Additive Manufacturing with NX
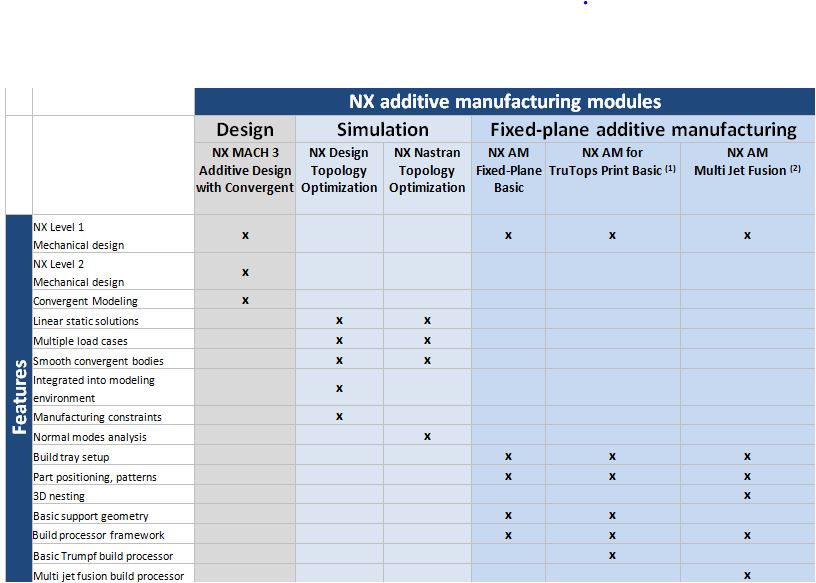
Read the complete solution overview of Siemens’ Additive Manufacturing with NX
Delivering design, simulation and manufacturing software solutions for powder bed 3D printing
Benefits
- Transform production processes and manufacture revolutionary products made of metal and plastic
- Realize a seamless design-to-3Dprinting workflow using a smart model-driven process that eliminates data conversion between applications
- Generate innovative designs that are lightweight and optimized to meet the functional and performance requirements of the product
- Work with 3D geometry consisting of facets/mesh, solids and surfaces in a single environment
- Verify that final designs will meet performance requirements prior to printing
- Support many 3D printing technologies, including 2.5-axis and multi-axis processes for metals and plastic
- Quickly adapt to design changes with a single, integrated software system for additive manufacturing
Summary
Additive manufacturing is changing the way products are made. New revolutionary machines and processes are rapidly pushing additive manufacturing from the prototype environment onto the production floor. Manufacturers are producing breakthrough product designs that were impossible to make using traditional methods. The benefits that additive production methods can provide include weight savings, better performance, simplified assemblies and more material options.
NX™ software provides a single, integrated system that meets the unique challenges of designing, optimizing and building metal and plastic components using the latest additive manufacturing methods. Because NX is a comprehensive platform for engineering design, simulation and manufacturing, you are able to combine special modeling functions with structural and topology optimization capabilities to develop groundbreaking designs using additive processes. By using NX you have the power to drive the latest additive manufacturing equipment, including powder bed 3D printers.
An integrated process
The additive manufacturing capabilities in NX facilitate the process from design model to printed part with seamless integration that eliminates the need to convert and remodel parts between applications. Production teams can now work concurrently on the same part using one comprehensive system.
This model-driven process leverages associative part models for design, simulation and 3D print planning, enabling manufacturers to quickly incorporate design changes that greatly improve accuracy and productivity. To connect the entire operation, the design and manufacturing process is managed with Siemens PLM Software’s collaboration platform, Teamcenter® software.
Optimizing design and performance
NX has a broad range of capabilities for designers and engineers to develop next-generation products. Breakthrough technology lets designers quickly create innovative, organically-shaped parts with improved performance that meet industry-specific requirements while ensuring they can be efficiently printed in 3D .
Original design; Optimize part topology; and Modify designs using Convergent Modeling
Workflow to reshape conventionally designed parts.
Convergent Modeling™ technology – For the engineer, this innovative technology greatly simplifies working with geometry consisting of facets, surfaces and solids. This generative design method helps engineers optimize part design for 3D printing, and speed up the overall process.
Scan-to-print – With Convergent Modeling technology, users can immediately begin using scanned data to design products. Combining convergent modeling with the capability to manufacture parts using 3D printing directly from NX simplifies the additive manufacturing process. The new scan-edit-and-print workflow supports the 3D manufacturing format (3MF) and Microsoft’s 3D print capabilities.
Convergent modeling enables the scan-to-print workflow.
Topology optimization – NX allows designers and engineers to create and optimize a completely new generation of product designs by taking performance requirements into account right from the start. The resulting organic shapes are lightweight and optimally satisfy all performance requirements. These breakthrough designs can be easily modified in NX with advanced capabilities, such as Convergent Modeling and synchronous technology, providing a single, complete environment to design additively manufactured components.Lightweight, organically-shaped products can be designed using topology optimization.
Design rules for 3D printing
Validating designs for 3D printing is a key step in the process. NX offers validation tools to check the following issues:
- Minimum wall thickness can be specified to ensure printability of the part
- Overhang angle lets you identify part regions that require support while printing
- Wholly enclosed volumes can be recognized to ensure efficient post-printing operations of these areas
- Printable volume quickly calculates if the part fits within the printer build volume
These validation tools help with data preparation and ensure the printability of the designed parts.
Simulation and performance engineering
Simulation engineers can use the new capabilities in the Simcenter™ portfolio and NX Nastran® software for topology optimization. The solution, designed for advanced analysts, supports static and normal modes analyses and can be used to work with models that have 1D, 2D and 3D elements and support all load types.
