5 Herausforderungen bei der Konstruktion und Entwicklung von Elektrofahrzeugen
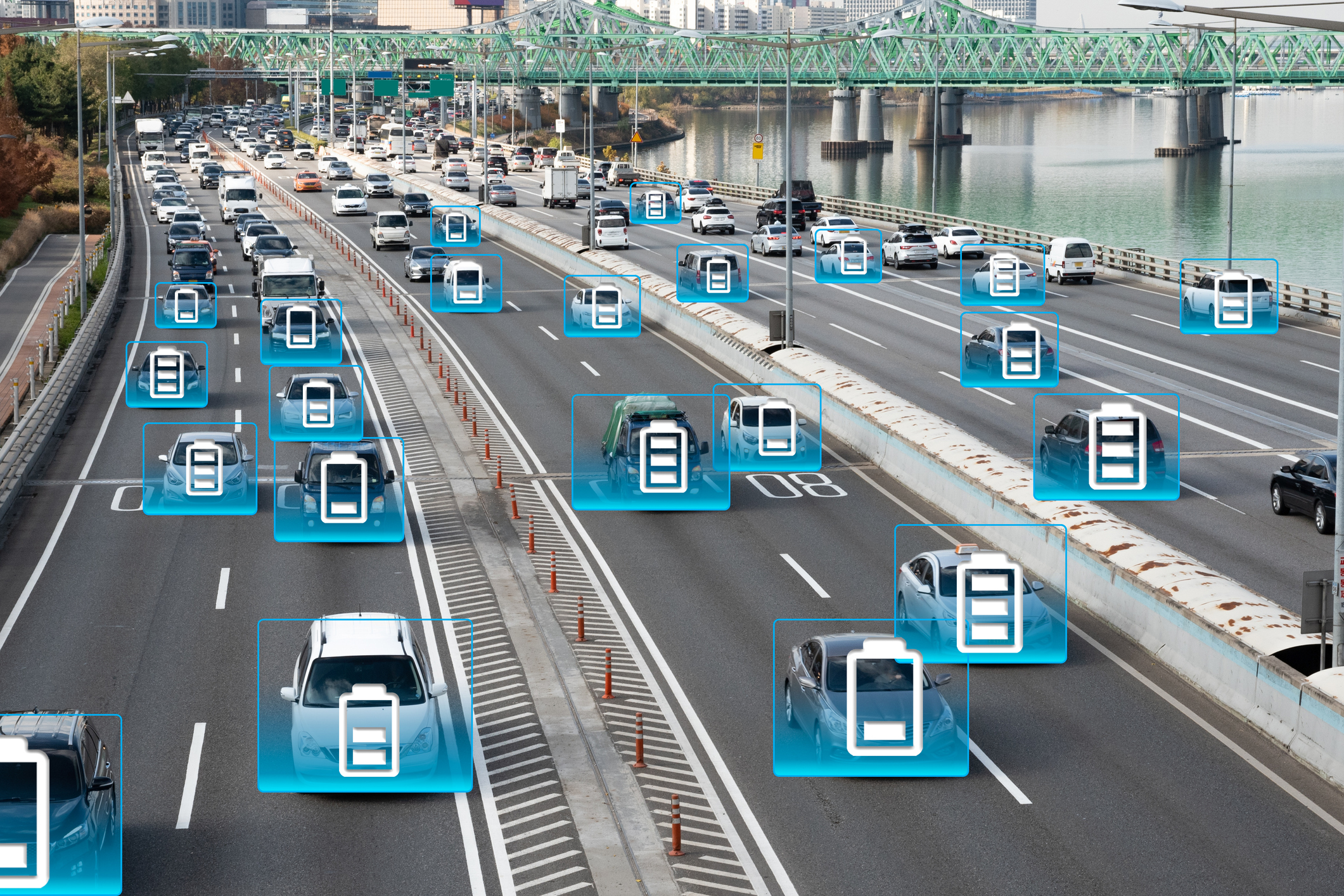
Unsere Konstrukteure aus der Automobilindustrie geben Einblicke in die Herausforderungen bei Konstruktion und Entwicklung von E-Fahrzeugen.
Denken Sie beim Kauf Ihres nächsten Autos über ein Elektrofahrzeug nach? Die Chancen stehen gut, dass Sie daran gedacht haben. Trotz der Wirtschaftskrise wird in Nordamerika, Europa oder China die Nachfrage nach Elektrofahrzeugen immer größer. Und die Hersteller reagieren auf diese Nachfrage. Die Auswahl an elektrifizierten Fahrzeugmodellen (xEV) und Marken ist größer denn je. Newcomer konkurrieren mit etablierten Autoherstellern um Marktanteile.
Was sind die 5 größten Herausforderungen bei der Konstruktion und Entwicklung von Elektrofahrzeugen?
Die Elektrifizierung von Fahrzeugen hat die Spielregeln neu gesetzt. Der beeindruckende Markterfolg von Tesla zeigt, dass der xEV-Bereich Mobilitätsvisionen ermöglicht, aber nicht mühelos verwirklicht. Um auf diesem hart umkämpften Markt zu bestehen, braucht es Engagement, Fachwissen, Kreativität, Teamgeist und vieles mehr. Neben der richtigen Geschäftsstrategie müssen Marktteilnehmer ihre Konstruktionsmethoden und -prozesse überdenken und ein rasantes Innovationstempo vorantreiben.
Was ändert der Trend zur Fahrzeugelektrifizierung für Konstrukteure? Welche Herausforderungen begegnen Konstrukteuren bei der Konstruktion und Entwicklung von E-Fahrzeugen?
Diese Frage haben wir Steven Dom, Director Business Development Automotive, und Warren Seeley, Director Business Development Powertrain, gestellt. Sie haben die 5 wichtigsten Konstruktionsaufgaben ermittelt, denen sich Konstrukteure in der Automobilindustrie heute stellen müssen. Lesen Sie die Expertenmeinungen im Artikel und teilen Sie Ihre eigenen Ansichten in den Kommentaren mit.
Herausforderung Nr. 1: Die „richtige“ Fahrzeugarchitektur auswählen

