How a top manufacturer reduced cycle times by 84% with PLM
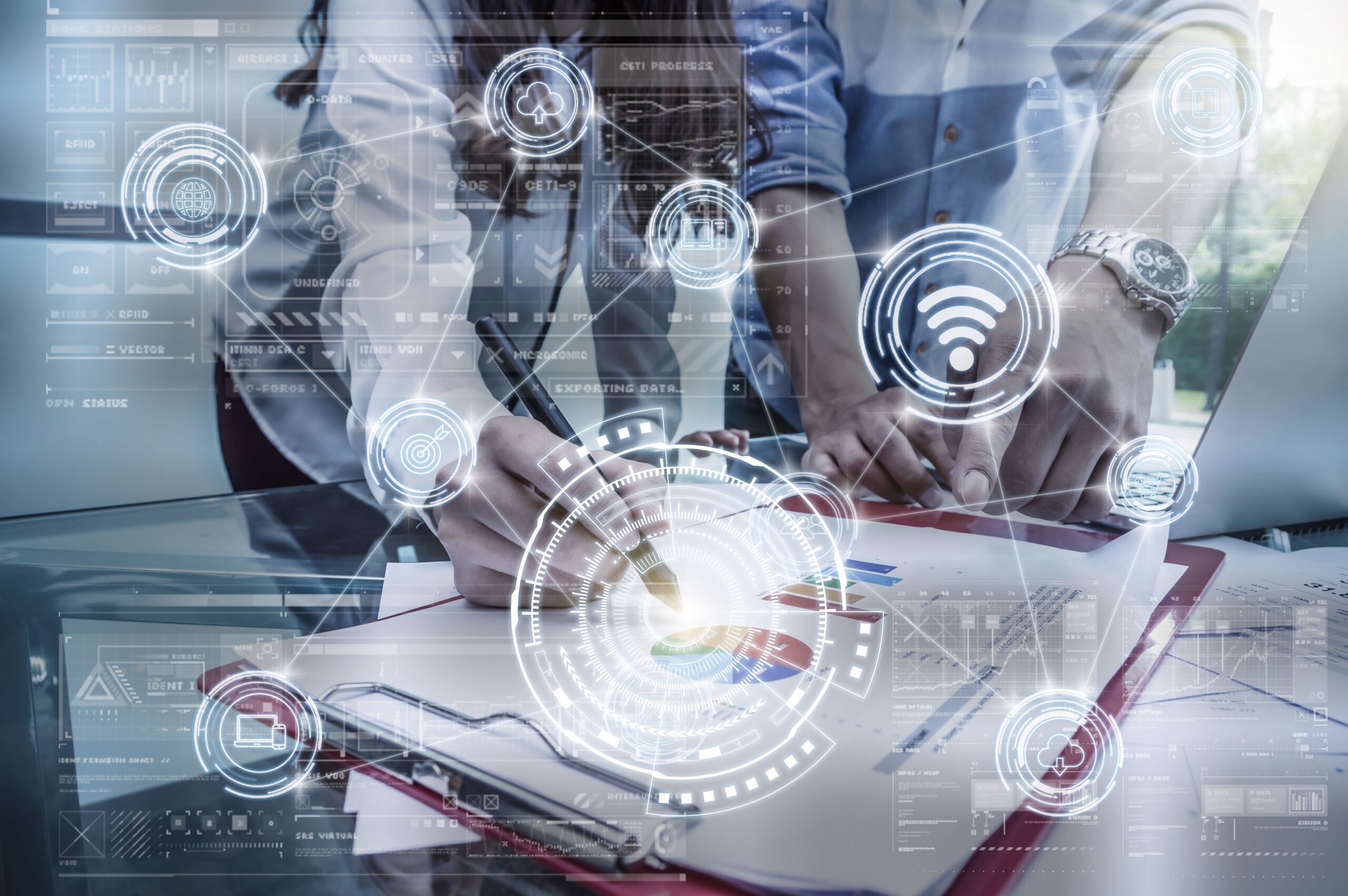
Electronics testing equipment manufacturers must manage frequent engineering change orders. The process is often further complicated by being geographically dispersed across a complex worldwide supply chain.
Is it possible to streamline this process and reduce change order cycle times? Yes. Customers adopting product lifecycle management for engineering change management have seen reduced cycle times from 90 days to just 14 days—an 84% reduction!
Inefficiencies impact more than change orders
Not only do inefficient engineering change order processes impact cycle time, but they can also significantly impact company performance. When parts are ordered from a bill of materials after a change order is submitted but prior to processing, companies face additional scrap and rework costs.
Similarly, with manual management of product requirements, the requirement changes may not be implemented timely and could lead to reworking a manufacturing process which may cause project schedules and customer deliveries to slip by months or more. This results in higher costs and lower customer satisfaction.
Less-than-timely engineering and requirement change orders snowball into larger, costly problems for manufacturers.
Where to even begin with implementing changing these processes?
Reviewing product lifecycle management
Looking inside existing processes that may be different across business units, enables manufacturers to gain insights into areas for optimization and streamlining. By looking at engineering requirements and change management processes, other processes are impacted positively, creating improvement throughout the organization.
Smaller companies may not encounter issues in these processes where co-located teams could rely on informal communication to collaborate and expedite change orders. For larger companies or those made up of multiple business units operating as one, informal communication doesn’t work as effectively or may not be available. Teams would lean on the strengths of individual members, using tools such as intranet sites or Notes software with workflows while others may use paper files. Different systems and storage locations meant documentation and project information would be difficult to find, especially if working on multiple projects across teams.
Committing to a single technology solution
Replace processes hindering engineering and manufacturing performance with a technology solution that dispersed teams have easy access to. Pulling together solution evaluation teams from across the company will develop the best set of requirements when reviewing available systems. Teams should look for systems that have high reliability and capabilities for requirements management, bill of materials management, and engineering change management. By including these business units, companies and teams can quickly see changes made by any of the other business units, cutting costs and time caused by manual delays and system integrations.
Implementing a solution with grass-roots support
Rather than implement a full suite of product lifecycle management capabilities at once, companies often opt for a phased-in approach. By slowly integrating the solution, teams can adopt the solution and then advocate for its effectiveness to others, gaining support and momentum in implementation. By building grass-roots support from the functionally and geographically diverse personnel who work with it, it also allows for the opportunity to fine-tune each aspect of deployment before moving on to the next.
Multiple workflows and databases are integrated into a single workflow and database that made part information consistent and easily accessible. All information on project requirements, parts, specifications, engineering changes, bills of materials, and engineering documentation is centralized in and managed via a single solution, accessible to anyone in the company.
Read the customer story
How does a leading test equipment manufacturer significantly reduce its engineering change order cycle? To answer this question and shed more light on this topic, read the Teradyne customer story. They reduced their engineering change order cycle by 84%, resulting in $2 million saved yearly. Learn more about Teradyne’s implementation of a centralized, automated process for engineering change management and collaboration with PLM below.