Dealing with Geometry: The Machinist’s Cost of Doing Business?
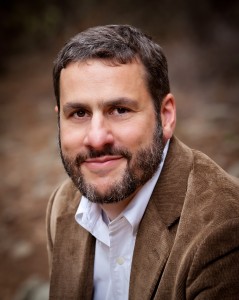
This blog post has been licensed for hosting by Siemens PLM. The concepts, ideas and positions of this post have been developed independently by Industry Analyst Chad Jackson of Lifecycle Insights. © LC Insights LLC
Design models can rarely be used as is when a manufacturing engineer receives them. They always need to be tweaked this way so they can fall out of a mold or tweaked that way so the milling machine can reach the undercut. Feature-based modeling, which can frequently lead to costly feature failures, has commonly been the approach for these activities. However, direct modeling approaches afford manufacturing engineers an entirely new way to get the job in a timely and efficient manner.
Deal with it
Are there any other words that cause so much muttering disdain? There are times in product development when you just have to buckle down and find a way around the problem. Yes, your manager admits, it’s probably a waste of your talents. No, your manager says, we can’t return it back to sender.
Such is the case, unfortunately, with design geometry and the machinist. Oftentimes, 3D models arrive in the machine shop in rough shape. There are misaligned edges, missing faces, unsealed solids and whatnot. But furthermore, machinists often need to create other representations of the design before they can do their work.
To design dies and molds, design geometry in some cases need to be tweaked to release. In other cases, design geometry must be transformed to represent its pre-machined shape.
Now, let’s be frank. All that time machinists sink into fixing and preparing geometry is a non-value add. Honestly. It’s simple a barrier that lies between the machinist and their final step: cutting metal. As a result, there’s one thing you can do with regards to this step: minimize it.
The Boon for Machinists
Ultimately, that’s why the emergence of Direct Modeling approaches is one of the most important technological advances in the past decade for machinists. Yes. I know. It doesn’t quite sound right. You’d expect it to be some uber-automated NC tool path generation algorithm. Or perhaps semi-sentient software to apply best practices.
In my eyes, however, you get more productive in one of two ways: you minimize non-value added tasks or you automate value added tasks. In a few posts, I’ll write about the second one. But here, let’s concentrate on that first one.
Why Is It Advantageous
Why are Direct Modeling tools such an advancement for machinists? Part of the answer lies in the engine that drives traditional CAD: features. For the original designer, features enable powerful and intelligent reaction to design changes. They literally can morph designs in dramatic ways. For those not familiar with how the 3D model was built, including the machinist, its merely a convoluted rats nest that results in model failures again and again. You can strip out those features by exporting and importing. However, you then have no mechanism (i.e. the original features) to make changes. You can try to fix the model, but that can take hours or even days. You could go back to the original designer, but they already have priorities that lie in new design projects. So machinists are left holding the grenade.
Direct Modeling offers an attractive alternative. There are variations on how to do it, but by and large, Direct Modeling approaches let machinists almost ignore the original features. Instead, they simply push, pull, drag, close, clean and tweak the geometry. In short, they minimize the amount of time machinists spend on fixing geometry.
The Business Perspective
Why is all this important? Well, it’s simple. The less time machinists spend wrangling geometry, the more time they can spend generated NC code and cutting metal. You can cut that lag in the development process. And if we’ve learned anything from years of studies on product development, time to market and/or delivery is critical. This represents a very real opportunity to shave more time off that cycle.
For the machinist, it’s pretty simple too: you get to eliminate a painful task. You get to spend more time on what you’ve been trained to do: generate code and cut metal. In the end, it’s about fulfillment at work.
Conclusion
The reality is clear. Machinists have and will continue to need to modify geometry to get it ready to be machined. The realistic objective is to minimize the time sunk into that non-value added task. Direct Modeling offers a very real opportunity to do that in contrast with feature-driven traditional CAD.
About the Author
Chad Jackson is the President and Principal Analyst of Lifecycle Insights, a research and advisory firm that assesses the business impact of software applications and systems on engineering organizations. Chad has more than 15 years of experience with CAD, CAE, PDM, PLM and related technologies as part of the analyst community and software industry. Due to his industry knowledge and thought leadership, Chad is a sought-after expert, author and speaker that has advised, published and presented dozens of times domestically and internationally. |