A new approach to service: Service lifecycle analytics for machine builders and OEMs
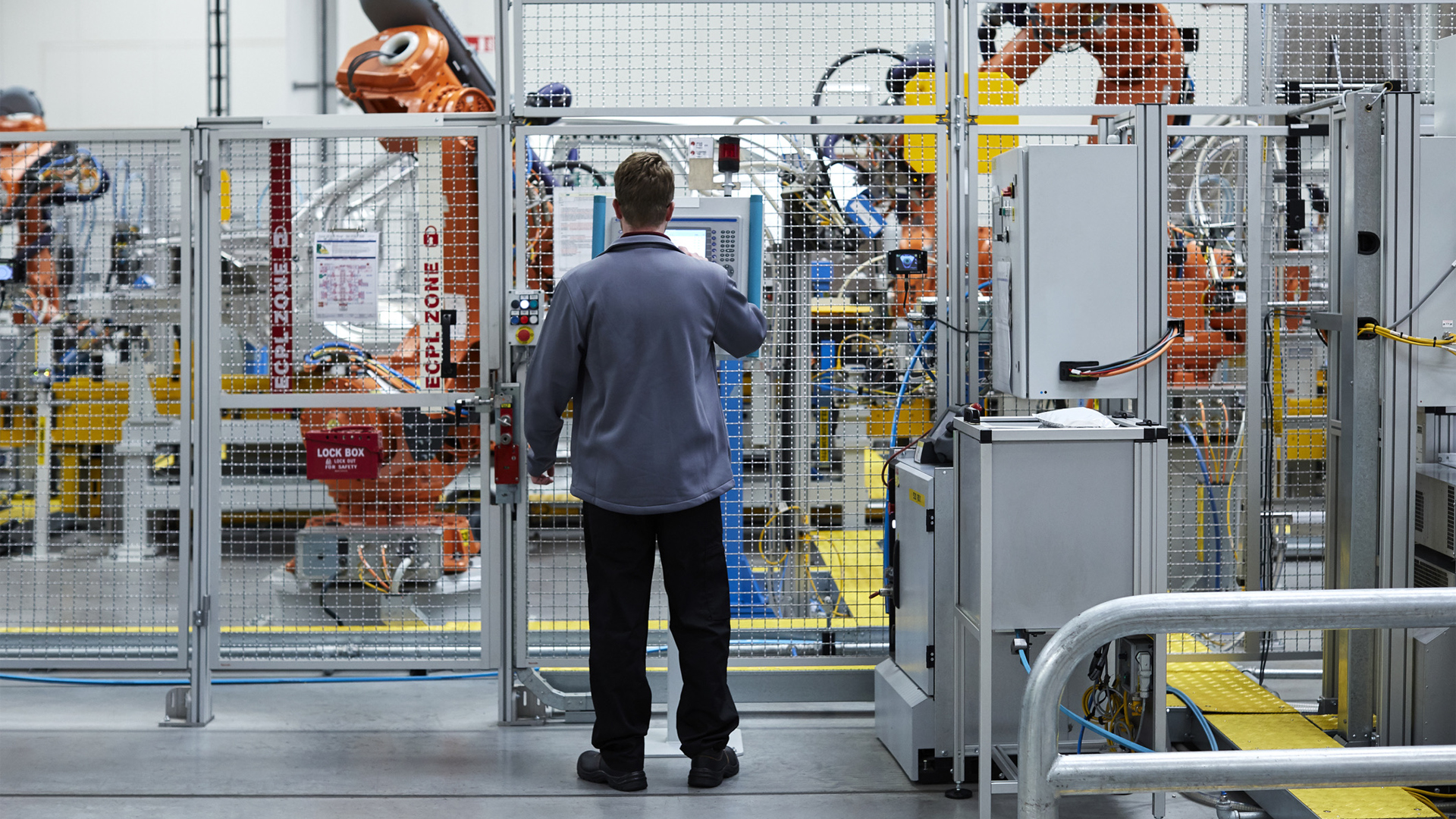
Industrial machine builders, suppliers and OEMs are leaving money on the table. There’s an untapped stream of revenue once the machine is delivered, installed and commissioned. The revenue we’re talking about is service, and service lifecycle analytics solutions make it easier.
Traditionally, once a machine is no longer under warranty, the customer is responsible for maintenance and service. However, as machines have become more complex, it’s more difficult for manufacturers to quickly identify and fix complex issues when machines aren’t performing. The resulting downtime grows longer and quickly becomes unaffordable.
With a more robust view of after-sale offerings, you – the expert – can be there for your customers in their time of need.
By establishing yourself as a reliable service partner for the entire lifecycle of your products, you cultivate the sort of esteem that leads to repeat business and an industry reputation as a manufacturer’s answer to any machine question.
Beyond the immediate injection of new revenue service offerings provided, machine builders and OEMs can secure long-term product excellence by maintaining hands-on experience with their machines throughout their time in the field. The streamlined observation of and feedback from machines, as they mature, provides important machine data and delivers priceless new insights needed to make the next generation of machines even better in the future.
Manifesting these new service capabilities a reality is made easier with service lifecycle analytics solutions from Siemens. This integrated service platform comprises of three main principles as navigational beacons, making the journey to service excellence – and the rewards that come with it – a straight shot. The infographic below shows what’s possible with the current machine industry trends and service lifecycle analytics’ three main principles: plan for service, service delivery and closed-loop service.
Planning for service with service lifecycle analytics
The journey to comprehensive service excellence begins with integrating key service considerations early on. By addressing service needs within the design phase, you can better control and predict the timelines surrounding how, when and where machines will be serviced.
This proactive pillar of service lifecycle analytics will improve machine maintainability, minimize the impact of unplanned downtime and accelerate manual and technical publication creation.
Plan for service focuses on building a comprehensive digital twin for service to provide end-to-end visibility of a machine’s complete lifespan. This ensures service technicians have current product configuration knowledge combined with customer knowledge to ensure superior service.
Service delivery with service lifecycle analytics
Now that processes are set and maintenance schedules are planned, service delivery solutions ensure high-quality repairs, maintenance, upgrades and more.
Digital solutions that supply technicians with the most accurate and up-to-date machine documentation and servicing history make sure the job gets done right the first time. Technicians armed with the right digital tools can make quick assessments and diagnoses before recommending solutions – and much of this can even be done remotely.
AR, VR and MR tools can also help machine service technicians identify what parts of a machine need to be fixed using digital twin visualizations. Virtual projections onto an operating machine can make it easier for technicians to complete service the first time.
Closed-loop service with service lifecycle analytics
The last part of service lifecycle analytics focuses on the return leg of the service excellence equation. Service-focused machine builders have already integrated service planning into the design to improve maintainability, traceability and predictability. And service delivery ensures accurate documentation and communication processes to enhance field service of existing equipment.
Closed-loop service gives engineers new insights into design changes for future machines. These insights are gathered from machine analytics collected by IIoT sensors and edge devices and combined with service data.
All of this feeds continuous improvements into the machine design and support processes. Unlocking crucial information leads to better, more serviceable and sustainable machines.
Conclusion
The opportunity to acquire a new and reliable revenue stream is there for the taking. With after-sale service, machine builders and OEMs can create deeper relationships with customers and get direct access to performance insights, paving the way for more innovative, higher-performing machines with a longer life.
With service lifecycle analytics and its planning for service, service delivery and closed-loop service pillars, machine builders and OEMs can diversify their revenue streams to position themselves capably no matter the industry conditions.