Getting Real: Shop Floor Connectivity
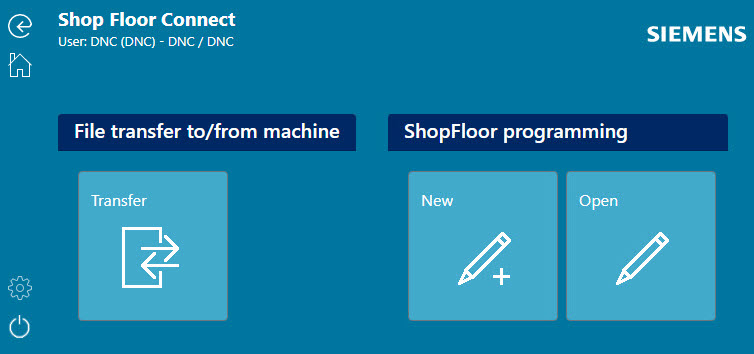
Welcome to the final post in our blog series on the Digital Machine Shop! My name is Corsin Buerer. I am the head of Production and Quality Software at Siemens Digital Industries Software, and I’ll be discussing shop floor connectivity, specifically how the work done in the previous stages of the quadcopter project made its way to the people and machines who turned the mold design into an actual mold.
Similar to the previous post on quality inspection, I’ll be discussing an area where traditionally paper documents, not digital data, have been the predominant form of communication. From drawings to tool lists to set-up sheets, the shop floor in many manufacturing companies is still a sea of paper.
We at Siemens believe that it’s past time for the shop floor to gain the benefits of going paperless. There is nothing preventing it at this point. NX software can create a comprehensive digital twin of your production processes, including digital versions of all shop documentation as well as the NC and inspection programs created at the end of the CNC and CMM programming processes. This all-digital approach can deliver significant benefits, such as improved part quality and shorter time to market.
In addition, we offer a specific solution for shop floor connectivity, called Teamcenter Shop Floor Connect, that facilitates transfer and access to the critical manufacturing data. Included in its functionality is the ability to send work instructions directly to machine tools, inspection equipment and presetters using a new technology for Direct Numerical Control (DNC). In this post, I’ll explain how we used Shop Floor Connect to extend the digital thread we have been following throughout this blog series all the way to the shop floor, and I’ll outline the advantages we gained as a result.
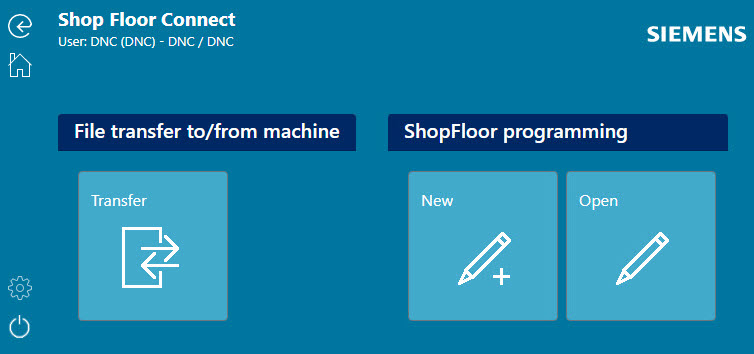
needed on the shop floor.
Only accurate, up-to-date information went to the shop
If you’ve followed this blog series from the beginning, you know that we’re now at the point where we’re ready to send manufacturing instructions for the quadcopter mold to the shop floor. Even though it is a moderately complex mold, the work package created by the manufacturing engineer contains a lot of information, everything from a comprehensive process plan to G-code for CNC machines.
If we had used the traditional approach, some of that information would have been conveyed by shop floor travelers – paper documents with bar codes that would have been manually transferred from station to station as the mold was built. There are obvious problems with static paper documents, such as ensuring that shop floor personnel have up-to-date revisions, missing and hard-to-locate documentation, and poor data security. For the NC programs, we probably would have used a thumb drive to upload it to the DNC, lacking revision control and data security. Also, over time a DNC can end up storing hundreds of NC programs and there’s always the risk that a machine operator can select the wrong one. Production errors like these are costly and can negatively impact your company’s productivity and competitiveness.
