Corporate
Future of Motor City Manufacturing
Automation World’s David Greenfield recently shared Reasons for U.S. Manufacturing’s Upswing, insights from a Kiplinger report. He noted that industries that require more advanced technology and ...
Automation World’s David Greenfield recently shared Reasons for U.S. Manufacturing’s Upswing, insights from a Kiplinger report. He noted that industries that require more advanced technology and processing – like aviation, auto making, biotechnology and industrial machinery are likely to stay put.
“The relative cost of producing in the U.S. versus overseas is declining; productivity improvements due to automation are shearing per-unit labor costs in the U.S. while wages elsewhere in the world increase; domestic energy supplies are abundant; fewer worries about intellectual property and technology theft; more timely deliveries; political stability; and legal and regulatory systems that are clearer and more easily navigated.”
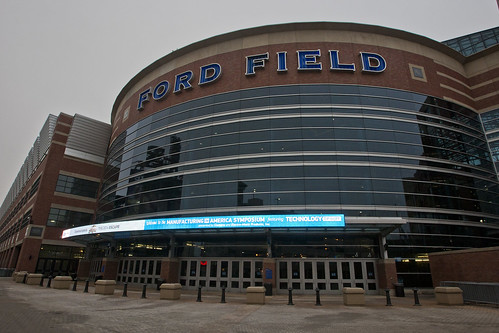
It’s against that backdrop that we’ve been having a series of conversations on the Software Revolution in Manufacturing. Last month we talked about training the next generation of technical rock stars in Ohio. This month the conversation moved to the Motor City, Michigan.
View some of the video and photo highlights on our interactive news release. Here are some of my notes from the event for a bit more of the discussion. Industry, academic and political leaders shared some stats and commentary about the future of manufacturing and future workforce:
- Future of Manufacturing: There is $1.8 trillion USD on the balance sheets – so this is the right time for manufacturing investment.
- Future of Manufacturing: The U.S. government spends less than 3 percent on R&D
- Future of Manufacturing: More than $100 billion in new manufacturing investments are underway or being planned.
- Future Workforce: According to a recent report by the World Economic Forum, 10 million manufacturing jobs around the globe are currently un-filled due to a growing skills gap.
- Future Workforce: The U.S. Chamber of Commerce notes there are more than 3 million jobs unfilled in America due to a skills gap despite high unemployment levels.
- Future Workforce: Just 40 percent of graduates are ready to work on day one, and companies have to supplement their training. 50 percent have the problem-solving skills needed by industry.
That last bullet highlights the skills/training gap we’re working to close as well as the need for more real-world problems, projects and competitions. Read more at Siemens PLM Software CEO Chuck Grindstaff’s executive blog post.
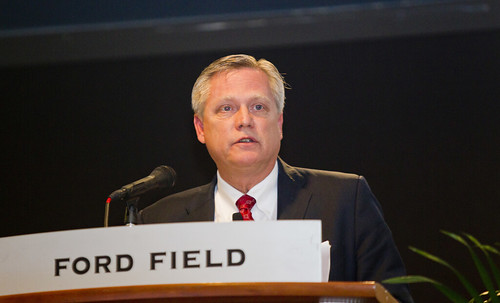
Chuck emphasized to the audience in Detroit the role software plays in modernizing manufacturing both from an infrastructure standpoint and in changing the image of manufacturing in the minds of the future workforce. He announced our latest in-kind software grant to Mott Community College.
This was an interesting grant to work on. We’ve been having discussions with several schools on moving beyond just a CAD software focus and consider implementing more PLM training. We’ve seen this work successfully in places like Iowa Western Community College. As Mott was reviewing its program and industry demand they had sudden increase in data management training.
Dr. Richard Shaink, president of Mott, noted they are taking more of a systems approach to training at Mott to provide the technical talent pipeline needed by Michigan manufacturers.
Nigel Francis, Senior Vice President, Automotive Industry Office, State of Michigan, noted the state needs to be more “loud and proud” of the tech talent in Michigan, where he emphasized they are training “super technicians.”
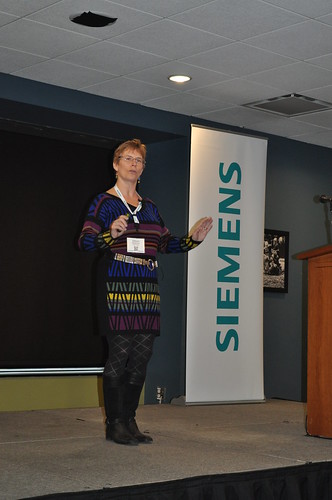
One of the customers who presented at our event in Detroit was ergonomics guru Allison Stephens of Ford. She shared with the audience that “what we are investing in is the right thing.” She shared how Ford uses software for ergonomics and planning the manufacturing jobs of the future in Ford plants. She noted how the “software becomes the communication tool.” Here is more of the story in Forbes: Ford Pilots a New Virtual Assembly Plant to Built its Cars. Greenfield also just published an article on Intosite: Ford uses Google Earth for Manufacturing Collaboration.
Last but not least was a panel discussion with Focus: Hope, Flint and Tinder, and Automation Alley. They provided three very diverse approaches to manufacturing in the U.S. Focus: Hope is a non-profit focused on manufacturing and education to end poverty. Flint and Tinder is an American manufactured clothing company. Automation Alley is a business accelerator in Southeast Michigan.
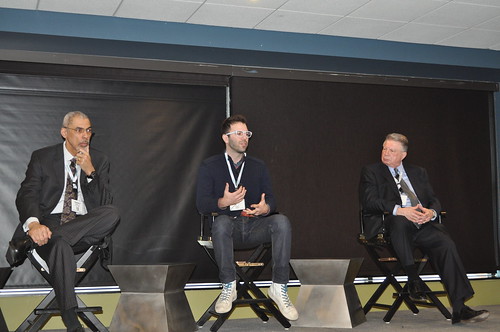
Automation Alley just released last week its Technology Industry Report. A few interesting stats:
- Tech industry employment in metro Detroit is up 15 percent (Silicon Valley shows a 4 percent drop).
- Schools in the metro Detroit region graduated more students in the areas of engineering and engineering technology than any other region in the study
- Michigan leads the nation in the advanced automotive industry, with a concentration of employment in metro Detroit that is 6 times the national average
Greenfield summarized our event in It’s not a Skills Gap. As the discussion above showed, if we get our software into the hands of the right community schools and train for specific “super technicians” or “technical rock star” rolls, the gap will narrow and this software revolution will result in jobs in Michigan and the U.S.
Stay tuned to the #SoftwareRev conversation and see where it takes us in April…
– Dora