Overcome the top medtech manufacturing challenges with integrated MES
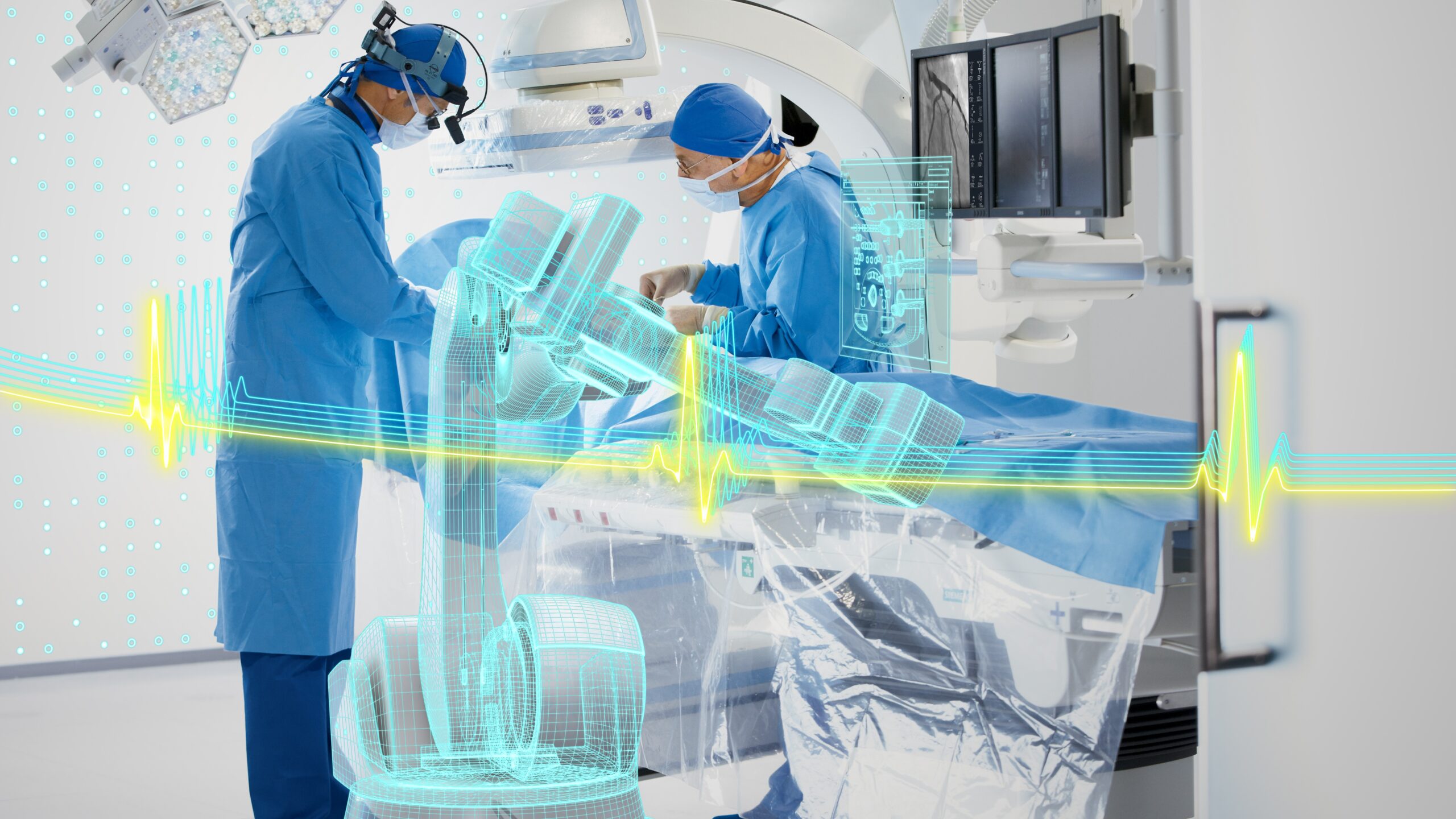
Why integrated MES is important
The medical device and diagnostics (MD&D) industry is a complex environment with ever-changing standards and disruptive events. To mitigate these disruptions, integrated manufacturing execution systems (MES) are the key to integrating the virtual world of design and engineering with the physical world of production.