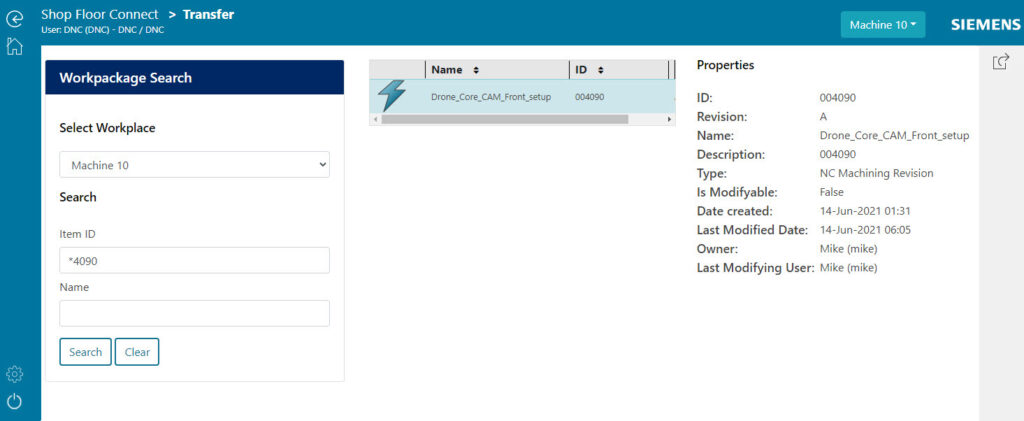
Fortunately, we didn’t face any of those issues. Shop Floor Connect, an app for Teamcenter, completely eliminated the need for paper documents at this stage of the quadcopter project. The team on the shop floor used tablet computers to access the data they needed. Regardless of the operator or the task, everyone accessed information from the same centralized Teamcenter database thanks to shop floor connectivity.
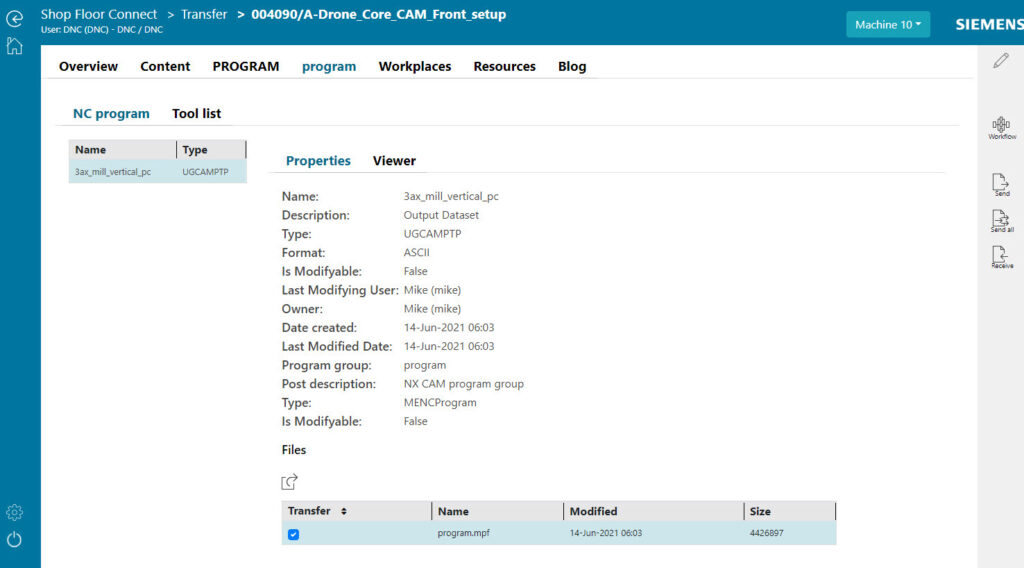
One of the advantages of this approach was that the shop floor staff lost no time trying to find what they needed. Whether it was a tool list or 3D geometry, work instructions or post processor output files – which previously would have been kept in different places – the information was all there in the Teamcenter database, accessible with one click.