Steven Dom: „Bei E-Autos gibt es keine vorgefasste Meinung zum Aussehen des Fahrzeugs.“ Herkömmliche Fahrzeuge mit Verbrennungsmotor waren um ein Kernelement konzipiert: den Antriebsstrang. Elektrofahrzeuge bieten den Konstrukteuren deutlich mehr Gestaltungsspielraum. Die Perspektive ist gleichermaßen faszinierend und beunruhigend. Einerseits ist es faszinierend, die Vielfalt innovativer Konstruktionen zu sehen, die von Start-ups und etablierten Firmen gleichermaßen vorgestellt werden. Einige Konstruktionen sind erst durch die Flexibilität von E-Fahrzeug-Architekturen möglich. Andererseits wandelt es die Rolle des Konstrukteurs und macht sie anspruchsvoller als je zuvor.
Wie kann der Konstrukteur die am besten geeignete, optimierte, kurz: die „beste“ Architektur wählen, die alle Leistungsanforderungen erfüllt? Es ist unmöglich, sämtliche Möglichkeiten zu testen. Erstens, weil es einfach zu viele davon gibt. Zweitens, weil auch die Markteinführungszeit ein drängendes Problem darstellt. „Der Konstrukteur muss nicht nur die beste Architektur wählen, sondern dies auch zügig tun.“
Von der generativen Konstruktion bis zur Konstruktionsoptimierung stehen Konstrukteuren verschiedene Werkzeuge zur Verfügung, um die unerschlossenen Bereiche des E-Fahrzeug-Designs zu erforschen.
Herausforderung Nr. 2: Einen menschenzentrierten Konstruktions- und Konstrukteursansatz umsetzen

Steven Dom: „Denken Sie darüber nach, wie künftige E-Mobilität das Leben der Menschen weit über Fortbewegung hinaus prägen wird. Seit über Hundert Jahren steht das Auto für mehr als nur Mobilität. Es hat die individuelle Mobilität revolutioniert. Und es hat das Erscheinungsbild menschlicher Wohnstätten und Städte neu gestaltet. Und es begeistert Auto- und Motorsportfans gleichermaßen.
Autos haben den Wandel in Branche und Wirtschaft zweifellos vorangetrieben. Doch unsere Welt wandelt sich. Die Folgen von CO2-Ausstoß auf das Klima und schwindende fossile Ressourcen treiben einen wirtschaftlichen und sozialen Umbruch voran. Die Denkweisen der Menschen wandeln sich. Ja, PS-starke Autos galten einst als Statussymbol und Stolz der Karriereleiter. „Doch statt des Brüllens eines hochdrehenden V12-Motors erwarten Kunden heute in erster Linie sichere, komfortable und umweltschonende Fahrzeuge.“
Mit der Konstruktion von Elektrofahrzeugen neu denken
„Elektrofahrzeuge sind einzigartig. Sie sind von Natur aus leiser. Der Sound eines Elektroautos entsteht nicht durch das Dröhnen des Motors, das Hämmern der Kolben oder die Geräusche von Ansaugung und Auspuff. Es besteht Raum für sorgfältig von Künstlern und Komponisten konstruierte Melodien. Ziel ist es, nicht nur ein Fußgängerwarnsystem zu implementieren, sondern auch die Identität des Modells und der Marke zu vermitteln.
Auch die Karosserien von E-Fahrzeugen glänzen mit zahlreichen innovativen Konstruktionen. Bei Luxuslimousinen mit großer Reichweite ist die Form oft stromlinienförmig und elegant, da die Verringerung des Luftwiderstands wichtiger denn je ist. Für urbane Mobilität zählt vor allem der Innenraum: Carsharing-Angebote werden zu rollenden Gemeinschaftsbüros oder Wohnzimmern. In Bezug auf die Konstruktion scheinen die Möglichkeiten grenzenlos. „Wie können Hersteller das Potenzial offener Konstruktion voll ausschöpfen?“