Furthermore, Simcenter 3D provides advanced capabilities for simulation to ensure that resulting designs satisfy all necessary performance criteria. Simcenter 3D can be completely integrated in the NX environment or it is available as a standalone system that works with any computer-aided design (CAD) system. Simcenter 3D enables engineering teams to address a variety of performance requirements for strength, vibration, acoustics, motion, flow and heat transfer.Results from topology optimization may be combined with convergent modeling techniques to further refine the design.
Print preparation
NX drives the entire 3D printing process by providing solutions for a wide range of additive technologies for both plastic and metal parts. The optimized product models from the design and simulation phase can be rapidly prepared for 3D printing.
Print job setup
NX helps engineers set up the build tray and nest parts, and define necessary support structures to prepare the setup for 3D printing.
The new NX solutions let you quickly load build tray configurations and easily position the printed parts using advanced capabilities.
Parts nesting
Optimized nesting of multiple parts on a build tray can dramatically increase the efficiency of additive manufacturing.
Metal parts can be quickly positioned and arranged in arrays using interactive assembly tools. The layout of the parts on the build tray can minimize the use of support structures so you can reduce the necessary finishing of the printed parts.
Metal parts can be easily arranged in patterns to speed up the build process, minimize use of support structures and improve printed parts quality.The automated 3D nesting (powered by Materialise technology) for plastic parts analyzes the geometry of the printed parts and arranges them on the build platform, thus saving material and minimizing the cycle time.
The automated 3D nesting of plastic parts on the build platform significantly increases printing productivity (powered by Materialise technology).
Creating support structures
Creating support structures for metal parts built using powder bed fusion methods is a necessary step that can be complex and time consuming. NX lets you automatically generate support geometry (powered by Materialise technology) while keeping associativity to the design model. The full associativity ensures automatic updates for the support structures due to subsequent engineering changes to the design. You have the flexibility to adjust the support geometry, such as using perforated walls to accelerate the printing and improve parts quality.
Advanced support structures for powder bed fusion applications can be automatically created (powered by Materialise technology).
Printer-specific output
3D printers require a set of parameters to run an efficient additive manufacturing process.
The build processor framework in NX provides support for a wide range of printers to generate the output to drive powder bed fusion 3D printers for plastic and metal parts.
You can use predefined parameters to create the right printing processes for the selected 3D printer, material and print strategy. The build processors available in NX give you the necessary flexibility to fine-tune printing parameters, including laser power and speed for a specific application.
Build processors can be obtained by contacting manufacturers of 3D printers supported by the Siemens PLM Software solution for additive manufacturing. Note that if you already have a Materialise build processor, you can easily access it in NX to generate the right output for your 3D printer.
To validate the additive process, you can preview the actual laser path layer-by-layer before sending it to the printer.
Technology partners
By working closely with leading manufacturers of industrial 3D printers, Siemens PLM Software has developed complete solutions to support powder bed fusion methods with NX, all with the capability of providing quick, associative updates to product or process changes.
Powder bed 3D printing
NX supports advanced powder bed additive methods that are described below.
Powder bed fusion
This 2.5-axis printing method involves spreading a thin layer of metal powder over a previously applied layer and selectively fusing some of this powder to the workpiece with a laser or electron beam. Parts are built up in one direction by layers.Powder bed fusion technologies enable you to build parts by fusing powder to the workplace layer-by-layer.HP Multi Jet Fusion technology
HP Multi Jet Fusion technology delivers advantages in build speed and control over part and material properties. By jetting HP functional agents using HP printheads, each layer of a part is defined by an area that is fused (or transformed) and surrounded by unfused powder, so material in the working area can be fused with energy, detailed and transformed point-by-point. Using the integrated Materialise build processor, NX can drive the latest HP Jet Fusion 3D printers, which can significantly speed up the production of high-quality functional parts.
Multi Jet Fusion deposits material using a multiport print head similar to ink jet printers (image courtesy of HP).Manufacturing production-quality finished parts
3D printed parts often require additional machining operations to achieve a high-quality surface finish and dimensional accuracy.
With the integrated computer-aided manufacturing (CAM) capabilities in NX, you can use the same 3D part model to create precise toolpaths to finish the printed parts with computer numerical control (CNC) machine tools.
NX CAM software provides advanced CNC programming capabilities, ranging from feature-based recognition to 5-axis milling, allowing you to efficiently machine printed parts of any complexity.
Printed parts can be finished using the advanced NC programming capabilities of NX CAM.
The accuracy of the finished parts can be inspected with coordinate measuring machines (CMM). NX CMM Inspection Programming lets you automatically create standard inspection programs to drive a wide range of inspection equipment, ensuring production of high-quality parts.
Beyond powder bed 3D printing
In addition to powder bed methods, NX supports other additive manufacturing processes.
Multi-axis fused deposition modeling involves squeezing molten, viscous material through a nozzle and depositing it in layers on the workpiece where it fuses. This method is used for plastic-and carbon-reinforced nylon materials and is suited for multi-axis robotic configurations. This deposition method provides more opportunities for geometry and size variations without supporting structures.
Hybrid-additive manufacturing involves spraying powder through a nozzle into a melt pool on the workpiece. The melt pool is created by a laser. The 3D printing method is combined with CNC machining in a single machine, making it possible to finish parts in a single setup. NX can drive the latest hybrid additive machines from DMG MORI.
Transform your manufacturing
With NX, the smart model drives all design and manufacturing processes necessary for 3D printing, CNC machining and CMM inspection.
Integrated in one solution, these revolutionary technologies will dramatically transform your manufacturing processes and enable you to make next-generation products.
NX Additive Manufacturing modules and features
Notes:
(1)Package available from Trumpf
(2)Available soon