-accurate simulation is critical to be able to stay competitive.” It requires using a comprehensive digital twin of the machine, controller, and the entire process, he added.
Manufacturers need the digital model of the machine model to be accurate, Kurciski added. “Possible issues might include incomplete definition of the kinematics of the machine tool and missing information about the controller and the underlying software. Typically, the in-CAM simulation is based on the internal representation of the toolpath, which is different from the G-code [NC program] that controls the machine,” he said.
To stay competitive, manufacturers need to deliver increasingly complex parts faster with better quality, while reducing production costs (due to shrinking profit margins), Kurciski said. This requires maximizing machine uptime, minimizing errors in production and shorter machining cycles. Digital validation of the machining process is the critical component in achieving these goals.
“Some form of machining simulation is available in many CAM systems. While in most cases the CAM systems can simulate the internal representation of the toolpath, this can differ from the G-code that runs the machine,” he said. “This causes a disconnect between the virtual and physical words of manufacturing that can result in costly errors on the shop floor.”
To address limitations of in-CAM simulation modules, Kurciski noted that some machine shops use third-party simulation software in addition to their CAM systems. “Introducing a stand-alone system in the process introduces more inefficiencies and possibilities to use incorrect data due to multiple data transfers between systems,” he said. “Additionally, this disjointed process relies on multiple systems and can make the process inflexible and slow.” He thinks it prevents manufacturers from quickly reacting to design or process changes that require automated toolpath recalculations and validation of the updated machining sequence.
Systems such as NX CAM include integrated G-code-based simulation, which enables programmers to ensure that the same NC program that runs the machine tool is used to simulate and verify in the same NC programming system, Kurciski said.
“You can achieve high-fidelity simulation only if the NC simulation module considers all the machine kinematics data and all the moves, which will finally be executed on the physical machine tool,” he said. “Without using G-code in simulation, you cannot accurately simulate the machining process. For example, using the actual G-code for simulation enables companies to get accurate machining time estimates, including cutting motions, position and transfer moves, and tool changes.”
NX offers one more level of simulation using Virtual NC Controller Kernel (VNCK) from Siemens’ Sinumerik controllers, Kurciski said, enabling a new level of accuracy when using 3D simulations to validate machining operations. “The integrated Virtual NC Controller Kernel solution is driven by an accurate and complete software model that is provided by the controller manufacturer and calibrated for your machine tool,” he said. “The resulting simulation responds exactly like a real machine with the same toolpath and setup. The integrated solution facilitates the closest possible digital representation of actual machine tool motion with highly accurate swept paths, speeds and accelerations, and tool changes. The solution’s software is calibrated for specific machine tools with the hundreds of unique performance parameters taken from the real machine and controller.”
Read the complete story in SME.org
Learn about the newest capabilities in NX for manufacturing.
Try NX CAM free for 30 days! Register now!
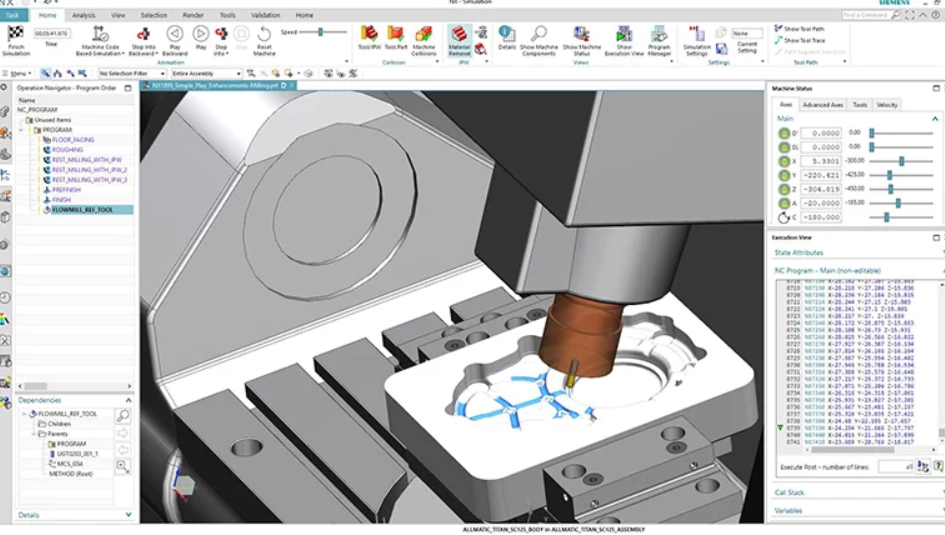