What automotive OEMs can learn from the 20-year partnership between Siemens and Oracle Red Bull Racing
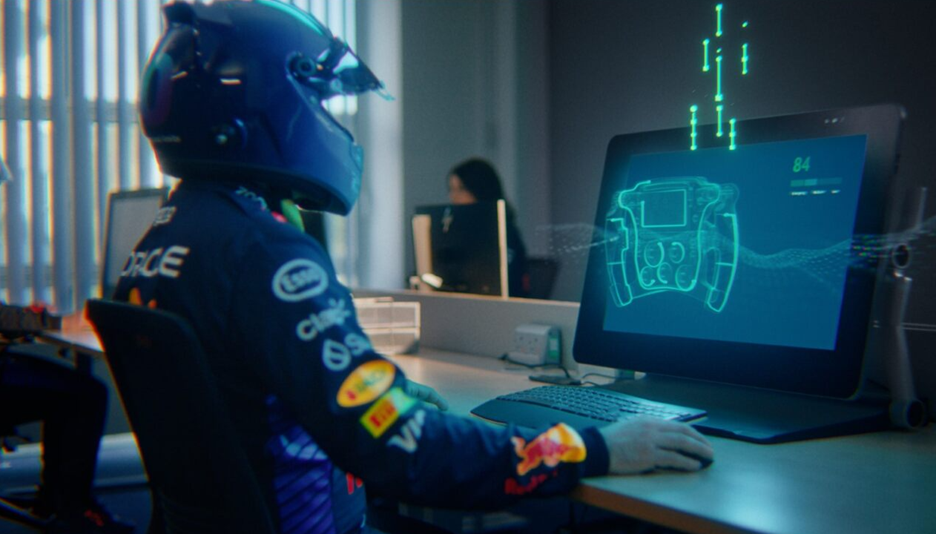
Oracle Red Bull Racing (the Team) is one of the most successful teams in Formula One (F1) history, dominating the sport with multiple Drivers’ and Constructors’ Championships, including recent titles in 2021, 2022, 2023 and 2024. Their ability to consistently outperform competitors stems from their incredible talent and leadership alongside a relentless pursuit of innovation, precision, and efficiency. This success stems from extraordinary talent, leadership, and an unwavering commitment to innovation, precision and efficiency.
For two decades, Siemens has proudly partnered with Oracle Red Bull Racing, setting new benchmarks in design, simulation, and manufacturing. The lessons learned from this partnership offer valuable insights for automotive OEMs, who can adopt these strategies to address development challenges and revolutionize their own operations.
Drive collaboration across teams
Formula One demands seamless collaboration between design, engineering, and manufacturing teams to meet strict regulations and tight deadlines. Oracle Red Bull Racing leverages Siemens Teamcenter, a robust product lifecycle management (PLM) platform, to centralize data and enable real-time collaboration. Digitalized workflows reduce bottlenecks and ensure that updates are implemented quickly and accurately.
For OEMs, managing large teams across suppliers and disciplines often creates silos and inefficiencies. Adopting a unified PLM system like Teamcenter can break down these barriers, enabling cohesive teamwork. From tracking thousands of parts to streamlining signoffs, a centralized system ensures everyone works with the same data in real-time, reducing errors and improving overall productivity.
Embrace the digital twin
Oracle Red Bull Racing faces the constant challenge of optimizing their cars in a sport where milliseconds determine outcomes. Due to time constraints and high costs, physical prototypes are not practical, so the team relies heavily on digital twin technology through Siemens solutions like NX and Simcenter. A digital twin—a virtual representation of a physical object or system—allows the Team to simulate designs, test components, and predict real-world performance for each race before production begins.
OEMs can also harness digital twins to transform their development process. By creating a virtual model of a vehicle, OEMs can identify potential issues early, reduce reliance on physical prototypes, and achieve faster development cycles. This right-first-time approach ensures vehicles meet safety, performance, and regulatory requirements while reducing costs and time-to-market.
Accelerate design iteration
The ability to iterate quickly is critical in Formula One. Oracle Red Bull Racing manages hundreds of design changes weekly, leveraging Siemens NX to create, test, and optimize components rapidly. Advanced modeling and automation features allow design iterations to be completed up to 20X faster, with part development speeds improved by 3X.
OEMs can apply these techniques to adapt quickly to market demands and regulatory changes. By using advanced CAD tools like NX, they can accelerate design processes, ensuring vehicles are optimized for performance and manufacturability. Faster iterations enable quicker responses to customer feedback and greater agility in development.
Digitalize electrical distribution engineering
Electrical distribution systems in Formula One must deliver high performance within compact, weight-sensitive designs, while enduring extreme conditions. Red Bull Technology uses Siemens Capital to digitalize electrical design and harness development. This eliminates the need for physical prototypes, accelerates initial development, and ensures seamless integration with the car’s architecture.
