Turn your brown to green: connect brownfield assets with the IoT
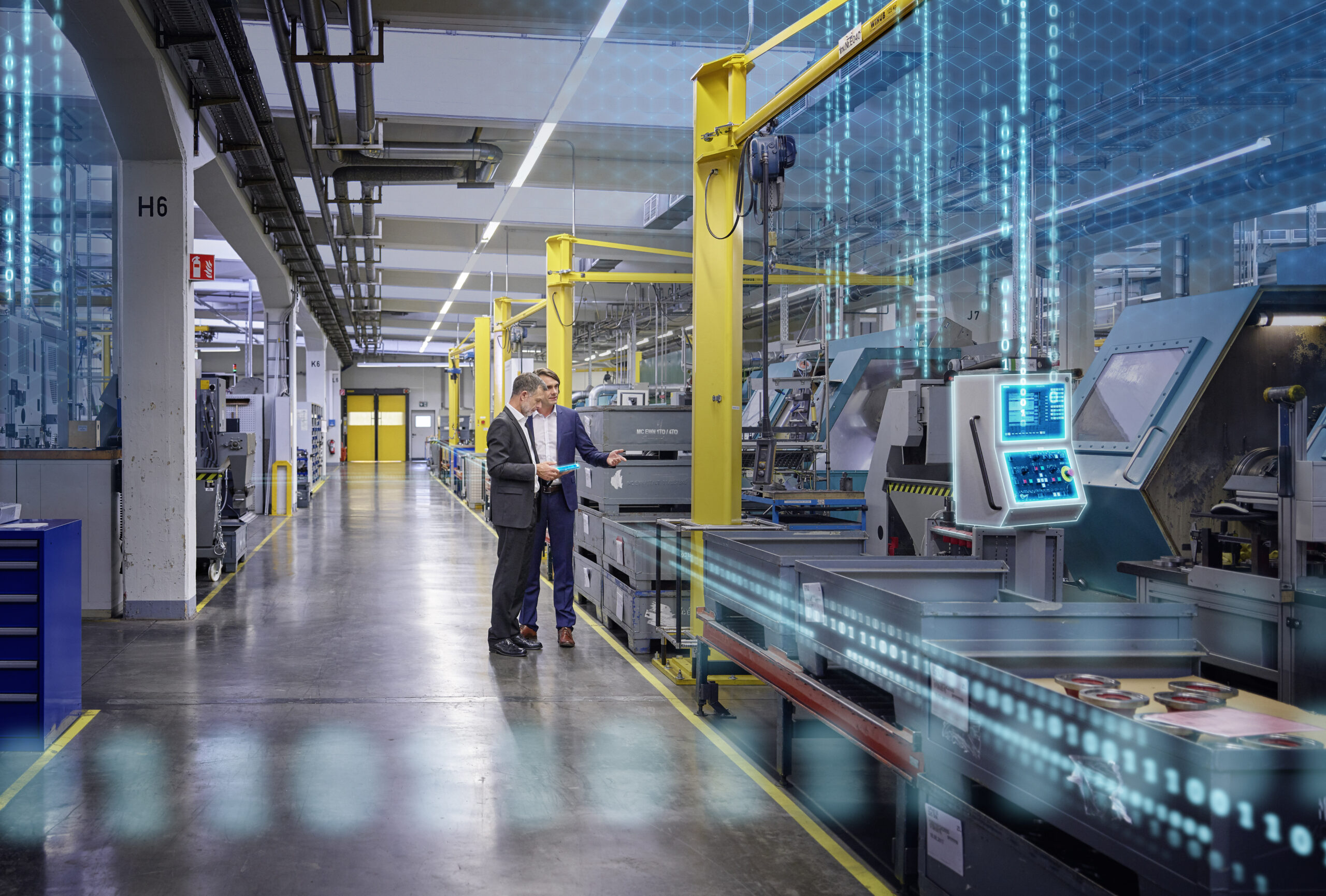
Connecting your older or disparate equipment to the industrial Internet of Things (IoT) might seem like a pipedream. But digitalizing your brownfield environment is possible, and it may be easier than you imagined. As the industrial IoT continues to evolve to face today’s challenges, there are new solutions for retrofitting older equipment with sensors to be IoT-ready. Now you can connect your systems and gain endless possibilities for data analytics, discover new sources of income, and implement cost-saving solutions for resource and time management.
Digitalization made possible for brownfield assets
Brownfield environments come with their own unique challenges to reaching digitalization. For example, siloed machine data, mismatched machine types and protocols, and legacy equipment are among the common issues found in older factories. But the industrial IoT now has proven solutions to get your legacy systems connected.
Have older assets without sensors? Not a problem! It’s now possible to install sensors on existing assets without sensors – or on assets that need more sensors. And, the cost of sensors has declined, making it even more accessible for factories to upgrade.
Curious to see how digitalization has worked for other brownfield environments? Let’s take a look at Siemens Guadalajara, a factory that recently upgraded their systems with industrial IoT solutions from Siemens.
Getting brownfield assets at Siemens Guadalajara connected
Siemens Guadalajara is a manufacturer of low-voltage NEMA motors. When they embarked on their digitalization journey, they faced many challenges: machines operating in isolation, no shared data or visibility into the machines, lack of ability to adjust or modify machines remotely, and the time consuming and complex extraction of generations of historical data.
Because the machines were not connected to the network, machine equipment performance measurements such as production time, machine availability and quality losses were compiled manually. In addition, the lack of connectivity made generating historical data complicated. Manual calculations were used to estimate data, leading to less than accurate performance measurements.
When upgrading their systems, the plant leadership and the engineers wanted to prioritize implementing automated calculations and dashboards to allow them to access their data and so that they could make decisions quickly and assertively. The dashboards would give them accurate information coming directly from the machines and they could then use this data to increase equipment availability and usage.
By implementing Insights Hub connectivity solutions, Siemens Guadalajara established communication between the production network and cloud, making it possible to connect machines to Insights Hub without modifying the configurations of the machines. The plant established connectivity between machines and installed human-machine interfaces to collect and calculate data. In addition, the Guadalajara plant created dashboards to monitor consumption of energy resources like electricity and gas in real time.
Within months of installing the solutions, they saw a 20% increase in efficiency and a 5% maintenance performance improvement. Now, the Siemens Guadalajara factory is planning to connect more machines to Insights Hub.
A deeper dive into digitalizing your brownfield assets
Looking for more information on the variety of apps and tools available for your brownfield factory? Check out our connectivity guide, “Connecting brownfield facilities,” for detailed information on available solutions.