Adventures in 3D Printing
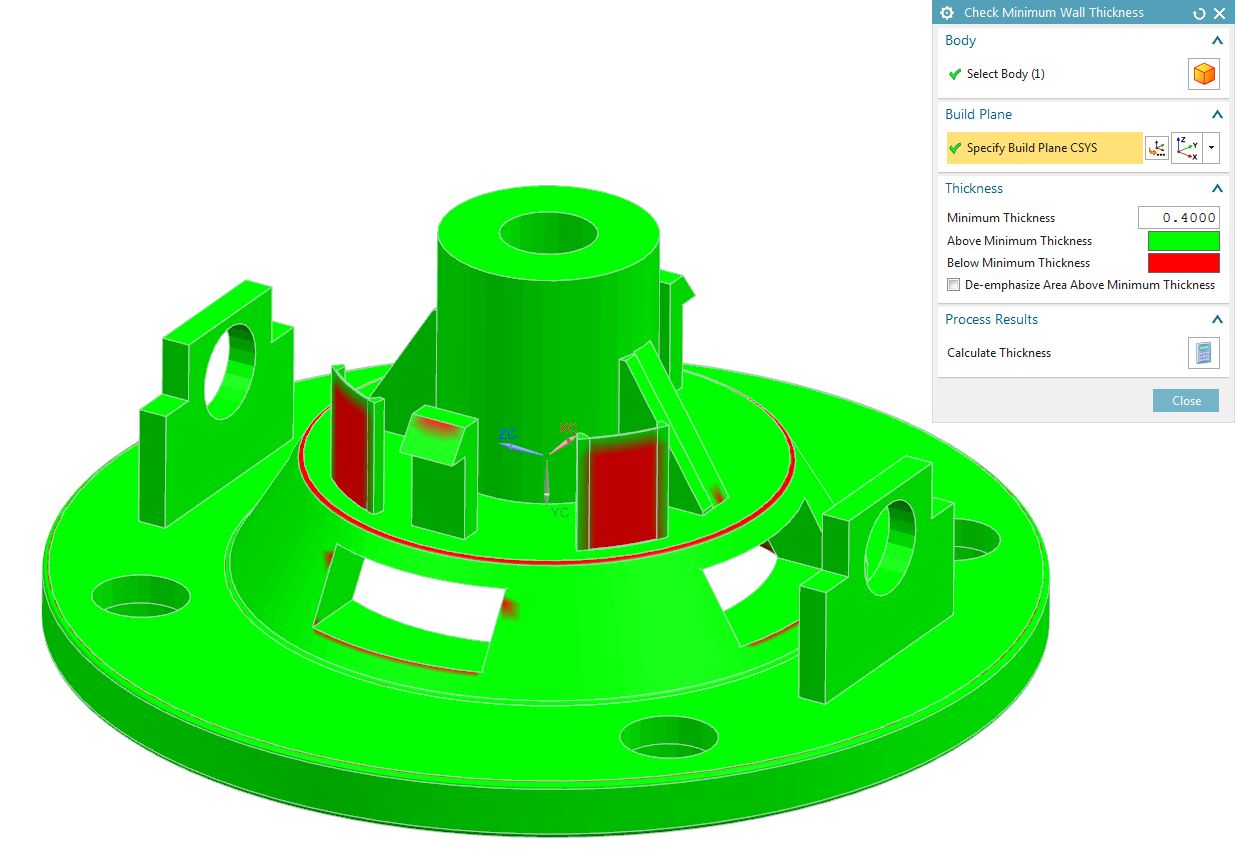
To go forward, you must first look back…
Figure 1- The metal awl from Tel Tsaf upon discovery. – Credit: PLOS ONE, doi: 10.1371/journal.pone.0096882In 2014, archaeologists working a site in Israel called Tel Tsaf uncovered an amazing artifact. The village dates as far back as 5100 B.C. It was first discovered in the 1950’s, and archaeologists have been working there since, even up to the present day. While excavating a grave in the village, the team came across a copper awl that was most likely set into a wooden handle. The exact use of the awl is still a mystery, but the awl itself has been deemed to be between 6,000 and 7,000 years old, making it the oldest metal object discovered to date.
