How to integrate simulation to enhance the medical device design process
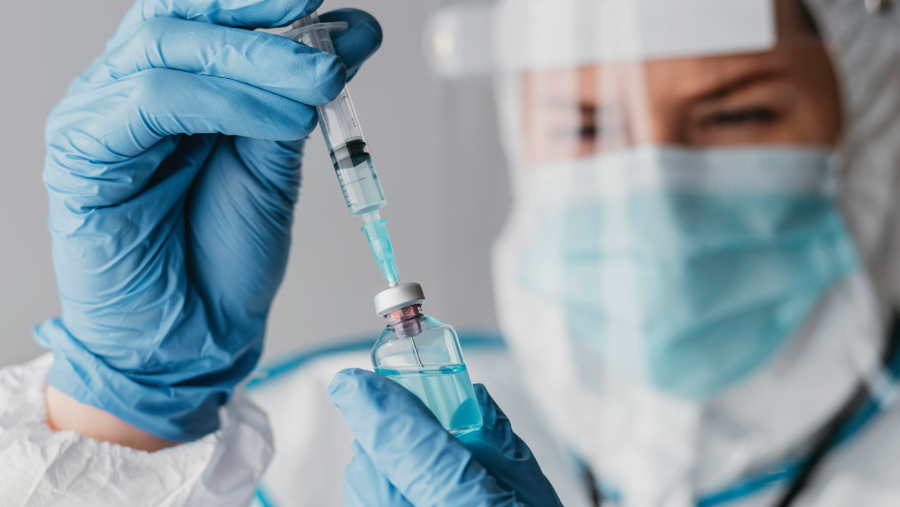
There is no doubt that every single person has been affected by the coronavirus disease since 2019 (COVID-19). Hospitals are swamped with patients. Stores were out of toilet paper for months. This pandemic is like nothing we have seen in our lifetime. Companies had to quickly pivot to start finding solutions to keep the public safe from COVID-19. Pharmaceutical companies jumped to developing new vaccines, while medical device companies started to create ventilators.
Today, medical device manufacturers are facing immense pressure to innovate rapidly and reduce costs of their devices. Because of COVID-19, the medical device industry, particularly the respiratory device sector, has had to adapt and evolve overnight. The global market for ventilators expanded, while elective surgical procedures were delayed indefinitely. Now, we are seeing rising recall rates in the industry, which are typically caused by design or software flaws. Manufacturers are noticing that traditional methods are not able to effectively solve the problem. Therefore, medical device manufacturers are turning to simulation to enhance their design process.
Industry challenges and how simulation can help
Unfortunately, the pandemic is not over, due to new variants and infection waves. With the rise in telemedicine and supply chain disruptions, the medical device industry must continuously adapt. In a fast-moving industry, the design and development process can be quite slow. Typically, effective testing for devices and medicine is not fast, due to the long duration of clinical trials. Not to mention, the cost of clinical trials is increasing. As a result, many medical device companies are turning to simulation to address their problems.
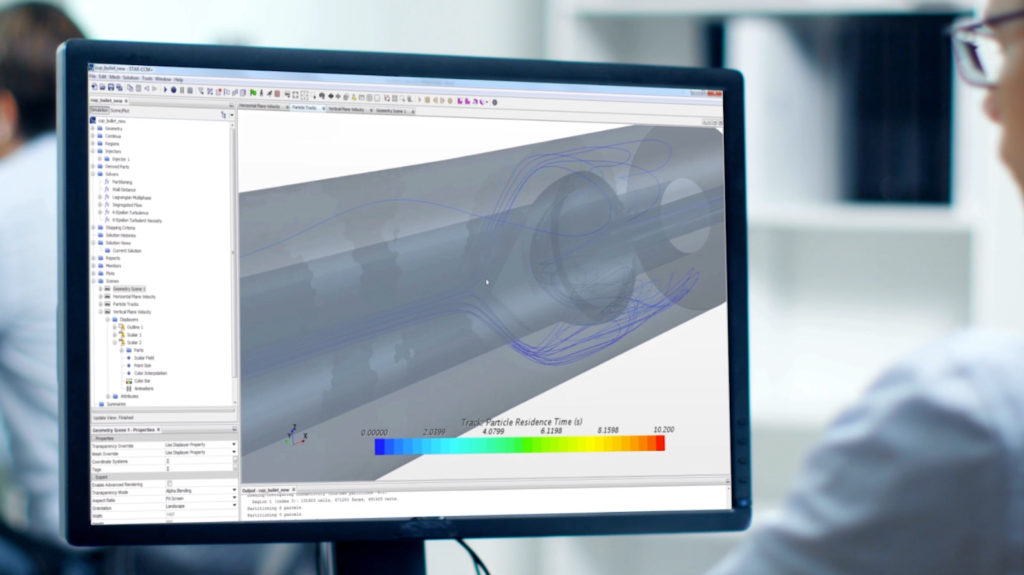
Currently, the medical device industry is behind other industries on adopting simulation. The main obstacle is a lack of trust in the models’ validity when people’s lives are at risk. However, the tide is turning. Design exploration with simulation enables rapid and thorough design optimization. This minimizes the risk of flaws and reduces development costs – allowing the device to be sold for less. Simulation can give manufacturers a distinct advantage over competitors who still use traditional design and testing methods. Virtual clinical trials allow the testing process to be accelerated with faster regulatory approval and innovation.
The benefits and capabilities of simulation
The use of simulation can enable more efficient design and testing to fight COVID-19. Simulation can test respiratory devices and effectively predict particle movement. This benefit allows for ventilation and COVID-19 contamination investigation.