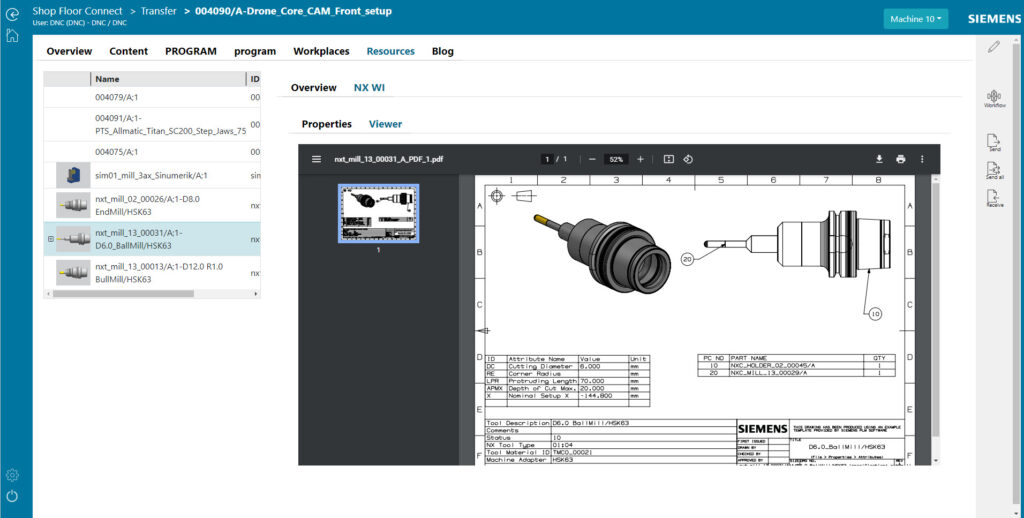
Another important advantage of this approach was that all the information was current and there were no duplications. The people on the shop floor had access to only one (approved) work package, eliminating any risk of working with outdated information. The displays in Shop Floor Connect are tailored to shop personnel – clear and easy to read – so there was no need to print anything. And since all of the data stayed in Teamcenter and no extra hard copy or digital versions were floating around, data security was good.
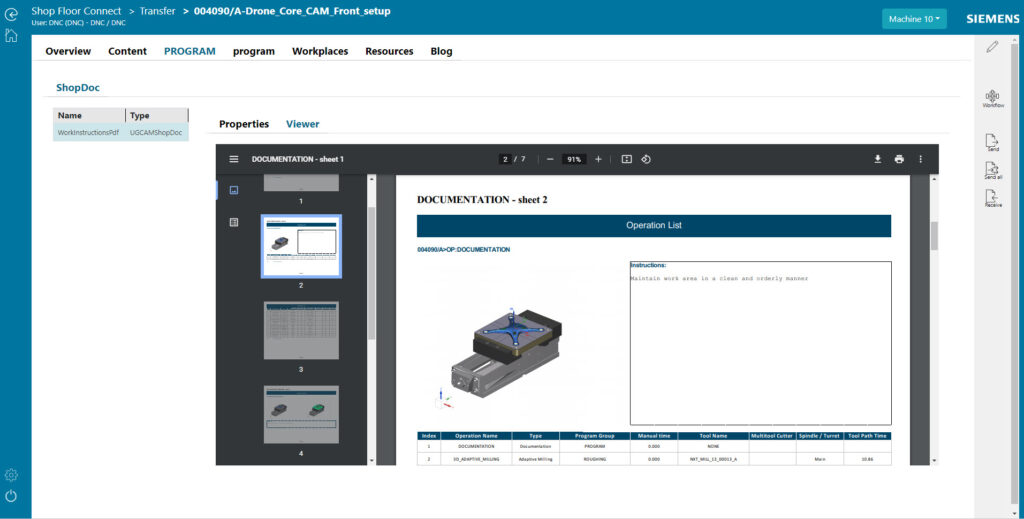
Direct machine connection for DNC
As explained in the CNC Programming of the Quadcopter’s Molds blog post, we needed only one CAM solution, NX CAM, to drive all of the machining process we needed for this project, including some ultra-efficient machining technologies such as Adaptive Milling. The NC programs the CAM experts created were transferred directly from the Teamcenter quadcopter database to the shop’s DNC computer but not stored there, eliminating problems caused in the past when hundreds of programs in the DNC made it hard to find the right one.
