3 knowledge retention strategies for Aerospace and Defense development teams
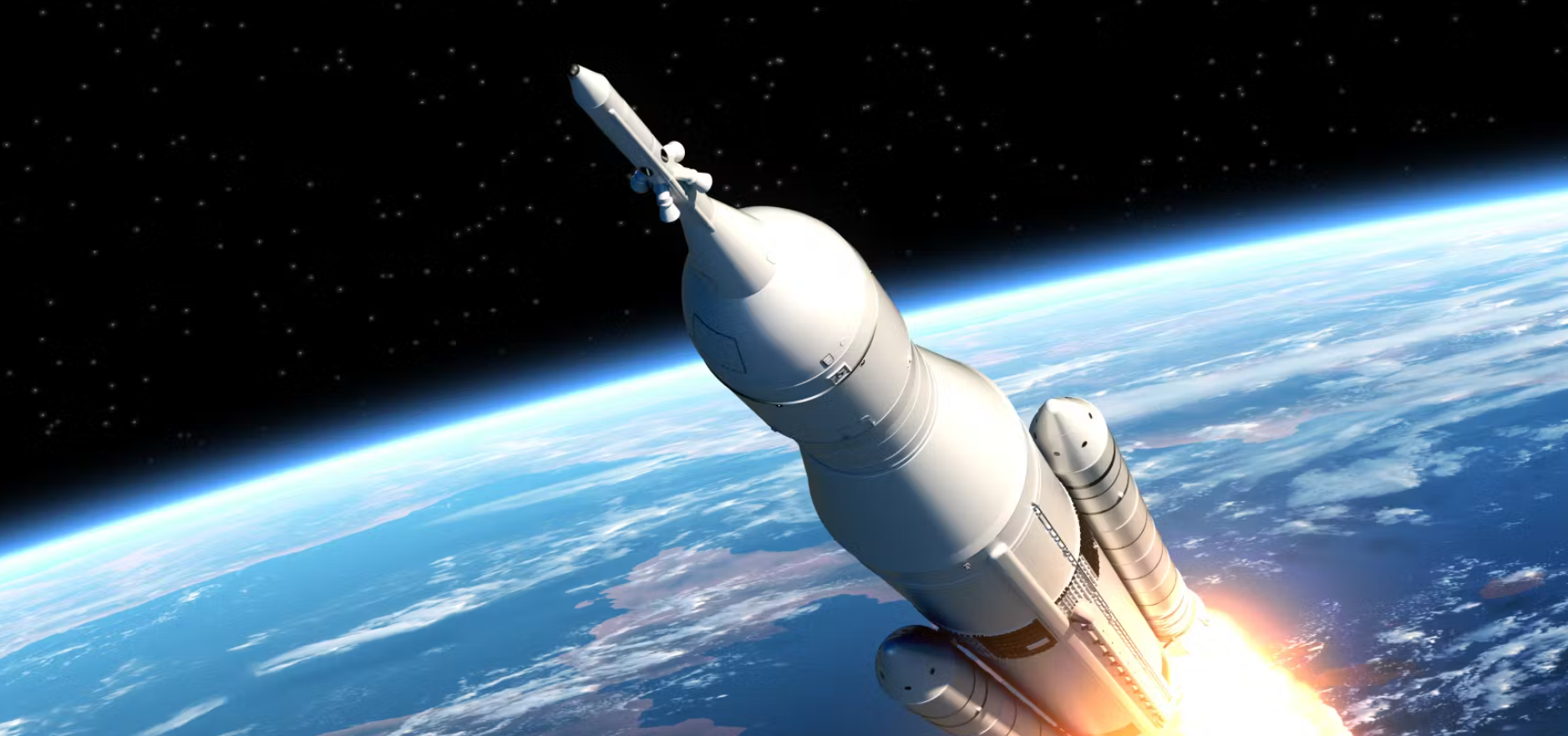
For many aerospace and defense (A&D) organizations, knowledge loss is a big problem. Knowledge retention strategies for Aerospace are few and far between. In fact, according to IDC, Fortune 500 companies lose at least $31.5 billion annually by failing to share knowledge. Retaining knowledge is critical for engineering teams working on complex systems, as it supports consistency and helps to prevent costly mistakes that can impact product quality.
What causes knowledge loss? Some of the most common causes include:
- Employee turnover and retirement: Engineers may leave a company or retire, and take their knowledge and expertise with them.
- Poor documentation: If important information, such as design decisions, implementation details or lessons learned is not properly documented, it becomes challenging for new team members to understand and build upon existing knowledge.
- Company culture: In some organizations, knowledge sharing is not encouraged or prioritized. When team members don’t actively share their knowledge with others, it remains siloed and is at risk of being lost when individuals leave or are unavailable.
- Communication breakdown: Effective collaboration and open communication channels are crucial for knowledge sharing within engineering teams. When team members may work in isolation, it hinders the exchange of knowledge and prevents the team from benefiting from diverse perspectives and experiences.
Addressing these sources of knowledge loss is essential for keeping engineering teams productive. Access to knowledge about proprietary technologies, products and processes enhances efficiency, reducing development time and costs. And, when teams can leverage retained knowledge to learn from past mistakes and successes, they don’t have to spend time getting up to speed – instead, they can add their own innovative ideas to take products further.
What can be done to prevent knowledge loss?
While some knowledge loss may be inevitable in the engineering world, leading A&D organizations can take steps to prevent it. Here are four critical strategies:
- Create a culture of knowledge retention. Today, 84% of A&D professionals surveyed by Ernst & Young say their employers offer remote working options. This type of work environment requires new ways of information sharing and collaboration using digital channels. To foster a company culture where knowledge can be easily shared and leveraged, make sure to implement tools and platforms that facilitate seamless communication and collaboration, and can be accessed securely from any location at any time.
- Support mentoring. When less experienced engineers have the opportunity to work alongside industry veterans, they learn a lot. While such work arrangements are not the norm, they facilitate the hand-off of years of knowledge before experts retire. This way, the new generation of A&E engineers can continue to build on the knowledge that the company has already invested in developing for years
- Boost productivity with digitization. Using a digital twin – a virtual model of a physical aircraft or spacecraft that includes all of its components, systems, and behaviors – simplifies data sharing, and ensures all prior knowledge is documented and easily accessible. It eliminates data silos and solves the dilemma of knowledge loss by preserving essential learnings and knowledge in digital form. In addition, many A&D firms are leveraging AI and machine learning to aggregate data, which saves engineers hours of information-chasing.
These three strategies will help reduce the risk of losing valuable knowledge, while providing myriad benefits, such as increased productivity, effective collaboration, improved product quality and faster time to market with innovative A&D solutions.
Siemens is transforming business processes through digitalization, helping A&D companies to achieve program execution excellence while reducing risk risk. Read our whitepaper, “Combatting Knowledge Loss in Aerospace and Defense E/E Design,” to learn how A&D organizations are using the Siemens Xcelerator open digital business platform to overcome the challenges of electrical/electronic (E/E) systems development and prevent knowledge loss.