Humans throughout time have taken inspiration from past generations when building the future. We as a species have been working metal since the time that that awl was created, through the Bronze Age and the Iron Age, up to the modern day. More recently, advances in chemical engineering have given us plastics, which we have been molding, extruding, and machining since the beginning of the 20th Century. This means that there are decades, sometimes even millennia, of experience guiding the designer’s hand when the final product is manufactured using methods and materials such as these.
However, we may not always be able to look to the past for guidance applicable to the present. When it comes to 3D printing (or “additive manufacturing”), the technology is relatively new, so there are rarely years of experience to build upon. The ability to place minute amounts of material in specific 3D positions has really only been commercially possible since the early 1990’s. Without millennia or even decades of experience to fall back on, how do you answer questions of manufacturability when it comes to additive manufacturing?
Make it and break it…
One way to solve the up-front manufacturability problem is simply to create knowledge through experimentation. In this case, that occurs by attempting (often multiple times) to manufacture the part in question. In many cases, trial runs and prototypes of printed parts can be created relatively inexpensively. Therefore, it is no wonder that we often see our customers begin experimentation with 3D printing by turning out prototypes. There is good reason why the terms “3D printing” and “rapid prototyping” are often used in the same breath.
Figure 2- Areas where there are thin walls that could not be replicated by the printerHowever, once people make prototypes and test parts, they often realize that the process generates more questions than answers. Can my part print accurately on this printer? Depending on the printer resolution, some regions might distort or not be represented at all. Should you add support structures? Support structures added at manufacturing time might affect the surface quality and require post-processing steps to correct. Can I even print this part on a given machine? If your part is larger than the build volume of the printer, you may need to select a different printer or segment the part into pieces. The problem is that the answers to these questions will most likely differ with each new part to be printed, each new machine acquired, and each new material used. Meanwhile, answering these questions incorrectly can waste both time and money.
Trust but verify…
At Siemens, we have been working to fill this dearth of process knowledge. This work includes internal experimentation, cooperation with partners and customers, as well as outright research. As we learn about the limits and intricacies of 3D printing, we are beginning to build this knowledge into our software. In NX 11.0.1, we have introduced a series of additive manufacturing validation tools. The goal is to give our customers the benefits of experience without having to create the knowledge from whole cloth.
Figure 3- Checking a part for minimum wall thickness at design time in NX 11.0.1Traditionally, validation of printed parts happens at manufacturing time. Most products on the market allow the shop floor operator to confirm the validity of a part for printing prior to starting the print, and validation at this stage is very useful for avoiding print errors. Ideally, however, the designer would have information about the viability of a part for printing long before it ever got to the shop floor. Having knowledge about the 3D printing viability of a part at the design stage can save time and money compared to addressing such issues at manufacturing time. Take, for example, knowing up-front if a part needs redesign to avoid support structures in a specific area. This is a huge time and money saver compared with discovering that the part has a compromised surface finish after manufacturing.
The validation tools in NX 11.0.1 allow our customers to identify areas of concern when 3D printing parts. These checks, which are available at design time, can help our customers answer important questions about the print viability of their part. Will the part fit within the build envelope of the selected printer? Do support structures need to be added? Will the support structures be able to be removed if they are added? Will the final print accurately represent the part as designed?
More to come…
At Siemens, we believe there is great value in up-front validation of additive manufacturing parts. Therefore, the utilities we have introduced into NX 11.0.1 are just the beginning of a multi-release process. As our partners, our customers, and we as a company learn more about how 3D printing works, we will continue to add more opportunities for up-front validation of 3D printed parts to NX to ensure that all of our customers can benefit from the knowledge gained by experience.
Imagine those first metalworkers thousands of years ago as they took the initial baby steps in the timeline of manufacturing. One can envision their ancient fires glowing as they experimented with smelting metal—forming it, learning, and trading valuable knowledge as they went. The designs of today truly are built upon knowledge from the past, even if that past is relatively recent history, as in the case of 3D printing.