The list of changing market conditions and trends is never-ending:
- Internet of Medical Things (IoMT)
- Personalized medicine
- Value-based care
- Real-world evidence models
- Demographic differences across regional economies
- Implications of treating chronic diseases
- European Union Medical Device Regulations (EU MDR)
Investing in MES is one of the most important technology enablers for accelerating high-quality innovation in the medical technology industry. With so many technologies available, manufacturers may have difficulties navigating and implementing these tools.
Top six challenges in the medtech industry
Let’s dive into the top six manufacturing challenges that medical device companies face and how to overcome them.
1. Accelerated product innovation
With new technologies reshaping the industry, more competition and complexity will emerge in the form of connected devices, wearable technology and device-as-a-service. Small and medium businesses (SMB) and startups will become larger competitors in the market. Medical device manufacturers must respond with increased speed-to-market, lower cost of production and better product performance.
Efficiency is key – both in operations and capital. Integrated MES can speed up new product innovation by creating a closed-loop manufacturing process to produce a collaborative environment. In addition, using MES ensures quality enforcement, feeds simulation and prevents human error.
2. Intelligent data analytics
Big data can be a big problem if medical device manufacturers cannot analyze and understand its impact on quality and cost. Manufacturers must shift from managing paper documents in siloed systems to using metrics that come from the value chain. Providing visibility and access to these metrics across the entire business will allow for more contextualized data and better performance.
It’s time to standardize data across the enterprise. With various systems and data formats, creating and maintaining consistency in the analysis of product performance and operational information is essential. MES is central to creating intelligent data analytics. Using MES standardizes manufacturing operations data with automation and helps to shift to enterprise-wide metrics management.
3. Mass customization and 3D printing
Personalization of medical devices is growing, and so is manufacturing complexity. Engineering, modeling and simulation will more closely integrate with manufacturing production to create personalized medicine. Manufacturers must adopt additive manufacturing and 3D printing to support mass customization and lower manufacturing costs. Multiple 3D printers or printing systems will be required to maximize cost and time efficiency.
MES can support 3D printer usage, such as printing products from different work orders at the same time. Using MES coordinates 3S printing systems, executes customer orders, controls machines and materials and provides cost visibility.
4. Market consolidation and technology partnerships
Mergers and acquisitions are not new in the medical device industry. Large companies often use these strategies to dominate a certain market or product portfolio. However, bringing together multiple companies can be challenging and lead to disparate systems. Not only that, but different organizations also have different cultures and communications. Manufacturers must leverage technology to support a common digital system to foster better cooperation.
Establishing strategic partnerships with high tech companies can enable more innovation and the ability to bring new devices to market. Using MES with mergers and acquisitions can help coordinate manufacturing operations, collaboration, visibility and analytics across the entire partner ecosystem.
5. Restrictive regulatory environment with global differences
Regulatory standards are still a constraint on the medical device industry. With new regulations, such as EU MDR, companies find it difficult to manage inquiries and quality inspections, while product recalls are increasing. Manufacturers must collect data throughout the entire product lifecycle and understand notified bodies’ quality metrics guidance.
To focus on product quality and compliance, MES can automatically control the manufacturing environment while simultaneously collecting data. Opportunities for error and failures are dramatically reduced, and managing inspections become more simplified. Using MES allows regulatory inspections to be easily managed and supports FDA and EU MDR requirements.
6. Value-based care and healthcare cost pressure
Value-based care is putting patient health and outcomes are the forefront of the industry. In a value-based model, payment is based on the patient outcome rather than the amounts of services provided. This means there is a growing need for cost-efficient medical devices. Manufacturers must implement outcome-based models and focus on creating devices that improve patient health rather than just performing as intended.
MES helps to drive cost efficiency in production. Using MES can help control costs, ensure quality and support flexibility across production.
Considering the challenges and trends emerging in the medical device industry, it is clear that operating without MES is not an option.
Learn more about enabling smart manufacturing with integrated MES. Read our e-book.