Keep complex routing projects on track with routing automation
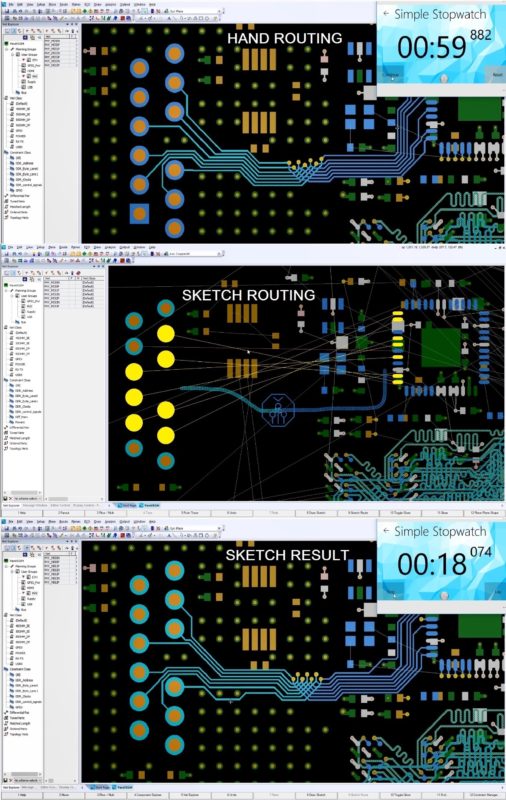
PCB design is typically the last step in the development of an electronic product. As such, what was a well thought out schedule for each phase of the design results in the PCB layout time line usually being cut by 25 to 50% to address design challenges encountered during other phases of the product design cycle. One of the techniques historically used to reduce PCB design time is autorouting. Historically autorouters have been thought of as difficult to setup, requires lots of clean up, and requires very extensive rules.
With today’s modern PCB design tools a new style of autorouting has been introduced called sketch routing. This routing technology allows you to select a specific group of nets (1 to N) between 2 components and draw a simple sketch path in the general location where you’d like the nets to be routed. If needed, while drawing your sketch path, layer transitions can be added with multiple options for via patterns. After-which, the autorouter will take over and do the rest. Sketch routing gives a designer with no experience with autorouting the power to start using this technology with confidence. This technology can reduce routing time up to 70%, when used with automated fan-out for signal, power, and ground nets you’re looking at closer to 80% in routing time reduction. Why is sketch routing so powerful? It allows you to experiment with part placement, verify design rules, and complete designs faster. Figure 1 shows what it looks like to sketch a set of nets along with a comparison of the same nets sketch routed and hand routed. You can quickly see how this technology should be adopted by everyone designing a PCB.
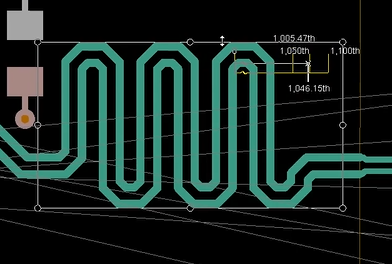
With sketch routing giving us the automation to create traces the next level is length matching traces for those designing circuits where timing is critical. There are 2 types of length matching available today to reduce that which is historically a very time consuming and tedious task. Interactive tuning gives you the ability to automatically add a tuning feature and then adjust as needed to provide the proper length via real-time feedback. The next level is using full automation, very much like sketch routing, to tune a group of nets. Auto-tuning can be done for 1 or any number of nets a time. By using intelligent selection methods, like groups created from your design rules, we can quickly select a group and then tune. To provide feedback for multiple nets being matched a spreadsheet view of all the nets and there length information should be provided. If for some reason the nets don’t tune – like spacing constraints – the process is so fast you can simply adjust the trace area and re-tune to complete all nets.
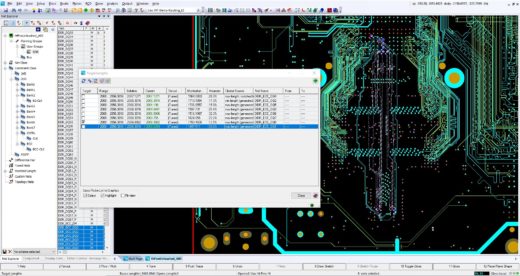