What’s New in NX | June 2023 | Performance Predictor

Introducing Performance Predictor
It’s time for the second episode in our new What’s New derivative content series! We’re exploring new capabilities added to the June 2023 release of NX™ software. In today’s episode, we’re taking a look at new tool; Performance Predictor. Let’s dive straight in 👇
What is Performance Predictor?
Performance Predictor focuses on validating material choices and mechanical performance of individual parts. It allows for a linear static analysis of a part with multiple constraints, loads, and a user-defined material.
Throughout the course of this blog (and the corresponding video) we’ll be taking a look at a typical Performance Predictor workflow, and how it can add real value when conducting simulation studies. The focus is on the coffee machine used in our June 2023 YouTube premiere; be sure to check that out if you missed it ⬅️
The tamping system
We’ll be using Performance Predictor to evaluate the tamping system within the coffee machine. The swinging mechanism pushes water through ground coffee at pressure to create espresso. Once done, it then ejects the used coffee for disposal. we’re going to simulate how the water pressure affects the mechanical performance of the system and test different materials.
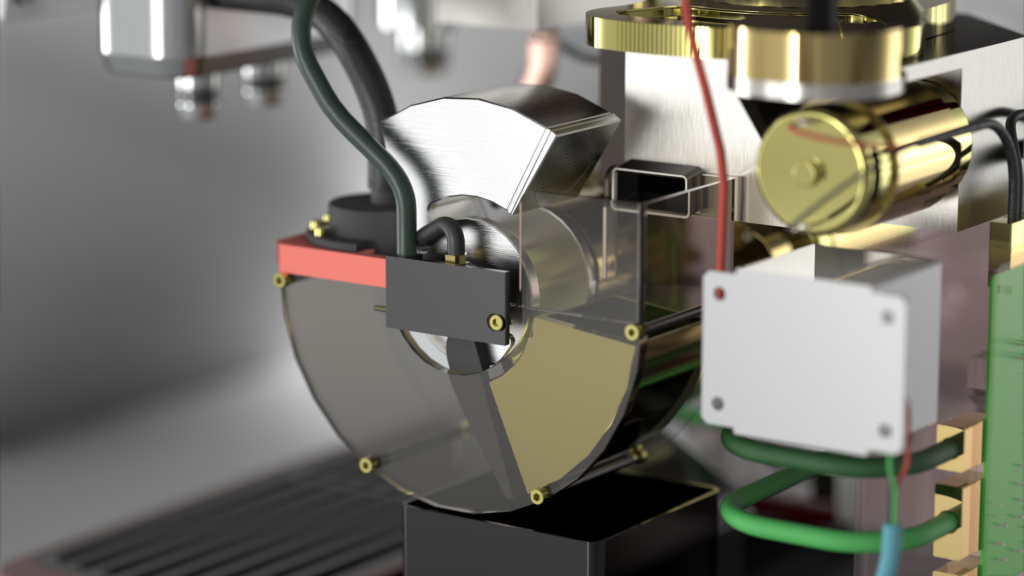
Setting up the analysis
Once the materials are assigned to the part, at this point it’s a case of defining constraints for our simulation. The constraints can be chosen and applied to the relevant faces on the part. Next, the loads for simulation need to be defined. All of these different elements are visible for review within the Performance Predictor navigator.
Results of the analysis
The analysis will run in the background – there’s no need to do anything else at this stage other than wait. Performance Predictor excels as it will run the analysis quickly and easily. Additionally, the analysis will display the part in a heatmap style display. It’s a quick and intuitive display to see where the maximum stresses are on the part.
Making tweaks to the tamping system
Changing material options
Once the initial analysis is completed, it’s important to remember that tweaks need to be made to any model too. In this use case, the part deforms too much when using aluminium, so the material is changed to steel, and a new simulation is ran. The new simulation results can be read easily; with steel, the displacement has decreased, and the material stress is now within an acceptable range.
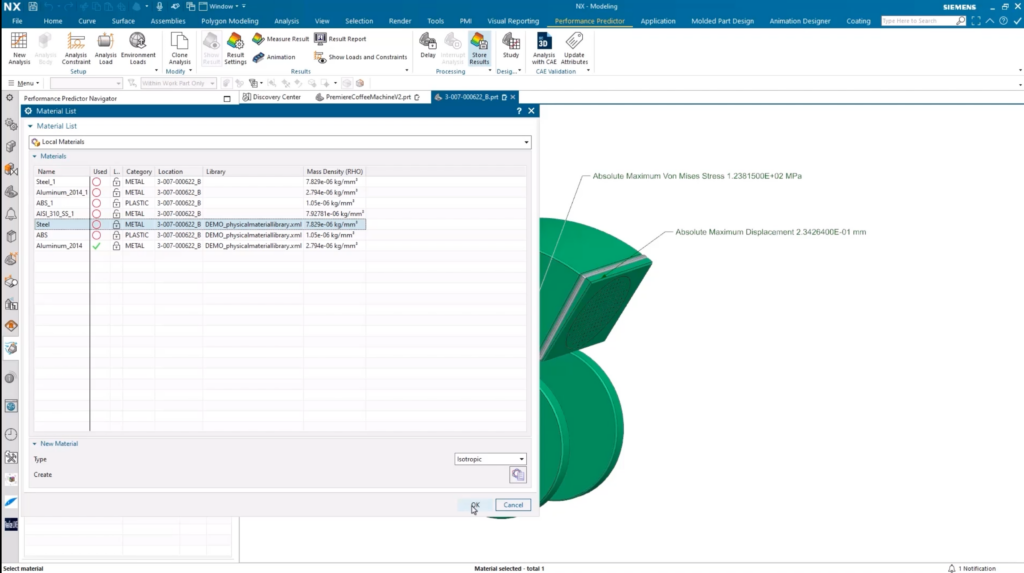
Analyzing mechanical design changes
The Performance Predictor study indicated steel as the best option, but we can also refine elements of the part to see how that will impact its performance. Edge blends with the most stress can be tweaked from directly within the Performance Predictor view, and the analysis recomputed automatically.
With the simulation complete, it can be viewed in a results report and shared with colleagues and stakeholders.
Continue your journey with NX
That brings our deep dive into Performance Predictor to a close. We really think that this type of simulation is a real game changer, and will enable you to optimize the mechanical performance of your designs. Having the ability to validate your own design systems in real-time will empower you to test and iterate ideas quickly before designs process to final validation.
Make sure to continue your journey with NX by taking a look at our content below 👇