How to add flexibility and efficiency to automotive manufacturing with advanced automation
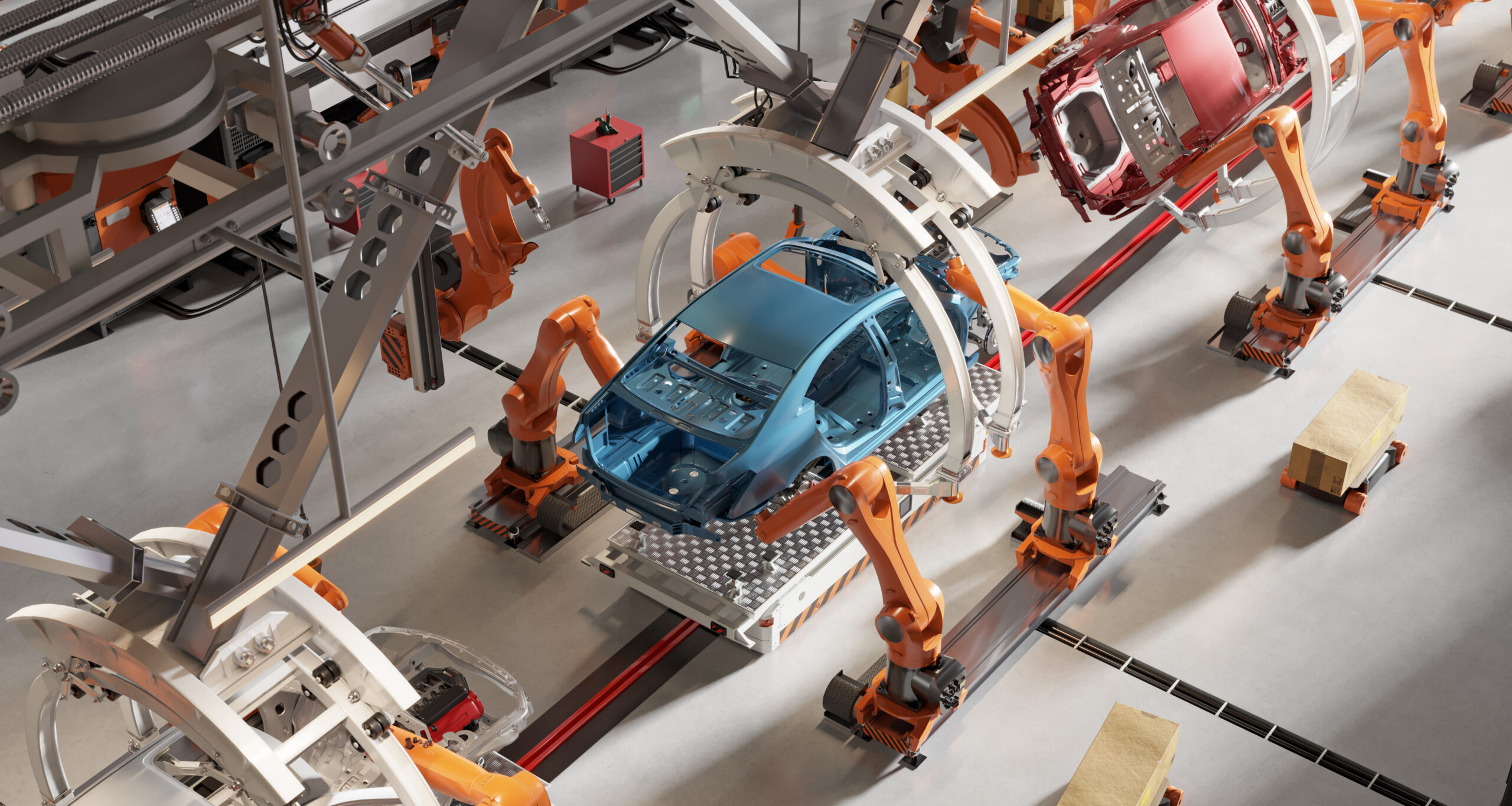
The automotive industry is rapidly evolving with the introduction of electric vehicles, autonomous technology, and an increased emphasis on sustainability. These developments compel manufacturers to upgrade their facilities, train their workforce in new skills, and handle a more complex supply chain. A significant challenge is satisfying the rising demand for various vehicle models while complying with stringent environmental regulations, requiring more adaptable production processes, and minimizing downtime.
