Welcome to the era of electrification and digitalization in aerospace
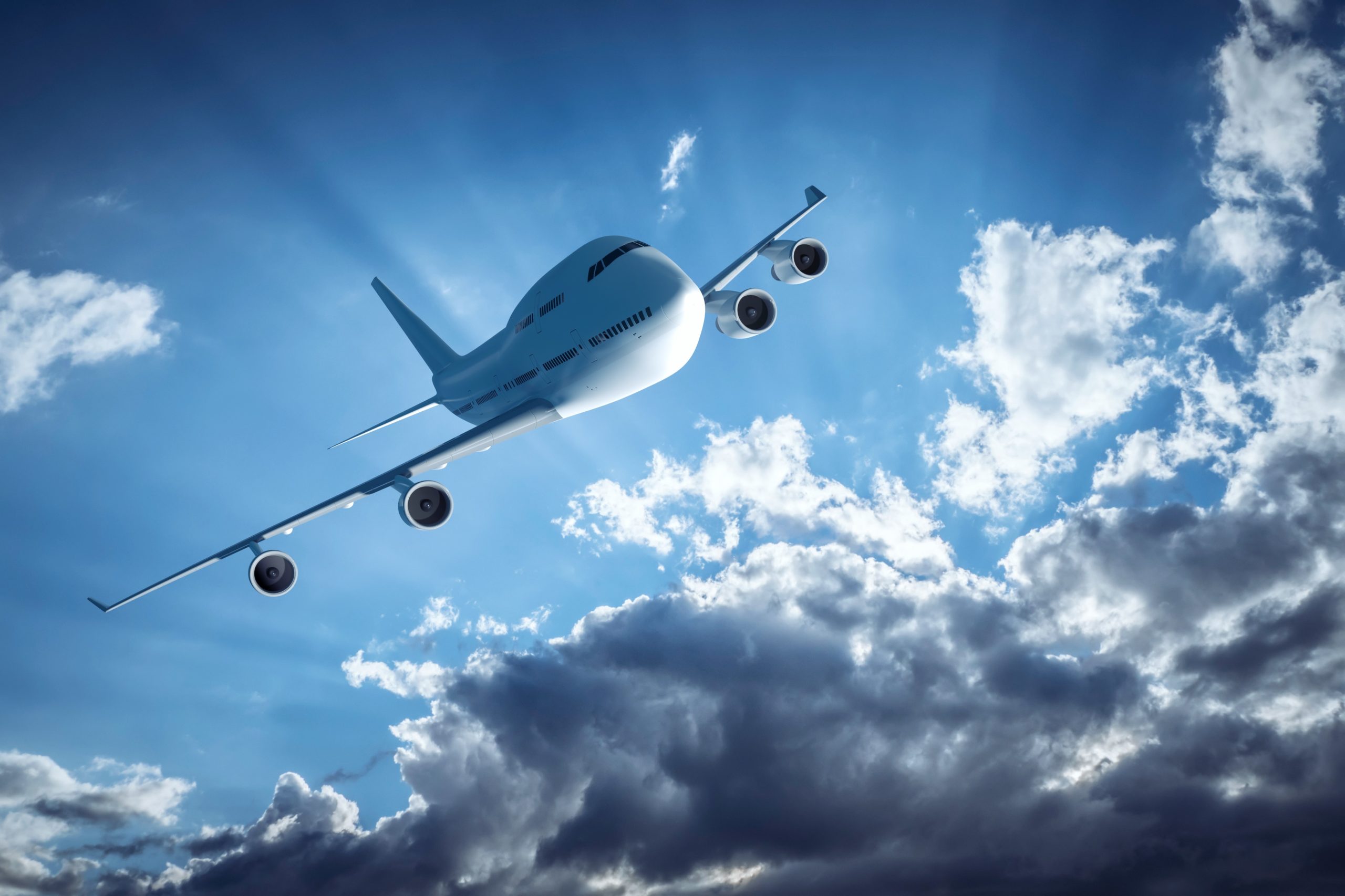
Aerospace OEMs increasingly turn to electrical systems to differentiate their new platforms, motivate new sales and enable advanced missions. It’s important to realize when discussing aircraft differentiation, it’s not necessarily about adding bigger or better features. Makers of commercial, business and general aviation aircraft are constantly on the lookout for ways to improve aircraft efficiency and reduce overall operating and maintenance costs.
