Driving the future for engineering and simulation
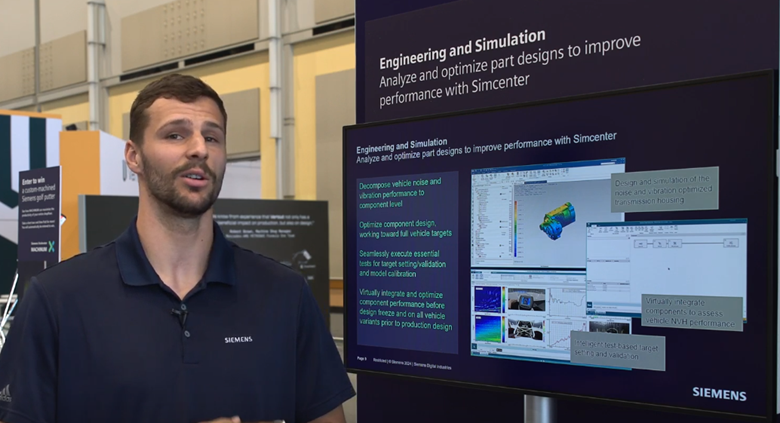
Siemens showcased how digital manufacturing is transforming the way we design, produce, and assemble high-performance components. Explore a fully integrated demonstration of the end-to-end digital thread showcased at the largest manufacturing technology show in North America, IMTS 2024. The showcase featured a seamless journey from identifying potential improvements through simulation to manufacturing and installing a new component. Experienced firsthand how cloud and AI technologies are enabling the future of manufacturing, with an innovative focus on the development of a transfer case for an electric vehicle transmission housing.
Engineering and simulation: the foundation of innovation
In the first stage of our process, Siemens Simcenter played a vital role in optimizing the transfer case design for NVH (noise, vibration, and harshness). This transfer case, built for high performance under extreme conditions, showcased significant improvements in noise reduction, vibration control, and structural strength. By digitally connecting tools for design, simulation, 3D printing, CNC machining, quality inspection, and assembly — all in collaboration with our partner ecosystems — we demonstrated the potential of a connected, data-driven manufacturing process.
Speaking at the event, Siemens engineering and simulation expert, Andrew Barlow explained:
Our challenge was to optimize the transfer case for NVH, and we did that with Simcenter 3D. Using acoustic analysis and integrations with NX CAD, we iterated on the design to achieve a 25% noise reduction and a 35% increase in strength. This optimized design was then prepared for manufacturing and assembled into the E-Rod displayed at our booth.”
Andrew Barlow, Siemens engineering and simulation expert
This process was powered by Simcenter TestLab, enabling precise acoustic analysis and correlation with real-world test data. By iterating virtually, we ensured a stronger, quieter transfer case while significantly reducing development time.
From simulation to reality: connected manufacturing
Once the design was validated through simulation, it transitioned seamlessly to the next stages of manufacturing. Attendees saw how Siemens leverages the digital twin to integrate:
- Additive manufacturing for lightweight, optimized geometries
- NX CAM for CNC machining precision
- Quality inspection tools for ensuring each part met exact specifications
- Assembly processes to bring the final product to life
This digitally connected workflow enables faster, more flexible manufacturing with greater precision and efficiency, paving the way for next-generation innovations in the automotive and other high-performance industries.
Driving the digital revolution
At IMTS, Siemens didn’t just present tools; we presented a vision of the future. By featuring an entire end-to-end digital thread for the transmission house installed on a next-generation electric vehicle. Using cloud-based solutions and AI technologies, we empower manufacturers to innovate faster, reduce costs, and improve product quality. The transfer case showcased at IMTS 2024 is more than just a component — it’s a symbol of the digital manufacturing revolution.
Interested in learning more? Watch the full video.