Our Production Operation and Optimization solutions help auto manufacturers quickly upgrade their facilities, accelerate product launches, and adapt swiftly to changes in production demands. This smart manufacturing approach addresses current challenges and lays the groundwork for long-term growth and innovation.
Next-level automation for automotive manufacturing
As the demand for electric and high-tech vehicles increases, manufacturers must ensure their production lines are adaptable, flexible, and scalable. Adopting cutting-edge automation technologies is crucial. Technologies such as digital twins, artificial intelligence (AI), and software-defined controls are vital for improving efficiency and adapting to rapid changes in the market. Standardizing processes that can be scaled and reused is essential for effectively meeting customer demands.
Advanced automation is critical in performance analyses of body shops and final assemblies, the virtualization of automation processes, and the use of robotics to enhance overall equipment effectiveness.
Benefits of next-level automation:
- Greater production line output
- Faster root cause analyses
- Reduction in storage expenses
- Lower operating costs
- Enhanced real-time decision-making
- Automated production data collection and integration
Efficient green production for the automotive industry
The transition towards electric vehicles highlights the need for sustainable production practices in the automotive industry. With stricter environmental regulations and ambitious sustainability goals, manufacturers must integrate eco-friendly practices throughout their operations. This includes adopting innovative solutions that also maintain quality and cost-efficiency.
Green production strategies include integrating sophisticated energy management systems, implementing technologies to cut energy use and carbon emissions, and using data to effectively manage environmental impacts across the supply chain.
Benefits of efficient green production:
- Automated collection of energy usage data
- Lower energy costs
- Full visibility of supply chain emissions
- Reduction of carbon footprints
- Optimized energy efficiency
Digital-enabled automotive workforce
The complexity of modern automotive manufacturing requires a technically proficient and flexible workforce. Implementing virtual and augmented training methods helps get plant personnel up to speed faster. Virtual maintenance training and remote support are practical applications of digital enablement that keep operations running smoothly even when changes must be made quickly.
Benefits of a digital-enabled workforce:
- Fewer manual errors
- Higher quality
- Reduction in training time
- Increased health and safety
- Greater employee satisfaction
Data-driven quality systems for automotive production
Collecting real-time data on production quality is crucial for preventing issues and reducing the reliance on manual inspections. Using automated inspection and performance analytics to identify anomalies ensures high-quality production. Notable applications of data-driven quality systems include visual defect detection in press shops and continuous process monitoring.
Benefits of data-driven quality systems:
- Reduction in manual classification efforts
- Fewer undetected defects
- Lower labor costs
Predictive maintenance in automotive manufacturing
Predictive maintenance involves using AI to analyze production data, enhancing quality and equipment performance monitoring. This proactive approach directs maintenance staff to address potential issues early, ensuring uninterrupted and efficient production. Examples include AI-driven data analysis in welding processes and predictive maintenance for conveyor systems.
Benefits of predictive maintenance:
- Greater accuracy in fault detection
- Enhanced overall equipment effectiveness (OEE)
- 100% automated detection of anomalies
- Minimal unplanned downtimes
Flexible automotive shopfloor orchestration and operation
Managing a flexible and efficient shop floor involves the intricate coordination and optimization of assets like robots, automated guided vehicles (AGVs), and machinery. Centralizing updates for security and operating systems through tools like Common Device Manager and Fleet Manager ensures seamless operations across the production line.
Benefits of flexible shopfloor orchestration and operation:
- Increased operational efficiency
- Continuous production during OT shopfloor configuration
- Increased equipment effectiveness
- Lower operational costs
Embracing flexibility, continuous optimization, and sustainability in automotive manufacturing
Siemens’ Production Operation and Optimization solutions provide unmatched flexibility, efficiency, quality, and sustainability, setting a new standard in automotive manufacturing excellence. By adopting these advanced solutions, manufacturers can meet the current market demands and position themselves for continued growth and success.