Electrification of existing aircraft functions allows the platform to become lighter and more reliable, and hence more cost effective to operate and maintain. Meanwhile, makers of military aircraft must relentlessly add new capabilities to their platforms to increase their survivability and mission envelope. Many of today’s military missions would be impossible without the sensing, communications and computing capabilities enabled by advanced electrical systems.
The increase in electrification
Electrification came to aircraft slowly. From the early days when the Wright brothers first took flight in 1903, up to the 1970s, the fundamental disciplines applied to aircraft design saw little change. New capability was typically implemented mechanically, pneumatically or hydraulically. Gathering decades of hard-earned experience, our industry developed the intuition necessary to contain aircraft development program risk.
Today, the stakes have changed. Now when an aircraft OEM differentiates a platform, an increasing number of the capabilities are electrically enabled. The industry made a big leap forward in electrification in the 1970s when the first fly-by-wire system was introduced. In the last 20 years, there has been a serious escalation in electrical content. Figure 1 demonstrates how commercial aircraft electrical power demand, a proxy for onboard electrical system content, has grown since the early days of flight.
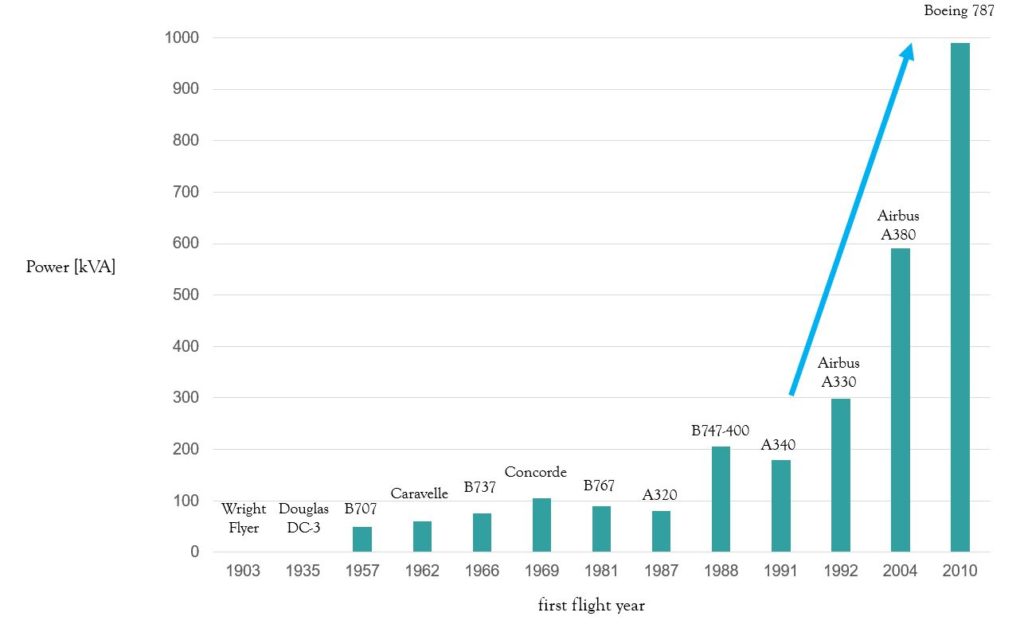
Electrical
system complexity on the rise
Increased electrification in modern aircraft translates into increased
electrical system complexity. On a typical business jet, for example, it’s not
uncommon to have over 120 independent electrical systems. The electrical wiring
interconnect system (EWIS), physically linking all these systems, can be
composed of up to 350 wire harnesses comprising as many as 30,000 wire
segments. This could easily add up to over 50 miles of wire – and well over
100,000 parts. Most of these electrical systems are intelligent, employing
sophisticated software to deliver their functionality.
Finally, as digital systems have replaced analog ones, networked digital communication has risen substantially. Today, analog point-to-point connections are declining while the use of sophisticated digital communication buses has dramatically increased, supplying a larger percentage of on-board data communication.
Balancing innovation and risk
To achieve profitability goals while satisfying their customers’ increasing demands for efficiency and mission capability, aerospace companies must execute development and manufacturing programs in adherence to their planned commitments. This requires program execution excellence.
What exactly does this mean?
