Design for Purpose: HEEDS Design Exploration Study
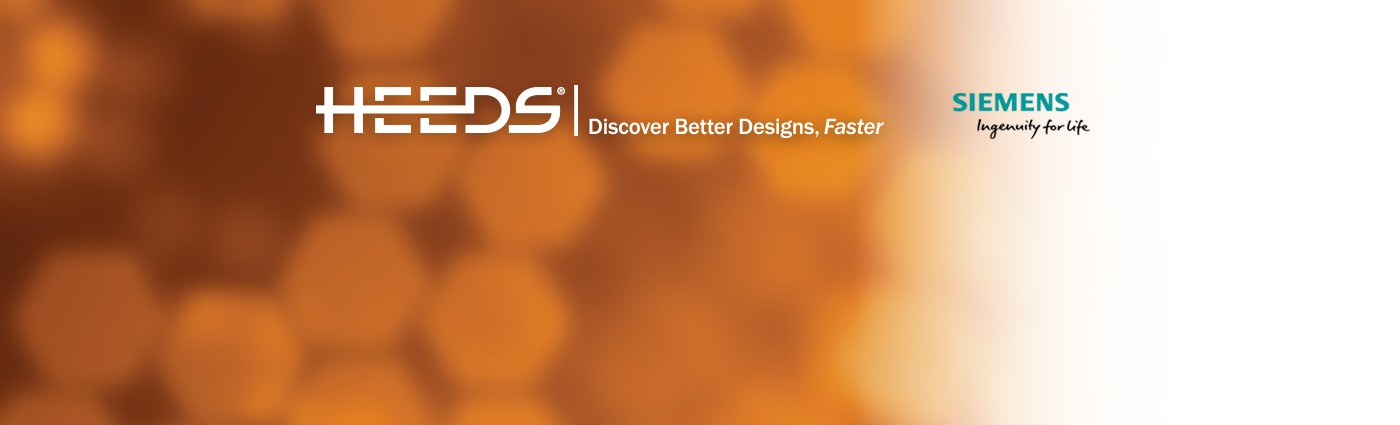
Welcome back to the Design for Purpose series, where I explain and demonstrate Siemen NX’s cohesive product lifecycle development workflow. We’ve previously explored the topics of lattice capabilities, Multimech integration, and benefits of virtual testing and simulation in relation to sustainable manufacturing. Now we are ready to explore the final step of this workflow.
Today, consumers are willing to pay higher prices for ecologically friendly products. This is great news for environmentally conscious companies who are ready to modernize their design processes. Advancing design methods can drastically reduce energy usage and abate material byproducts. While this is the goal for many engineers, HEEDS can make it happen.
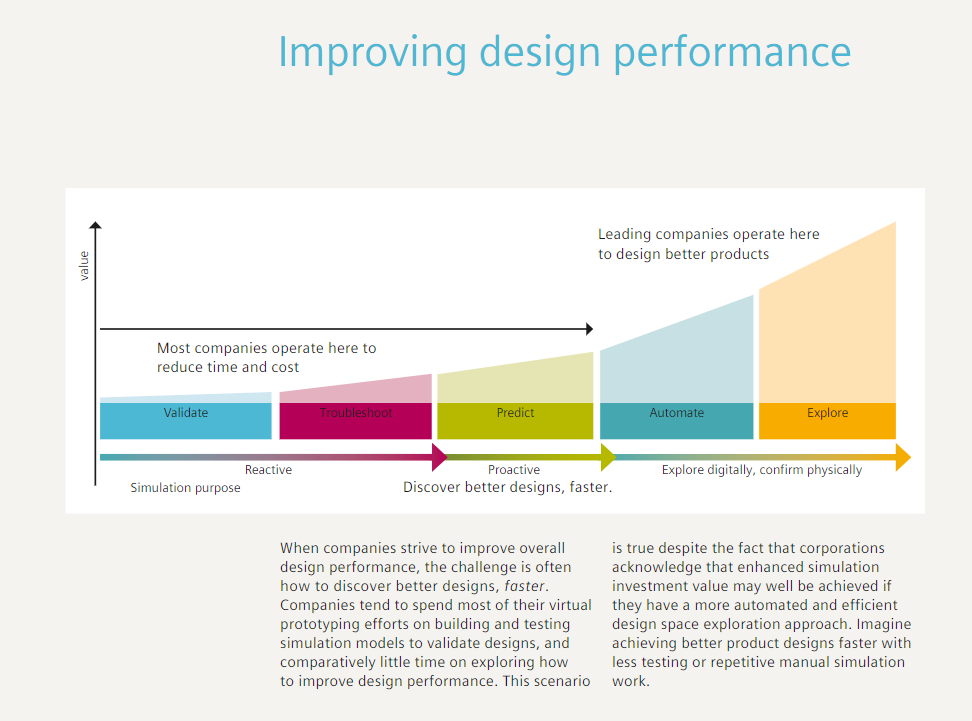
HEEDS is a design exploration and optimization software that enables engineers to determine the most efficient and sustainable design. It allows users to drive product innovation and accelerate the product development process by automating analysis workflows. Completely integrated within Siemens Simcenter 3D, HEEDS further maximizes the available computational hardware and software resources available. This software package efficiently explores the design space for innovative solutions while assessing new concepts to ensure performance requirements are met. HEEDS integration allows you to save tremendous amounts of time and resources to get your products to market faster.
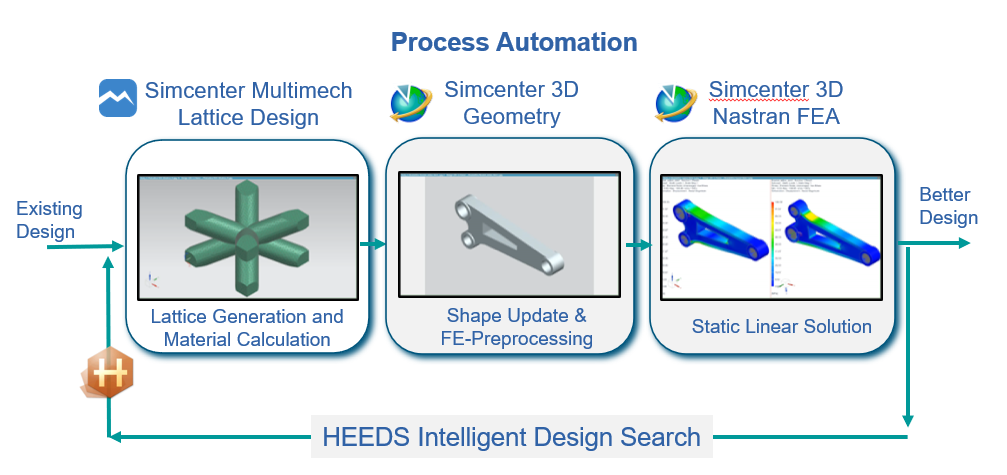
As opposed to most traditional optimization tools that require expert technical skill and simplification of models, HEEDS can be used by engineers and designers to unlock innovation. HEEDS includes proprietary Design Space Exploration functionality to efficiently find design concepts that meet or exceed performance requirements. It automatically adapts its search strategy as it learns more about the design space to find the top solution within the chosen timeframe. HEEDS delivers the ability to effortlessly compare performance over a wide spectrum of designs that display desirable features and robustness. Instead of an entire team of engineers spending weeks to create optimized designs, HEEDS does it for you in hours.
HEEDS assists in the visualization of design performance trade-offs between opposing objectives and constraints. Results are analyzed and many plots, tables, graphs, and images are automatically created to discover state-of-the-art outcomes. The numerous capabilities that HEEDS offers enables the development of designs that are production-ready, producing a true digital twin! HEEDS automated workflow facilitates easy product development cycles and quickly integrates many technologies without the need for custom scripting. The data is then automatically shared between different modeling and simulation products to evaluate performance trade-offs and design robustness. Quick optimization allows for efficient designs that are lightweight, structurally improved, and easily manufacturable. This process radically reduces material waste and energy consumption throughout the lifetime of the part.
