Realize LIVE blog series: Siemens NX add-on for Additive Manufacturing with CIIRC
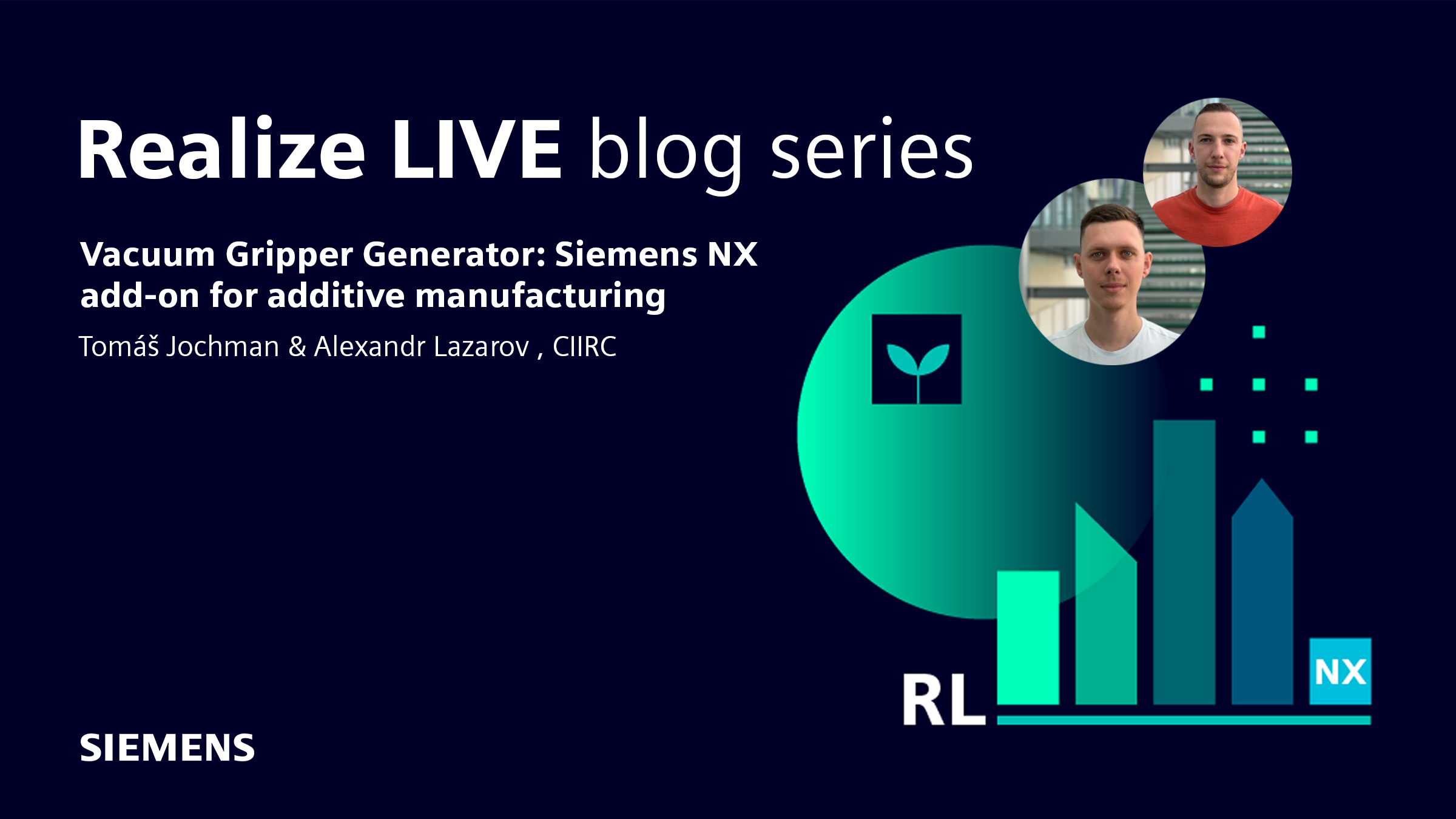
At Realize LIVE 2024, the Czech Institute of Informatics, Robotics, and Cybernetics (CIIRC) from the Czech Technical University showcased their groundbreaking work on a vacuum gripper generator. This innovative project, which has been in development for the past year, promises to significantly reduce costs and effort in creating end effectors, transforming a process that used to take hours or days into one that can be completed in mere minutes.
