Modernizing Wire Harness Manufacturing with a Model-Based Approach
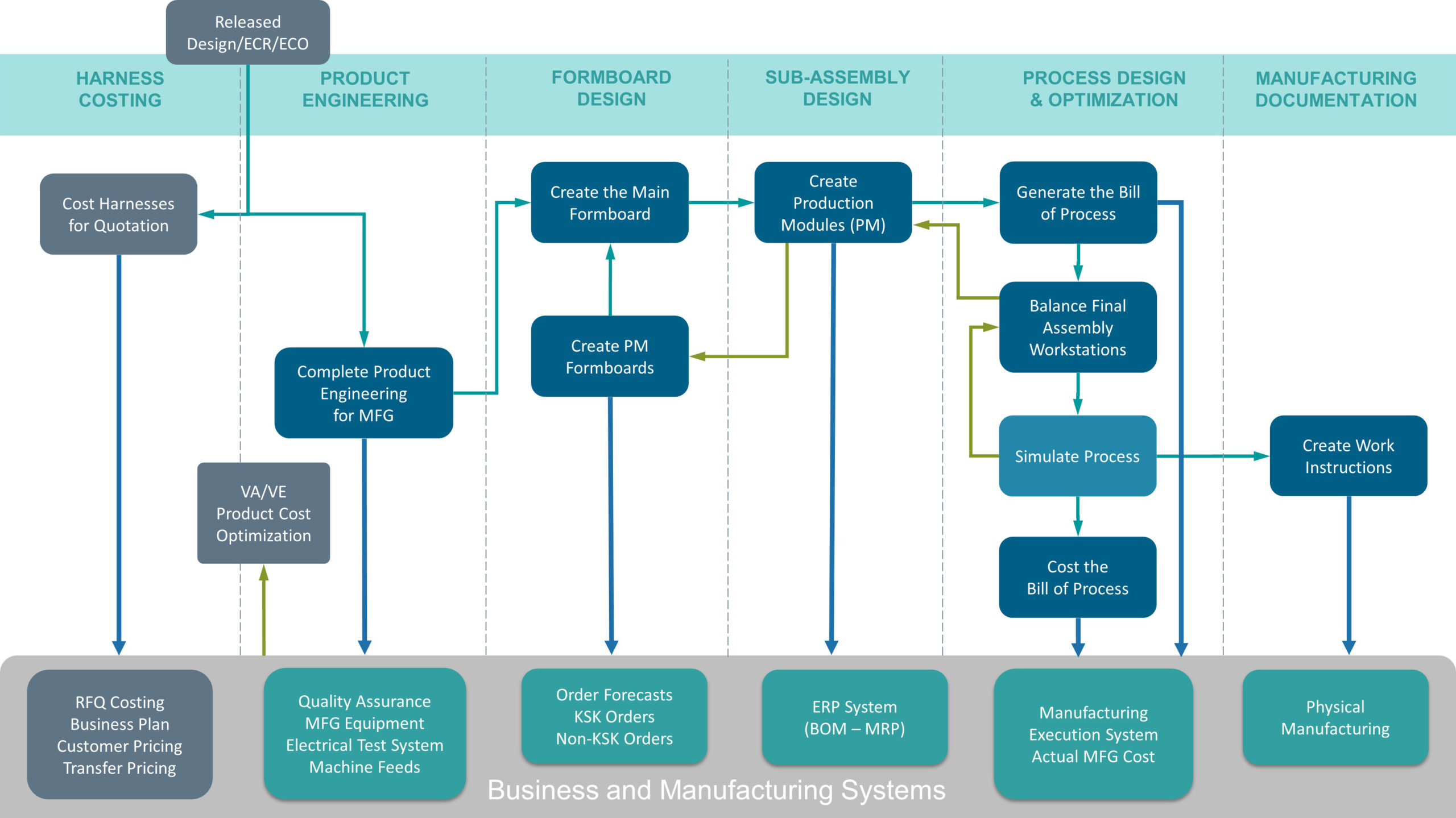
The increase in electrical and electronic features in modern vehicles is placing more emphasis on the wiring harness that transmits power and signals between actuators, sensors and ECUs (figure 1). ADAS and automated driving systems are particularly demanding due to the external sensors that the systems need to perceive the vehicle’s environment, such as approaching objects or speed limit signs.

Furthermore, increasing demand for highly automated and electrically propelled cars directly translates to a growing wire harness manufacturing industry. Analysts predict that by 2023 the automotive wiring harness industry will grow to over 70 billion dollars in yearly revenue and more than 91 billion dollars by 2025 (Future Market Insights, 2016).
