Automotive supplier designs and builds sophisticated mechatronic parts with Siemens solutions
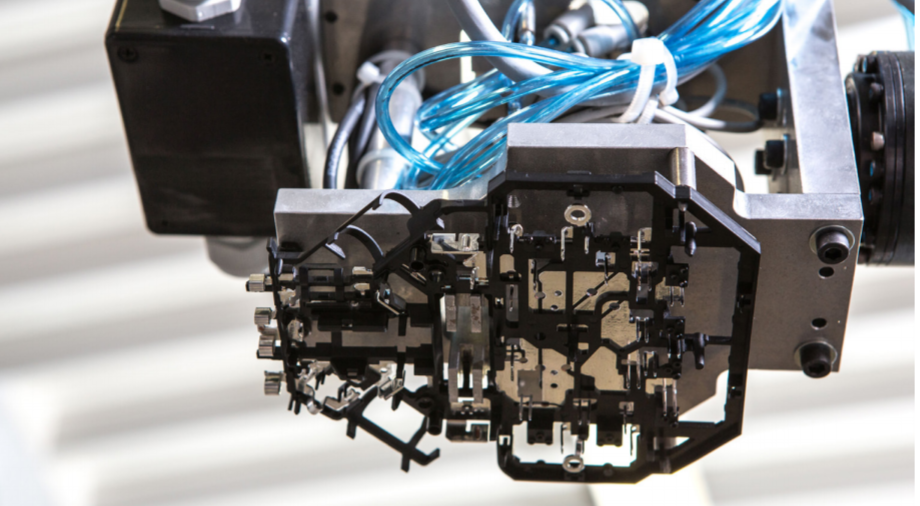
NX, Teamcenter and Tecnomatix enable Pollmann to maintain a leading position as an automotive components supplier
Almost every car manufactured around the globe includes components made by Pollmann International (Pollmann). The family business boasts more than 130 years of innovation experience and is among the global market leaders in its niche. At the company’s headquarters in Austria, Pollmann engineers create highly complex mechatronic assemblies.
Among these products are sunroof kinematics, door latches and assemblies for the engine compartment and for the power train. Recently, parts and assemblies for e-mobility applications have been added to the company’s portfolio of custom solutions. From five production facilities in Europe, Asia and North America, Pollmann supplies automotive brands around the globe with these intelligent combinations of metal, plastics and electronics.
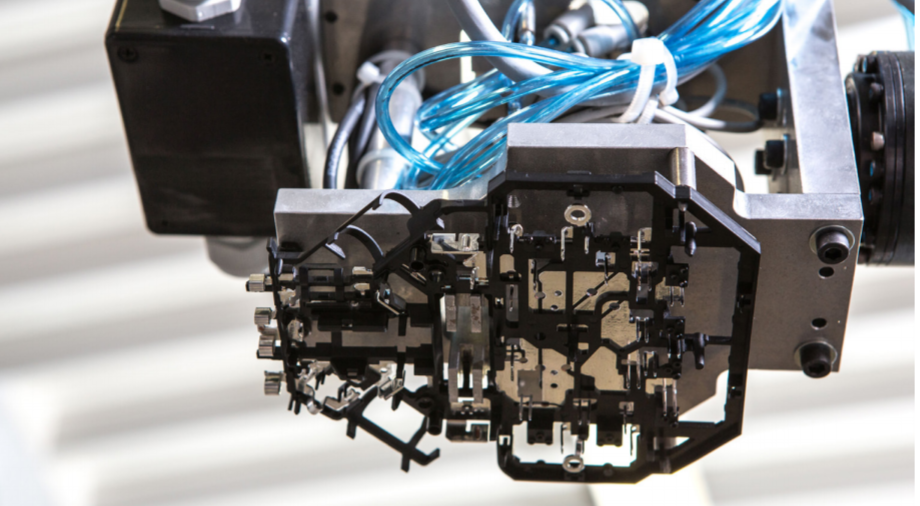
Key technologies used in the production of these components are insert injection molding, where metal parts are overmolded, and outsert injection molding, where plastic functional elements are molded onto carrying metal structures. Pollmann acts as a one-stop-shop for Tier 1 suppliers. Customers benefit from components created as integrated solutions from a single source, complete with the stamping dies and injection molds and the automated systems required for part production. At all Pollmann sites, the parts are combined to form complex assemblies ready for direct integration with the customers’ production processes.