Introduction to CIIRC
Alex Lazarov, the head of the additive manufacturing lab, introduced the team and their mission. “We are from the Czech Institute of Informatics, Robotics, and Cybernetics, part of the Czech Technical University. Our department, Three Cape Testbed Prague, focuses heavily on Industry 4.0,” he explained. Since 2013, CIIRC has invested 50 million euros in 20 robotic workplaces and nearly 3 million euros in additive manufacturing machinery, emphasizing their commitment to bridging the gap between academia and industry.
The vacuum gripper generator
The session highlighted the development journey of the vacuum gripper generator, a tool designed to automate and streamline the creation of end effectors. “What it brings to you is lowering your costs and effort to make end effectors on a daily basis,” Lazarov noted. The generator reduces the time required to create an effector from hours or days to just minutes, a significant improvement for manufacturing efficiency.
Collaboration and innovation
Tomáš, a researcher and developer at CIIRC, emphasized their long-term partnership with Siemens, which has spanned over a decade. “On our 20 workplaces, we are utilizing hardware and software components from Siemens, including PLCs, HMIs, and NX for CAD and CAM,” he said. This collaboration has been crucial in developing and validating the vacuum gripper generator.
The Lego project
The inspiration for the vacuum gripper generator came from a project with Lego. “Lego came to us and said, ‘Guys, we are in big trouble. Our bin picking is not working. We need a solution in one month,’” Tomáš recounted. The team developed a 4-kilogram gripper, but it was too heavy and affected the work cell’s performance. This challenge led to the creation of a lighter, more efficient design using NX, which incorporated pathways for compressed air or vacuum.
Automating the design process
The need to automate the design process became evident as CIIRC managed 20 workplaces. “It’s not possible to design such a complicated gripper each time manually,” Tomáš explained. The project, initiated with Siemens Czech Republic and validated with Stoibli, aimed to create a user-friendly plugin that simplifies the design process. “The inputs from the users should be as little as possible,” he added, highlighting the plugin’s ease of use.
Functional and efficient design
The session also covered the technical aspects of the vacuum gripper generator. “Using this plugin, a designer can create the necessary geometries in a few seconds,” Tomáš said. The plugin also considers forces and loads, ensuring the gripper’s functionality and efficiency. The team utilized additive manufacturing to create functional parts with integrated threads, allowing for easy assembly and use.
Advanced manufacturing techniques
CIIRC’s use of powder bed technology in additive manufacturing enables the creation of hollow structures, which serve as both mechanical structures and pathways for compressed air or vacuum. “We can print them and use them as a mechanical structure of the whole gripper,” Tomáš explained. The team also leveraged lattice structures in NX to enhance the stiffness and reduce deflection of the parts.
Simcenter 3D integration
A key highlight of the session was the integration of Simcenter 3D into the design process. “We use Simcenter 3D to generate the outer shell and meshing surface automatically,” Tomáš noted. This automation simplifies the evaluation process, allowing users to generate heat maps and reflect on the results with just one click. “We wanted to make it as simple as possible while ensuring valuable results,” he added. This approach also supports the use of various materials, making it versatile for different applications.
Seamless integration with NX
CIIRC’s innovative software solution integrates seamlessly into the Siemens NX environment, making production in Siemens AM a simple one-click solution. “Using advanced powder-based polymer printing, our add-on ensures that complex structures retain all crucial details and functionalities,” Tomáš explained. The modular architecture guarantees optimal geometry, lightweight design, and cost efficiency, perfect for agile manufacturing.
With this add-on, users can effortlessly select the ideal vacuum effector for their industrial manipulators. The software adapts the geometry based on specific parameters like the center of gravity and load conditions, ensuring precise and stable gripping. Before production, users can validate the strength and suitability of the designed gripper, ensuring it meets their requirements.
Customizable modules
The system features a variety of customizable modules, including robot flange attachments, effector identifiers, pressure sensors, and suction cups. “We’ve also integrated an external product catalog from Festo, Schunk, and others, allowing for seamless incorporation of additional components based on user needs,” Tomáš highlighted. This flexibility ensures that the solution can be tailored to meet diverse industrial requirements.
Real-world applications
The vacuum gripper generator has already proven its value in real-world applications. Tomáš shared an example of a project involving the disassembly of EV batteries for a company. “We used this gripper for disassembly of BMW i3 batteries,” he explained. The gripper’s mechanical side was used to pick up modules, while the vacuum side dismantled other parts like covers. This project demonstrated the gripper’s effectiveness and versatility in industrial settings.
Conclusion
The vacuum gripper generator developed by CIIRC represents a significant advancement in manufacturing technology. By automating the design process and utilizing advanced manufacturing techniques, CIIRC has created a tool that not only reduces costs and effort but also enhances the efficiency and functionality of end effectors. This project exemplifies the innovative spirit and collaborative efforts that drive progress in robotics and manufacturing.