With growth comes fresh challenges and new pressures on the industry. To support the greater number of electrical and electronic systems, some of which are very sophisticated, wiring harnesses are becoming intensely complex. Manufacturers must also accommodate all of the possible configurations of a vehicle, a number that frequently rockets into the tens of millions. While manufacturing these complex systems, companies have to meet very tight timelines, exacting quality requirements, and minimize the cost and weight of the harness.
Current Challenges
Engineering and manufacturing methods common across the industry have been in use for decades, and are showing their limitations in a new era. Wire harness manufacturing continues to be an extremely labor-intensive process. Today, approximately 85% of all wire harness manufacturing operations are carried out manually.
Even more troublesome is the fragmentation between the harness design and manufacturing departments and systems. Design and manufacturing engineers often transfer data manually between their respective domains, recreating and reentering the transferred design data into each of their systems, such as CAD, production, assembly board design, or costing systems, among others.
Conventional wire harness manufacturing methods are starting to creak under the weight of these new challenges. First, fragmented design and manufacturing processes lead to manual data transfer and reentry between domains. This is slow, error-prone, and an inefficient use of engineers’ time and attention. As manufacturing engineers make changes to improve the manufacturability of the harness, these changes often are lost in the transition of data between teams. Even in state-of-the-art facilities, the high-level process from design engineering through product engineering, manufacturing engineering and generation of the manufacturing documentation is completed with basic office applications and AutoCAD drawings. The information is passed along to the next person in the chain, who manually recreates the non-digital information in another format or style.
This is no longer contemporary nor acceptable. New product introduction cycles can take months, and design changes up to a few weeks to be fully implemented. Manual data sharing and reentry causes mistakes that cost money, time, and, even worse, can jeopardize a good relationship with the customer.
The accelerating pace of program milestones also means that manufacturing engineers have little time to optimize the manufacturing process, leading to a sub-optimal process from the beginning. One task that can be particularly challenging is the creation of work instructions. With current methods, creating work instructions is a difficult, time-consuming, and challenging job that requires skill and expertise to complete accurately, and on time. Work instructions that are late or low-quality can lead to inadequate and unsatisfactory workstations, further leading to assembler errors. Errors that are found during testing cause engineers to perform lengthy reworks, or even scrap the faulty harness entirely, producing unexpected costs.
Figure 2 shows a typical, high-level manufacturing engineering flow in the wire harness industry. Today, errors from manual data reentry can occur at any of these stages, each of which requires great skill and experience to complete accurately. Adjustments and corrections made downstream in the flow must be fed upstream manually in order to achieve data coherency. The conventional wire harness manufacturing methodology is vulnerable to errors from fragmented processes, and the loss of tribal knowledge as engineers retire or leave their jobs. Other key issues include inconsistent or inaccurate costings, sub-optimal formboard design or manufacturing process design, and misplacing key information on the shop floor. These can lead directly to inefficiency during production. As a result, manufacturing and overall costs can overshoot the quotation made to the customer, and production quality can suffer.
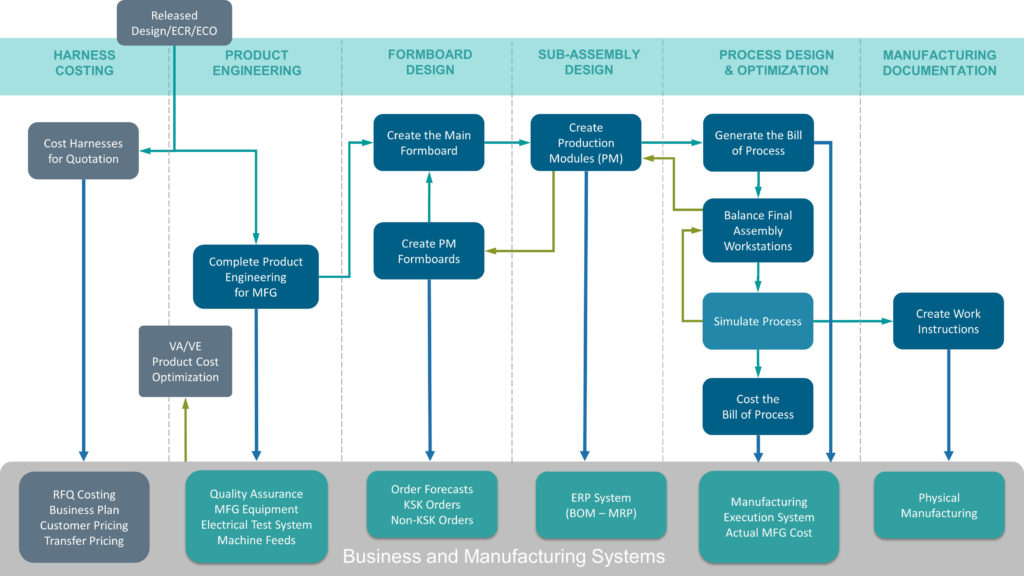
Model-Based Harness Manufacturing
A model-based flow unifies the previously fragmented domains of design and manufacturing by automating data exchange and providing engineers with access to cross-domain decisions. Tribal knowledge, previously held by experienced engineers, is captured through integrated design rules that support automation, guide all engineers consistently and check designs for issues.