Hersteller müssen die Bedürfnisse und Wünsche der Menschen in den Mittelpunkt ihrer Konstruktionen stellen, nicht die Technologie. Sie sollten sich weiterhin an Verbraucherbedürfnissen und -erwartungen ausrichten und deren Anliegen gebührend berücksichtigen.
Verbraucherbedenken ausräumen
Trotz zunehmender Akzeptanz bei Verbrauchern bestehen weiterhin große Hürden für die flächendeckende Einführung der E-Mobilität. Die Hersteller müssen Grenzen überwinden, um Fahrzeuge zu entwickeln, die den Kundenbedürfnissen gerecht werden. Sie müssen Aspekte wie Reichweite, Kosten, Akkuleistung, Ladezeit und weitere Faktoren ausbalancieren. Dom und Seeley staunen über die immer höheren Kundenerwartungen. Trotz erheblicher Fortschritte in der E-Mobilitätstechnik scheint es, als wäre es nie genug. Werden Verbraucher Fahrzeuge akzeptieren, die eine ähnliche oder größere Reichweite als Verbrenner haben? Das Beratungsunternehmen Deloitte zeigt sich zuversichtlich:
„Wir erwarten, dass in den kommenden Jahren einige Hürden gänzlich wegfallen werden. „Die Reichweite von E-Autos ist bereits mit der von Verbrennern vergleichbar; preislich herrscht Parität, bedenkt man Förderungen und Gesamtkosten; zudem wächst die Modellvielfalt stetig.“
Quelle: Deloitte
Deloitte erkennt den Mangel an Ladeinfrastruktur als neue Hauptsorge der Verbraucher, was darauf hindeutet, dass E-Autos zunehmend als realistische Option wahrgenommen und die praktischen Aspekte des Besitzes nun in den Fokus rücken.
Kundenerwartungen übertreffen
Doch selbst wenn Hersteller die Bedenken künftiger Besitzer oder Anwender erfolgreich ausräumen, bleibt die Frage der Erfüllung unausgesprochener Erwartungen bestehen. Der zunehmende Automatisierungsgrad zwingt NVH-Konstrukteure, ihre Komfortdefinition neu zu überdenken. Trotz technischer Fortschritte stehen NVH-Konstrukteure vor der größeren Herausforderung denn je: Wie lässt sich das angenehmste Fahrerlebnis für Fahrer und Mitfahrer gestalten? Beim Umgang mit Robotertaxis erwarten Menschen eine sichere, bequeme und angenehme Fahrt. Und während Sicherheit ein relativ objektives Kriterium ist, das fortgeschrittene Fahrerassistenzsysteme (ADAS) aktiv adressieren, lässt sich der Begriff von Komfort und Fahrvergnügen schwerer definieren.

Lesen Sie den Blogbeitrag Verfolgen Sie einen menschenzentrierten Ansatz beim Sound-Design von E-Fahrzeugen, um weitere Erkenntnisse zu diesem Thema zu erhalten.
Herausforderung Nr. 3: Management der thermischen Fahrzeugeigenschaften
Warren Seeley: „Apropos Komfort: Befassen wir uns mit der komplexen Frage des thermischen Wohlbefindens. Bei konventionellen Fahrzeugen war die Antwort einfach: Die Motorwärme half beim Aufheizen des Innenraums und Enteisen der Frontscheibe. Und da die Reichweite kein Thema war, konnten Batterien und Elektrik problemlos Sitzheizung oder Klimaanlage versorgen. Aber wie lässt sich der Wärmekomfort in E-Autos gewährleisten, ohne die Reichweite zu opfern? „Und wie sorgen Sie für eine optimale Wärmeverteilung, damit die Batterien kühl bleiben, ohne dass die Fahrgäste frieren?“
Die frühzeitige Betrachtung des Thermomanagements in der Konzeptphase der Fahrzeugentwicklung ist erfolgsentscheidend für die Marke. Siemens' ganzheitlicher Ansatz des digitalen Zwillings balanciert Energie- und Wärmeeigenschaften mit weiteren essentiellen Fahrzeugleistungsmerkmalen wie Langlebigkeit, NVH und Fahrdynamik.