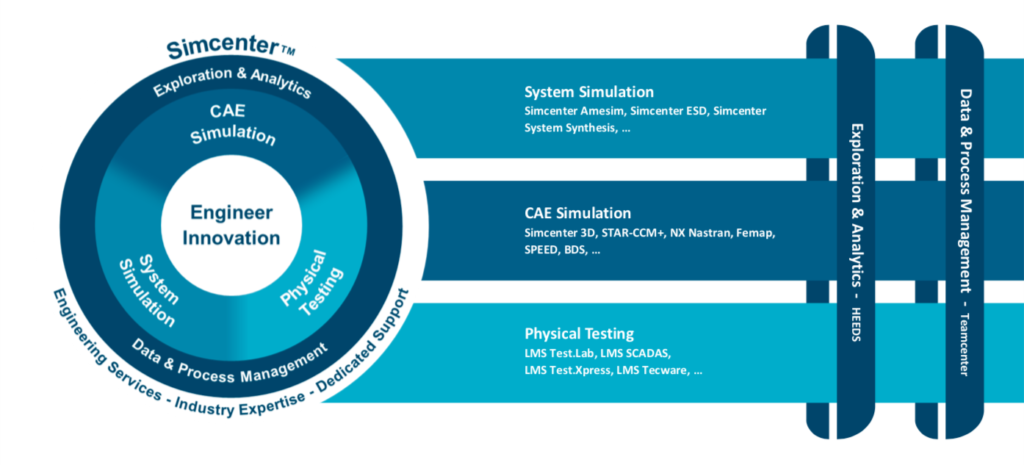
To prove it to you, let’s watch a demonstration of HEEDS in action. Continuing with the drone mold die part that we’ve redesigned with lattice structures for additive manufacturing, we’re going to run a HEEDS study to explore 10 different design options. The changing parameter is the thickness of the lattice structures, ranging from 0.2 mm to 0.5 mm. To determine the optimal design, the Von-Mises stress output will be compared and the design that generates the least amount of stress will be chosen. The demonstration workflow is relatively simple with only three steps: first, generating the lattice structures with varying width. Second, loading the lattice file generated in step one into Multimech for analysis and exporting to simulation when complete. Third, run the simulation on the drone mold die with the automatically imported material properties. With this workflow in mind, creating a new HEEDS study is easy. First, add portals to generate the lattice and run the simulation (Simcenter and Nastran portals), as well as an analysis portal for importing the lattice variations of each design’s simulation. Next, for each portal, we add execution commands, input and output files, dependencies, and environment variables. Moving forward, study variables are identified, and responses are created. Subsequently, files containing the documented parameters are tagged so that HEEDS can locate and record their values. The final step is to create the design set and response objective. For this example, ten designs of variable lattice structure thickness are evaluated for stress minimization.
As seen in the video, HEEDS delivers user-friendly process automation for straightforward and effortless configuration. While not explicitly shown in this video, the creation of the tagged Macro file was recorded in the Multimech export process in NX, the design number tag being required to adjust the file paths generated by Macro. With HEEDS integration with NX, you’ll discover better designs, increase productivity, decrease material waste, and lower energy usage.
You’ve now seen the entire workflow for how NX, Multimech, Simcenter Simulation, and HEEDS are fully integrated for additive manufacturing processes. But don’t let it stop there; this workflow is adaptive for all designs and projects. Design for purpose can be applied for nearly all projects. Is it possible to create a study on an office chair design to minimize cost and reduce stress on the chair legs? Yes! Can this workflow be used to make a vacuum study to maximize suction power? Undoubtedly! Are you able to optimize a cooler design to increase insulation and decrease mass? Affirmative! Innovation shouldn’t involve jumping through hoops. The next article will detail how to apply the fully integrated additive manufacturing lifecycle development process as a catalyst for sustainable innovation.