CFD modeling in catalytic reactors: Historical developments through future innovations
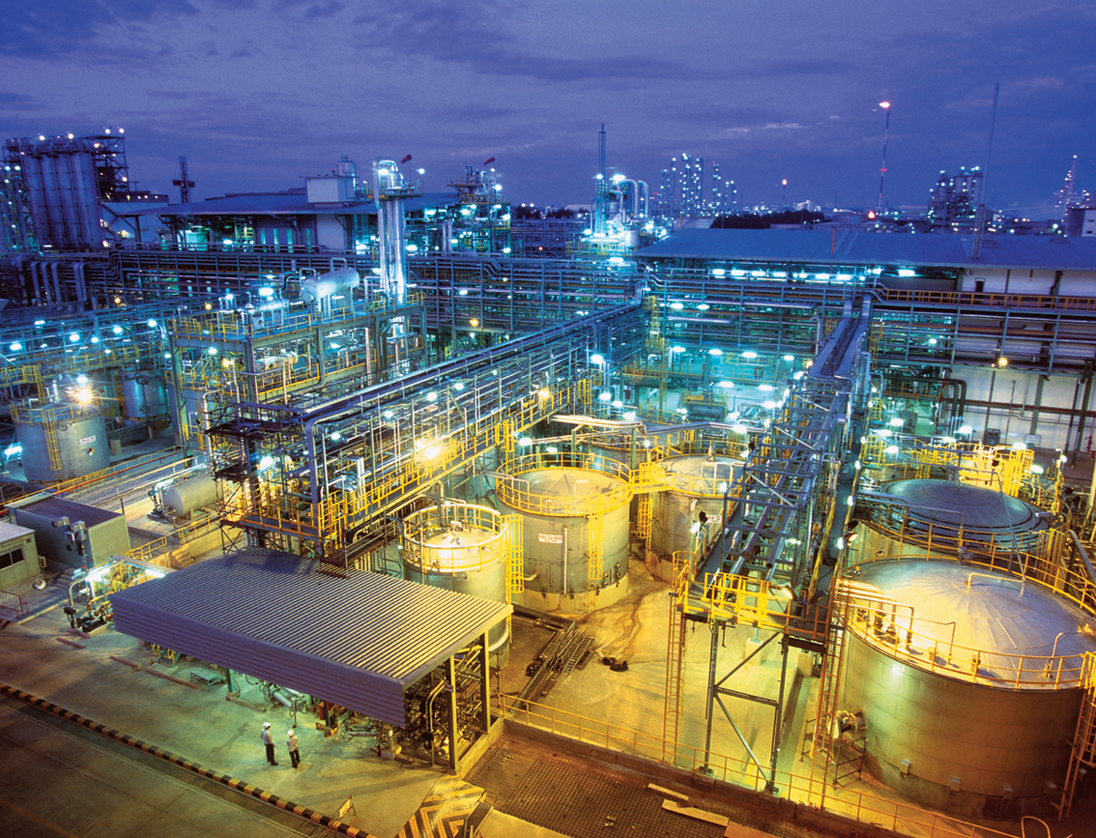
Catalytic packed-bed reactors are critical components in the chemical and process industry. These workhorses impact approximately 80 to 90% of all heterogeneous catalysis processes within chemical production alone.
Despite their robustness and longevity, catalytic packed-bed reactors are complex to design, their behavior is difficult to understand, and they’re challenging to operate in a controlled manner. Improving understanding of these reactors is crucial to helping the chemical and process industry play a leading role in solving the world’s toughest challenges.
In Siemens’ recent webinar (now available on-demand), two distinguished chemical and process industry experts presented an overview of the past, present and future of the particle-resolved computational fluid dynamics (CFD) approach towards modeling catalytic reactors. Scroll down for webinar highlights and discover how advanced CFD modeling and simulation provide new insights that can help engineers optimize reactor performance and sustainability.
To improve catalytic reactor understanding, engineering simulation software is crucial
Because of their importance in manufacturing all types of chemicals in small to large quantities, catalytic reactors have been investigated by the chemical industry and academia for decades.
As webinar presenter Dr Ravindra Aglave discussed below, a key research area for improving reactor knowledge is gaining a better understanding of process length-scales and time-scales. Analyzing and validating reactor models using engineering simulation software is expected to help establish this knowledge.
Particle-resolved CFD simulation has played a promising role in providing reactor insights
Fixed bed reactors, a catalytic reactor type, require detailed computational fluid dynamics (CFD) simulations to understand their behavior. These simulations are crucial for packed beds, where the arrangement of catalyst pellets significantly affects performance.
As highlighted in this clip by webinar presenter Prof. Gregor Wehinger, utilizing particle-resolved CFD simulation in catalytic reactor design has shown promising results in recent decades. It often matches experimental outcomes while providing new insights into reactor behavior.
Chemical businesses can generate realistic packed bed structures using Simcenter STAR-CCM+ CFD software
To create realistic packed-bed structures, Dr Wehinger’s team developed a fully automatic procedure that can be completed using Simcenter Star-CCM+ CFD software. The procedure enables bed structure or section generation that can be incorporated into the CFD pipeline and shared with other chemical engineers to discuss results.
Watch the clip to learn about the workflow, which also enables the generation of non-spherical particles and high beds larger than 10 meters.
Emerging research includes multiscale transport, combining CFD with virtual reality and AI
Technological advancements are transforming catalytic reactor research, with emerging focus areas including multiscale transport phenomena in porous catalysts, combining CFD with virtual reality, and testing artificial intelligence (AI).
Watch the clip to hear Dr Wehinger discuss cutting-edge research trends and areas where breakthroughs could happen.
Ready to learn more about CFD modeling for catalytic reactors?
Catalytic-packed bed reactors are indispensable to the chemical and processing industry, and CFD modeling advancements are crucial for helping optimize reactor performance.
To learn more about the past, present and future of CFD modeling for catalytic reactors, watch our on-demand webinar.