Hier ein Beweis, dass E-Autos auch unter Extrembedingungen überzeugen – sehen Sie sich die Aufzeichnung dieses Webinars an: Schnelle Leistungsvalidierung durch Systemsimulation und Modelle reduzierter Ordnung. Er behandelt unter anderem das Thermomanagement von E-Autos unter den Extrembedingungen der glühenden Sonne im kalifornischen Death Valley.
Herausforderung Nr. 4: Batteriekonstruktion und -integration meistern
Warren Seeley: „Sollten E-Auto-Hersteller Batterietechnologie selbst beherrschen oder auf Zulieferer-Expertise setzen? Die Frage steht noch im Raum. Die meisten E-Auto-Hersteller beziehen Fahrzeugteile größtenteils von Zulieferern und fungieren primär als Systemintegratoren. „Obwohl sich dieser Trend umkehrt und Hersteller verstärkt die Konstruktion und Entwicklung größerer Fahrzeugteile selbst übernehmen, bleibt die Batteriekonstruktion und -entwicklung die Domäne spezialisierter Zulieferer.“

In einem aktuellen Gespräch mit Ed Bernardon, Vizepräsident für strategische Initiativen in der Automobilindustrie, erläutert Henrik Fisker, Gründer, Vorstandsvorsitzender und Geschäftsführer von Fisker Inc.: „Dieses Mal ging es mir nicht darum, jemandem zu beweisen, dass ich ein Auto bauen kann. Wir werden einen Großteil der für uns wichtigen Technologie selbst besitzen. […] Ich muss die Entwicklung einer Klimaanlage nicht besitzen, das ist ein Standardprodukt.
Im Moment haben wir intensive Batterieforschung betrieben und festgestellt, dass keine Festkörperbatterietechnologie in Sicht ist. Die Technologie ist zu komplex und schwer zu skalieren. Daher ist klar: Lithium-Ionen-Batterien werden uns noch lange begleiten, ohne dass wir die Zellfertigung selbst beherrschen müssen. „Ich bevorzuge Offenheit für verschiedene Batterietechnologien bei leichten Verbesserungen und die Möglichkeit, Batterien so zu gestalten, dass ich bei Lieferengpässen eines Herstellers auf andere zurückgreifen kann.“
Erneut ist die Integration der Komponenten, vor allem der Batterien, entscheidend für den Erfolg. Der digitale Zwilling ermöglicht die frühzeitige Bewertung und den Vergleich der Batterieleistung in verschiedenen Aufbauten und Konfigurationen.

Hören Sie sich hier den vollständigen Podcast mit Henrik Fisker und Ed Bernardon an.
Herausforderung Nr.: Anpassung an das wandelnde Umfeld der Lieferkette
Steven Dom: „Konstruktion und Fertigung eines Elektrofahrzeugs verändern die Beziehung zwischen Erstausrüster und Zulieferer grundlegend. Zunächst besteht ein Elektromotor aus lediglich rund 200 Einzelteilen, während ein Verbrennungsmotor mindestens 4000 Komponenten aufweist. Diese drastische Reduktion der Teileanzahl bietet den Herstellern vielfältige Vorteile. Dies kann einerseits zu erheblichen Kosteneinsparungen führen. Der Einkauf der Teile ist günstiger, und die EV-Produktion ermöglicht Skaleneffekte, da Erstausrüster ihre Teile von weniger Zulieferern beziehen. Die geringere Teileanzahl wirkt sich positiv auf Wartung und Gesamtbetriebskosten aus. Es wird deutlich einfacher, einzelne Komponenten zu ersetzen.
Für Zulieferer ist der Nachteil eine engere Bindung an den Erstausrüster. Beispielsweise ist die von Warren aufgeworfene Frage der Batterieintegration von zentraler Bedeutung. Der Ansatz des digitalen Zwillings treibt oder lenkt die Entscheidungen der Lieferanten. Sie sind praktisch gezwungen, dieselben Simulationstools wie die Erstausrüster zu nutzen. Kurz gesagt: Integration ist heute wichtiger denn je.“

Natürlich gibt es keinen Königsweg, um all diesen Herausforderungen zu begegnen. Bei Siemens sind wir überzeugt: Ein ganzheitlicher Ansatz digitaler Zwillinge wird uns helfen, die Mobilitätszukunft zu meistern. Die Partnerschaft mit Siemens, die Nutzung von Konstruktionsdienstleistungen für den Technologietransfer und der Einsatz des digitalen Zwillings sind Schritte zum Erfolg.
Bewältigung der Herausforderungen bei der Konstruktion und Entwicklung von Elektrofahrzeugen
Erfahren Sie durch unser umfassendes Whitepaper, wie Sie digitale Zwillinge in Ihren Konstruktions- und Entwicklungsprozess für Elektrofahrzeuge integrieren können: „Verlassen Sie sich auf einen umfassenden digitalen Zwilling –
Mit Simcenter die Komplexität des Performance Engineering von elektrifizierten Fahrzeugen beherrschen“