There are three key aspects to digitalization and the model-based enterprise in the wire harness industry (figure 3). First are digital models of the wire harness product and the manufacturing process. The digital models of the harness and production process together constitute the digital twin. Automation is the second pillar. Modern harness design and manufacturing solutions can consume design rules created by veteran engineers and use them to automate the transformation of the digital harness and process models into bills-of-process, work instructions, and other output formats. The third pillar is data reuse. Instead of recreating or reentering data, in a model-based engineering flow, data is created once and reused to the greatest extent possible by all upstream and downstream consumers.
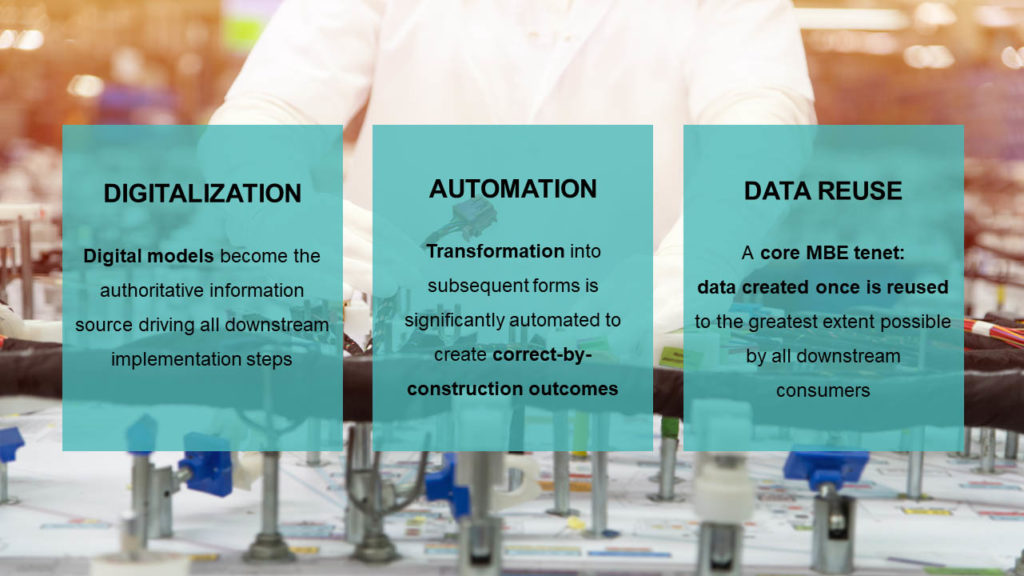
Companies create a digital thread in which all of the functions, from architectural and functional design through to physical design, manufacturing engineering and after-sales service, can all use the same data. At each stage of the harness lifecycle, each stakeholder can use the same data models and have access to decisions that are made in other domains. Using a digital thread, design cycles are faster and issues can be caught and resolved earlier in the process when they are much less expensive. By also reducing design rework, data reuse minimizes costs and enables superior manufacturing efficiency.
Today, solution partners offer integrated software portfolios to help wiring harness manufacturers prepare for the challenges of tomorrow. Capital, part of the Xcelerator portfolio, supports the full wiring harness engineering and manufacturing flow, from definition through production. In part 2, we will examine how such solutions can help wiring harness manufacturers implement a model-based engineering flow to improve their quality, efficiency, and profitability.
You can also read our whitepaper on model-based systems engineering for wiring harness manufacturing by clicking here.
Comments
Leave a Reply
You must be logged in to post a comment.
I like the general approach. One comment, in the graphic it shows the harness product engineering, and the harness formboard as two separate steps, however in Capital the formboard is part of the product definition. Ideally those artifacts would be separate items in Capital. This way you could create multi-harness formboards more easily, and separate the formboard and the harness engineering release in the product lifecycles, and schedule.
Hi Rich, my name is Humberto Cantu I am part of the Siemens Capital team. One of the benefits of the Capital tools is its flexibility to adopt different flows to make sure that user maximize their IP advantage. As you mentioned, Capital Formboard can be in the Product Definition domain for some companies but also can be part of the Manufacturing domain for other companies. The definition depends on the needs and requirements of companies. I can reach out to you to go over these two flows and discuss the details of each flow.