Track quality and medical device compliance data with a digital framework
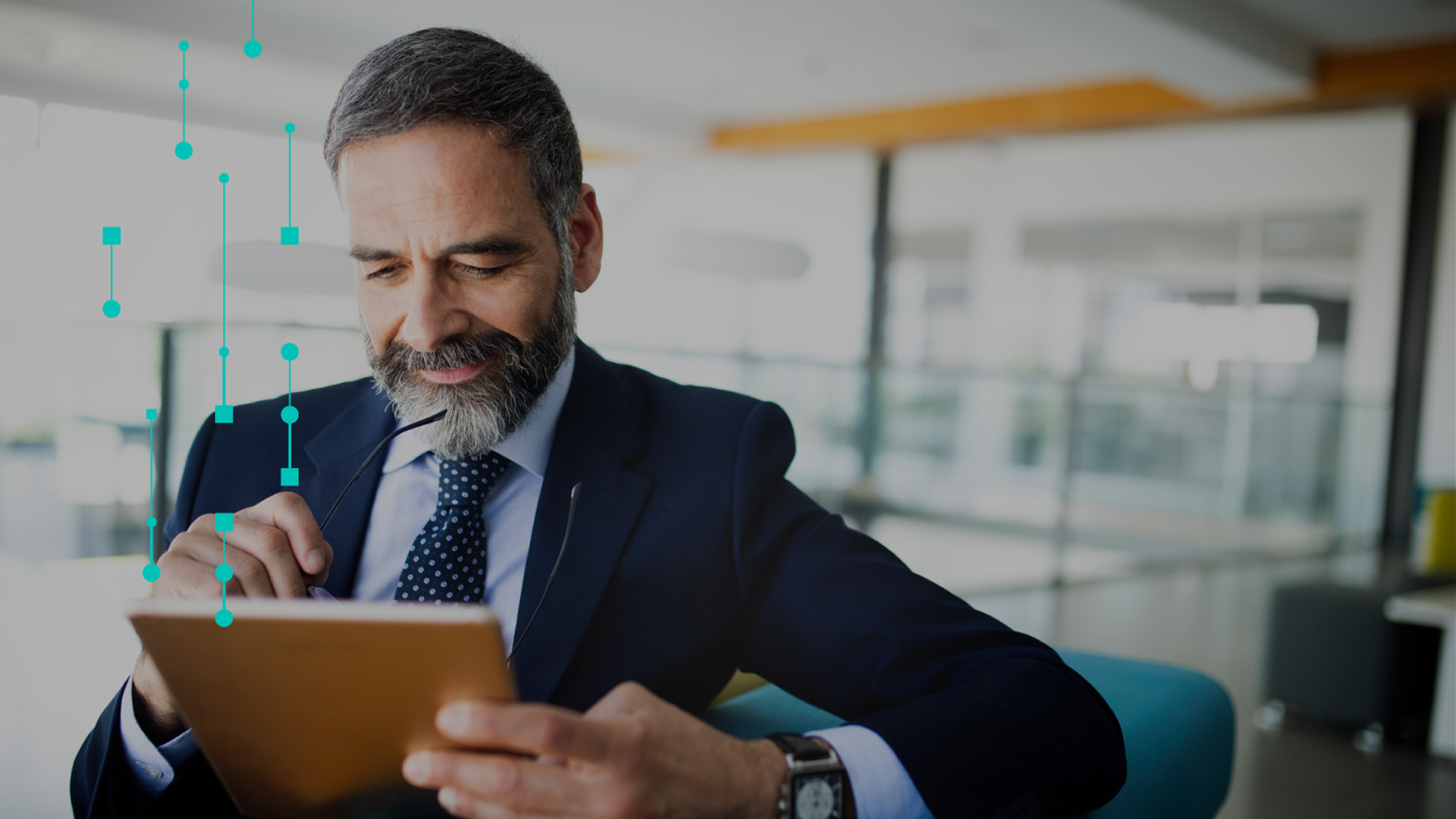
Between 2018 and 2022, over 13,000 medical devices were recalled in the United States alone.
As 90% of medical device manufacturers proactively promote quality and have a defined quality strategy across their companies, the focus ends up being more about reacting to product failures as opposed to its prevention.
Quality process issues continue to be a leading cause of recalls globally. A siloed approach will hinder the process and cause delays due to the time it takes to track down data. And who’s to say that data is the most accurate or up to date? This, in turn, can cause problems when proving the medical device meets region-specific regulations or, worse, be the reason a recall is ordered.
Digital tools that centralize quality data from all company departments are important for medical device compliance, as they can be used to continuously master and monitor compliance with regulations and procedures.
Data traceability tools to foster medical device compliance
To implement an integrated and collaborative digital backbone for data and documents, one that provides data traceability, centralizes quality data across departments and fosters collaboration, you’ll need a digital quality and compliance framework.
On top of that, consider the importance of tracking all quality data for products and processes. To do so, medical device manufacturers must implement a powerful, industry-specific tool as a digital backbone. This is where having a Product Lifecycle Management and Application Lifecycle Management tool in place will help ensure all activities related to design, development, manufacturing and post-market surveillance are planned, controlled and monitored. It also means that stakeholders will access the right data, when they need it.
Siemens Closed Loop Quality and Compliance solutions to meet medical device regulations
Our Closed Loop Quality and Compliance solutions address critical aspects of medical device quality and compliance and ensure that siloed teams will be more coordinated on quality activities, data and trace transparency. This enhances your opportunities to focus on a variety of medical device quality and compliance areas and functions, including:
- Design Data Management
- Product Line Management
- Quality Process Management
Let’s take a closer look at these three areas.
Design Data Management
Remotely distributed design teams can work together with a common set of tools and make full use of the digital twin and design inputs as model-based, traceable data. This enables visibility of parallel design activities for design evolution across domains, such as systems, mechanical, electrical and software, and empowers data to define, measure, analyze, improve and control bringing a product to market.
Product Line Management
Product line management enables identification, early creation and synchronization of accurate and structured product and manufacturing specifications, which includes suppliers.
Your teams can manage, change and manufacture product variations according to regional needs through visibility and integration across the entire value chain, which will ensure that medical device and SKU management is in line with global medical device regulations. This also provides lifecycle management of design history, submissions, labeling and Device Master Records with an integrated, industry-specific labeling and unique device identifier (UDI) tool.
Quality Process Management
Maintain a master system of record that is compatible with all discipline workflows and data trace, history and change control with quality process management solutions. Enable modular and discrete re-use of requirements, risk analysis and testing objects from similar designs. You’ll have the tools to enable you to:
- Establish design control platforms
- Map requirements to Verification & Validation (V&V) activities, including BOMs
- Integrate standards into the development process, with re-use from a document library
- Implement electronic change and document control workflows linked with master data
- Reduce errors through an electronic Corrective & Preventive Actions (CAPA) process
Unleash innovation with data traceability
Imagine stakeholders in the innovation of your product having the full capability to clearly view context and regulatory medical device compliance throughout the product and market lifecycle.
Siemens Closed Loop Quality and Compliance data traceability tools will help you enhance your digital transformation initiatives by automating a document and data flow that offers components unattainable through traditional paper processes. These tools empower users to coordinate multi-disciplinary teams, establish key performance indicators (KPIs) and ensure compliance with regulatory requirements.
Read the ebook to learn more about data traceability.