A heterogeneous software landscape
In the past, Pollmann engineers used parametric software for computer-aided design (CAD) from one supplier and several different brands of computer-aided manufacturing (CAM) software for numerical control (NC) programming. There was no product data management (PDM) or product lifecycle management (PLM) system.
All product-related information was stored in various file-based systems. This variety of software tools and information silos became increasingly cumbersome. Due to the file-based storage, release management caused extra work and time-consuming searches as well as frequent errors. The absence of a common information base also caused delays in cross-location engineering projects. Moreover, using inconsistent methods for processing neutral format CAD data made processing 3D models from external sources difficult.
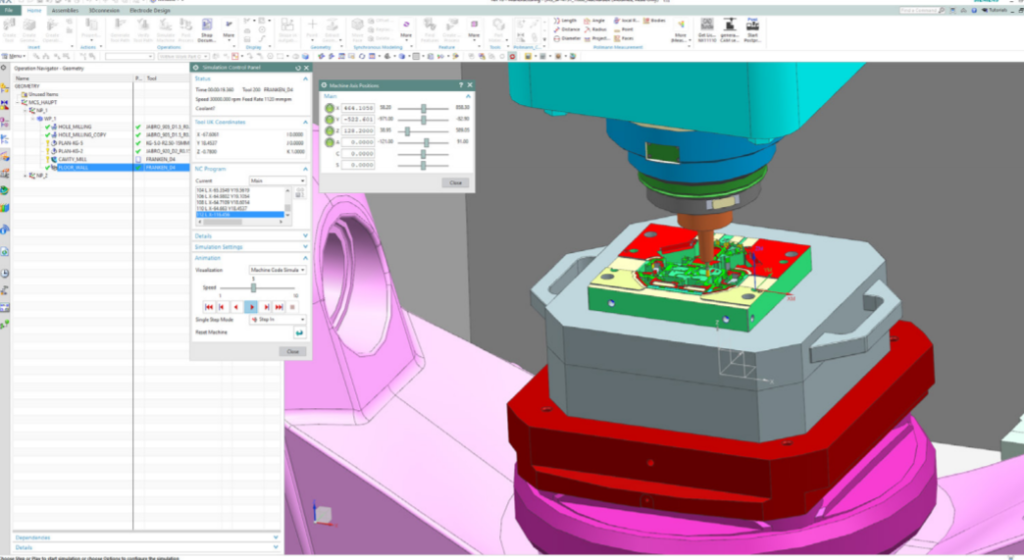
Pollmann management was aware that they needed to improve engineering information management in order to stay competitive. “Our aim was to reduce unproductive work and manage changes required by customers quickly and with tracability,” says Markus Stocklasser, design engineering manager, Pollmann. “To make global collaboration easier, we developed a vision to store and manage all product-related data and documents in a PDM system.”
An integrated solution with Teamcenter and NX
During initial market inquiries, Pollmann’s experts extended the scope of their product search to include workflow functionalities, changing their specified target system from PDM to PLM. Pollmann’s experts evaluated five software suppliers. Among these were independent PLM software providers as well as companies offering both PLM and CAD/CAM and computer-aided engineering (CAE) software. “We had also discovered shortcomings of the strictly parametric design software we had been using,” says Markus Hiess, PLM/ CAD administrator, Pollmann. “To overcome these and to achieve greater data consistency, we decided to pursue a more integrated approach, combining a new PLM system with more flexible software for CAD and CAM.”
Out of the three remaining contestants, Pollmann’s engineering experts chose a combined implementation of Siemens Digital Industries Software’s Teamcenter® software, an adaptable PLM system that connects people and processes across functional silos with a digital thread, and Siemens’ NX™ software, an integrated CAD/CAM/CAE solution.
Spanning all aspects of product creation, NX ensures full data consistency and associativity all the way from part design to tool assembly without external interfaces. NX tool design applications can work with almost any type of 3D input data. Engineers can verify their designs without leaving NX.
Future-oriented software strategy
“Using this comprehensive solution, product and part designers, tool designers and NC programmers can share the same software environment,” says Stocklasser. “As tool development can commence even before product design is completed, this considerably speeds up the overall process.”