It means aircraft OEMs, and their suppliers must deliver on their technical promises while remaining within the cost and schedule estimates made at the time the program was proposed or bid. This is a tall order. As an aircraft OEM embarks on any new program, they must always balance the amount of innovation promised against the amount of financial, schedule and reputation risk they are willing to accept.
With increased electrical complexity comes increased program risk. With electrification still relatively new manufacturers lack the deep experience to develop low-risk, electrically enabled platforms. Hence, they run into substantial program problems. These missteps can cost billions of dollars. Some of the more common and costlier issues include:
- Inadvertently routing signals close to each other which require greater separation to comply with regulatory standards, and not discovering this until after initial production ramp has begun
- Devoting unnecessarily long durations and large budgets to the analysis and evidence generation required for certification as a result of disconnected design authoring, analysis and reporting environments
- The reiteration of platform designs arising from electromechanical issues found during physical integration
- Loss of configuration control, such that an OEM can no longer be assured that aircraft electrical systems are being manufactured consistently with the certified configuration
Model-based, electrical and electronic system development
Successfully coping with increased electrical system complexity requires a model-based approach to platform electrical and electronic (E/E) system development. Those who invest in this type of digital competency gain a competitive advantage through a combination of increased productivity and decreased risk levels.
A model-based approach to E/E system development goes well beyond eliminating drawings and paper-based documents. Rather than simply digitizing these documents, a model-based approach employs digital models, or twins, of a product’s design, manufacturing process (and the artifacts that support it), and sustainment to automate and better manage the entire product lifecycle. It integrates the entire product lifecycle digitally, employing a digital thread to connect the various life cycle stages (Figure 2). Physical hand-offs between teams and independent data systems are significantly reduced and ultimately eliminated. As part of the Siemens Xcelerator portfolio, this represents an evolutionary shift to a connected digital work environment, employing continuity of digital information to enable collaboration among multiple engineering disciplines, up and down the value chain.
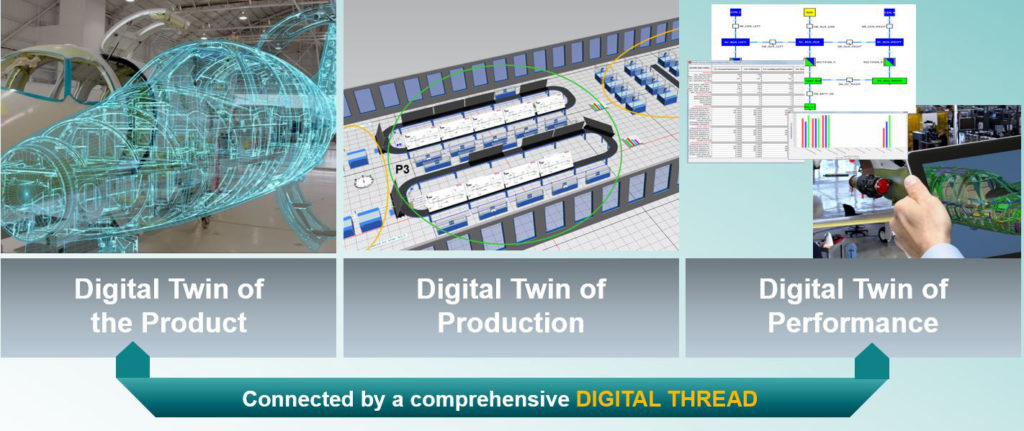
Taking electrical system development to the next level
Implementing a model-based approach for aerospace E/E system development is an essential aspect of gaining overall digital business process competency, leading to reduced program risk. It allows those who participate to transform their business and engineering processes, improving productivity, accelerating program completion and adding innovative new platform capabilities to differentiate themselves in their markets.
And this is where the Siemens’ Capital solution comes into play. Capital enables model-based development. The principles that underlie it are inherent to its architecture and naturally result in a digital twin of the platform’s electrical system. Furthermore, this approach natively implements the digital thread connecting E/E system development throughout the lifecycle and among the core electrical implementation disciplines.
And the results of adopting this model-based approach are already evident. One business jet OEM who invested in Capital deployed the full digital thread from design through manufacturing to implement model-based EWIS development. They carried this out fully, improving harness manufacturing tooling, processes and work instruction. The result: a reduction in harness manufacturing touch labor that ultimately added more than three percent to platform profitability!
To learn more about how you can apply Capital’s platform solution to address the complexity of the more electric aircraft, please visit this website.