EV component manufacturing – Part 3
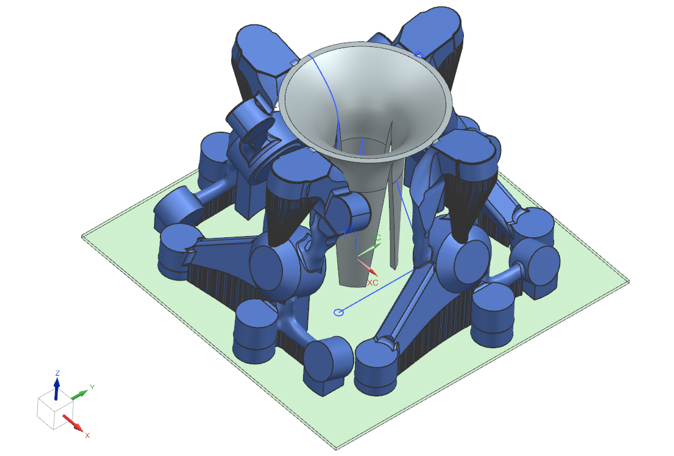
Additive Manufacturing: Design and 3D printing
In our previous blog post, we explained how we used Teamcenter as our digital backbone enabling real-time collaboration among our engineers, increasing planning efficiency, and maximizing resource utilization. With this infrastructure in place, we turn our attention to Adam, our additive manufacturing engineer located in Indiana. Adam’s responsibility was to redesign the steering knuckle to ensure lighter weight and higher performance.
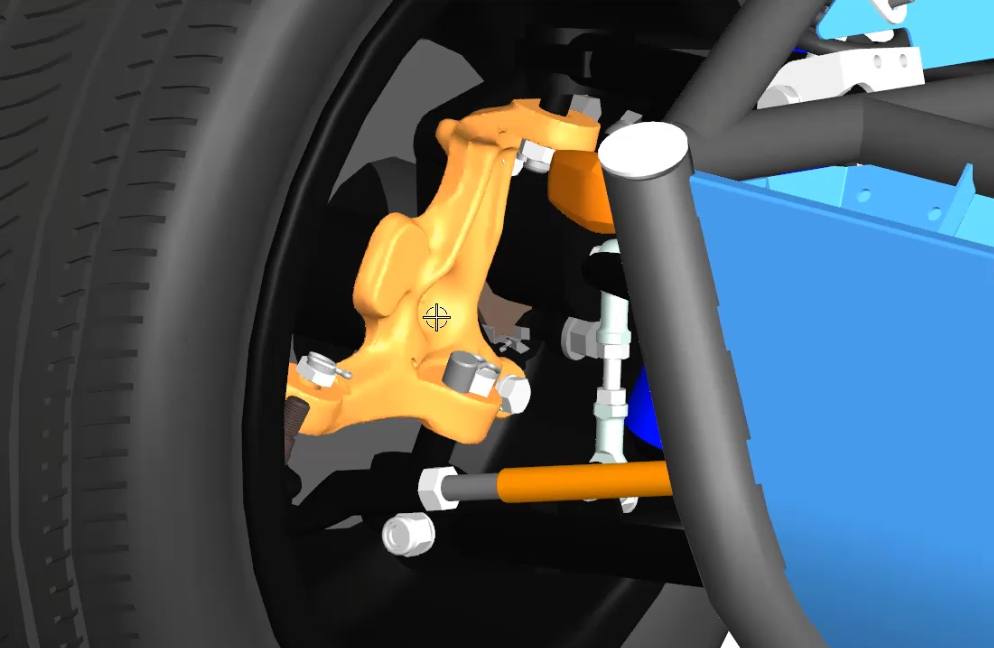
The foundation of an efficient manufacturing process is always in the design. More and more companies are using additive manufacturing as their guiding blueprint, resulting in less material waste and optimizing cost savings for real production.
We used our NX software, part of the Siemens Xcelerator portfolio, to guide our additive manufacturing design. NX allows manufacturers to create optimal part designs with integrated generative engineering tools like design space exploration, which helps us optimize the steering knuckle for production from design to post-print validation. Simulation-driven design, like topology optimization, ensures that the optimal part is created with a minimal amount of material.