“Teamcenter gives us full control of our product data,” adds Hiess. “The software also allows us to enforce our processes across departments and locations while relieving colleagues of undesired side activities.”
The superior properties of these software products were not the only reasons for Pollmann’s decision. “Siemens’ software strategy was a similarly important factor in our decision-making,” says Stocklasser. “The long-term commitment to extend its portfolio to cover all aspects of product and production with a digital twin and with full data consistence spoke strongly in favor of that global player.”
In a first implementation phase, Pollmann equipped about 60 workplaces across all design and tooling departments generating CAD and CAM data as well as the tooling department at its Austrian headquarters with Teamcenter and NX. To ensure a smooth transition, five key users and an administrator were designated for system implementation. As most Pollmann parts are individual items, they did not migrate any product data but decided to recreate parts in case of repeats.
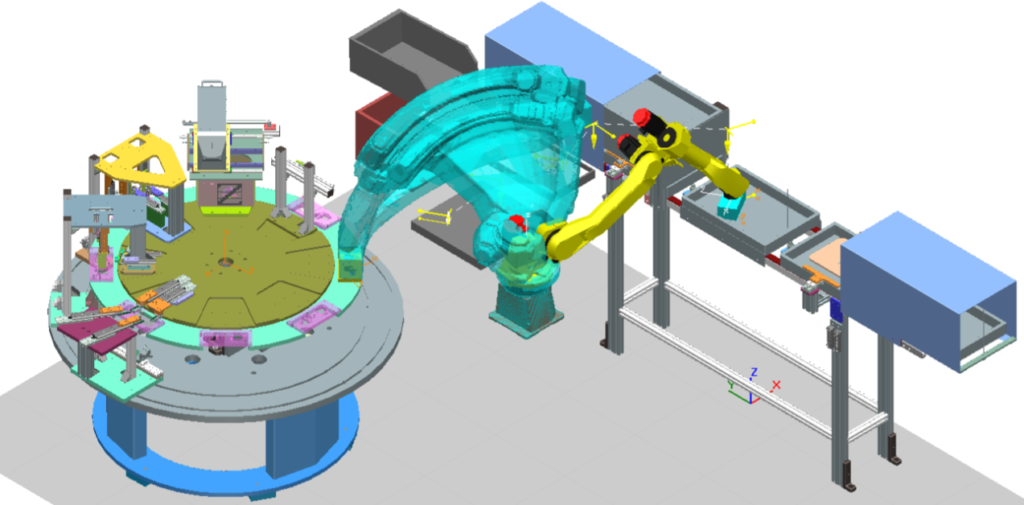
Design automation as a benefit
This transition showed considerable beneficial effects. “Using NX, motion simulations and filling studies for plastics as well as FEM calculations help us verify and evaluate part geometries even before the prototype phase,” says Hiess. “Using Teamcenter as the single source of truth, our various departments jointly develop cost-optimized solutions and innovations.”
“While NX does support parametric work, the unparalleled flexibility of its synchronous technology reduced the time required for mold design by 35 percent,” says Stocklasser. “I was also pleasantly surprised by the software’s sheet metal capabilities, especially the speed of flat projection of complex freeform sheet metal parts.”
In their tool designs, Pollmann’s engineers had always implemented logic functionality. They now utilize NX Open to automate complex and repetitive tasks. They are also using NX Mold Wizard, the NX Progressive Die Wizard and NX Electrode Wizard. Without any programming, this powerful set of automated applications can greatly optimize tooling design. NX Mold Wizard provides automated sequences for working with part geometry, creating parting surfaces and enabling automatic updates. The NX Progressive Die Wizard guides users through all of the stages required to construct a progressive die, streamlining complex processes and automating tedious tasks for significant time savings.
The NX Electrode Wizard allows automated electric discharge machining (EDM) electrode design using the die’s model that in turn has been derived from the 3D model of the part. Electrode design was once a week’s worth of work for highly skilled specialists” says Hiess. Using the NX Electrode Wizard, our people can now complete this task in two days.
“Taking advantage of the considerable speed gains NX brings, we can now design our tools with a much greater wealth of detail,” says Stocklasser. “This directly results in improved quality and manufacturability, eliminating all manual rework.”