Simulation gives companies greater power to find out what is possible. More possibilities and scenarios can be tested in a shorter period of time. Ineffective designs can be discarded earlier in the process. Different health conditions and body types can be considered when manufacturers do not have to use physical prototypes. Accurate models of the respiratory system can be used to investigate illnesses and evaluate the effects of treatment.
And how can all this happen through simulation? Let’s discuss the capabilities of simulation.
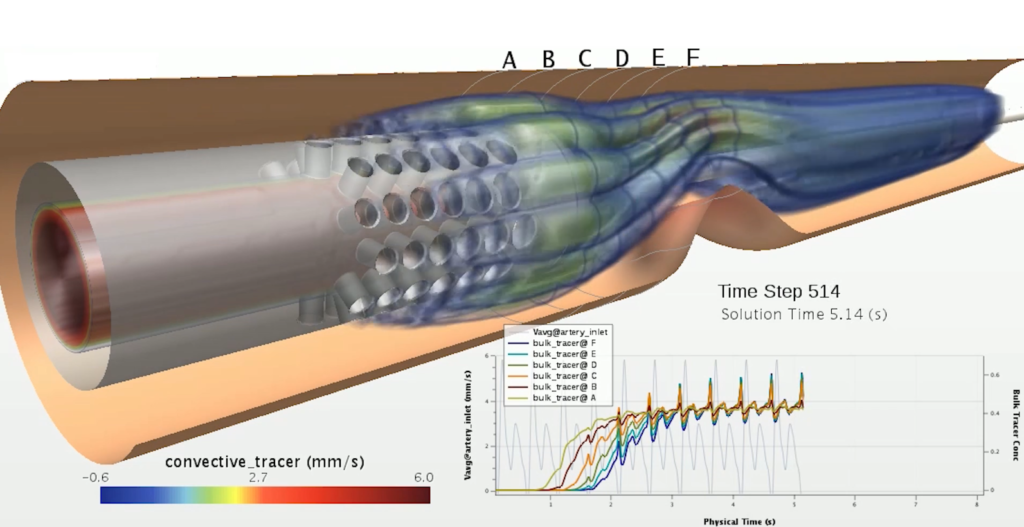
Simulation models can be created using computational fluid dynamics (CFD). CFD is the method for mathematically modeling a physical scenario that involves fluid flow. This results in a virtual solution for a physical phenomenon, which enables investigation of the scenario.
Our Simcenter™ software portfolio contains a large range of software packages to support innovation for designers, engineers and analysts. Simcenter enables complex scenario simulation, design exploration and testing capabilities.
- Simcenter Flovent™ software is used for predicting 3D airflow, heat transfer and contamination distribution in and around all building sizes with CFD.
- Simcenter STAR-CCM+™ software is used to perform more detailed analysis by including multiphysics in a single integrated environment.
- Simcenter FLOEFD™ software is a mechanical computer-aided design (MCAD) embedded CFD simulation tool that enables easy, rapid and accurate fluid flow and heat transfer analysis.
The future of the medical device industry
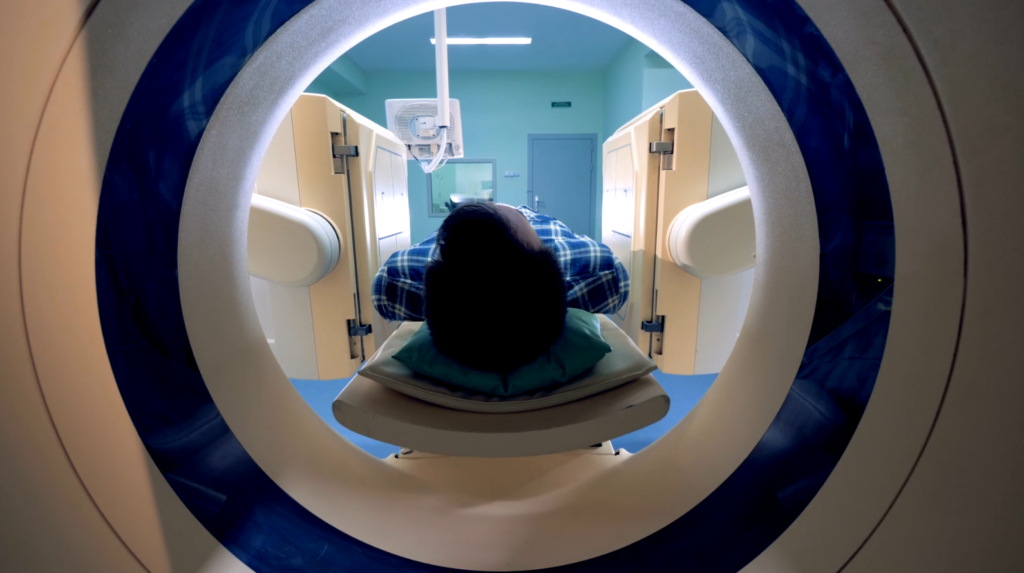
COVID-19 has irreversibly changed the face of health care and accelerated the move toward digitalization. Simulation is necessary to fight the virus and give medical device companies all the possibilities when it comes to testing products. The need for rapid and faultless decisions making in an industry where there is little room for error is heightened by the pandemic. The urgent nature of COVID-19 enhanced the severity of existing problems.
The FDA has identified simulation as a priority for the industry. The focus should be on clinical trial reduction by using in silico clinical trials. In the future, the FDA is looking for evidence to be more targeted with less reliance on animal and human tests. The use of virtual evidence will help speed up the design and testing process. Simulation has the potential to produce better designs and solve problems.
Interested in other blogs about the medical device industry? Explore more here.