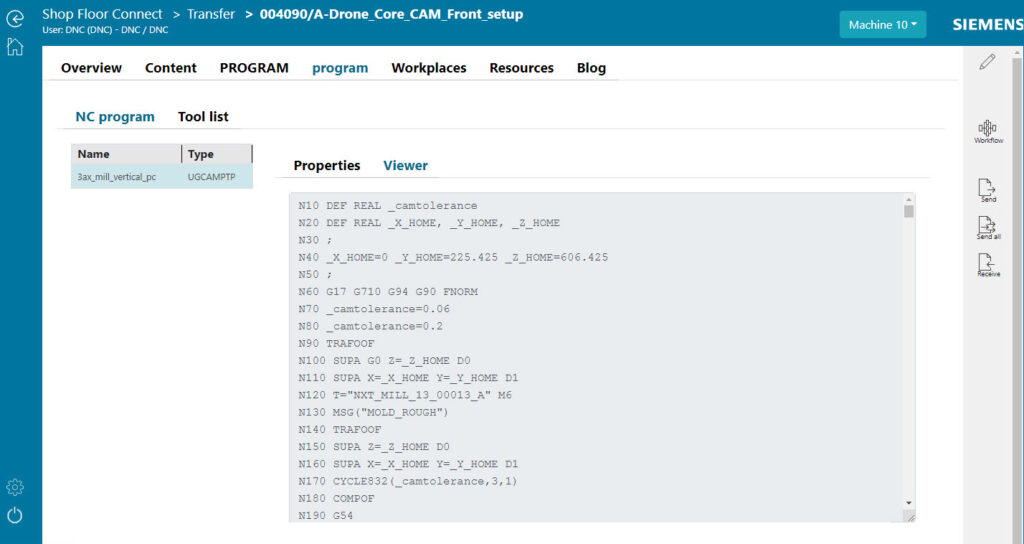
The machine operator simply selected the program he needed from the database, confident that it was approved and up to date. When machinists need to provide feedback or adjust machining parameters, they can enter it into the same Teamcenter database using the Shop Floor Connect app. This shop floor connectivity enables the shop floor personnel to instantly share this info with the manufacturing engineers, creating a true closed-loop manufacturing.
To machine this mold, we didn’t need to support unattended (lights out) production, but it would have been possible. The machining processes had been previously verified to be error-free, and rather than having an operator request NC programs from Teamcenter, cell management software could have been set up to do that automatically.
Time to implement your own Digital Machine Shop
The continuous digital thread that we’ve been following throughout this series on the Digital Machine Shop continues. Siemens offers many technologies that help companies digitalize part manufacturing, like the MindSphere’s Manage MyMachines app. It acquires machine operating data and sends it to the cloud, where it can be put to many uses – for detecting unusual energy consumption, for example, or higher than normal operating temperatures or lengthy setup times – ultimately improving operating efficiency.
My colleagues and I who wrote the quadcopter blog series thank you for interest. I hope we’ve convinced you of the many advantages a Digital Machine Shop has over a traditional, disconnected part manufacturing process. While we outlined the benefits to our own specific domains, we also reviewed the benefits to this modern, digital approach: faster time to market, improved quality and greater efficiency, to name a few.
Although our quadcopter story ends here, Siemens has a wealth of additional information that can help you implement your own Digital Machine Shop. Make sure to check out our webinar on how to gain an advantage by automating your machine shop and our eBook on the advantages of a digital machine shop for more information.
Catch up on the other blogs in the quadcopter series here, and we hope you enjoyed your journey with us through the quadcopter mold design in our Digital Machine Shop!