Design for manufacturability
As Adam looks to optimize the part design, it is important to understand the problem that he is trying to solve. Adam isn’t simply designing the printing of the part, but he’s also designing the associated support structures and the required fixtures. Additionally, he must consider how the supports will be removed after the printing process. Solving this problem at the beginning is critical, because removing the support structures can be expensive and time-consuming manual labor.
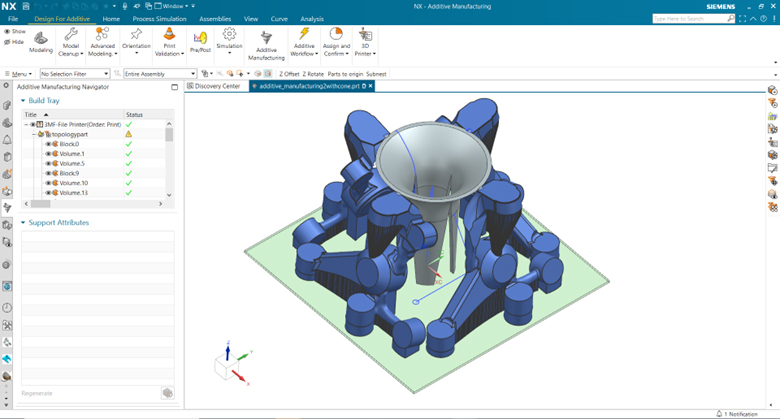
As an aside, the industrialization of additive manufacturing has been hampered by similar issues. Without designing for manufacturability, the removal of support structures will take highly skilled laborers working with manual tools like hammers, chisels, and Dremels. Additionally, design iterations and the number of variants required to perfect the part, as well as the manufacturing process, can further make the entire workflow impractical. However, digital manufacturing can change all of that by seamlessly connecting each step of the process and enabling close collaboration between design, engineering, and manufacturing.
Optimizing the part, supports, and fixtures
For this project, we almost started from scratch. Since we didn’t have a drawing of the original steering knuckle, Adam scanned the existing knuckle with a hand scanner to better understand the design spaces. He modified the scan data using convergent modeling, to improve a few surfaces so he could use it as the optimization area for his topology optimization.
Adam validates our new designs using simulation with NX additive manufacturing, checking wall thickness and other part geometry. This ensures the success of the printing processes, aligning with our goal of achieving “right first-time” printing. Additional information such as Product and Manufacturing Information (PMI) is added to the part model and stored in Teamcenter, making this information available to the entire team.
Utilizing additive manufacturing checkers within NX before placing the digital knuckle into our digitalized car, Adam was then able to design optimal support structures and custom fixturing. This unique part placement on the build plate allowed us to manufacture four steering knuckle parts with each print run.
Before printing the part, Adam was able to simulate build-distortions and create compensated geometry so we could print to specification. This ability to virtually print various designs, provides an important advantage in that you can optimize both the design and the manufacturing process. This capability is a key feature of the digital twin. After each run, Adam could look at what he had done in the digital world without consuming any physical resources and make design changes that would update the entire down stream process.
Now, after completing all the design and manufacturing engineering tasks, Adam can seamlessly hand it off to our manufacturing team within our PLM system to start manufacturing operations. We printed our digital part on the DMG MORI LASERTEC 30 DUAL in Titanium TI 64.
An end-to-end solution for additive manufacturing
In the video below, you can see how Siemens Xcelerator drives the entire process from initial design through 3D printing. It provides unmatched flexibility; for example, when a design engineer makes changes, the additive manufacturing engineer assesses the feasibility of printing it. This involves simulation testing to ensure structural integrity and to verify that fixtures can be printed alongside the part and later removed through machining. This iterative process is supported in a digital environment that helps coordinate the entire process and keeps the team in sync.
End result: a high performance EV component
We began this project with the clear objective to improve the design and performance of the steering knuckle component. Using our solutions, we were able to make substantial improvements to the manufacturing process and the component specifications.
The result was the creation of a true performance part for our EV sports car that showcased:
- An innovative design
- Improved manufacturability (additive and subtractive manufacturing)
- 45% weight reduction
- Durability improved by 150%
Continue on this journey with our team in Part 4 of this blog series where we show you how to generate advanced machining operations using modern CAM software. Coming soon!