Tecnomatix for Plant Design
Pollmann’s digitalization efforts include its automation and robotics department. There, the automotive supplier develops, manufactures and commissions custom automation solutions for in-house use. These systems range from assisted manual workplaces to highly complex injection molding equipment combined with testing and assembly functionality.
The plant engineering team use Process Simulate, a digital manufacturing solution in Siemens’ Tecnomatix® portfolio, for manufacturing process verification in a 3D environment. It allows them to virtually validate their manufacturing concepts upfront. This includes the verification of space requirements for robots and cycle time evaluations for programmable logic control (PLC) and robot programming.
For modeling, simulating, analyzing, visualizing and optimizing larger production systems and processes such as the company’s new plant in Vitis, Austria, the specialists use Plant Simulation, also part of the Tecnomatix portfolio. To create the models, the engineers import data from NX using the JT™ data format.
“Using Tecnomatix, we build the digital twin of the production facilities required to manufacture the parts we create,” says Michael Appel, industrial process and control engineer, Pollmann. “Virtual commissioning of our production cells complete with robots, conveyor belts and machines contributes to improved process stability and helps reduce our time-to-market.”
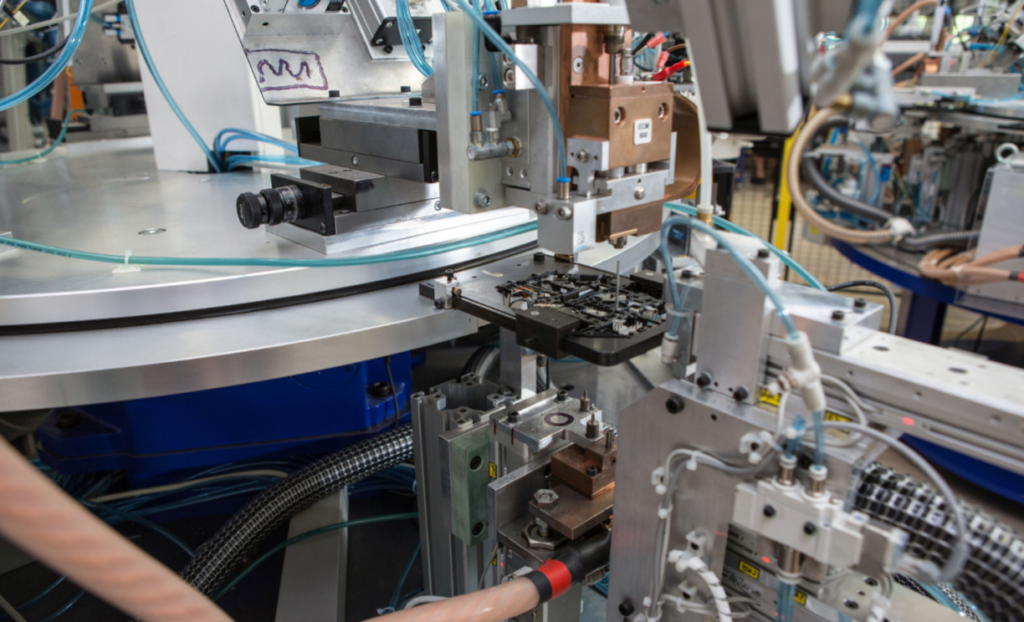
Global digitalization benefits
Following the successful implementation in the Karlstein plant, Pollmann rolled out NX and Teamcenter to all global sites. Creating a uniform PLM software environment greatly improved the intensive collaboration between locations.
“Especially at the end of tooling design phases, corrections required to make up for deformation or shrinking are timecritical,” says Hiess. “While previously we sometimes lost several days due to lack of data reconciliation between locations, this has been eliminated completely.”
In the future, all relevant product data will be available for non-technical departments as well through Microsoft® Office® integration and Teamcenter visualization. This will enable sales to create powerful presentations using valid design information.
Using Teamcenter’s workflow capabilities, all bill-of-materials (BOM), drawings, PDF and STEP files are automatically created and passed on down the line upon completion of a tool by the design engineers. “This relieves our design engineers from a lot of undesired side activities,” says Hiess. “It also prevents errors and gives us the certainty that all downstream processes are based on valid information.”