Stop throwing designs over the wall – bridge the electronic and mechanical design divide
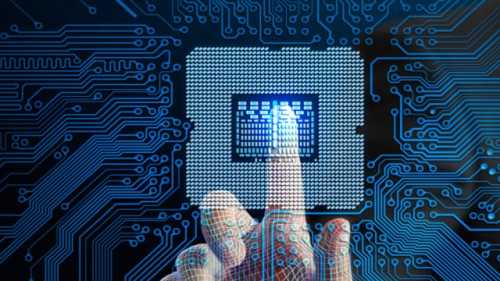
Stop to think for just a minute – how well do your electronic and mechanical teams collaborate? Is it a cohesive process? Is it iterative? What’s the process for sharing design files? How long do design changes take? When can you start prototyping? Is there room for improvement?
With that exercise in mind, let’s compare two teams:
- Team A’s mechanical design group uses its design tools and data to prepare the mechanical design. Once complete, they toss it over the wall via email or some other manual method to the electronics design team. The electronics team then builds out the electronics side of the design, discovering some issues with the compatibility of the mechanical design while placing components. The design goes back over the wall to the mechanical team, creating design iterations and wasting time. At some point, the design is mature enough for software to get started.
- Team B’s mechanical and electronics teams work on the product’s design concurrently with a shared dataset and the ability to view the other up-to-date design at any time. The software design team can leverage digital prototypes that accurately represent the product at nearly any time, enabling them to start software design much earlier. Concurrent and collaborative design results in a shorter time-to-market, fewer errors that need correction later in the design process and enables better product innovation.
I’d prefer to work in Team B. Yet, in today’s connected world, you would expect companies to have overcome the long-standing collaboration challenges that electromechanical designers often face. The reality is that most development teams still struggle and rely on manual methods, such as emails and exchanging files, to overcome even the most straightforward tasks.
Benefits of a common, unified view of MCAD-ECAD design data
When design engineers can spend less time searching for information, they’ll have more time to create innovative and disruptive products. A unified MCAD and ECAD software view into design data and an optimized design process reduce design errors and rework for a more efficient and speedier design flow.
In addition, a common parts library for ECAD and MCAD software mitigates organizational complexity. Single item representations of part footprints, symbol and attributes reduces the need for duplicate data entry and ensures design teams are working from the same reference point. It also enables multi-directional collaboration to adapt to internal workflows for synchronous or asynchronous use.
Optimize designs for performance and design for manufacturing
When teams have a speedier, collaborative process, optimizing designs for performance and manufacturing (DFM) becomes a reality. Teams can integrate a shift-left approach for design intent analysis and validation throughout the development process. This approach ensures zero-spin products and provides comprehensive visibility to product development across multiple domains.
Watch this webinar to learn how to bring more complex products to market by reducing design iterations with cross-domain collaboration, increasing visibility using a common view of design data and validating designs in the virtual domain instead of waiting for physical prototypes.