OEMs can adopt Siemens Capital to streamline their electrical engineering processes. The software automates design and validation, optimizing electrical systems for weight, layout, and performance. Its integration with other Siemens tools allows teams to collaborate across disciplines, minimizing errors and enhancing overall vehicle quality and reliability.
Implement design changes faster
Managing change is one of the most challenging aspects of Formula One, with thousands of updates required per season. Oracle Red Bull Racing’s engineering change processes, powered by Siemens Teamcenter, reduce signoff times from weeks to hours. These workflows provide improved visibility, ensuring every stakeholder understands how changes impact the overall design and manufacturing process.
For OEMs, implementing digitalized change management can significantly improve agility. Automated workflows and transparent data tracking allow changes to be implemented with minimal disruption, reducing costs and avoiding delays. This approach is particularly valuable in industries where regulatory changes or shifting market demands require frequent updates.
Add precision to composite manufacturing
Oracle Red Bull Racing relies heavily on composite materials like carbon fiber to create lightweight yet durable car components. With Siemens Fibersim, they design and manufacture these parts faster, achieving a 30% reduction in design-to-delivery time. Automated ply modeling adds precision, reduces material waste, ensures consistent part characteristics, and enhances overall performance.
OEMs, especially those producing electric vehicles, face growing pressure to reduce vehicle weight while maintaining safety and durability. By integrating solutions like Fibersim into their manufacturing processes, OEMs can optimize composite designs and produce lighter, more efficient vehicles. This approach improves fuel economy and meets the market’s increasing demand for sustainability.
Automate data integration
With so many interconnected systems and processes in a Formula One car, data integration is critical for efficiency and accuracy. Oracle Red Bull Racing uses Siemens Active Integration to automate the flow of data between systems, ensuring consistency and real-time access to actionable insights. This automation reduces manual errors and frees up teams to focus on innovation.
OEMs can benefit from similar automation by integrating their PLM, ERP, and manufacturing systems. This integration ensures data flows seamlessly across the organization, improving collaboration and decision-making. Real-time insights enable OEMs to identify opportunities for improvement and make informed decisions faster.
Key takeaways for automotive manufacturers
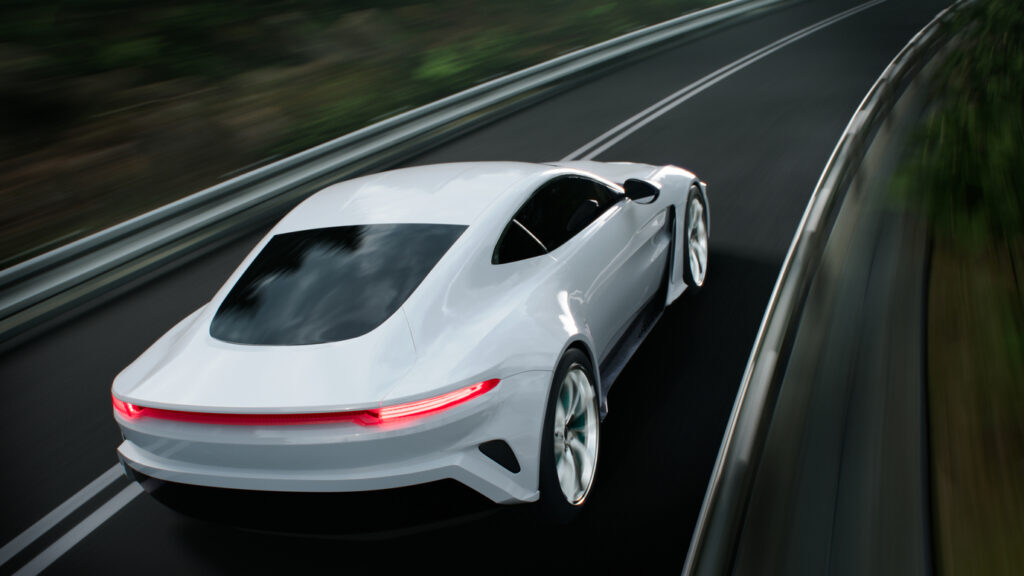
The Siemens-Oracle Red Bull Racing partnership has set a high standard for innovation, efficiency, and collaboration in Formula One. By adopting the same tools and strategies, automotive OEMs can transform their design and manufacturing processes to deliver vehicles that meet modern demands faster.
- Centralized collaboration: Unified tools like Siemens Teamcenter streamline workflows and enhance team efficiency
- Digital twins: Virtual models and performance engineering reduce reliance on prototypes and accelerate development cycles
- Accelerated design: Advanced CAD tools like Siemens NX enable faster design iterations and innovation
- Electrical engineering: Siemens Capital improves harness design, validation, and integration
- Composite manufacturing: Siemens Fibersim produces lightweight, high-performance parts while reducing waste
- Change management: Automated workflows enable quick, accurate updates
- Data integration: Connected systems improve efficiency, collaboration, and decision-making
Learn more
Siemens and Oracle Red Bull Racing celebrate 20th anniversary
Siemens Accelerated Product Development for the automotive industry